How much electricity does an electric injection molding machine use?
2024/05/22 By Topstar
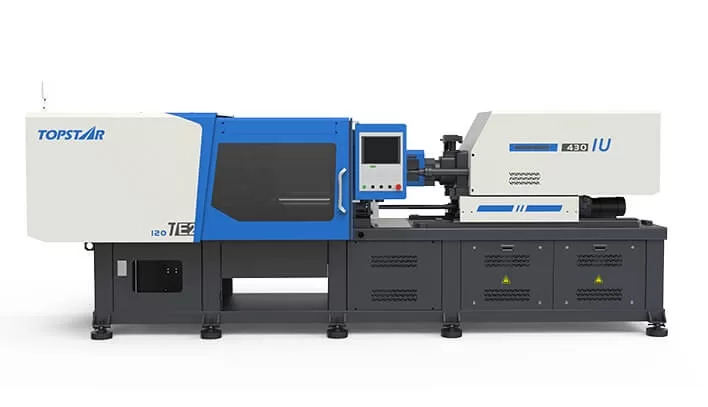
In recent years, many companies have used electric injection molding machines in their production lines. Its cleaner performance and lower energy consumption make it popular with many plastics manufacturers. When purchasing, these manufacturers will also ask how much electricity is used during work. So, in this guide, we’ll answer how much electricity an electric injection molding machine uses and what the relevant factors are.
Injection molding machine power consumption
An injection molding machine is key equipment in the injection molding production process, using various mechanisms to convert raw materials into finished products. Among them, the type and size of the injection molding machine significantly affect its power consumption. Hydraulic machines that utilize hydraulic systems for mold clamping and injection tend to consume more electricity than fully electric machines. The cycle time during the injection molding process will also directly affect power consumption. Longer cycle times will lead to increased energy consumption when producing each part. In addition, they also consume a certain amount of energy and electricity during the heating and cooling process.
Factors affecting power consumption of electric injection molding machines
The size and configuration of the electric injection molding machine play a very important role in its power consumption. The clamping force range of Topstar’s electric injection molding machine is between 90T-460T. Larger machines with higher clamping force and injection capacity may require more power to operate, with their power consumption ranging from 3.8 kWh to 17.9 kWh. Machines running continuously or with long production runs tend to use less energy per component than machines that start and stop frequently. The efficiency of its servo motors and heating elements also affects energy usage. Proper maintenance and calibration of these components are critical to optimize energy efficiency.

Calculate energy consumption and electricity usage
Since different stages of the molding process have different energy requirements, measuring the power consumption of an electric injection molding machine can estimate energy usage by monitoring parameters such as motor power rating, cycle time, and operating temperature. They usually have a power consumption rating, which is the amount of electricity the machine requires to perform its operations. It includes the electricity used by motors, heaters, pumps, and other components.
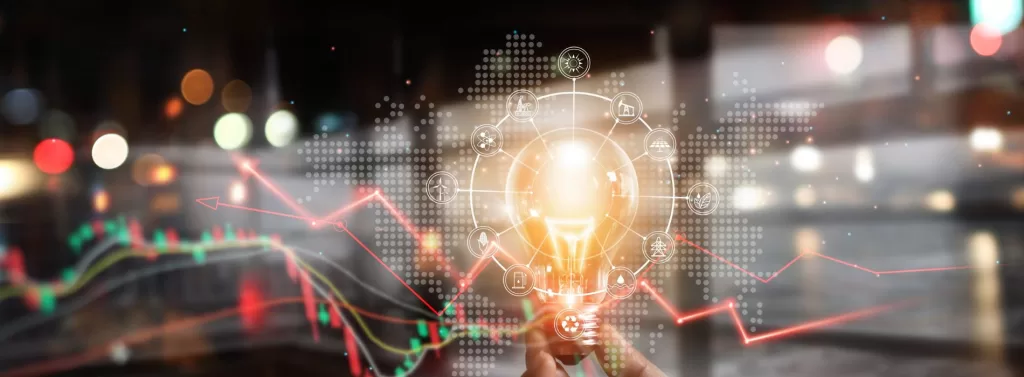
The cycle time of the injection molding process refers to the time required to complete an injection molding cycle, from mold closing to mold opening. The energy consumption formula is equal to power consumption (kW) × cycle time (hours) × operating time (hours/day). Some modern machines are equipped with energy monitoring systems that provide real-time data on energy consumption, allowing operators to identify areas for improvement.
Energy saving features
Electric injection molding machines utilize electric servo motors for all movements, including injection, mold clamping, and ejection. Unlike hydraulic machines, which rely on energy-intensive pumps and valves, electric motors convert electrical energy directly into mechanical motion, significantly reducing energy losses and increasing efficiency. Electric servo motors can also precisely control the entire injection molding process. This precision allows for more accurate control of injection speed, pressure, and position, as well as shortening cycle times and optimizing energy consumption. Topstar’s electric injection molding machines are equipped with regenerative braking systems that capture and store the kinetic energy generated during the deceleration phase and reuse it in subsequent cycles.
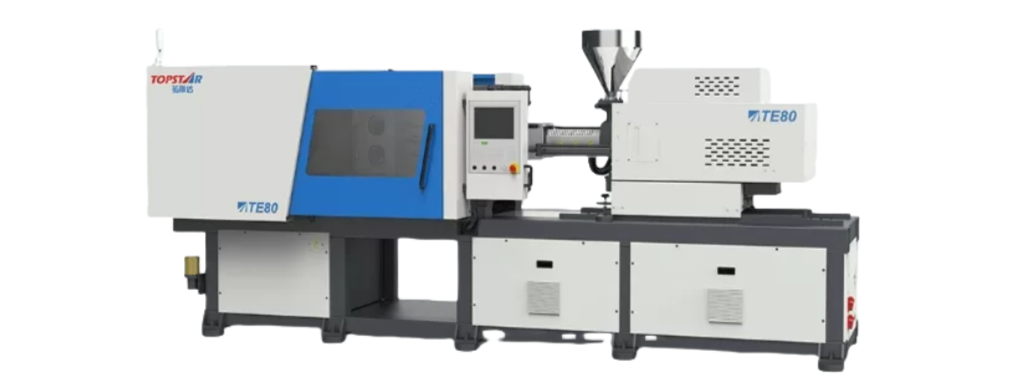
Ways to Save Energy Efficiency
Optimizing the energy efficiency of electric injection molding machines can take a multifaceted approach. Regular maintenance is essential to ensure your machine is running at peak efficiency. They themselves are also different from hydraulic machines, which require a pump to run continuously. Electric injection molding machines can switch off the motor during inactive phases. This feature significantly reduces idle energy consumption, ensuring the machine only uses power when necessary. Over time, significant energy savings can be achieved. Finally, using data from energy monitoring systems to identify patterns and trends can help manufacturers optimize machine settings.
Ultimately
The power consumption of electric injection molding machines ranges from 3.8 kWh to 17.9 kWh. Manufacturers can minimize power consumption by considering factors such as machine utilization, energy-saving features, and maintenance practices while maintaining high productivity and product quality.
TRENDING POSTS
- What factors can cause delays in the injection molding process of plastic molding machine? 2024/05/22
- Exhibition Review| Topstar participates in InterPlas Thailand 2024 2024/05/22
- Star Case | Topstar helps Santong upgrade its intelligent plant 2024/05/22
- Topstar Special | National Science and Technology Workers Day 2024/05/22
HOT TOPIC
- 3 in 1 Compact Dehumidifying Dryer
- 5-axis CNC machine
- accuracy
- Air Chillers
- all electric injection molding machine
- All-electric injection molding machines
- and overall production quality. Therefore
- AP-RubberPlas
- automated injection molding machine
- Automation changed engineering
- automation of injection molding robots
- auxiliary machine
- Bench Injection Molding Machine
- Cabinet dryer manufacturers
- Cabinet dryers
- chiller
- CNC Drilling Machine
- CNC Drilling Machines
- cnc engraving machine manufacturer
- cnc laser cutting machine manufacturer
- CNC machine
- CNC Machine Center
- CNC Machine for Sale
- CNC Machine Manufacturing
- CNC Machine Tool
- CNC machine tool product
- CNC Machining Center
- CNC wood carving machine
- Cooling system
- Cross-Walking Single Axis Servo Cylinder Robot
- Cross-Walking Single-Axis Servo Cylinder Robot
- Cross-Walking Three-Axis/Five-Axis Servo Driven Robot
- cross-walking three-axis/five-axis servo-driven robot
- Dehumidifier Dryer
- Dehumidifying Dryer
- delta parallel robot
- Desktop Injection Molding Machine
- Desktop injection molding machines
- Desktop Molding Machine
- desktop plastic injection machine
- Desktop Plastic Injection Molding Machine
- direct clamp injection molding machine
- Direct clamp injection molding machines
- Dosing & mixing system
- Drilling Centers
- Drying and dehumidification system
- drying and dehumidifying equipment
- Drying and Dehumidifying System
- drying system
- effective and efficient. Cabinet dryers are also used in other industries where large quantities of material need to be dried
- efficient injection molding machine
- elbow hydraulic injection molding machines
- electric injection molding machine
- electric injection molding machines
- etc. Among injection molding robots
- exhibition
- features of CNC machine
- Feeding And Conveying System
- Five Axis Machine Center
- Fully automatic injection molding machine
- Gathering Topstar
- giant injection molding machine
- GMU-600 5-Axis Machining Center
- Granulating & Recycling System
- Heavy duty injection molding machine
- Honeycomb rotor dehumidifier
- horizontal injection molding machine
- Horizontal Injection Molding Machines
- Horizontal Injection Moulding Machine
- Horizontal Mixer manufacturer
- How The CNC Machine Works
- hybrid injection molding machine
- hydraulic injection molding machine
- Hydraulic Injection Molding Machines
- in this article
- Industrial robot
- Industrial Robot Chinese brand
- industrial robot parts
- industrial robot supplier
- Industrial robots
- Industry Chain
- Injection Manipulator
- injection mold machines
- Injection molding
- Injection molding automation
- Injection Molding Automation Solution
- injection molding dryer
- Injection molding equipment
- injection molding hopper dryer
- Injection molding machine
- injection molding machine brand
- Injection Molding Machine Factory
- Injection Molding Machine Manufacture
- Injection molding machine manufacturer
- injection molding machine manufacturers
- Injection molding machine procurement
- injection molding machine robotic arm
- injection molding machine with a robot
- Injection molding machines
- injection molding material dehumidifying
- injection molding plant
- Injection Molding Robot
- injection molding robot arm
- Injection molding robot automation
- Injection molding robotic arm
- injection molding robots
- Injection Moulding Robots
- Injection Robot
- Injection robot arm
- Injection robot manufacturer
- Injection robot wholesale
- injection robots
- intelligent injection molding machines
- Introducing Injection Robot
- It is the best choice for drying large quantities of material at once. Cabinetmakers use these machines because they are fast
- large injection molding machine
- Learn what industrial automation and robotics is
- low speed sound-proof granulator
- machine plastic molding
- make sure to add some! Improvements (2) Keyphrase in introduction: Your keyphrase or its synonyms appear in the first paragraph of the copy
- manipulator machine
- manufacturing
- micro injection molding machine
- middle speed granulator
- Mini CNC machine manufacturers.
- Mold Temperature Control System
- mold temperature controller
- molding material Dehumidifying System
- mould temperature controller
- mould temperature controllers
- New electric injection molding machine
- nitrogen dryer manufacturer
- nitrogen dryer system manufacturer
- Oil type mold temperature controller
- open day
- Outbound links: No outbound links appear in this page. Add some! Images: No images appear on this page. Add some! Internal links: No internal links appear in this page
- PET Preform injection molding
- phone case maker machine
- phone case making machine
- plastic bottle making machine
- plastic bottle manufacturing
- plastic bucket making machine
- plastic bucket manufacturing
- Plastic chair making machine
- plastic forming equipment
- plastic hopper dryer
- plastic injection machine
- plastic injection machines
- plastic injection molding
- Plastic injection molding equipment
- Plastic injection molding machine
- Plastic Injection Molding Machines
- plastic injection robot
- Plastic Molding machine
- Plastic Molding Machines
- plastic molding press
- plastic phone case making machine
- plastic-molding machine
- powerful granulator
- Powerful Type Sound-Proof Granulator
- production of plastic seats
- Robot injection molding
- robot injection molding machine
- robot manufacturing companies
- Robotic arm for injection molding machine
- robotic injection molding machines
- robotics in injection molding
- SCARA robot
- SCARA robots
- Service-oriented manufacturing
- Servo Cylinder Robot
- servo driven robot
- Servo Driven Robots
- servo injection robots
- Servo-Driven Robot
- Setup of injection machine
- Silicone Injection Molding Machine
- six-axis industrial robot
- Stainless Hopper Dryer
- Stainless Hopper Dryers
- star club
- swing arm robot
- the choice between servo-driven robots and hydraulic robots will have a certain impact on efficiency
- the most popular injection molding machine
- the type of injection molding robot
- toggle clamp injection molding machine
- Toggle Hydraulic Injection Molding Machines
- toggle injection molding machine
- Top 10 brands of injection robots
- Topstar
- Topstar Engineering
- Topstar Industrial Robots
- Topstar injection molding intelligent
- Topstar Scara Robots
- Useful Injection molding machine
- Vertical machining centers
- volumetric type blender
- water chiller
- water chillers
- water distributor
- Water Type MoldTemperature Controller
- We often face choices when performing injection molding. We will choose the type of injection molding machine
- wholesale of injection molding machines
- x carve CNC