How long is the service life of injection molding machines?
2024/06/11 By Topstar
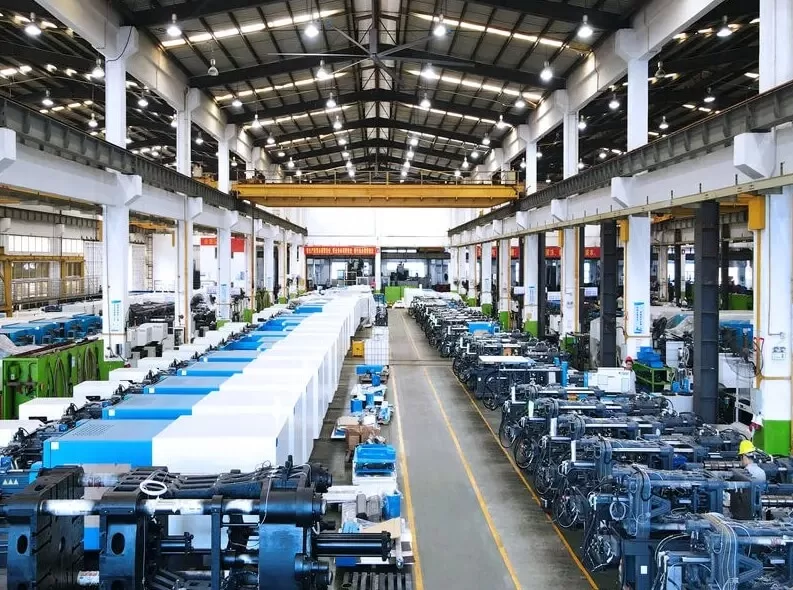
Most plastic manufacturers pay attention to the service life of injection molding machines during the procurement stage. The length of life is often also a reflection of the quality of the machine. In this guide, we will tell you how long the service life of the Topstar injection molding machine series is, as well as the factors that affect their service life and strategies to extend their service life.
Typical service life of injection molding machines
The Topstar injection molding machine series typically has a service life of 10 to 20 years. This is the feedback most of our users give, and the actual service life may differ. High-grade precision steel materials and advanced servo and hydraulic technologies are used throughout the series. The use of hardened steel parts and precision machining enhances these machines’ structural integrity and operational flexibility. In terms of design, the whole machine moves smoothly and is not prone to vibration, improving energy efficiency, greatly extending the life of mechanical parts and molds, and reducing parts wear and tear failure.
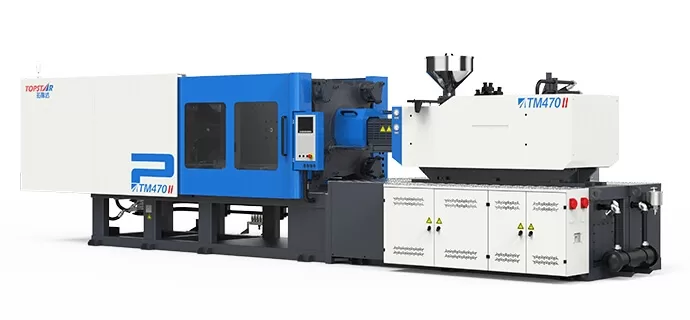
Factors affecting the service life of injection molding machines
The service life of injection molding machines varies depending on different factors. First, the quality of the machine itself. For some high-end machines, high-quality steel materials and advanced technology are usually used, which help extend the service life, the operating environment, and daily maintenance. Regular and proactive maintenance can extend the service life of injection molding machines. Usually, maintenance work such as lubrication, cleaning, inspection, and replacement of worn parts are added to daily maintenance to prevent failures.
Another critical factor is the intensity of use. Compared with machines with lower frequency of use, machines that run continuously at high speed and high load will naturally experience more wear, thereby shortening their service life. In addition, the type of processing material will also affect the service life. For example, some plastics contain abrasives like glass fiber, which will accelerate the wear of machine parts.
Technological advances extend service life
In Topstar’s injection molding machine series, self-developed servo and control systems are used to accurately control the injection process and optimize parameters such as temperature, pressure, and injection speed. Enhanced control capabilities enable consistent production quality while reducing the possibility of mechanical failure caused by process variations. In addition, the materials used in machine components also improve durability and performance. For example, the use of advanced alloys and coatings in screws and barrels also significantly improves wear and corrosion resistance. In addition, integrating injection molding robots enhances efficiency and reduces machine wear. Consistently handle repetitive tasks such as loading materials and removing finished parts. Reduced manual handling of components reduces the risk of damage and wear.
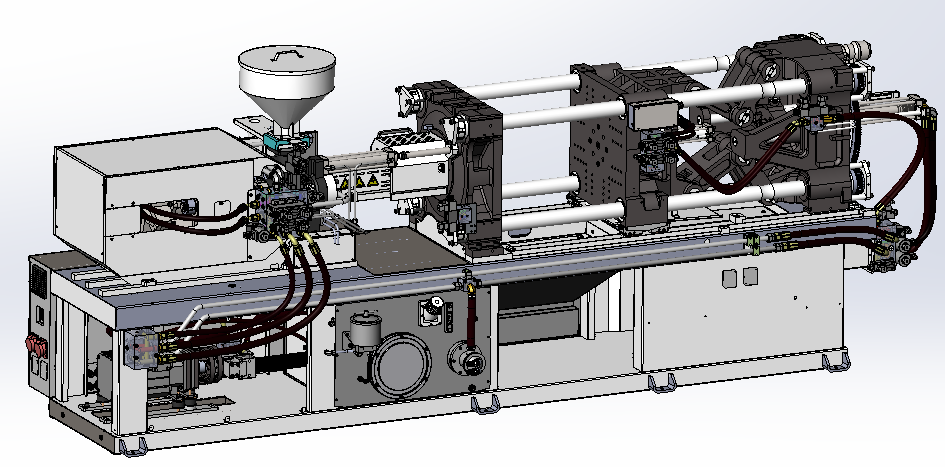
Upgrading components to extend service life
Mechanical components such as screws, barrels, and molds will experience severe wear over time. Upgrading to bimetallic barrels and wear-resistant screws can greatly improve their durability, and precision PVD alloy three-pieces are also more suitable for a wide range of plasticizing requirements. These components can withstand higher pressures and temperatures, thereby reducing wear rates. Replacing standard molds with molds made of more rigid materials or molds that have undergone surface treatment can also extend their service life. Upgrading auxiliary equipment such as cooling systems, mold control systems, and injection molding robots also helps extend the service life of injection molding machines. Improved cooling systems ensure consistent mold temperatures, reducing the thermal stress on molds and machine components, etc.
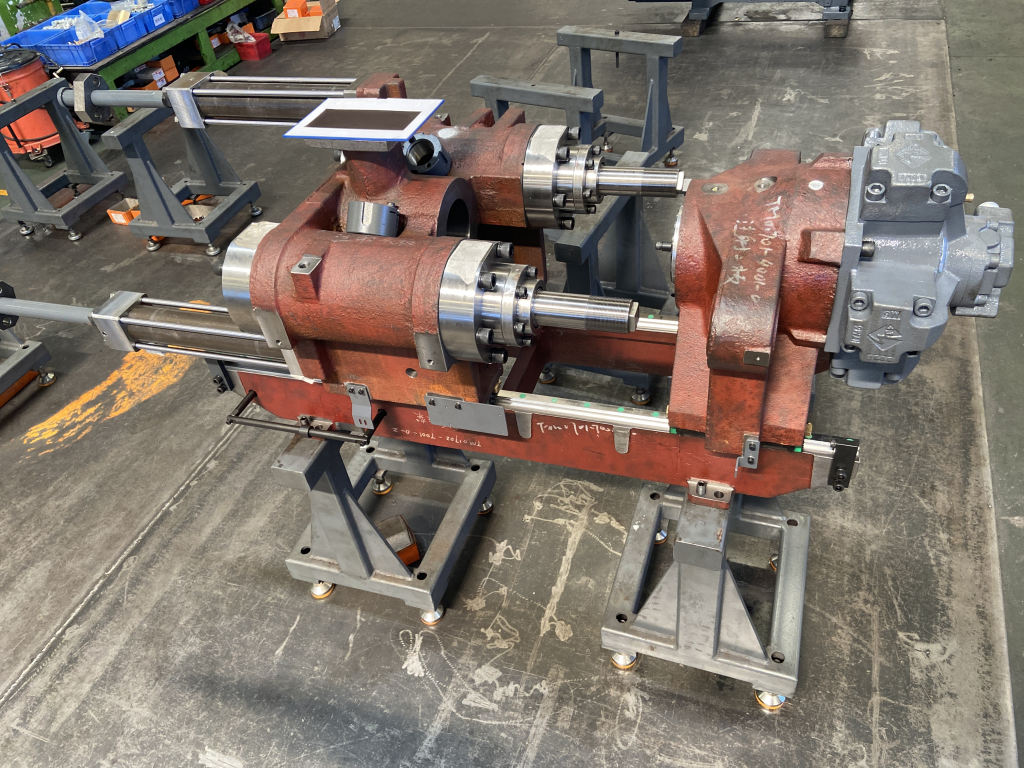
Perform regular maintenance
Performing regular maintenance on injection molding machines can also extend their life. Regular inspection, lubrication of moving parts, calibration, and replacement of worn parts can prevent minor problems from becoming big problems. Maintenance should focus not only on mechanical components but also on hydraulic and electrical systems. Ensuring the hydraulic oil is clean and at the correct level can prevent damage to pumps and valves. Regularly inspecting and cleaning cooling channels, checking coolant levels, and ensuring that pumps and fans are operating correctly can avoid failures that can cause costly downtime or machine damage.
Let your injection molding machine have a longer life
The service life of an injection molding machine is generally around 10-20 years. The machine’s service life can be significantly extended through maintenance practices, controlling operating intensity and upgrading technology. Implementing proactive maintenance strategies and upgrading components are vital to achieving this goal.
TRENDING POSTS
- What factors can cause delays in the injection molding process of plastic molding machine? 2024/06/11
- Exhibition Review| Topstar participates in InterPlas Thailand 2024 2024/06/11
- Star Case | Topstar helps Santong upgrade its intelligent plant 2024/06/11
- Topstar Special | National Science and Technology Workers Day 2024/06/11
HOT TOPIC
- 3 in 1 Compact Dehumidifying Dryer
- 5-axis CNC machine
- accuracy
- Air Chillers
- all electric injection molding machine
- All-electric injection molding machines
- and overall production quality. Therefore
- AP-RubberPlas
- automated injection molding machine
- Automation changed engineering
- automation of injection molding robots
- auxiliary machine
- Bench Injection Molding Machine
- Cabinet dryer manufacturers
- Cabinet dryers
- chiller
- CNC Drilling Machine
- CNC Drilling Machines
- cnc engraving machine manufacturer
- cnc laser cutting machine manufacturer
- CNC machine
- CNC Machine Center
- CNC Machine for Sale
- CNC Machine Manufacturing
- CNC Machine Tool
- CNC machine tool product
- CNC Machining Center
- CNC wood carving machine
- Cooling system
- Cross-Walking Single Axis Servo Cylinder Robot
- Cross-Walking Single-Axis Servo Cylinder Robot
- Cross-Walking Three-Axis/Five-Axis Servo Driven Robot
- cross-walking three-axis/five-axis servo-driven robot
- Dehumidifier Dryer
- Dehumidifying Dryer
- delta parallel robot
- Desktop Injection Molding Machine
- Desktop injection molding machines
- Desktop Molding Machine
- desktop plastic injection machine
- Desktop Plastic Injection Molding Machine
- direct clamp injection molding machine
- Direct clamp injection molding machines
- Dosing & mixing system
- Drilling Centers
- Drying and dehumidification system
- drying and dehumidifying equipment
- Drying and Dehumidifying System
- drying system
- effective and efficient. Cabinet dryers are also used in other industries where large quantities of material need to be dried
- efficient injection molding machine
- elbow hydraulic injection molding machines
- electric injection molding machine
- electric injection molding machines
- etc. Among injection molding robots
- exhibition
- features of CNC machine
- Feeding And Conveying System
- Five Axis Machine Center
- Fully automatic injection molding machine
- Gathering Topstar
- giant injection molding machine
- GMU-600 5-Axis Machining Center
- Granulating & Recycling System
- Heavy duty injection molding machine
- Honeycomb rotor dehumidifier
- horizontal injection molding machine
- Horizontal Injection Molding Machines
- Horizontal Injection Moulding Machine
- Horizontal Mixer manufacturer
- How The CNC Machine Works
- hybrid injection molding machine
- hydraulic injection molding machine
- Hydraulic Injection Molding Machines
- in this article
- Industrial robot
- Industrial Robot Chinese brand
- industrial robot parts
- industrial robot supplier
- Industrial robots
- Industry Chain
- Injection Manipulator
- injection mold machines
- Injection molding
- Injection molding automation
- Injection Molding Automation Solution
- injection molding dryer
- Injection molding equipment
- injection molding hopper dryer
- Injection molding machine
- injection molding machine brand
- Injection Molding Machine Factory
- Injection Molding Machine Manufacture
- Injection molding machine manufacturer
- injection molding machine manufacturers
- Injection molding machine procurement
- injection molding machine robotic arm
- injection molding machine with a robot
- Injection molding machines
- injection molding material dehumidifying
- injection molding plant
- Injection Molding Robot
- injection molding robot arm
- Injection molding robot automation
- Injection molding robotic arm
- injection molding robots
- Injection Moulding Robots
- Injection Robot
- Injection robot arm
- Injection robot manufacturer
- Injection robot wholesale
- injection robots
- intelligent injection molding machines
- Introducing Injection Robot
- It is the best choice for drying large quantities of material at once. Cabinetmakers use these machines because they are fast
- large injection molding machine
- Learn what industrial automation and robotics is
- low speed sound-proof granulator
- machine plastic molding
- make sure to add some! Improvements (2) Keyphrase in introduction: Your keyphrase or its synonyms appear in the first paragraph of the copy
- manipulator machine
- manufacturing
- micro injection molding machine
- middle speed granulator
- Mini CNC machine manufacturers.
- Mold Temperature Control System
- mold temperature controller
- molding material Dehumidifying System
- mould temperature controller
- mould temperature controllers
- New electric injection molding machine
- nitrogen dryer manufacturer
- nitrogen dryer system manufacturer
- Oil type mold temperature controller
- open day
- Outbound links: No outbound links appear in this page. Add some! Images: No images appear on this page. Add some! Internal links: No internal links appear in this page
- PET Preform injection molding
- phone case maker machine
- phone case making machine
- plastic bottle making machine
- plastic bottle manufacturing
- plastic bucket making machine
- plastic bucket manufacturing
- Plastic chair making machine
- plastic forming equipment
- plastic hopper dryer
- plastic injection machine
- plastic injection machines
- plastic injection molding
- Plastic injection molding equipment
- Plastic injection molding machine
- Plastic Injection Molding Machines
- plastic injection robot
- Plastic Molding machine
- Plastic Molding Machines
- plastic molding press
- plastic phone case making machine
- plastic-molding machine
- powerful granulator
- Powerful Type Sound-Proof Granulator
- production of plastic seats
- Robot injection molding
- robot injection molding machine
- robot manufacturing companies
- Robotic arm for injection molding machine
- robotic injection molding machines
- robotics in injection molding
- SCARA robot
- SCARA robots
- Service-oriented manufacturing
- Servo Cylinder Robot
- servo driven robot
- Servo Driven Robots
- servo injection robots
- Servo-Driven Robot
- Setup of injection machine
- Silicone Injection Molding Machine
- six-axis industrial robot
- Stainless Hopper Dryer
- Stainless Hopper Dryers
- star club
- swing arm robot
- the choice between servo-driven robots and hydraulic robots will have a certain impact on efficiency
- the most popular injection molding machine
- the type of injection molding robot
- toggle clamp injection molding machine
- Toggle Hydraulic Injection Molding Machines
- toggle injection molding machine
- Top 10 brands of injection robots
- Topstar
- Topstar Engineering
- Topstar Industrial Robots
- Topstar injection molding intelligent
- Topstar Scara Robots
- Useful Injection molding machine
- Vertical machining centers
- volumetric type blender
- water chiller
- water chillers
- water distributor
- Water Type MoldTemperature Controller
- We often face choices when performing injection molding. We will choose the type of injection molding machine
- wholesale of injection molding machines
- x carve CNC