How is the screw design of a all electric injection molding machine different from that of other machines?
2024/11/15 By Topstar
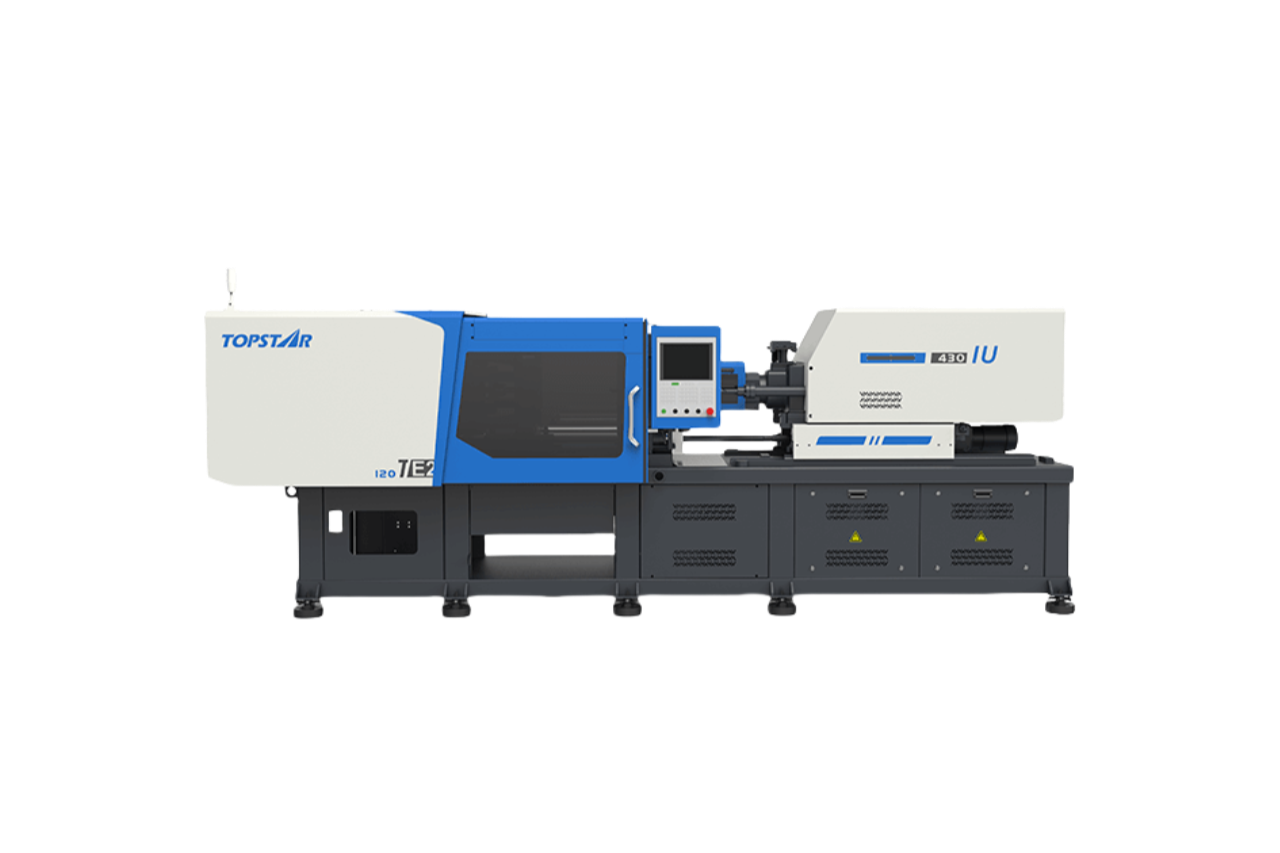
In the injection molding industry, the design of the screw in the injection molding machine plays a vital role. It has a certain impact on the quality and efficiency of the molding process. The current injection molding machine market is almost all electric injection molding machines for injection molding. Their precision, energy-saving, and control capabilities are well-suited to industries with high precision requirements. The special screw design used in them distinguishes them from traditional hydraulic and hybrid models. The unique characteristics of the screw in the all electric injection machine optimize the plasticizing, melting, and injection processes, thereby producing more consistent and precise products. This guide will explore how the screw design of the all electric injection molding machine is different from the screw design of other types of machines.
Enhanced precision and control capabilities of the full electric injection molding machine screw
The main advantage of the all electric injection molding machine is its precise control of every stage of the injection molding process, which is mainly due to the advanced screw design. The screw in the all electric machine is carefully designed to provide fine control of speed, pressure, and positioning during the injection molding process. Unlike hydraulic systems that fluctuate due to fluid dynamics, the screw in the all electric injection molding machine benefits from servo motors that provide direct and stable control. This design enables even material flow, accurate shot sizes, and consistent fill rates, which are critical for products that require tight tolerances.
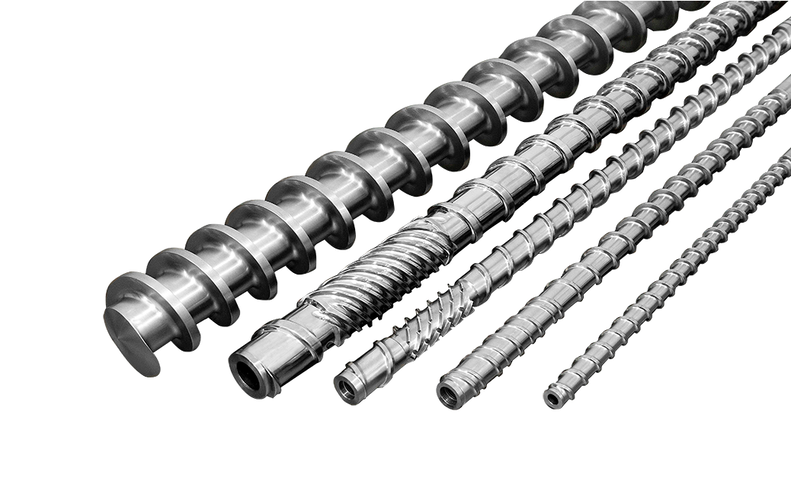
In addition, Topstar’s proprietary control systems in all-electric machines precisely adjust screw position and speed, giving operators unrivaled control over every stage of plasticization. This precision is particularly valuable for applications that require high levels of repeatability and consistency, as the screw design minimizes variation from one cycle to the next.
Energy efficiency with all electric injection molding machine screw design
Energy efficiency is a fundamental benefit of all electric injection molding machines, and screw design contributes greatly to this advantage. In traditional hydraulic presses, a hydraulic pump drives the screw, consuming a lot of energy. In contrast, a servo motor drives the screw in an all-electric machine, using energy only when needed. These machines feature a screw design optimized to work with the servo motor system, reducing energy consumption during idle time and maximizing efficiency during the plasticization phase.
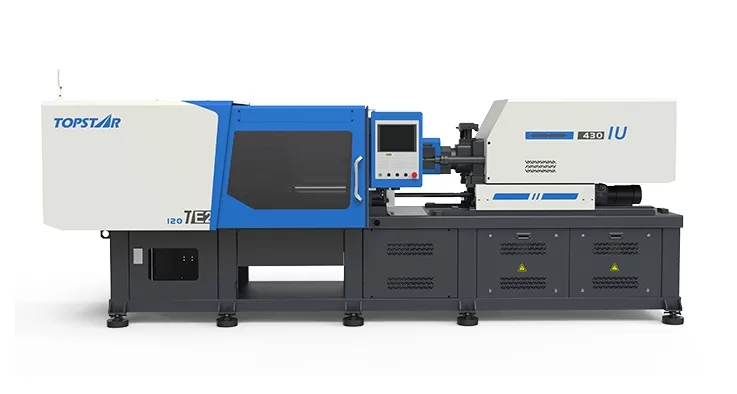
The screws in all electric machines often have features such as reduced drag and optimized barrel contact, which together reduce energy requirements. With a greater focus on design elements that improve thermal efficiency and reduce friction, screws that require less power to achieve the same (or even higher) performance as their hydraulic counterparts are also available on the market.
Speed and consistency
In a high-volume production environment, both speed and consistency are required. The screw design of the all electric injection molding machine can meet both aspects. The servo-driven screw can quickly and accurately adjust the injection speed and pressure, which is difficult to achieve with hydraulic systems. The screw design of the all-electric machine supports high-speed rotation and fast retraction, which means that the machine can run in shorter cycle times without compromising quality. The uniform motion provided by the direct control of the screw reduces shear stress on the material, resulting in consistent melt quality and smoother part surfaces. In addition, the screw design minimizes the occurrence of hesitation or material hang-up, which can slow down the production cycle of hydraulic systems.
Reduced downtime
A major advantage of all electric injection molding machines is the reduced maintenance requirements, and the screw design plays a big role in this. Hydraulic systems have complex fluid mechanisms and require regular maintenance to prevent leaks and pressure issues. In contrast, the screws in all electric machines require minimal lubrication and simpler mechanics to operate due to their servo motor design. This reduces wear parts and reduces maintenance frequency.
All electric machines feature a screw design optimized to withstand high pressures without risking hydraulic fluid leaks, which reduces downtime and minimizes production interruptions. This reliability is critical in industries where uptime is directly related to profitability, such as automotive and consumer goods manufacturing.
Enhanced Quality Control
The screw design of all electric injection molding machines ensures repeatability and consistency throughout the production process, which significantly improves quality control. The servo-driven screw precisely controls injection speed, pressure, and shot size to produce highly uniform products. In applications such as medical device manufacturing, where tight dimensional tolerances must be adhered to, the screw design of all electric machines helps reduce product defects and waste. This level of quality control is difficult to achieve with hydraulic systems because of inconsistencies caused by pressure and speed variations. By providing precise control of the screw movement, all-electric machines ensure that each cycle meets precise specifications, reducing the possibility of production errors and maintaining product quality.
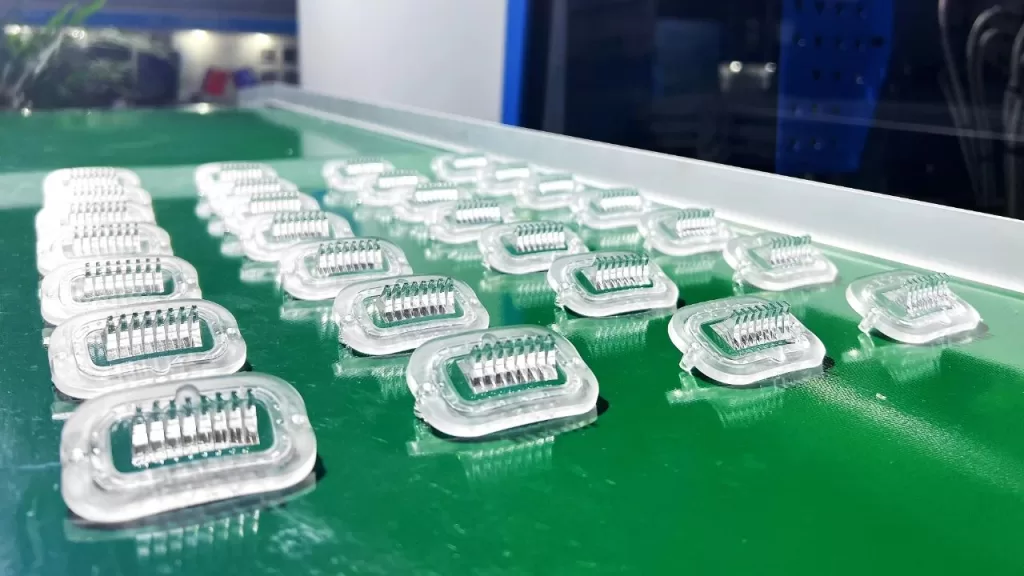
Unique Benefits
The screw design of all electric injection molding machines utilizes servo drive control, making them more precise, with lower energy consumption and lower maintenance requirements than hydraulic models. At the same time, these machines offer significant advantages to a variety of industries, especially for manufacturers that require high precision and sustainability.
TRENDING POSTS
- What factors can cause delays in the injection molding process of plastic molding machine? 2024/11/15
- Exhibition Review| Topstar participates in InterPlas Thailand 2024 2024/11/15
- Star Case | Topstar helps Santong upgrade its intelligent plant 2024/11/15
- Topstar Special | National Science and Technology Workers Day 2024/11/15
HOT TOPIC
- 3 in 1 Compact Dehumidifying Dryer
- 5-axis CNC machine
- accuracy
- Air Chillers
- all electric injection molding machine
- all electric injection molding machines
- All-electric injection molding machines
- and overall production quality. Therefore
- AP-RubberPlas
- automated injection molding machine
- Automation changed engineering
- automation of injection molding robots
- auxiliary machine
- Bench Injection Molding Machine
- Cabinet dryer manufacturers
- Cabinet dryers
- chiller
- CNC Drilling Machine
- CNC Drilling Machines
- cnc engraving machine manufacturer
- cnc laser cutting machine manufacturer
- CNC machine
- CNC Machine Center
- CNC Machine for Sale
- CNC Machine Manufacturing
- CNC Machine Tool
- CNC machine tool product
- CNC Machining Center
- CNC wood carving machine
- Cooling system
- Cross-Walking Single Axis Servo Cylinder Robot
- Cross-Walking Single-Axis Servo Cylinder Robot
- Cross-Walking Three-Axis/Five-Axis Servo Driven Robot
- cross-walking three-axis/five-axis servo-driven robot
- Dehumidifier Dryer
- Dehumidifying Dryer
- delta parallel robot
- Desktop Injection Molding Machine
- Desktop injection molding machines
- Desktop Molding Machine
- desktop plastic injection machine
- Desktop Plastic Injection Molding Machine
- direct clamp injection molding machine
- Direct clamp injection molding machines
- Dosing & mixing system
- Drilling Centers
- Drying and dehumidification system
- drying and dehumidifying equipment
- Drying and Dehumidifying System
- drying system
- effective and efficient. Cabinet dryers are also used in other industries where large quantities of material need to be dried
- efficient injection molding machine
- elbow hydraulic injection molding machines
- electric injection molding machine
- electric injection molding machines
- energy-saving injection molding machine
- etc. Among injection molding robots
- exhibition
- features of CNC machine
- Feeding And Conveying System
- Five Axis Machine Center
- Fully automatic injection molding machine
- Gathering Topstar
- giant injection molding machine
- GMU-600 5-Axis Machining Center
- Granulating & Recycling System
- Heavy duty injection molding machine
- Honeycomb rotor dehumidifier
- horizontal injection molding machine
- Horizontal Injection Molding Machines
- Horizontal Injection Moulding Machine
- Horizontal Mixer manufacturer
- How The CNC Machine Works
- hybrid injection molding machine
- hydraulic injection molding machine
- Hydraulic Injection Molding Machines
- in this article
- Industrial robot
- Industrial Robot Chinese brand
- industrial robot parts
- industrial robot supplier
- Industrial robots
- Industry Chain
- Injection Manipulator
- injection mold machines
- Injection molding
- Injection molding automation
- Injection Molding Automation Solution
- injection molding dryer
- Injection molding equipment
- injection molding hopper dryer
- Injection molding machine
- injection molding machine brand
- Injection Molding Machine Factory
- Injection Molding Machine Manufacture
- Injection molding machine manufacturer
- injection molding machine manufacturers
- Injection molding machine procurement
- injection molding machine robotic arm
- injection molding machine with a robot
- Injection molding machines
- injection molding material dehumidifying
- injection molding plant
- Injection Molding Robot
- injection molding robot arm
- Injection molding robot automation
- Injection molding robotic arm
- injection molding robots
- Injection Moulding Robots
- Injection Robot
- Injection robot arm
- Injection robot manufacturer
- Injection robot wholesale
- injection robots
- intelligent injection molding machines
- Introducing Injection Robot
- It is the best choice for drying large quantities of material at once. Cabinetmakers use these machines because they are fast
- large injection molding machine
- Learn what industrial automation and robotics is
- low speed sound-proof granulator
- machine plastic molding
- make sure to add some! Improvements (2) Keyphrase in introduction: Your keyphrase or its synonyms appear in the first paragraph of the copy
- manipulator machine
- manufacturing
- micro injection molding machine
- middle speed granulator
- Mini CNC machine manufacturers.
- Mold Temperature Control System
- mold temperature controller
- molding material Dehumidifying System
- mould temperature controller
- mould temperature controllers
- New electric injection molding machine
- nitrogen dryer manufacturer
- nitrogen dryer system manufacturer
- Oil type mold temperature controller
- open day
- Outbound links: No outbound links appear in this page. Add some! Images: No images appear on this page. Add some! Internal links: No internal links appear in this page
- PET Preform injection molding
- phone case maker machine
- phone case making machine
- plastic bottle making machine
- plastic bottle manufacturing
- plastic bucket making machine
- plastic bucket manufacturing
- Plastic chair making machine
- plastic forming equipment
- plastic hopper dryer
- plastic injection machine
- plastic injection machines
- plastic injection molding
- Plastic injection molding equipment
- Plastic injection molding machine
- Plastic Injection Molding Machines
- plastic injection robot
- Plastic Molding machine
- Plastic Molding Machines
- plastic molding press
- plastic phone case making machine
- plastic-molding machine
- powerful granulator
- Powerful Type Sound-Proof Granulator
- production of plastic seats
- Robot injection molding
- robot injection molding machine
- robot manufacturing companies
- Robotic arm for injection molding machine
- robotic injection molding machines
- robotics in injection molding
- SCARA robot
- SCARA robots
- Service-oriented manufacturing
- Servo Cylinder Robot
- servo driven robot
- Servo Driven Robots
- servo injection robots
- Servo-Driven Robot
- Setup of injection machine
- Silicone Injection Molding Machine
- six-axis industrial robot
- Stainless Hopper Dryer
- Stainless Hopper Dryers
- star club
- swing arm robot
- the choice between servo-driven robots and hydraulic robots will have a certain impact on efficiency
- the most popular injection molding machine
- the type of injection molding robot
- toggle clamp injection molding machine
- Toggle Hydraulic Injection Molding Machines
- toggle injection molding machine
- Top 10 brands of injection robots
- Topstar
- Topstar Engineering
- Topstar Industrial Robots
- Topstar injection molding intelligent
- Topstar Scara Robots
- Useful Injection molding machine
- Vertical machining centers
- volumetric type blender
- water chiller
- water chillers
- water distributor
- Water Type MoldTemperature Controller
- We often face choices when performing injection molding. We will choose the type of injection molding machine
- wholesale of injection molding machines
- x carve CNC