How energy-efficient is a mould temperature controller?
2024/06/19 By Topstar
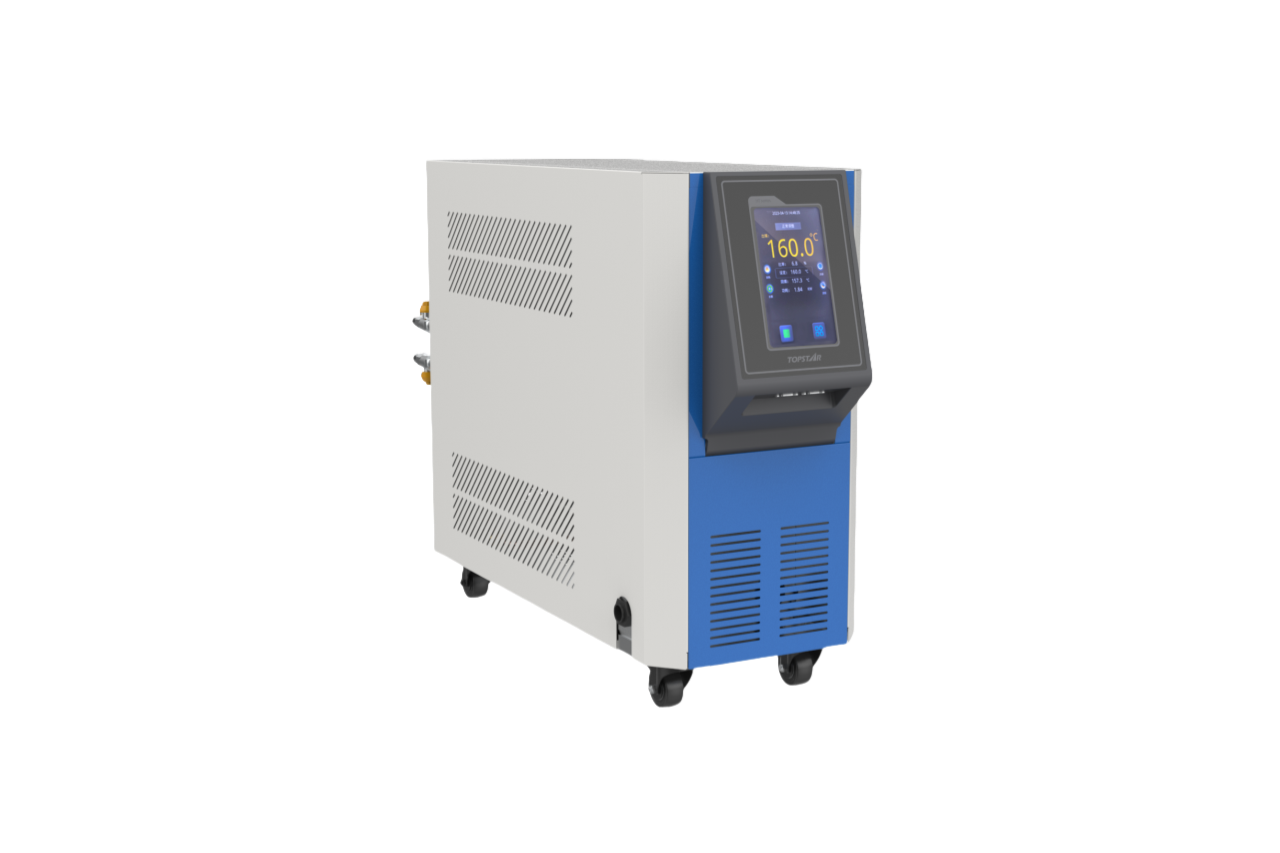
Mould temperature controller is used in many fields. In injection molding, they can achieve precise temperature control so that the injection molding machine can produce high-quality plastic parts. They play a vital role in maintaining the optimal temperature of the mold during the injection molding process, which directly affects the quality of the final product. Besides knowing their functional advantages for many users, the main thing is their energy-saving effect. Therefore, this article will also explain their energy-saving characteristics and benefits.
Mould temperature controller
This device is used to maintain the required temperature of the mold during the injection molding process. It is used for temperature regulation of plastic molding molds and extrusion molding. It usually consists of a heating and cooling unit, a temperature sensor, and a control unit. The temperature of the mold and the roller is controlled with high precision by the heating and cooling device. The main function of the controller is to circulate a heat transfer fluid (such as water or oil) through the mold to achieve the precise temperature required for molding.

The energy-saving effect of the mould temperature controller can be attributed to various factors, including efficient heat transfer fluids and optimized system design. By maintaining specific technologies and functions to keep the mold temperature constant, these controllers minimize the need for frequent heating and cooling cycles, thereby reducing energy consumption and the energy required to achieve the molding temperature.
Energy saving of mould temperature controllers
Topstar’s mould temperature controllers can save more than 35% of electricity. There are two types in total. Suppose it is a water-type mold temperature controller. In that case, water is used as the heat transfer medium to achieve heat exchange in direct (low-temperature) or indirect cooling (high-temperature type). It has high heat conduction efficiency and less pollution. Suppose oil is used as the heat transfer medium. In that case, indirect cooling is used for heat exchange, which has the advantages of a comprehensive temperature control range and good thermal stability. In addition, it has functions such as PID automatic temperature control to further save energy.
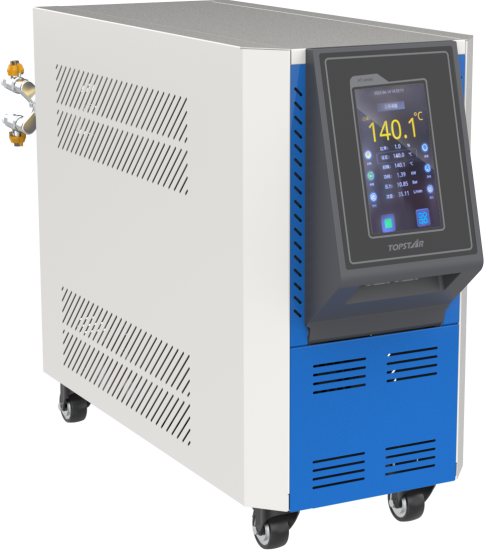
PID adjustment function
The PID adjustment function in the mold temperature controller is a control mechanism. After integration, the PID adjustment function provides a balanced and powerful temperature adjustment method. They continuously monitor the mold temperature and fine-tune the heating and cooling devices to maintain the set temperature. The best energy savings are achieved when PID parameters are correctly tuned. Accurate PID tuning results in uniform temperature distribution, shorter cycle times, and better product quality. It also minimizes thermal gradients, preventing defects such as warping, shrinkage, or incomplete filling. By maintaining consistent mold temperatures, PID tuning improves the molding process’s efficiency and reliability, increasing productivity and saving energy.
Efficient heat transfer fluids
Heat transfer fluids such as water and oil are commonly used in mold temperature controllers to transfer heat. The heat transfer efficiency of these two fluids directly affects the energy consumption of the mold temperature controller.
Water is one of the most efficient heat transfer fluids because it has a high specific heat capacity and thermal conductivity. Water can absorb and transfer a large amount of heat with minimal energy input, requiring energy to reach the desired mold temperature. Therefore, water-based mold temperature controllers are highly energy efficient. Oil-based mold temperature controllers are another commonly used heat transfer fluid. Still, they have the advantage of higher operating temperatures and lower viscosities and advances in heat transfer fluid technology have made it possible to minimize energy consumption.
Clever heat dissipation channel design
The mould temperature controller adopts the multi-channel heat dissipation structure design, and the coolant flows through multiple paths within the mold. This increases the surface area for heat exchange and improves heat dissipation efficiency. Topstar turbulence inducers are integrated into the channels to enhance the heat transfer rate. These inducers induce turbulence in the coolant flow, destroy the thermal boundary layer, and increase the convective heat transfer coefficient. In addition, a spiral channel design is used to extend the path length of the coolant in the mold. This extended flow path ensures more thorough heat exchange, reduces hot spots, and promotes uniform cooling. Most importantly, Topstar uses molds and water channels made of high thermal conductivity materials to ensure that heat can be conducted quickly, minimizing thermal lag to achieve energy-saving effects.
Essential equipment in the injection molding process
The mold temperature controller is essential in injection molding and can provide precise temperature control. In addition to its functional advantages, the mold temperature controller is also very energy-efficient. Its energy-saving performance is achieved through the PID adjustment function, efficient heat transfer fluid, etc., and the power-saving rate can reach more than 35%.
TRENDING POSTS
- What factors can cause delays in the injection molding process of plastic molding machine? 2024/06/19
- Exhibition Review| Topstar participates in InterPlas Thailand 2024 2024/06/19
- Star Case | Topstar helps Santong upgrade its intelligent plant 2024/06/19
- Topstar Special | National Science and Technology Workers Day 2024/06/19
HOT TOPIC
- .ervo motor-driven linear robots
- 3 axis robot
- 3 axis robots
- 3 in 1 Compact Dehumidifying Dryer
- 3-axis robot
- 3-axis robots
- 5-axis CNC machine
- accuracy
- Air Chillers
- all electric injection molding machine
- all electric injection molding machines
- All-electric injection molding machines
- and overall production quality. Therefore
- AP-RubberPlas
- automated injection molding machine
- Automation changed engineering
- automation of injection molding robots
- auxiliary machine
- Bench Injection Molding Machine
- Cabinet dryer manufacturers
- Cabinet dryers
- chiller
- CNC Drilling Machine
- CNC Drilling Machines
- cnc engraving machine manufacturer
- cnc laser cutting machine manufacturer
- CNC machine
- CNC Machine Center
- CNC Machine for Sale
- CNC Machine Manufacturing
- CNC Machine Tool
- CNC machine tool product
- CNC Machining Center
- CNC wood carving machine
- Cooling system
- Cross-Walking Single Axis Servo Cylinder Robot
- Cross-Walking Single-Axis Servo Cylinder Robot
- Cross-Walking Three-Axis/Five-Axis Servo Driven Robot
- cross-walking three-axis/five-axis servo-driven robot
- Dehumidifier Dryer
- Dehumidifying Dryer
- delta parallel robot
- Desktop Injection Molding Machine
- Desktop injection molding machines
- Desktop Molding Machine
- desktop plastic injection machine
- Desktop Plastic Injection Molding Machine
- direct clamp injection molding machine
- Direct clamp injection molding machines
- Dosing & mixing system
- Drilling Centers
- Drying and dehumidification system
- drying and dehumidifying equipment
- Drying and Dehumidifying System
- drying system
- effective and efficient. Cabinet dryers are also used in other industries where large quantities of material need to be dried
- efficient injection molding machine
- elbow hydraulic injection molding machines
- electric injection molding machine
- electric injection molding machines
- energy-efficient injection molding robot
- energy-saving injection molding machine
- etc. Among injection molding robots
- exhibition
- features of CNC machine
- Feeding And Conveying System
- Five Axis Machine Center
- Fully automatic injection molding machine
- Gathering Topstar
- giant injection molding machine
- GMU-600 5-Axis Machining Center
- Granulating & Recycling System
- Heavy duty injection molding machine
- High-precision electric molding machines
- high-precision plastic molding machines
- high-speed all electric injection molding machine
- Honeycomb rotor dehumidifier
- horizontal injection molding machine
- Horizontal Injection Molding Machines
- Horizontal Injection Moulding Machine
- Horizontal Mixer manufacturer
- How The CNC Machine Works
- hybrid injection molding machine
- hydraulic injection molding machine
- Hydraulic Injection Molding Machines
- in this article
- Industrial robot
- Industrial Robot Chinese brand
- industrial robot parts
- industrial robot supplier
- Industrial robots
- Industry Chain
- Injection Manipulator
- injection manipulator robot
- injection mold machines
- Injection molding
- Injection molding automation
- Injection Molding Automation Solution
- injection molding dryer
- Injection molding equipment
- injection molding hopper dryer
- Injection molding machine
- injection molding machine brand
- Injection Molding Machine Factory
- Injection Molding Machine Manufacture
- Injection molding machine manufacturer
- injection molding machine manufacturers
- Injection molding machine procurement
- injection molding machine robotic arm
- injection molding machine with a robot
- Injection molding machines
- injection molding material dehumidifying
- injection molding plant
- Injection Molding Robot
- injection molding robot arm
- Injection molding robot automation
- Injection molding robotic arm
- injection molding robots
- Injection moulding machine
- Injection Moulding Robots
- Injection Robot
- Injection robot arm
- Injection robot manufacturer
- Injection robot wholesale
- injection robots
- intelligent injection molding machines
- Introducing Injection Robot
- It is the best choice for drying large quantities of material at once. Cabinetmakers use these machines because they are fast
- large injection molding machine
- Learn what industrial automation and robotics is
- linear robot
- linear robots
- low speed sound-proof granulator
- machine plastic molding
- make sure to add some! Improvements (2) Keyphrase in introduction: Your keyphrase or its synonyms appear in the first paragraph of the copy
- manipulator machine
- manufacturing
- medical grade injection molding machines
- medical injection molding machine
- medical injection molding machines
- micro injection molding machine
- middle speed granulator
- Mini CNC machine manufacturers.
- Mold Temperature Control System
- mold temperature controller
- mold temperature controllers
- molding material Dehumidifying System
- mould temperature control system
- mould temperature controller
- mould temperature controllers
- New electric injection molding machine
- nitrogen dryer manufacturer
- nitrogen dryer system manufacturer
- Oil type mold temperature controller
- Oil type mold temperature controllers
- open day
- Outbound links: No outbound links appear in this page. Add some! Images: No images appear on this page. Add some! Internal links: No internal links appear in this page
- PET Preform injection molding
- phone case maker machine
- phone case making machine
- plastic bottle making machine
- plastic bottle manufacturing
- plastic bucket making machine
- plastic bucket manufacturing
- Plastic chair making machine
- plastic forming equipment
- plastic hopper dryer
- plastic injection machine
- plastic injection machines
- plastic injection molding
- Plastic injection molding equipment
- Plastic injection molding machine
- Plastic Injection Molding Machines
- plastic injection moulding machine
- plastic injection robot
- Plastic Molding machine
- Plastic Molding Machines
- plastic molding press
- plastic moulding machine
- plastic phone case making machine
- plastic-molding machine
- powerful granulator
- Powerful Type Sound-Proof Granulator
- precision injection molding
- precision injection molding machines
- production of plastic seats
- pure water mould temperature controller
- Robot injection molding
- robot injection molding machine
- robot manufacturing companies
- Robotic arm for injection molding machine
- robotic injection molding machines
- robotics in injection molding
- SCARA robot
- SCARA robots
- Service-oriented manufacturing
- Servo Cylinder Robot
- servo driven robot
- Servo Driven Robots
- servo injection robots
- servo motor-driven linear robots
- servo-driven 3-axis robot
- Servo-Driven Robot
- Setup of injection machine
- Silicone Injection Molding Machine
- six-axis industrial robot
- Stainless Hopper Dryer
- Stainless Hopper Dryers
- star club
- swing arm robot
- take-out robots
- the choice between servo-driven robots and hydraulic robots will have a certain impact on efficiency
- the most popular injection molding machine
- the type of injection molding robot
- toggle clamp injection molding machine
- Toggle Hydraulic Injection Molding Machines
- toggle injection molding machine
- Top 10 brands of injection robots
- Topstar
- Topstar Engineering
- Topstar Industrial Robots
- Topstar injection molding intelligent
- Topstar Scara Robots
- Useful Injection molding machine
- Vertical machining centers
- volumetric type blender
- water chiller
- water chillers
- water distributor
- water type mold temperature controller
- Water Type MoldTemperature Controller
- Water-Type Mould Temperature Controllers
- We often face choices when performing injection molding. We will choose the type of injection molding machine
- wholesale of injection molding machines
- x carve CNC