How do you reduce your production costs with an injection molding machine?
2024/10/25 By Topstar
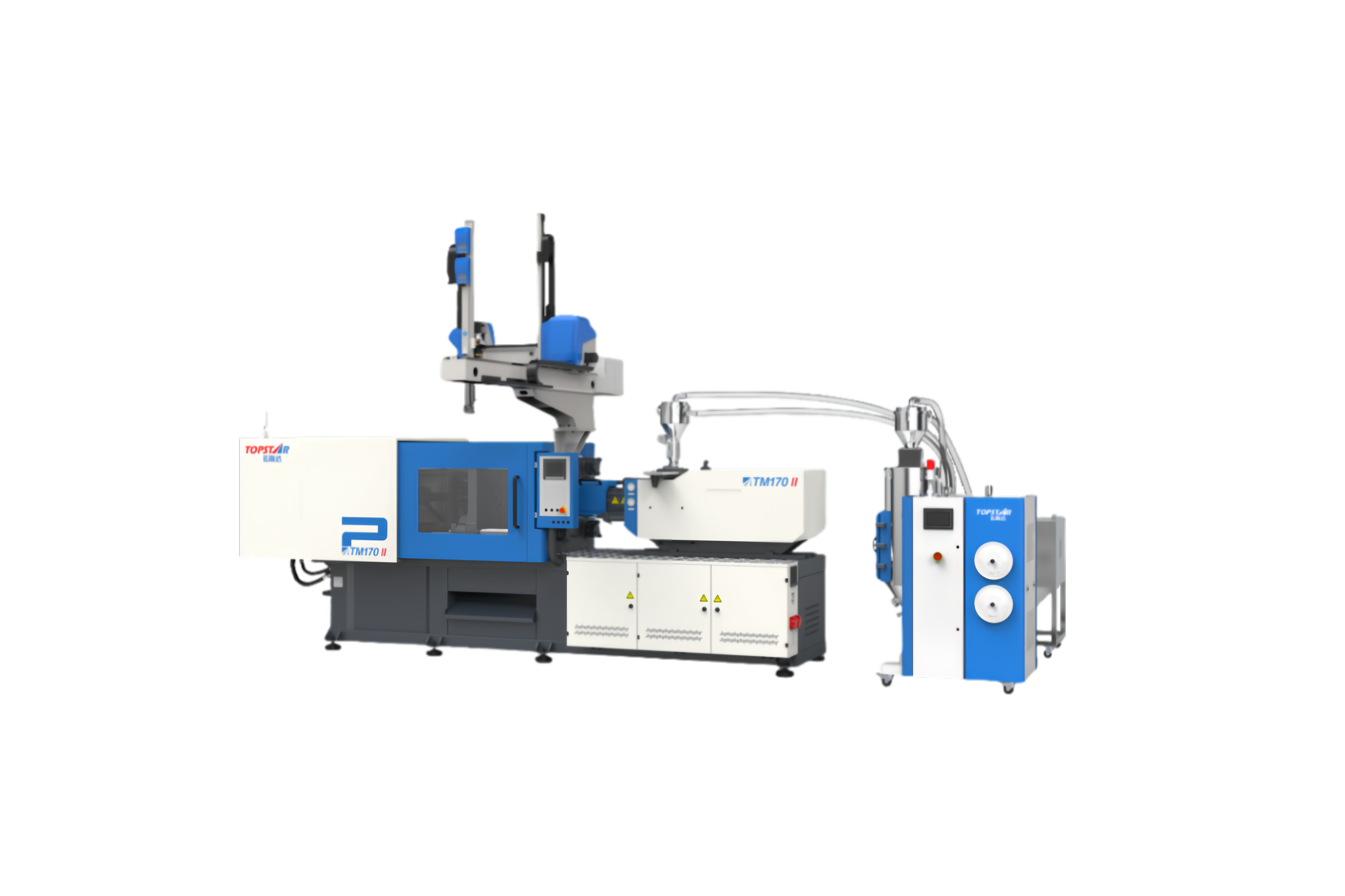
Some large manufacturing companies are faced with the problem of unnecessary production costs, which will affect not only the output but also the final revenue. On the one hand, there is an increase in labour costs, and on the other hand, there is an impact on equipment performance, so this problem must be solved fundamentally. As an injection molding machine manufacturer that can provide injection molding solutions, Topstar will solve this problem through a complete set of injection molding equipment and systems. First of all, we start with the injection molding machine. The injection molding machine is a necessary equipment for companies that rely on large-scale production of plastic parts.
Use injection molding machines to improve production efficiency.
The most direct way to reduce the production cost of injection molding is to upgrade existing equipment. In the case of Industry 4.0, automated workshops have become very common. Topstar proposed the “integrated injection molding process” concept on this basis. The “integrated process machine” realizes the integration of the main machine, auxiliary machine, and automated control through an integrated and open system, thereby significantly improving the efficiency of the production cycle. Traditionally, there is a problem of independent operation between different links, which requires manual debugging and intervention, reducing production efficiency.
Therefore, the TM ll and TE ll series of injection molding machines were developed. By integrating various links into one system, the technical coordination between the injection molding machine and peripheral auxiliary equipment, injection molding robots, mold temperature controllers, and other equipment can be achieved, which can reduce the number of equipment debugging times for front-line operators, especially for those industries with clean production requirements. The effect is more significant.
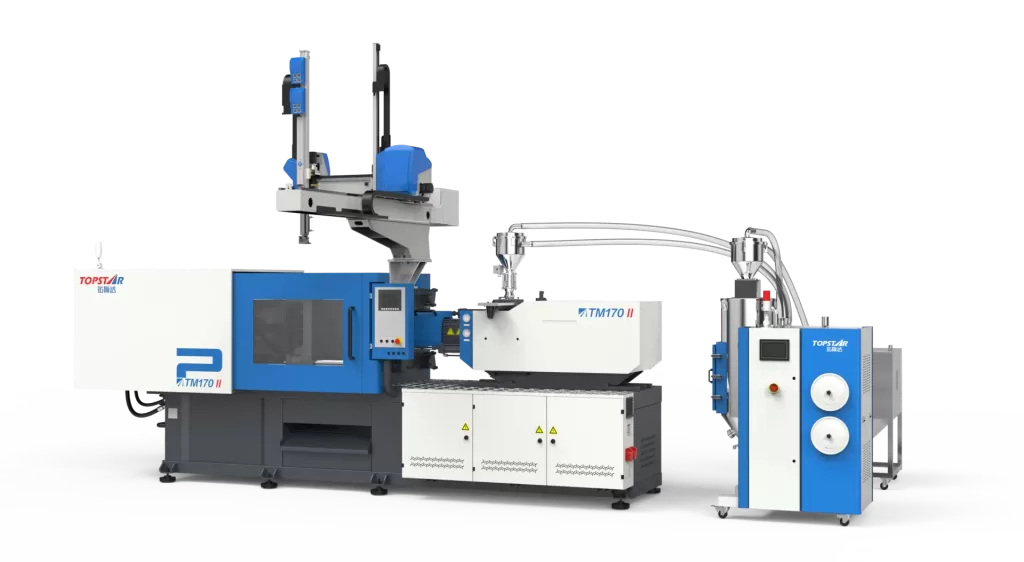
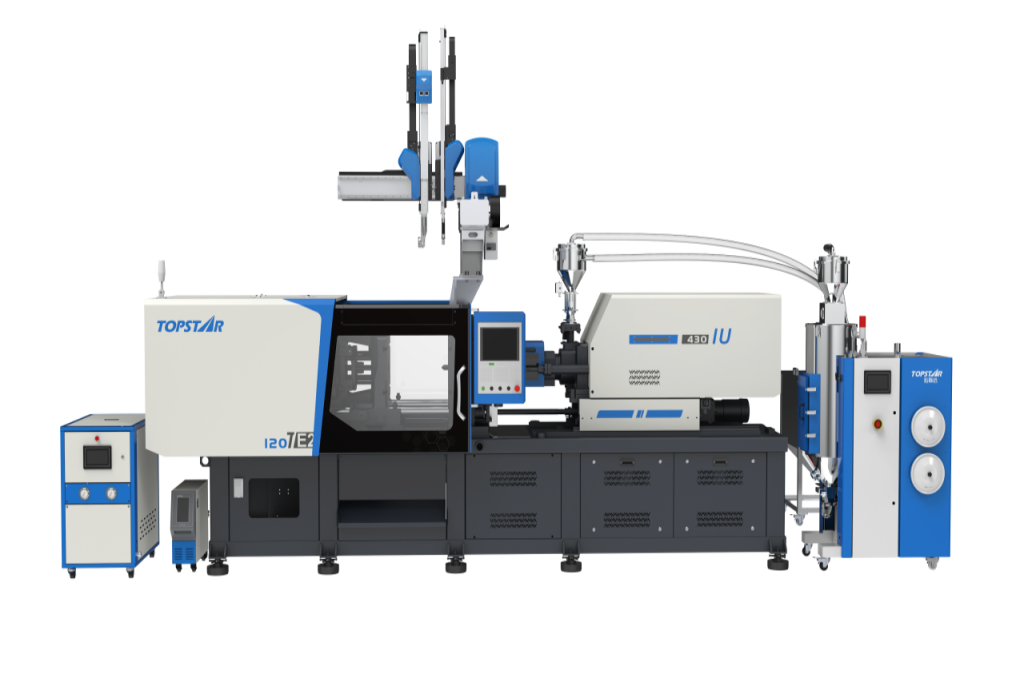
Adopting application integration technology
The TM II and TE II series integrate injection molding machines with injection molding robots and auxiliary machine systems. Users can directly obtain the operating data of auxiliary equipment on the injection molding machine, making operation more convenient. This integration allows users to access and monitor the operating data of various auxiliary equipment directly from the control panel of the injection molding machine. By integrating all operating data into a single interface, operators can manage the entire production process more effectively, reducing the need for separate monitoring systems and simplifying workflows.
For example, the system instantly displays real-time data from auxiliary equipment like mold temperature controller, conveyors, or drying systems, enabling operators to adjust quickly based on real-time performance indicators. This approach improves operational accuracy, minimizes downtime, enhances productivity, and ensures all components synchronize for optimal performance. In addition, the integrated system also shortens the learning cycle for new operators. Workers do not need to be familiar with multiple machines and interfaces but only focus on mastering one comprehensive system, improving training efficiency.
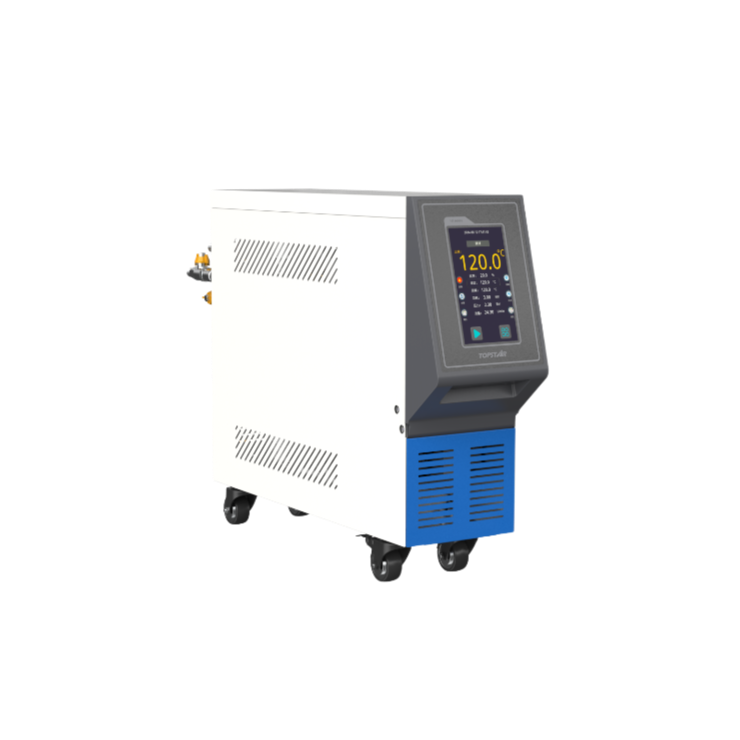
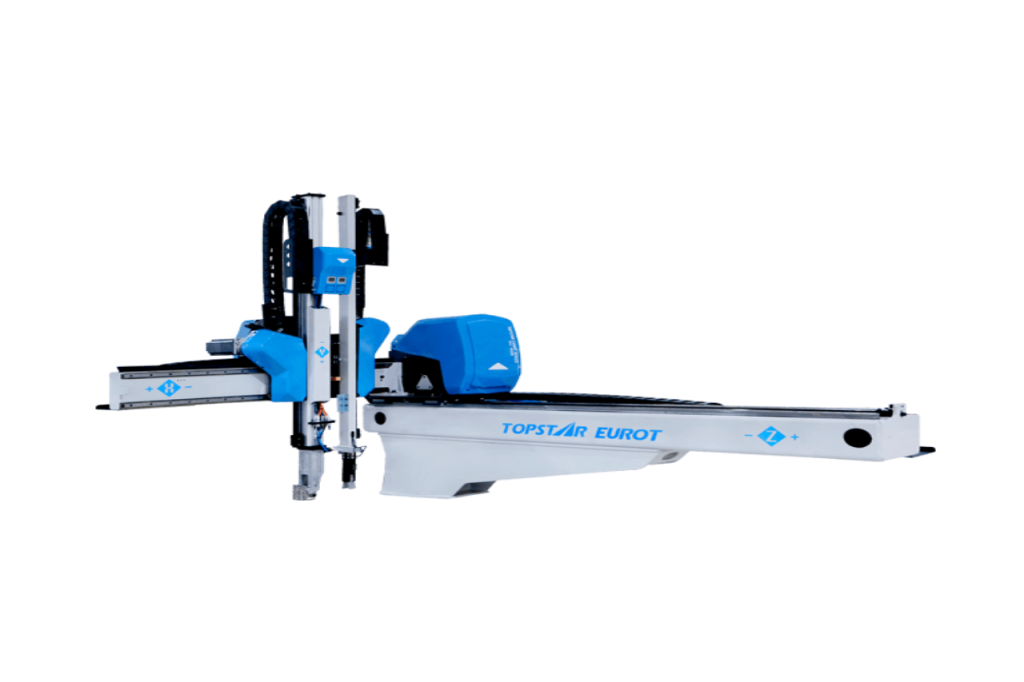
Automatic compensation function for mold opening position
The automatic compensation function for the mold opening position of the injection molding robot enables the robot to accurately grasp and place parts during high-speed mold opening operation, making production more stable and efficient. In a high-speed manufacturing environment, maintaining accuracy during mold opening is critical to prevent defects and ensure proper processing of each part.
Integrating this automatic compensation function helps solve the challenges of rapid movement during the mold opening, sometimes leading to misalignment or incomplete part processing in less advanced systems. In the TM II and TE II series, the injection molding robot adjusts in real time, automatically correcting any deviation in the mold opening position and ensuring unparalleled precision in picking up and placing parts. This minimizes the risk of production errors, reduces material waste, and increases overall output in the manufacturing process.
Optimize injection molding energy consumption.
Energy costs are essential in overall production expenses, and reducing energy consumption is a crucial way to reduce costs. The TE ll series electric injection molding machine has a high energy-saving effect and consumes significantly less electricity than traditional hydraulic presses.
Electric injection molding machines use servo motors that consume power only when necessary, which means more efficient energy use during the production cycle. This difference in energy use can bring significant savings in the long term, especially for manufacturers with long production cycles. In addition, they are all equipped with energy monitoring systems that enable companies to track and analyze energy consumption in real time. This data allows companies to identify opportunities for further energy savings, such as adjusting machine settings or optimizing production plans to reduce peak energy use.
Improve the quality of production delivery.
When you work with Topstar, we continuously operate all equipment for more than 48 hours before delivery, test it using a 10,000-level statistical system, and conduct two full-cycle tests on the entire machine. Topstar pays more attention to customers’ production and operation results and provides standardized services for the entire cycle of equipment, not just a single device. This comprehensive solution can meet the needs of the three parties of operation, management, and operation for production, improved management, and efficient production. Regarding quality management, we have integrated parts and product information by connecting the supply chain, manufacturing, and product traceability management. Ensure that every link can bring you an improvement in production efficiency.
Make your production more cost-effective.
Injection molding machines are a powerful tool for reducing production costs in all walks of life. Automation can improve production efficiency, reduce waste, reduce labor and energy costs, and improve product quality through an integrated injection molding machine process and the intelligence of related peripheral auxiliary equipment. Companies can use injection molding equipment to optimize operations and improve profitability in automotive, medical equipment, consumer goods, or other industries.
TRENDING POSTS
- What factors can cause delays in the injection molding process of plastic molding machine? 2024/10/25
- Exhibition Review| Topstar participates in InterPlas Thailand 2024 2024/10/25
- Star Case | Topstar helps Santong upgrade its intelligent plant 2024/10/25
- Topstar Special | National Science and Technology Workers Day 2024/10/25
HOT TOPIC
- 3 in 1 Compact Dehumidifying Dryer
- 5-axis CNC machine
- accuracy
- Air Chillers
- all electric injection molding machine
- all electric injection molding machines
- All-electric injection molding machines
- and overall production quality. Therefore
- AP-RubberPlas
- automated injection molding machine
- Automation changed engineering
- automation of injection molding robots
- auxiliary machine
- Bench Injection Molding Machine
- Cabinet dryer manufacturers
- Cabinet dryers
- chiller
- CNC Drilling Machine
- CNC Drilling Machines
- cnc engraving machine manufacturer
- cnc laser cutting machine manufacturer
- CNC machine
- CNC Machine Center
- CNC Machine for Sale
- CNC Machine Manufacturing
- CNC Machine Tool
- CNC machine tool product
- CNC Machining Center
- CNC wood carving machine
- Cooling system
- Cross-Walking Single Axis Servo Cylinder Robot
- Cross-Walking Single-Axis Servo Cylinder Robot
- Cross-Walking Three-Axis/Five-Axis Servo Driven Robot
- cross-walking three-axis/five-axis servo-driven robot
- Dehumidifier Dryer
- Dehumidifying Dryer
- delta parallel robot
- Desktop Injection Molding Machine
- Desktop injection molding machines
- Desktop Molding Machine
- desktop plastic injection machine
- Desktop Plastic Injection Molding Machine
- direct clamp injection molding machine
- Direct clamp injection molding machines
- Dosing & mixing system
- Drilling Centers
- Drying and dehumidification system
- drying and dehumidifying equipment
- Drying and Dehumidifying System
- drying system
- effective and efficient. Cabinet dryers are also used in other industries where large quantities of material need to be dried
- efficient injection molding machine
- elbow hydraulic injection molding machines
- electric injection molding machine
- electric injection molding machines
- energy-saving injection molding machine
- etc. Among injection molding robots
- exhibition
- features of CNC machine
- Feeding And Conveying System
- Five Axis Machine Center
- Fully automatic injection molding machine
- Gathering Topstar
- giant injection molding machine
- GMU-600 5-Axis Machining Center
- Granulating & Recycling System
- Heavy duty injection molding machine
- Honeycomb rotor dehumidifier
- horizontal injection molding machine
- Horizontal Injection Molding Machines
- Horizontal Injection Moulding Machine
- Horizontal Mixer manufacturer
- How The CNC Machine Works
- hybrid injection molding machine
- hydraulic injection molding machine
- Hydraulic Injection Molding Machines
- in this article
- Industrial robot
- Industrial Robot Chinese brand
- industrial robot parts
- industrial robot supplier
- Industrial robots
- Industry Chain
- Injection Manipulator
- injection mold machines
- Injection molding
- Injection molding automation
- Injection Molding Automation Solution
- injection molding dryer
- Injection molding equipment
- injection molding hopper dryer
- Injection molding machine
- injection molding machine brand
- Injection Molding Machine Factory
- Injection Molding Machine Manufacture
- Injection molding machine manufacturer
- injection molding machine manufacturers
- Injection molding machine procurement
- injection molding machine robotic arm
- injection molding machine with a robot
- Injection molding machines
- injection molding material dehumidifying
- injection molding plant
- Injection Molding Robot
- injection molding robot arm
- Injection molding robot automation
- Injection molding robotic arm
- injection molding robots
- Injection Moulding Robots
- Injection Robot
- Injection robot arm
- Injection robot manufacturer
- Injection robot wholesale
- injection robots
- intelligent injection molding machines
- Introducing Injection Robot
- It is the best choice for drying large quantities of material at once. Cabinetmakers use these machines because they are fast
- large injection molding machine
- Learn what industrial automation and robotics is
- low speed sound-proof granulator
- machine plastic molding
- make sure to add some! Improvements (2) Keyphrase in introduction: Your keyphrase or its synonyms appear in the first paragraph of the copy
- manipulator machine
- manufacturing
- micro injection molding machine
- middle speed granulator
- Mini CNC machine manufacturers.
- Mold Temperature Control System
- mold temperature controller
- molding material Dehumidifying System
- mould temperature controller
- mould temperature controllers
- New electric injection molding machine
- nitrogen dryer manufacturer
- nitrogen dryer system manufacturer
- Oil type mold temperature controller
- open day
- Outbound links: No outbound links appear in this page. Add some! Images: No images appear on this page. Add some! Internal links: No internal links appear in this page
- PET Preform injection molding
- phone case maker machine
- phone case making machine
- plastic bottle making machine
- plastic bottle manufacturing
- plastic bucket making machine
- plastic bucket manufacturing
- Plastic chair making machine
- plastic forming equipment
- plastic hopper dryer
- plastic injection machine
- plastic injection machines
- plastic injection molding
- Plastic injection molding equipment
- Plastic injection molding machine
- Plastic Injection Molding Machines
- plastic injection robot
- Plastic Molding machine
- Plastic Molding Machines
- plastic molding press
- plastic phone case making machine
- plastic-molding machine
- powerful granulator
- Powerful Type Sound-Proof Granulator
- production of plastic seats
- Robot injection molding
- robot injection molding machine
- robot manufacturing companies
- Robotic arm for injection molding machine
- robotic injection molding machines
- robotics in injection molding
- SCARA robot
- SCARA robots
- Service-oriented manufacturing
- Servo Cylinder Robot
- servo driven robot
- Servo Driven Robots
- servo injection robots
- Servo-Driven Robot
- Setup of injection machine
- Silicone Injection Molding Machine
- six-axis industrial robot
- Stainless Hopper Dryer
- Stainless Hopper Dryers
- star club
- swing arm robot
- the choice between servo-driven robots and hydraulic robots will have a certain impact on efficiency
- the most popular injection molding machine
- the type of injection molding robot
- toggle clamp injection molding machine
- Toggle Hydraulic Injection Molding Machines
- toggle injection molding machine
- Top 10 brands of injection robots
- Topstar
- Topstar Engineering
- Topstar Industrial Robots
- Topstar injection molding intelligent
- Topstar Scara Robots
- Useful Injection molding machine
- Vertical machining centers
- volumetric type blender
- water chiller
- water chillers
- water distributor
- Water Type MoldTemperature Controller
- We often face choices when performing injection molding. We will choose the type of injection molding machine
- wholesale of injection molding machines
- x carve CNC