How do you reduce waste with an efficient injection molding machine?
2024/06/26 By Topstar
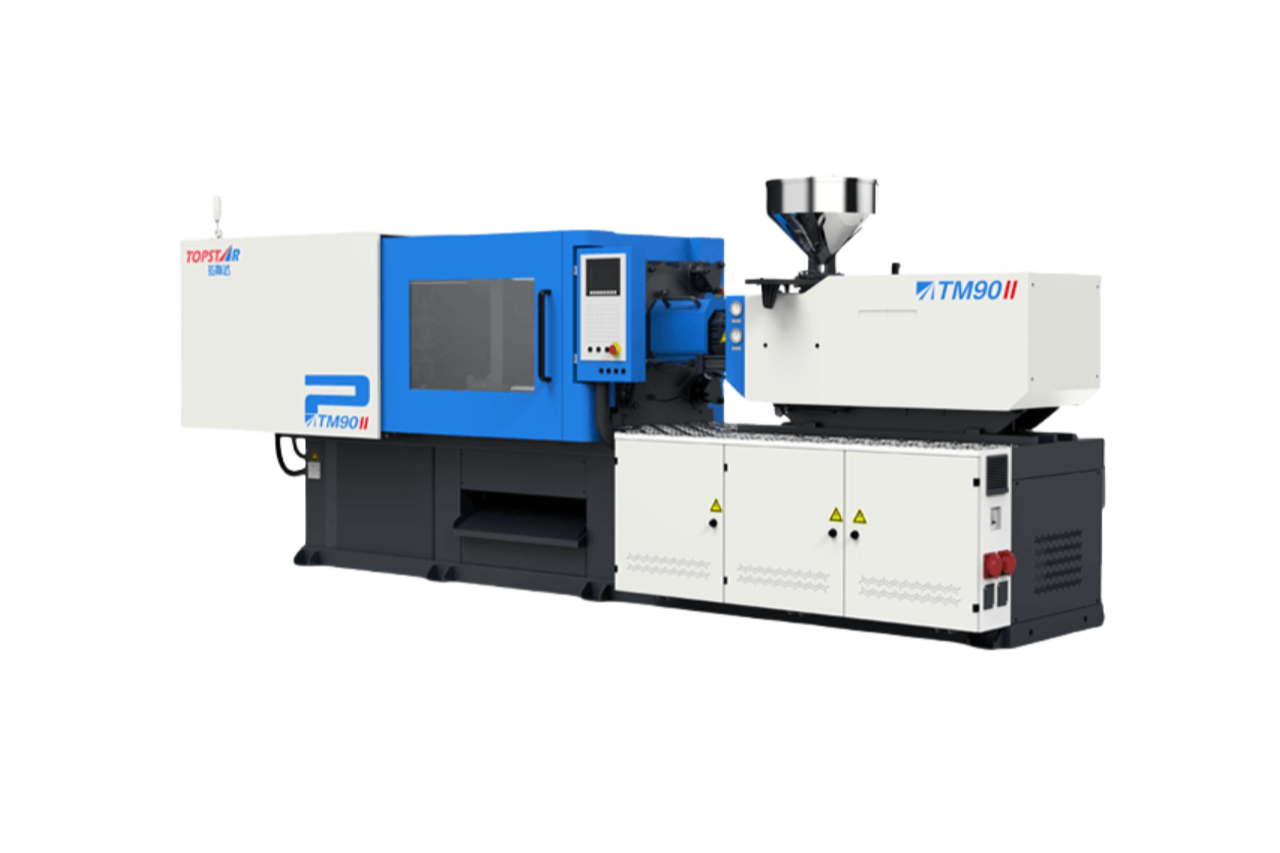
In the manufacturing industry, there is waste to varying degrees every day. The cause of the waste may be poor production technology, failure of equipment parts, and other problems. An efficient injection molding machine can minimize material waste, energy consumption, and production time, achieved through a series of technologies in the injection molding industry. This guide will teach users and consumers how to use them to reduce waste.
Advanced technologies for efficient injection molding machines
First, incorporating advanced technologies into efficient injection molding machines is a key driver for reducing waste. These technologies improve machine performance, increase precision, and provide better control over the molding process.
Automatic compensation for mold opening position
The high-efficiency injection molding machines of Tosda are equipped with robots as standard, which have the function of automatic compensation for the mold opening position of the robot. The robot can accurately grasp and place parts during high-speed mold opening operation, making production more stable and efficient. Precise grasping can reduce the waste of time and materials. At the same time, the host computer system also integrates auxiliary machines such as mould temperature controller, hopper dryer, and dehumidifier.
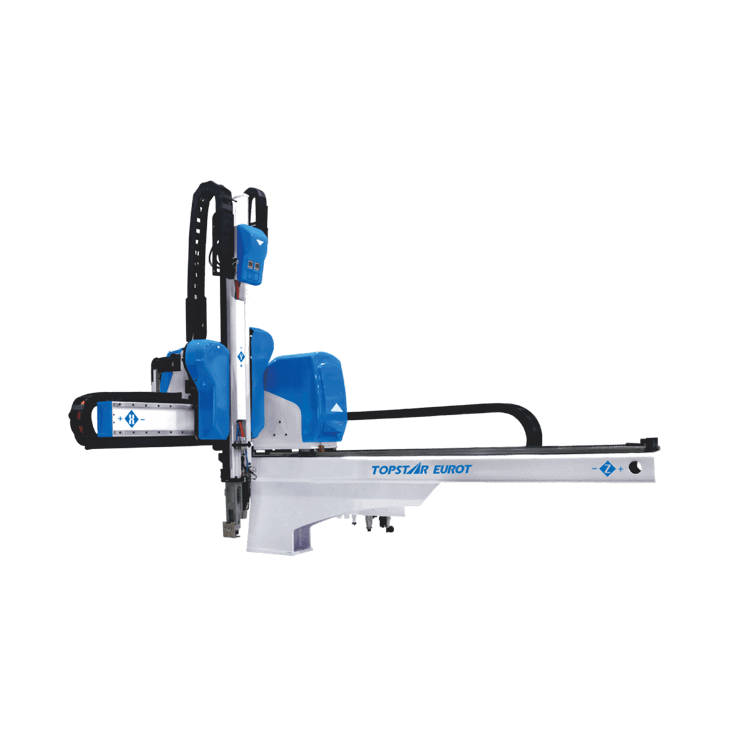
Using double-shot cylinders with linear guides
The double-shot cylinder can accurately position and inject different materials into the mold. This ensures that the materials are placed precisely where needed, reducing the possibility of overflow, underflow, and other defects that lead to material waste. At the same time, it is possible to produce multiple material parts in one molding cycle, so there is no need to assemble separate components. Multiple molding cycles reduce the waste generated and the associated gates, runners, and defective parts.
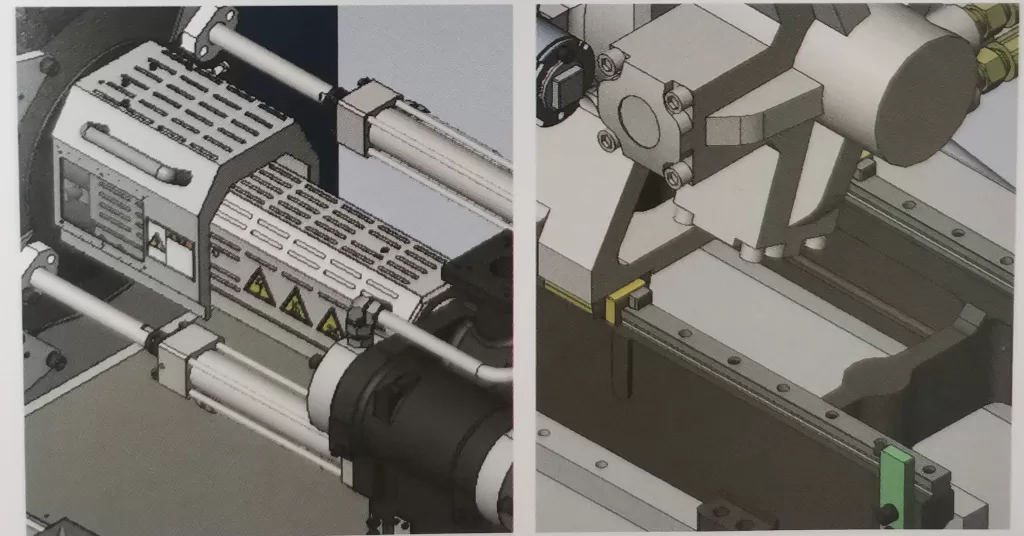
The linear guide can accurately control the movement of the injection unit, thereby achieving accurate material placement and consistent part quality. This high level of precision minimizes defects caused by misaligned or inaccurate injections, which reduces waste. Additionally, the smooth motion provided by linear guides reduces mechanical wear on machine components, which extends machine life and reduces the frequency of part replacement. This reduces waste generated by worn parts and improves overall machine efficiency.
Efficient injection molding machine optimize material use
One of the main ways to reduce injection molding waste is to optimize material use. They are equipped with self-developed control systems, KEBA controllers, PHASE servo motors, and DELTA servo drives to ensure that the exact amount of material is used for each part, thereby minimizing overage and waste. This optimization is facilitated by advanced features such as shot volume control and automatic material feeding systems, ensuring consistent and accurate material delivery. In addition, machines equipped with PHASE servo motors can be controlled accurately and stably through electric means, ensuring accurate and repeatable injection cycles to reduce material waste.
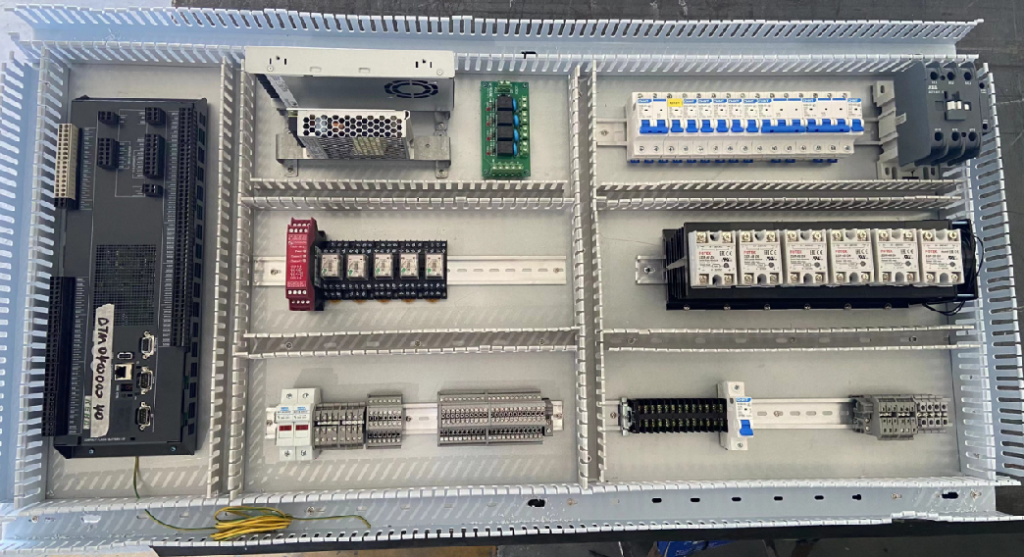
Efficient injection molding machine shorten cycle time
Cycle time is the duration of the entire injection molding process and is a critical factor in reducing waste. Efficient injection molding machines use high-speed injection devices, electroplated screw groups, and temperature control at the feed port to quickly fill the molten plastic into the mold while increasing productivity and applying a more comprehensive range of rubber materials. Servo motors and drives also provide precise and fast motion for components such as injection and clamping. Both ensure quick and accurate performance at each stage of the injection molding process, helping to shorten cycle times.
Make a sound production plan
In addition to their technical characteristics, daily production planning is also the key to reducing waste. Material requirements can be accurately predicted based on past historical data. This minimizes excess inventory and reduces the risk of material degradation and waste. At the same time, it is necessary to select raw materials that are suitable for the product characteristics. Work with relevant material suppliers to ensure raw materials’ high quality and consistency to minimize scrap and waste. Moreover, real-time monitoring systems track key parameters and detect abnormalities.
Help you reduce waste
Reducing waste in injection molding requires advanced technology, optimized processes, and skilled operators. They provide the required technology and capabilities to minimize material waste, energy consumption, and production time. As an injection molding machine manufacturer, helping you and different manufacturers reduce waste and increase costs is also what we are most willing to see.
TRENDING POSTS
- What factors can cause delays in the injection molding process of plastic molding machine? 2024/06/26
- Exhibition Review| Topstar participates in InterPlas Thailand 2024 2024/06/26
- Star Case | Topstar helps Santong upgrade its intelligent plant 2024/06/26
- Topstar Special | National Science and Technology Workers Day 2024/06/26
HOT TOPIC
- 3 in 1 Compact Dehumidifying Dryer
- 5-axis CNC machine
- accuracy
- Air Chillers
- all electric injection molding machine
- all electric injection molding machines
- All-electric injection molding machines
- and overall production quality. Therefore
- AP-RubberPlas
- automated injection molding machine
- Automation changed engineering
- automation of injection molding robots
- auxiliary machine
- Bench Injection Molding Machine
- Cabinet dryer manufacturers
- Cabinet dryers
- chiller
- CNC Drilling Machine
- CNC Drilling Machines
- cnc engraving machine manufacturer
- cnc laser cutting machine manufacturer
- CNC machine
- CNC Machine Center
- CNC Machine for Sale
- CNC Machine Manufacturing
- CNC Machine Tool
- CNC machine tool product
- CNC Machining Center
- CNC wood carving machine
- Cooling system
- Cross-Walking Single Axis Servo Cylinder Robot
- Cross-Walking Single-Axis Servo Cylinder Robot
- Cross-Walking Three-Axis/Five-Axis Servo Driven Robot
- cross-walking three-axis/five-axis servo-driven robot
- Dehumidifier Dryer
- Dehumidifying Dryer
- delta parallel robot
- Desktop Injection Molding Machine
- Desktop injection molding machines
- Desktop Molding Machine
- desktop plastic injection machine
- Desktop Plastic Injection Molding Machine
- direct clamp injection molding machine
- Direct clamp injection molding machines
- Dosing & mixing system
- Drilling Centers
- Drying and dehumidification system
- drying and dehumidifying equipment
- Drying and Dehumidifying System
- drying system
- effective and efficient. Cabinet dryers are also used in other industries where large quantities of material need to be dried
- efficient injection molding machine
- elbow hydraulic injection molding machines
- electric injection molding machine
- electric injection molding machines
- energy-saving injection molding machine
- etc. Among injection molding robots
- exhibition
- features of CNC machine
- Feeding And Conveying System
- Five Axis Machine Center
- Fully automatic injection molding machine
- Gathering Topstar
- giant injection molding machine
- GMU-600 5-Axis Machining Center
- Granulating & Recycling System
- Heavy duty injection molding machine
- Honeycomb rotor dehumidifier
- horizontal injection molding machine
- Horizontal Injection Molding Machines
- Horizontal Injection Moulding Machine
- Horizontal Mixer manufacturer
- How The CNC Machine Works
- hybrid injection molding machine
- hydraulic injection molding machine
- Hydraulic Injection Molding Machines
- in this article
- Industrial robot
- Industrial Robot Chinese brand
- industrial robot parts
- industrial robot supplier
- Industrial robots
- Industry Chain
- Injection Manipulator
- injection mold machines
- Injection molding
- Injection molding automation
- Injection Molding Automation Solution
- injection molding dryer
- Injection molding equipment
- injection molding hopper dryer
- Injection molding machine
- injection molding machine brand
- Injection Molding Machine Factory
- Injection Molding Machine Manufacture
- Injection molding machine manufacturer
- injection molding machine manufacturers
- Injection molding machine procurement
- injection molding machine robotic arm
- injection molding machine with a robot
- Injection molding machines
- injection molding material dehumidifying
- injection molding plant
- Injection Molding Robot
- injection molding robot arm
- Injection molding robot automation
- Injection molding robotic arm
- injection molding robots
- Injection Moulding Robots
- Injection Robot
- Injection robot arm
- Injection robot manufacturer
- Injection robot wholesale
- injection robots
- intelligent injection molding machines
- Introducing Injection Robot
- It is the best choice for drying large quantities of material at once. Cabinetmakers use these machines because they are fast
- large injection molding machine
- Learn what industrial automation and robotics is
- low speed sound-proof granulator
- machine plastic molding
- make sure to add some! Improvements (2) Keyphrase in introduction: Your keyphrase or its synonyms appear in the first paragraph of the copy
- manipulator machine
- manufacturing
- micro injection molding machine
- middle speed granulator
- Mini CNC machine manufacturers.
- Mold Temperature Control System
- mold temperature controller
- molding material Dehumidifying System
- mould temperature controller
- mould temperature controllers
- New electric injection molding machine
- nitrogen dryer manufacturer
- nitrogen dryer system manufacturer
- Oil type mold temperature controller
- open day
- Outbound links: No outbound links appear in this page. Add some! Images: No images appear on this page. Add some! Internal links: No internal links appear in this page
- PET Preform injection molding
- phone case maker machine
- phone case making machine
- plastic bottle making machine
- plastic bottle manufacturing
- plastic bucket making machine
- plastic bucket manufacturing
- Plastic chair making machine
- plastic forming equipment
- plastic hopper dryer
- plastic injection machine
- plastic injection machines
- plastic injection molding
- Plastic injection molding equipment
- Plastic injection molding machine
- Plastic Injection Molding Machines
- plastic injection robot
- Plastic Molding machine
- Plastic Molding Machines
- plastic molding press
- plastic phone case making machine
- plastic-molding machine
- powerful granulator
- Powerful Type Sound-Proof Granulator
- production of plastic seats
- Robot injection molding
- robot injection molding machine
- robot manufacturing companies
- Robotic arm for injection molding machine
- robotic injection molding machines
- robotics in injection molding
- SCARA robot
- SCARA robots
- Service-oriented manufacturing
- Servo Cylinder Robot
- servo driven robot
- Servo Driven Robots
- servo injection robots
- Servo-Driven Robot
- Setup of injection machine
- Silicone Injection Molding Machine
- six-axis industrial robot
- Stainless Hopper Dryer
- Stainless Hopper Dryers
- star club
- swing arm robot
- the choice between servo-driven robots and hydraulic robots will have a certain impact on efficiency
- the most popular injection molding machine
- the type of injection molding robot
- toggle clamp injection molding machine
- Toggle Hydraulic Injection Molding Machines
- toggle injection molding machine
- Top 10 brands of injection robots
- Topstar
- Topstar Engineering
- Topstar Industrial Robots
- Topstar injection molding intelligent
- Topstar Scara Robots
- Useful Injection molding machine
- Vertical machining centers
- volumetric type blender
- water chiller
- water chillers
- water distributor
- Water Type MoldTemperature Controller
- We often face choices when performing injection molding. We will choose the type of injection molding machine
- wholesale of injection molding machines
- x carve CNC