How do mould temperature controllers manage rapid temperature changes?
2024/11/11 By Topstar
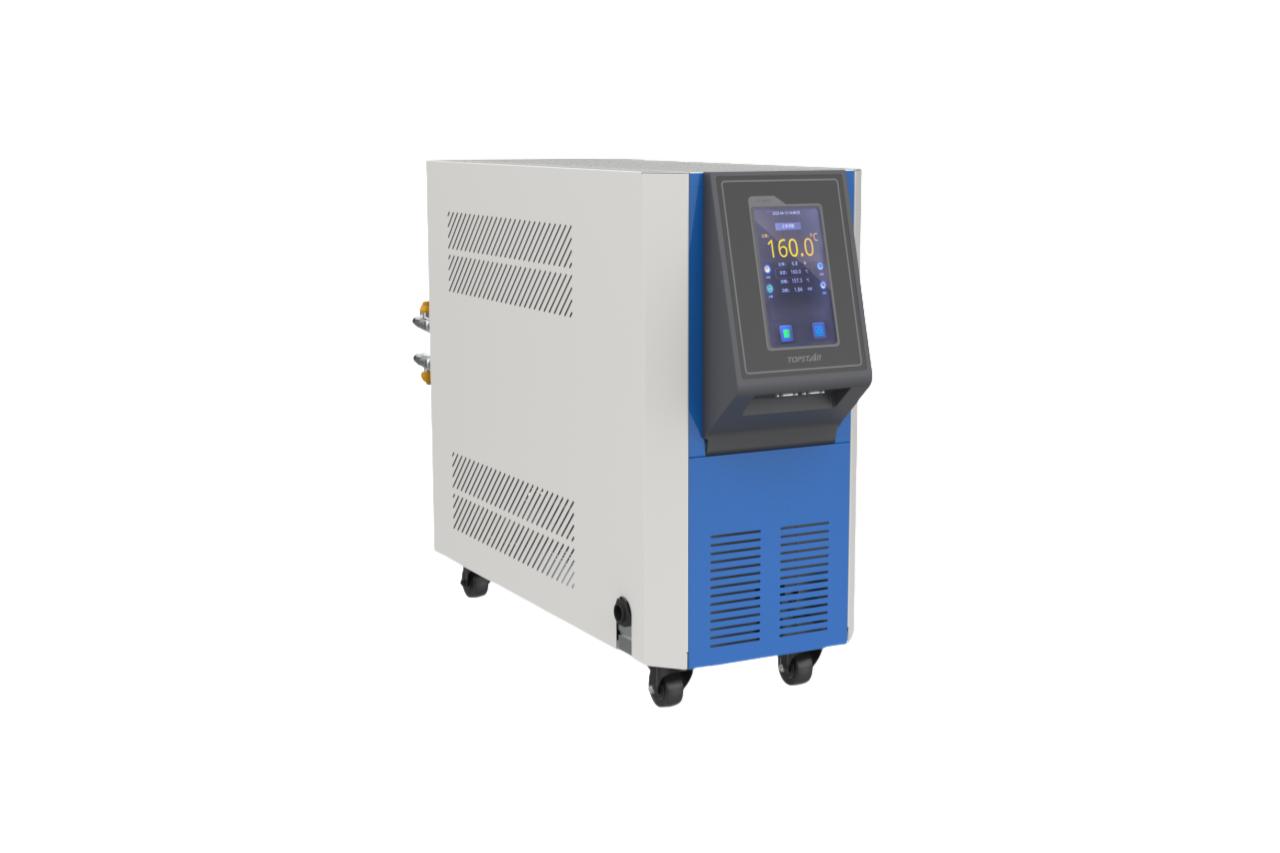
During the injection molding process, the mold’s temperature change will affect the product’s quality, thereby affecting precision, especially when there is a rapid temperature change. If this situation is not managed well, it will have an adverse effect. This is a problem that many customers often need help with. After the upgrade, Topstar’s fourth-generation mould temperature controllers are more intelligent. They are specially designed to manage and maintain the optimal temperature of the mould throughout the molding process, including rapid temperature changes. This article will share how the mould temperature controller handles these temperature fluctuations.
The role of heating and cooling systems in mould temperature controllers
One of the core functions of a mould temperature controller is managing rapid temperature changes through heating and cooling systems. Topstar added powerful heating elements and high-performance cooling circuits to adapt to different temperatures, allowing for quick adjustments. The system raises or lowers the temperature in seconds, ensuring that the mould temperature meets the needs of each specific production cycle.
The mould temperature controller’s heating elements provide precise heat energy to ensure fast and uniform heating. When cooling is required, the controller circulates coolant through a chiller circuit to absorb excess heat and quickly reduce the mould temperature. The mould temperature controller can effectively manage rapid temperature changes using heating and cooling technology.
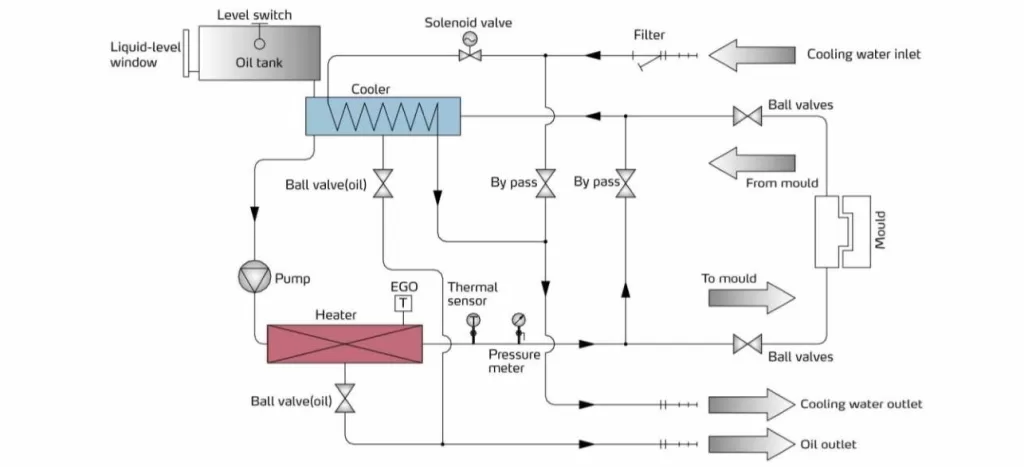
The Role of Temperature Sensors in Mould Temperature Controllers
Temperature sensors are essential for managing rapid temperature changes in mould temperature controllers. These sensors monitor mould temperature in real time and send data back to the controller to ensure that mould temperature remains within the desired range. Susceptible sensors provide the required accuracy for rapid temperature changes and can detect even minor deviations, allowing fast adjustments.
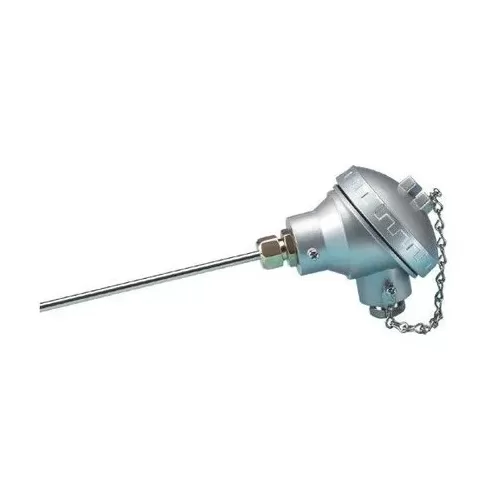
The injection molding process may require customization of different types of sensors, such as thermocouples or resistance temperature detectors (RTDs), based on their specific requirements. High-precision sensors enable the controller to react to changes almost instantly, ensuring the mould temperature is always accurate during each cycle. With precise temperature feedback from the sensor, the mould temperature controller can dynamically respond to temperature fluctuations, maintain stability and improve the overall efficiency of the injection molding process.
Using PID Control to Ensure Stability
PID control is a crucial function of mould temperature controllers, enabling them to manage rapid temperature changes accurately. The PID temperature control algorithm can improve the temperature control efficiency by 10% to ensure temperature uniformity. PID control continuously calculates the difference between the desired and actual temperatures and adjusts the heating or cooling output to minimize this gap. This approach achieves precise and stable temperature control even under rapidly changing conditions. When dealing with rapid temperature changes, PID control is critical to prevent overshooting or undershooting (temperature exceeding or falling below the desired level). By adjusting in real-time, the PID controller maintains a balanced temperature, ensuring the mould remains within the specified range during every part of the molding cycle.
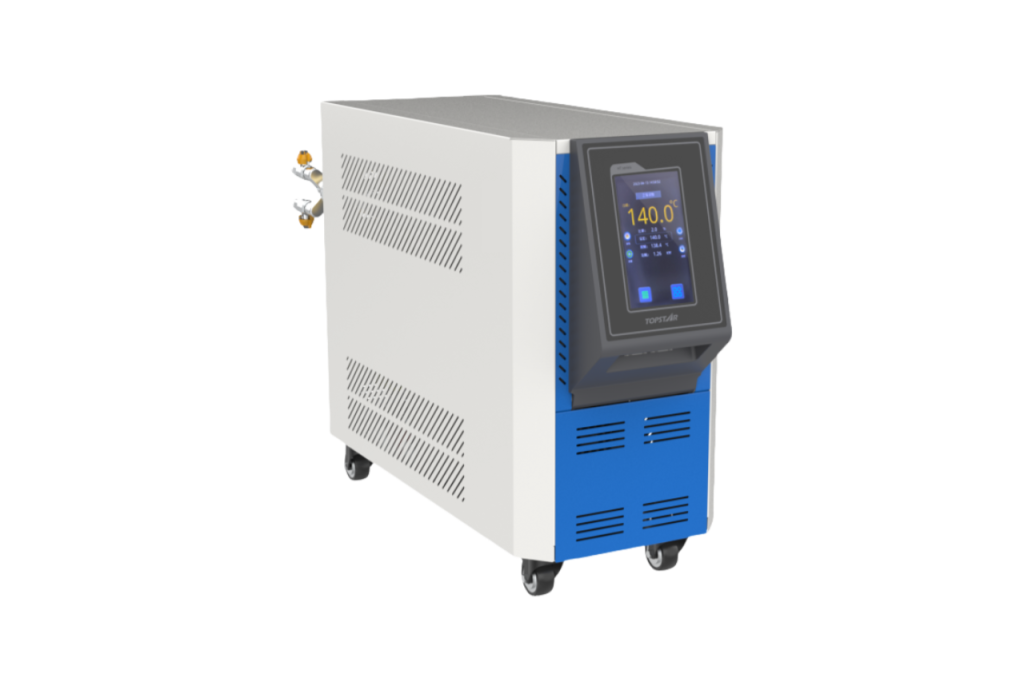
Perform real-time monitoring and alarms
Real-time monitoring and alarms can also manage rapid temperatures in mould temperature controllers. Topstar has a self-developed system that can continuously give feedback on the mould temperature and notify the operator when the temperature exceeds the specified parameters. This real-time data enables operators to take immediate action when necessary to prevent problems that may cause defects or production delays. They usually have an integrated alarm system to issue abnormal signals, such as temperature spikes or drops. Visual indicators, alarms, and even remote notifications deliver these alerts for off-site monitoring. In addition, when mold replacement arises, they provide forced cooling and timed scheduled power on and off functions, continuously opening the cooling solenoid valve for cooling, which reduces mold temperature in about 10 minutes.
Manage energy efficiency from rapid temperature changes
High-efficiency controllers regulate temperature with minimal energy consumption, balancing heating and cooling needs without excessive electricity use. These controllers optimise temperature changes using energy-efficient components and intelligent algorithms while keeping energy costs low. The fourth generation of mould temperature controllers recycles and reuses heat energy whenever possible, reducing the need for additional heating or cooling. This energy-saving approach reduces operating costs and minimizes environmental impact, aligning with the manufacturing industry’s sustainable development goals.
Better manage temperature changes for you.
With features such as advanced heating and cooling systems, PID control, real-time monitoring, and energy efficiency, these controllers handle the complexity of rapid temperature management in various industries. Whether producing automotive parts, medical devices, or electronic products, mold temperature controllers can maintain ideal conditions, improve production efficiency, and meet industry quality standards.
TRENDING POSTS
- What factors can cause delays in the injection molding process of plastic molding machine? 2024/11/11
- Exhibition Review| Topstar participates in InterPlas Thailand 2024 2024/11/11
- Star Case | Topstar helps Santong upgrade its intelligent plant 2024/11/11
- Topstar Special | National Science and Technology Workers Day 2024/11/11
HOT TOPIC
- 3 in 1 Compact Dehumidifying Dryer
- 5-axis CNC machine
- accuracy
- Air Chillers
- all electric injection molding machine
- all electric injection molding machines
- All-electric injection molding machines
- and overall production quality. Therefore
- AP-RubberPlas
- automated injection molding machine
- Automation changed engineering
- automation of injection molding robots
- auxiliary machine
- Bench Injection Molding Machine
- Cabinet dryer manufacturers
- Cabinet dryers
- chiller
- CNC Drilling Machine
- CNC Drilling Machines
- cnc engraving machine manufacturer
- cnc laser cutting machine manufacturer
- CNC machine
- CNC Machine Center
- CNC Machine for Sale
- CNC Machine Manufacturing
- CNC Machine Tool
- CNC machine tool product
- CNC Machining Center
- CNC wood carving machine
- Cooling system
- Cross-Walking Single Axis Servo Cylinder Robot
- Cross-Walking Single-Axis Servo Cylinder Robot
- Cross-Walking Three-Axis/Five-Axis Servo Driven Robot
- cross-walking three-axis/five-axis servo-driven robot
- Dehumidifier Dryer
- Dehumidifying Dryer
- delta parallel robot
- Desktop Injection Molding Machine
- Desktop injection molding machines
- Desktop Molding Machine
- desktop plastic injection machine
- Desktop Plastic Injection Molding Machine
- direct clamp injection molding machine
- Direct clamp injection molding machines
- Dosing & mixing system
- Drilling Centers
- Drying and dehumidification system
- drying and dehumidifying equipment
- Drying and Dehumidifying System
- drying system
- effective and efficient. Cabinet dryers are also used in other industries where large quantities of material need to be dried
- efficient injection molding machine
- elbow hydraulic injection molding machines
- electric injection molding machine
- electric injection molding machines
- energy-saving injection molding machine
- etc. Among injection molding robots
- exhibition
- features of CNC machine
- Feeding And Conveying System
- Five Axis Machine Center
- Fully automatic injection molding machine
- Gathering Topstar
- giant injection molding machine
- GMU-600 5-Axis Machining Center
- Granulating & Recycling System
- Heavy duty injection molding machine
- Honeycomb rotor dehumidifier
- horizontal injection molding machine
- Horizontal Injection Molding Machines
- Horizontal Injection Moulding Machine
- Horizontal Mixer manufacturer
- How The CNC Machine Works
- hybrid injection molding machine
- hydraulic injection molding machine
- Hydraulic Injection Molding Machines
- in this article
- Industrial robot
- Industrial Robot Chinese brand
- industrial robot parts
- industrial robot supplier
- Industrial robots
- Industry Chain
- Injection Manipulator
- injection mold machines
- Injection molding
- Injection molding automation
- Injection Molding Automation Solution
- injection molding dryer
- Injection molding equipment
- injection molding hopper dryer
- Injection molding machine
- injection molding machine brand
- Injection Molding Machine Factory
- Injection Molding Machine Manufacture
- Injection molding machine manufacturer
- injection molding machine manufacturers
- Injection molding machine procurement
- injection molding machine robotic arm
- injection molding machine with a robot
- Injection molding machines
- injection molding material dehumidifying
- injection molding plant
- Injection Molding Robot
- injection molding robot arm
- Injection molding robot automation
- Injection molding robotic arm
- injection molding robots
- Injection Moulding Robots
- Injection Robot
- Injection robot arm
- Injection robot manufacturer
- Injection robot wholesale
- injection robots
- intelligent injection molding machines
- Introducing Injection Robot
- It is the best choice for drying large quantities of material at once. Cabinetmakers use these machines because they are fast
- large injection molding machine
- Learn what industrial automation and robotics is
- low speed sound-proof granulator
- machine plastic molding
- make sure to add some! Improvements (2) Keyphrase in introduction: Your keyphrase or its synonyms appear in the first paragraph of the copy
- manipulator machine
- manufacturing
- micro injection molding machine
- middle speed granulator
- Mini CNC machine manufacturers.
- Mold Temperature Control System
- mold temperature controller
- molding material Dehumidifying System
- mould temperature controller
- mould temperature controllers
- New electric injection molding machine
- nitrogen dryer manufacturer
- nitrogen dryer system manufacturer
- Oil type mold temperature controller
- open day
- Outbound links: No outbound links appear in this page. Add some! Images: No images appear on this page. Add some! Internal links: No internal links appear in this page
- PET Preform injection molding
- phone case maker machine
- phone case making machine
- plastic bottle making machine
- plastic bottle manufacturing
- plastic bucket making machine
- plastic bucket manufacturing
- Plastic chair making machine
- plastic forming equipment
- plastic hopper dryer
- plastic injection machine
- plastic injection machines
- plastic injection molding
- Plastic injection molding equipment
- Plastic injection molding machine
- Plastic Injection Molding Machines
- plastic injection robot
- Plastic Molding machine
- Plastic Molding Machines
- plastic molding press
- plastic phone case making machine
- plastic-molding machine
- powerful granulator
- Powerful Type Sound-Proof Granulator
- production of plastic seats
- Robot injection molding
- robot injection molding machine
- robot manufacturing companies
- Robotic arm for injection molding machine
- robotic injection molding machines
- robotics in injection molding
- SCARA robot
- SCARA robots
- Service-oriented manufacturing
- Servo Cylinder Robot
- servo driven robot
- Servo Driven Robots
- servo injection robots
- Servo-Driven Robot
- Setup of injection machine
- Silicone Injection Molding Machine
- six-axis industrial robot
- Stainless Hopper Dryer
- Stainless Hopper Dryers
- star club
- swing arm robot
- the choice between servo-driven robots and hydraulic robots will have a certain impact on efficiency
- the most popular injection molding machine
- the type of injection molding robot
- toggle clamp injection molding machine
- Toggle Hydraulic Injection Molding Machines
- toggle injection molding machine
- Top 10 brands of injection robots
- Topstar
- Topstar Engineering
- Topstar Industrial Robots
- Topstar injection molding intelligent
- Topstar Scara Robots
- Useful Injection molding machine
- Vertical machining centers
- volumetric type blender
- water chiller
- water chillers
- water distributor
- Water Type MoldTemperature Controller
- We often face choices when performing injection molding. We will choose the type of injection molding machine
- wholesale of injection molding machines
- x carve CNC