How do mold temperature controller handle thermal overloads?
2024/10/18 By Topstar
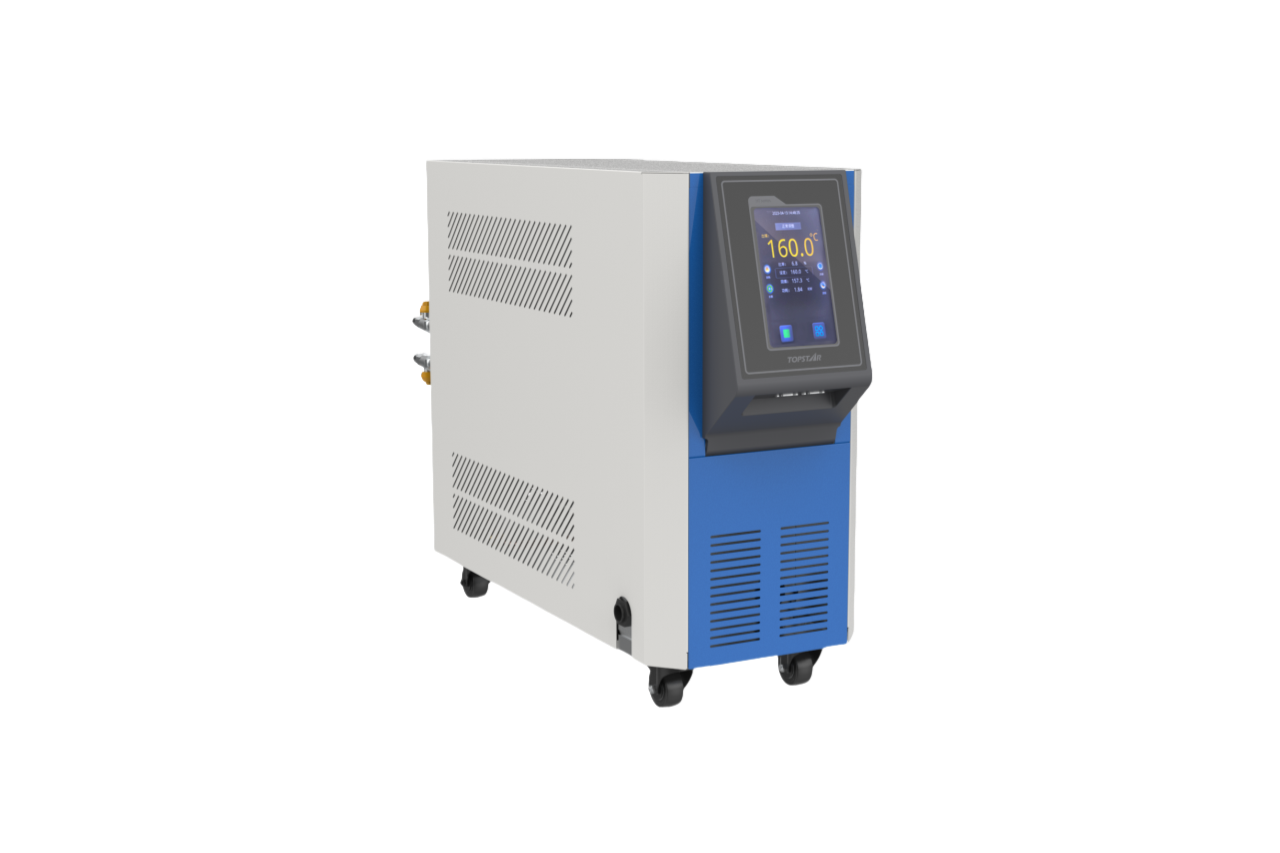
In plastic product manufacturing, precise temperature control allows the production of high-quality parts. Mold temperature controllers are critical to maintaining a constant temperature during injection molding. These devices regulate the mold’s temperature to ensure it remains within the optimal operating parameters, improving part quality and production efficiency. However, when exposed to excessive temperatures, thermal overloads may damage the equipment and products. Therefore, Topstar will discuss how our mold temperature controller handles thermal overloads.
Thermal Overload and Its Effect on Injection Molding
Thermal overload occurs when the temperature in the injection molding system exceeds the safe operating level. This can occur due to various factors, including equipment failure, poor heat transfer, or external environmental conditions. During the injection molding, thermal overloads can cause multiple problems, such as warping, material degradation, and mold damage. Parts may shrink unevenly, the surface may become discolored, or mechanical properties may weaken. Therefore, effectively handling these temperature peaks is necessary to maintain product quality and protect machinery. To prevent these problems, mold temperature controllers can continuously monitor the temperature of the mold to ensure that it remains within a predefined range to avoid overheating. When temperatures rise to potentially dangerous levels, the controller can take immediate action to prevent damage and maintain production efficiency.
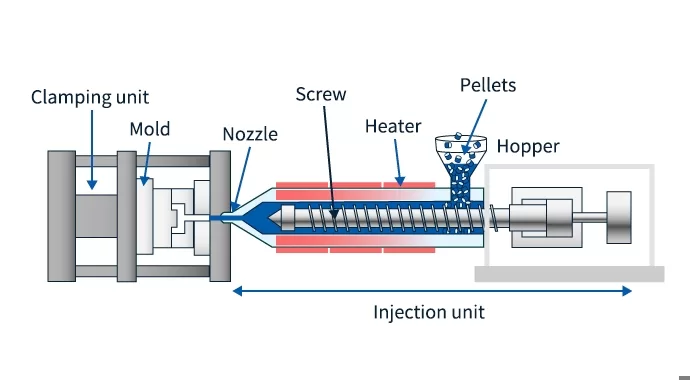
How Mold Temperature Controller Detect Thermal Overload?
A vital feature of a mold temperature controller is its ability to detect thermal overload in real-time. Sensors in the controller measure the mold temperature and the temperature of the coolant circulating through the system. The sensors provide continuous feedback to the controller, which processes this data and adjusts the temperature accordingly.
If the mold temperature exceeds a set threshold, the controller’s sensors immediately signal the system to intervene. At the same time, there is also a built-in safety mechanism that triggers the automatic shutdown of the cooling system when abnormal heat levels are detected. This real-time detection prevents prolonged exposure to high temperatures, minimizing the risk of thermal overload damage. The fast response time for manufacturers enables the system to take action before any critical thresholds are breached, protecting the equipment and molded parts from damage.
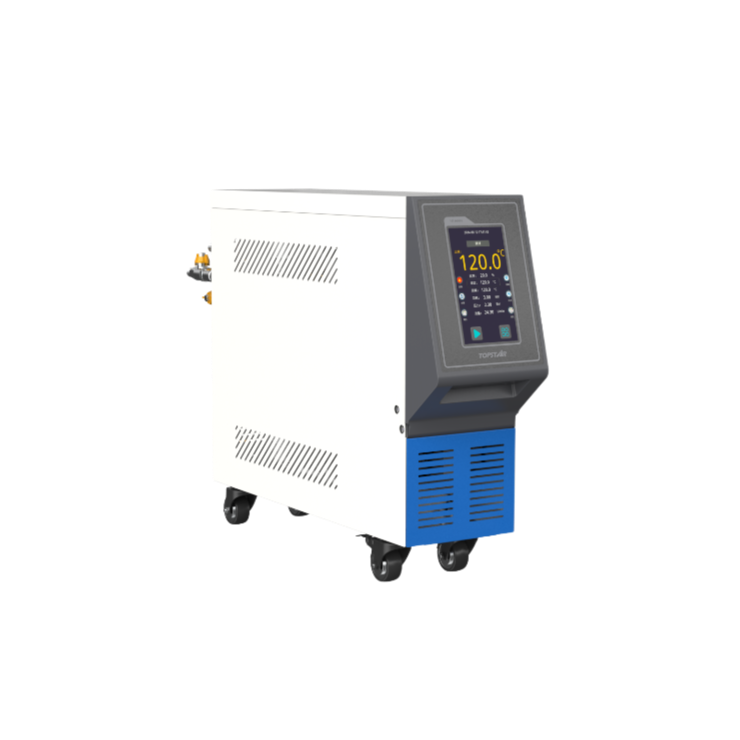
Cooling Systems and Heat Dissipation in Mold Temperature Controller
Once a mold temperature controller detects a potential thermal overload, it must effectively dissipate excess heat to return the mold to a safe operating range. A combination of water—or oil-based cooling systems is typically used to manage the mold’s temperature. These fluids circulate in the mold’s channels, absorbing heat and transferring it away from the surface.
In the event of a thermal overload, the controller will increase the coolant’s flow rate or adjust the coolant’s temperature to ensure more efficient heat dissipation. The cooling technology, such as high-efficiency heat exchangers, helps transfer heat faster and more efficiently. These systems can be customized according to the molding material and mold design to ensure optimized cooling for each specific application. At the same time, the copper heater has been newly upgraded. The copper material has excellent ductility and thermal conductivity; its life is increased by 40%, and its efficiency is increased by 10%. The mold temperature controller can be used commonly even when the water quality is poor.
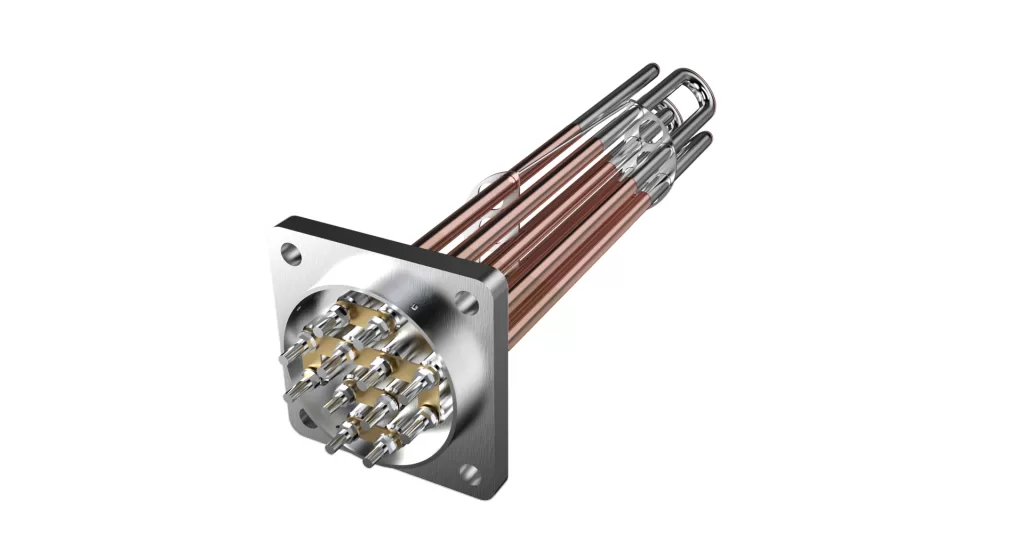
Automatic safety mechanism
When dealing with thermal overload, the mold temperature controller is equipped with automatic safety mechanisms to ensure that the system is protected even in the event of a significant increase in temperature. These safety features include automatic shutdown protocols, alarm systems, and manual override functions. The mold temperature will automatically shut down when it exceeds a critical threshold. The controller cuts off the heating element or starts the emergency cooling system to reduce the mold temperature. At the same time, the alarm may notify the operator that the system has encountered a thermal overload so that quick action can be taken to solve the potential problem.
Of course, in addition to the automatic shutdown function, Topstar’s mold temperature controller has forced cooling and timed scheduled power on and off functions. Continuously opening the cooling solenoid valve reduces the mold’s temperature by about 10 minutes. Preheating one hour in advance increases efficiency by 10%.
Bringing higher energy efficiency
Overheating will significantly increase energy consumption because the system needs to work harder to control the rise in temperature. By preventing thermal overload, mold temperature controllers help optimize energy use and reduce costs. They fine-tune the heating and cooling systems to use energy only when necessary, ensuring efficiency. Rather than overcompensating for temperature fluctuations from thermal overload, they maintain a stable temperature throughout the molding cycle. This balance not only saves energy but also extends the life of the equipment by reducing wear.
Let you have higher quality products.
Using the right equipment and systems, manufacturers can effectively manage these risks. The mold temperature controller is critical in maintaining the ideal mold temperature and preventing overheating. From detecting temperature spikes in real time to initiating automated cooling systems and implementing safety shutdowns, they provide the precision and control needed to protect equipment and maintain high product quality across various manufacturing industries.
TRENDING POSTS
- What factors can cause delays in the injection molding process of plastic molding machine? 2024/10/18
- Exhibition Review| Topstar participates in InterPlas Thailand 2024 2024/10/18
- Star Case | Topstar helps Santong upgrade its intelligent plant 2024/10/18
- Topstar Special | National Science and Technology Workers Day 2024/10/18
HOT TOPIC
- .ervo motor-driven linear robots
- 3 axis robot
- 3 axis robots
- 3 in 1 Compact Dehumidifying Dryer
- 3-axis robot
- 3-axis robots
- 5-axis CNC machine
- accuracy
- Air Chillers
- all electric injection molding machine
- all electric injection molding machines
- All-electric injection molding machines
- and overall production quality. Therefore
- AP-RubberPlas
- automated injection molding machine
- Automation changed engineering
- automation of injection molding robots
- auxiliary machine
- Bench Injection Molding Machine
- Cabinet dryer manufacturers
- Cabinet dryers
- chiller
- CNC Drilling Machine
- CNC Drilling Machines
- cnc engraving machine manufacturer
- cnc laser cutting machine manufacturer
- CNC machine
- CNC Machine Center
- CNC Machine for Sale
- CNC Machine Manufacturing
- CNC Machine Tool
- CNC machine tool product
- CNC Machining Center
- CNC wood carving machine
- Cooling system
- Cross-Walking Single Axis Servo Cylinder Robot
- Cross-Walking Single-Axis Servo Cylinder Robot
- Cross-Walking Three-Axis/Five-Axis Servo Driven Robot
- cross-walking three-axis/five-axis servo-driven robot
- Dehumidifier Dryer
- Dehumidifying Dryer
- delta parallel robot
- Desktop Injection Molding Machine
- Desktop injection molding machines
- Desktop Molding Machine
- desktop plastic injection machine
- Desktop Plastic Injection Molding Machine
- direct clamp injection molding machine
- Direct clamp injection molding machines
- Dosing & mixing system
- Drilling Centers
- Drying and dehumidification system
- drying and dehumidifying equipment
- Drying and Dehumidifying System
- drying system
- effective and efficient. Cabinet dryers are also used in other industries where large quantities of material need to be dried
- efficient injection molding machine
- elbow hydraulic injection molding machines
- electric injection molding machine
- electric injection molding machines
- energy-efficient injection molding robot
- energy-saving injection molding machine
- etc. Among injection molding robots
- exhibition
- features of CNC machine
- Feeding And Conveying System
- Five Axis Machine Center
- Fully automatic injection molding machine
- Gathering Topstar
- giant injection molding machine
- GMU-600 5-Axis Machining Center
- Granulating & Recycling System
- Heavy duty injection molding machine
- High-precision electric molding machines
- high-precision plastic molding machines
- high-speed all electric injection molding machine
- Honeycomb rotor dehumidifier
- horizontal injection molding machine
- Horizontal Injection Molding Machines
- Horizontal Injection Moulding Machine
- Horizontal Mixer manufacturer
- How The CNC Machine Works
- hybrid injection molding machine
- hydraulic injection molding machine
- Hydraulic Injection Molding Machines
- in this article
- Industrial robot
- Industrial Robot Chinese brand
- industrial robot parts
- industrial robot supplier
- Industrial robots
- Industry Chain
- Injection Manipulator
- injection manipulator robot
- injection mold machines
- Injection molding
- Injection molding automation
- Injection Molding Automation Solution
- injection molding dryer
- Injection molding equipment
- injection molding hopper dryer
- Injection molding machine
- injection molding machine brand
- Injection Molding Machine Factory
- Injection Molding Machine Manufacture
- Injection molding machine manufacturer
- injection molding machine manufacturers
- Injection molding machine procurement
- injection molding machine robotic arm
- injection molding machine with a robot
- Injection molding machines
- injection molding material dehumidifying
- injection molding plant
- Injection Molding Robot
- injection molding robot arm
- Injection molding robot automation
- Injection molding robotic arm
- injection molding robots
- Injection moulding machine
- Injection Moulding Robots
- Injection Robot
- Injection robot arm
- Injection robot manufacturer
- Injection robot wholesale
- injection robots
- intelligent injection molding machines
- Introducing Injection Robot
- It is the best choice for drying large quantities of material at once. Cabinetmakers use these machines because they are fast
- large injection molding machine
- large injection molding machines
- Learn what industrial automation and robotics is
- linear robot
- linear robots
- low speed sound-proof granulator
- machine plastic molding
- make sure to add some! Improvements (2) Keyphrase in introduction: Your keyphrase or its synonyms appear in the first paragraph of the copy
- manipulator machine
- manufacturing
- medical grade injection molding machines
- medical injection molding machine
- medical injection molding machines
- micro injection molding machine
- middle speed granulator
- Mini CNC machine manufacturers.
- Mold Temperature Control System
- mold temperature controller
- mold temperature controllers
- molding material Dehumidifying System
- mould temperature control system
- mould temperature controller
- mould temperature controllers
- New electric injection molding machine
- nitrogen dryer manufacturer
- nitrogen dryer system manufacturer
- Oil type mold temperature controller
- Oil type mold temperature controllers
- open day
- Outbound links: No outbound links appear in this page. Add some! Images: No images appear on this page. Add some! Internal links: No internal links appear in this page
- PET Preform injection molding
- phone case maker machine
- phone case making machine
- plastic bottle making machine
- plastic bottle manufacturing
- plastic bucket making machine
- plastic bucket manufacturing
- Plastic chair making machine
- plastic forming equipment
- plastic hopper dryer
- plastic injection machine
- plastic injection machines
- plastic injection molding
- Plastic injection molding equipment
- Plastic injection molding machine
- Plastic Injection Molding Machines
- plastic injection moulding machine
- plastic injection robot
- Plastic Molding machine
- Plastic Molding Machines
- plastic molding press
- plastic moulding machine
- plastic phone case making machine
- plastic-molding machine
- powerful granulator
- Powerful Type Sound-Proof Granulator
- precision injection molding
- precision injection molding machines
- production of plastic seats
- pure water mould temperature controller
- Robot injection molding
- robot injection molding machine
- robot manufacturing companies
- Robotic arm for injection molding machine
- robotic injection molding machines
- robotics in injection molding
- SCARA robot
- SCARA robots
- Service-oriented manufacturing
- Servo Cylinder Robot
- servo driven robot
- Servo Driven Robots
- servo injection robots
- servo motor-driven linear robots
- servo-driven 3-axis robot
- Servo-Driven Robot
- Setup of injection machine
- Silicone Injection Molding Machine
- six-axis industrial robot
- Stainless Hopper Dryer
- Stainless Hopper Dryers
- star club
- swing arm robot
- take-out robots
- the choice between servo-driven robots and hydraulic robots will have a certain impact on efficiency
- the most popular injection molding machine
- the type of injection molding robot
- toggle clamp injection molding machine
- Toggle Hydraulic Injection Molding Machines
- toggle injection molding machine
- Top 10 brands of injection robots
- Topstar
- Topstar Engineering
- Topstar Industrial Robots
- Topstar injection molding intelligent
- Topstar Scara Robots
- Useful Injection molding machine
- Vertical machining centers
- volumetric type blender
- water chiller
- water chillers
- water distributor
- water type mold temperature controller
- Water Type MoldTemperature Controller
- Water-Type Mould Temperature Controllers
- We often face choices when performing injection molding. We will choose the type of injection molding machine
- wholesale of injection molding machines
- x carve CNC