How do injection molding machine manufacturer deal with high precision requirements?
2024/11/13 By Topstar
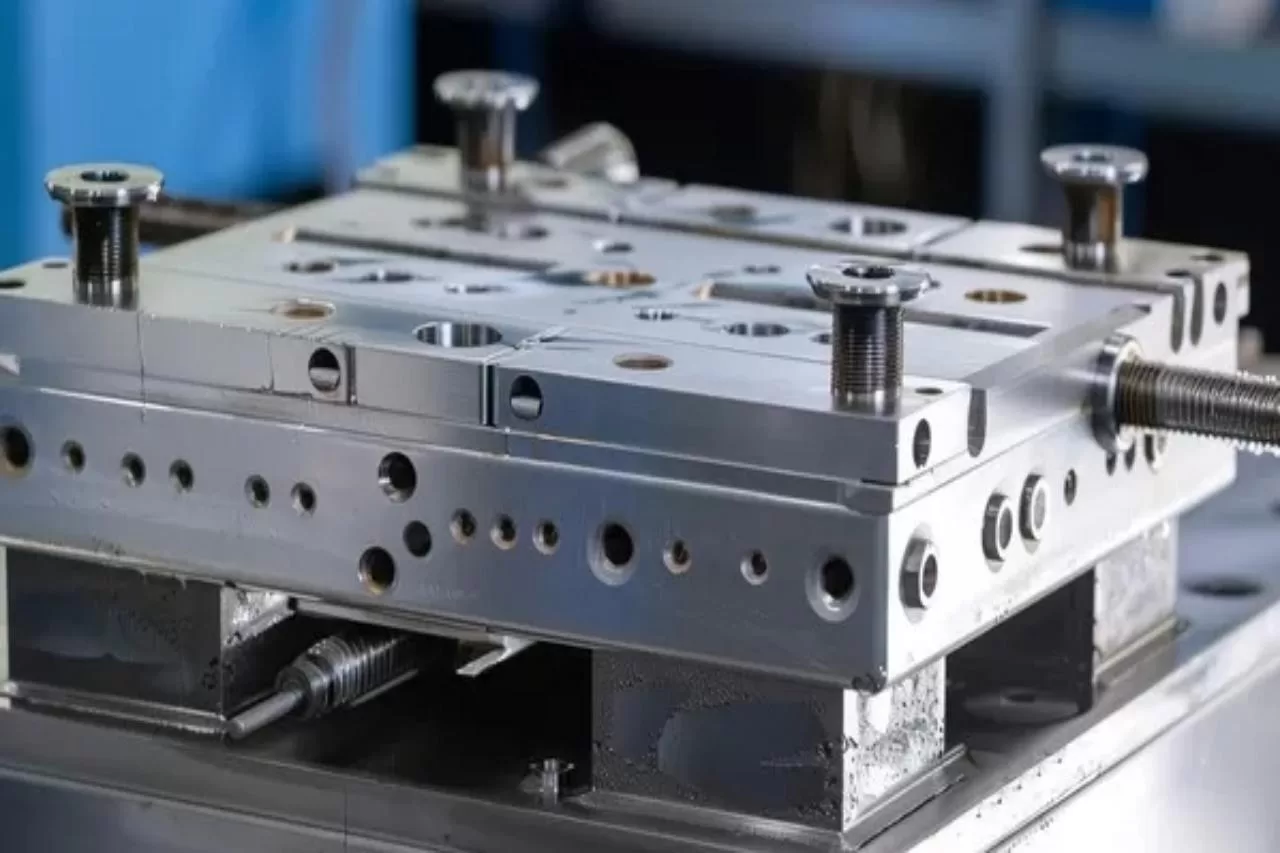
In pursuit of higher precision, electric injection molding machines have gradually replaced hydraulic presses, but traditional electric injection molding machines still have a communication delay of several milliseconds. This will lead to uneven quality control when pursuing precision injection molding products. This is a problem that many customers involved in the precision industry need help with, and they are also looking for injection molding machine manufacturers that can provide precision injection molding solutions. As an injection molding machine manufacturer with three core technologies, Topstar relies on the concept of integrated injection molding process and discrete intelligent drive to launch TE ll electric injection molding machine, making control more precise and injection molding iteration more thoughtful, making customers’ intelligent upgrades and precision management easier.
Discrete intelligent drive used by injection molding machine manufacturer
We use discrete intelligent drive communication as an injection molding machine manufacturer with a self-developed team and core technology. This principle solves the problem of product stability caused by control system communication delay, reduces the feedback cycle, and makes the mechanism movement more precise. In addition, this intelligent drive control mode minimizes the impact of communication delay on the high-speed operation of the servo motor, realizes real-time control of the servo motor, improves the accuracy of position, speed, and pressure control, and increases the response speed by 8-16 times.
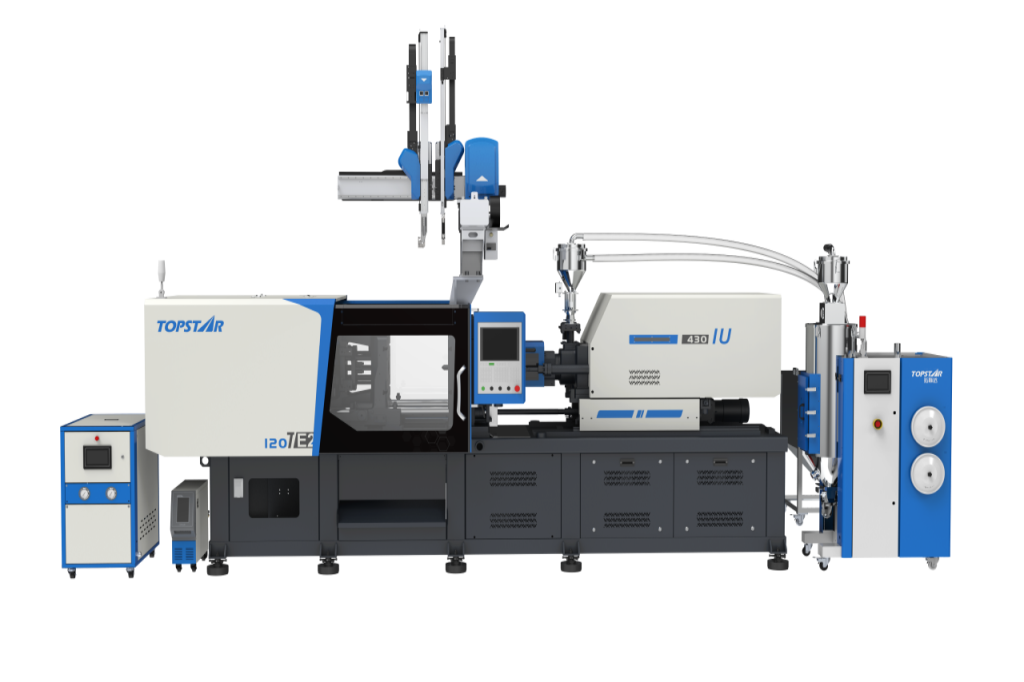
When the servo drive receives the setting parameters from the HMI, it can save these parameters in the internal latch without waiting to receive the control speed from the upper controller during every cycle, making the execution process more efficient. At the same time, it also solves the problem that the operator of the traditional injection molding machine cannot intuitively understand the working conditions of the machine, improves the human-machine interaction, and makes the injection molding equipment more intelligent to reduce the number of debugging times for the production line operator.
Injection molding machine manufacturer use high-precision mold design.
The precision of the injection molding process lies not only in the system control but also in the design and production of the mold. Our mold designers will use high-quality steel and alloys to make durable, wear-resistant molds. They can withstand high pressure and temperature during the injection molding process, as well as CNC machining and EDM technology to produce molds with micron-level precision. These technologies can enable molds to achieve complex geometries. Topstar can create molds that handle tight tolerances and produce components with high dimensional accuracy to meet the precision requirements of industries such as medical equipment, automobiles, and electronics.
Dedicated integrated injection unit
The integrated injection unit has higher rigidity, stable structure, and more precise control, which can accurately control the injection volume, speed, and pressure. These units are calibrated to ensure that molten plastic is injected into the mold at the optimal rate and pressure, eliminating problems such as warping, shrinkage, or incomplete filling. For industries that require micro-molding or micro-components, the injection units are specially modified to handle micro-amounts of material without sacrificing control. They are carefully designed to achieve the precision needed for small parts and meet the high electronics, medical devices, and aerospace industry standards. In addition, the enhanced rigidity of the one-piece injection unit reduces mechanical wear, helping to extend machine life and maintain stable performance. By reducing the number of joints and potential weak points, the unit minimizes maintenance requirements and reduces operating costs, bringing long-term value to manufacturers.
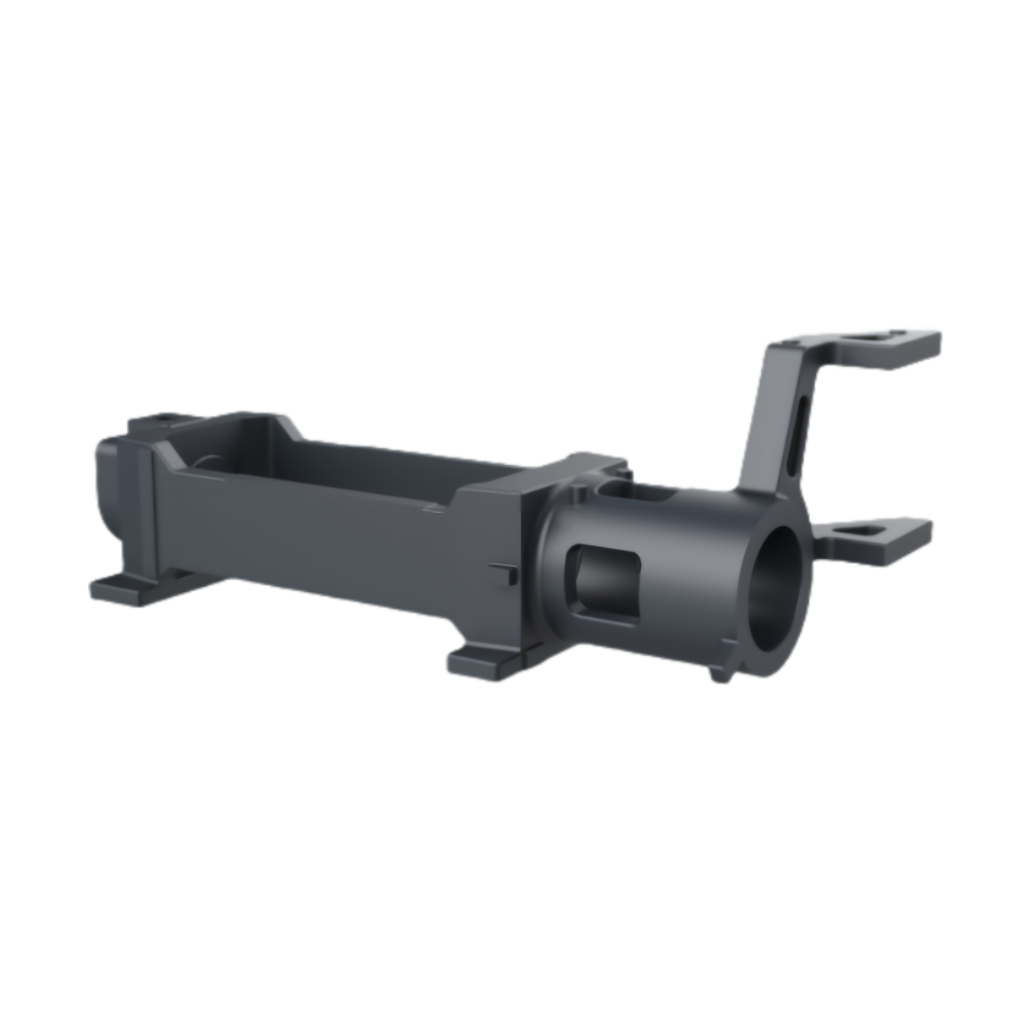
Using linear guide rail
Linear guide rails have low damping, are more sensitive to pressure detection, and have more precise pressure control. Traditional guides react slowly to small changes in pressure, but linear guide rails detect even small fluctuations quickly. This high sensitivity allows real-time adjustments, which can significantly improve product quality by minimizing the risk of defects due to inconsistent pressure, such as warping or inadequate filling. With linear guide rails, electric injection molding machines can detect the smallest changes in pressure and make corresponding adjustments. In addition, linear guide rails improve pressure control accuracy, which is a key factor in molding complex designs or micro parts. By controlling pressure more accurately, manufacturers can achieve consistency, which is particularly important in electronics, automobiles, and medical devices.
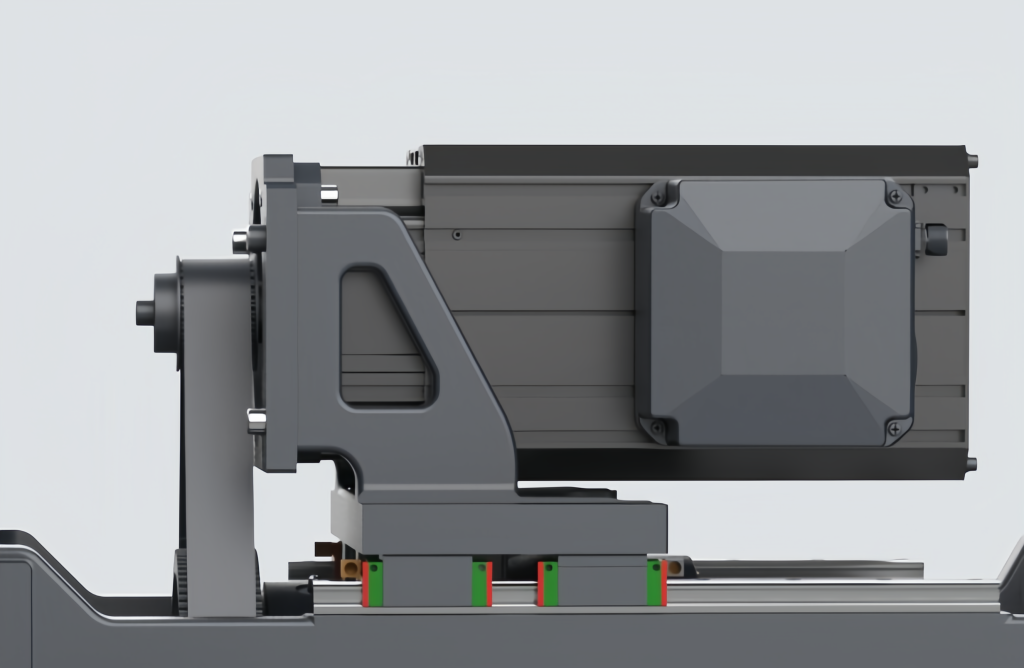
Strengthen control of mold temperature controller
Accurate temperature control is also important for precision injection molding, especially for high-precision applications. In many cases, large temperature fluctuations occur because the temperature control accuracy of the mold temperature controller cannot meet actual production requirements. Plastic viscosity changes with temperature, affecting the mold’s flow and filling. Using the mold temperature controller with the latest PID temperature control algorithm can improve the temperature control efficiency by 10%, ensuring temperature uniformity, keeping the plastic at an ideal consistency, and ensuring uniform filling of complex mold geometries. In addition, the 1MHz ultrasonic flow monitoring monitors the flow in time, can detect bubbles larger than 2mm, ensures that the water flow is liquid, and provides stable and accurate temperature control.
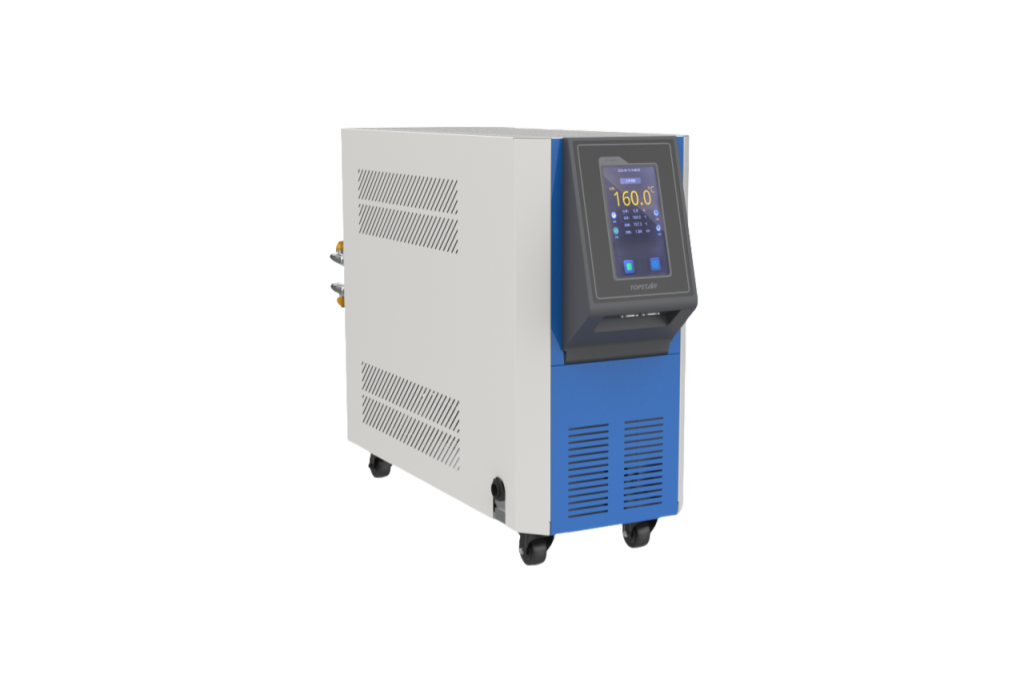
Bring you higher precision management
We use discrete intelligent drive technology, precise mold design, and mold temperature controllers to meet strict standards. As an injection molding machine manufacturer, we provide plastic product companies with the injection molding equipment they need to achieve high-quality production, from precise temperature control to dedicated injection units.
TRENDING POSTS
- What factors can cause delays in the injection molding process of plastic molding machine? 2024/11/13
- Exhibition Review| Topstar participates in InterPlas Thailand 2024 2024/11/13
- Star Case | Topstar helps Santong upgrade its intelligent plant 2024/11/13
- Topstar Special | National Science and Technology Workers Day 2024/11/13
HOT TOPIC
- 3 in 1 Compact Dehumidifying Dryer
- 5-axis CNC machine
- accuracy
- Air Chillers
- all electric injection molding machine
- all electric injection molding machines
- All-electric injection molding machines
- and overall production quality. Therefore
- AP-RubberPlas
- automated injection molding machine
- Automation changed engineering
- automation of injection molding robots
- auxiliary machine
- Bench Injection Molding Machine
- Cabinet dryer manufacturers
- Cabinet dryers
- chiller
- CNC Drilling Machine
- CNC Drilling Machines
- cnc engraving machine manufacturer
- cnc laser cutting machine manufacturer
- CNC machine
- CNC Machine Center
- CNC Machine for Sale
- CNC Machine Manufacturing
- CNC Machine Tool
- CNC machine tool product
- CNC Machining Center
- CNC wood carving machine
- Cooling system
- Cross-Walking Single Axis Servo Cylinder Robot
- Cross-Walking Single-Axis Servo Cylinder Robot
- Cross-Walking Three-Axis/Five-Axis Servo Driven Robot
- cross-walking three-axis/five-axis servo-driven robot
- Dehumidifier Dryer
- Dehumidifying Dryer
- delta parallel robot
- Desktop Injection Molding Machine
- Desktop injection molding machines
- Desktop Molding Machine
- desktop plastic injection machine
- Desktop Plastic Injection Molding Machine
- direct clamp injection molding machine
- Direct clamp injection molding machines
- Dosing & mixing system
- Drilling Centers
- Drying and dehumidification system
- drying and dehumidifying equipment
- Drying and Dehumidifying System
- drying system
- effective and efficient. Cabinet dryers are also used in other industries where large quantities of material need to be dried
- efficient injection molding machine
- elbow hydraulic injection molding machines
- electric injection molding machine
- electric injection molding machines
- energy-saving injection molding machine
- etc. Among injection molding robots
- exhibition
- features of CNC machine
- Feeding And Conveying System
- Five Axis Machine Center
- Fully automatic injection molding machine
- Gathering Topstar
- giant injection molding machine
- GMU-600 5-Axis Machining Center
- Granulating & Recycling System
- Heavy duty injection molding machine
- Honeycomb rotor dehumidifier
- horizontal injection molding machine
- Horizontal Injection Molding Machines
- Horizontal Injection Moulding Machine
- Horizontal Mixer manufacturer
- How The CNC Machine Works
- hybrid injection molding machine
- hydraulic injection molding machine
- Hydraulic Injection Molding Machines
- in this article
- Industrial robot
- Industrial Robot Chinese brand
- industrial robot parts
- industrial robot supplier
- Industrial robots
- Industry Chain
- Injection Manipulator
- injection mold machines
- Injection molding
- Injection molding automation
- Injection Molding Automation Solution
- injection molding dryer
- Injection molding equipment
- injection molding hopper dryer
- Injection molding machine
- injection molding machine brand
- Injection Molding Machine Factory
- Injection Molding Machine Manufacture
- Injection molding machine manufacturer
- injection molding machine manufacturers
- Injection molding machine procurement
- injection molding machine robotic arm
- injection molding machine with a robot
- Injection molding machines
- injection molding material dehumidifying
- injection molding plant
- Injection Molding Robot
- injection molding robot arm
- Injection molding robot automation
- Injection molding robotic arm
- injection molding robots
- Injection Moulding Robots
- Injection Robot
- Injection robot arm
- Injection robot manufacturer
- Injection robot wholesale
- injection robots
- intelligent injection molding machines
- Introducing Injection Robot
- It is the best choice for drying large quantities of material at once. Cabinetmakers use these machines because they are fast
- large injection molding machine
- Learn what industrial automation and robotics is
- low speed sound-proof granulator
- machine plastic molding
- make sure to add some! Improvements (2) Keyphrase in introduction: Your keyphrase or its synonyms appear in the first paragraph of the copy
- manipulator machine
- manufacturing
- micro injection molding machine
- middle speed granulator
- Mini CNC machine manufacturers.
- Mold Temperature Control System
- mold temperature controller
- molding material Dehumidifying System
- mould temperature controller
- mould temperature controllers
- New electric injection molding machine
- nitrogen dryer manufacturer
- nitrogen dryer system manufacturer
- Oil type mold temperature controller
- open day
- Outbound links: No outbound links appear in this page. Add some! Images: No images appear on this page. Add some! Internal links: No internal links appear in this page
- PET Preform injection molding
- phone case maker machine
- phone case making machine
- plastic bottle making machine
- plastic bottle manufacturing
- plastic bucket making machine
- plastic bucket manufacturing
- Plastic chair making machine
- plastic forming equipment
- plastic hopper dryer
- plastic injection machine
- plastic injection machines
- plastic injection molding
- Plastic injection molding equipment
- Plastic injection molding machine
- Plastic Injection Molding Machines
- plastic injection robot
- Plastic Molding machine
- Plastic Molding Machines
- plastic molding press
- plastic phone case making machine
- plastic-molding machine
- powerful granulator
- Powerful Type Sound-Proof Granulator
- production of plastic seats
- Robot injection molding
- robot injection molding machine
- robot manufacturing companies
- Robotic arm for injection molding machine
- robotic injection molding machines
- robotics in injection molding
- SCARA robot
- SCARA robots
- Service-oriented manufacturing
- Servo Cylinder Robot
- servo driven robot
- Servo Driven Robots
- servo injection robots
- Servo-Driven Robot
- Setup of injection machine
- Silicone Injection Molding Machine
- six-axis industrial robot
- Stainless Hopper Dryer
- Stainless Hopper Dryers
- star club
- swing arm robot
- the choice between servo-driven robots and hydraulic robots will have a certain impact on efficiency
- the most popular injection molding machine
- the type of injection molding robot
- toggle clamp injection molding machine
- Toggle Hydraulic Injection Molding Machines
- toggle injection molding machine
- Top 10 brands of injection robots
- Topstar
- Topstar Engineering
- Topstar Industrial Robots
- Topstar injection molding intelligent
- Topstar Scara Robots
- Useful Injection molding machine
- Vertical machining centers
- volumetric type blender
- water chiller
- water chillers
- water distributor
- Water Type MoldTemperature Controller
- We often face choices when performing injection molding. We will choose the type of injection molding machine
- wholesale of injection molding machines
- x carve CNC