How do I prevent scaling and corrosion in mould temperature controller?
2024/11/18 By Topstar
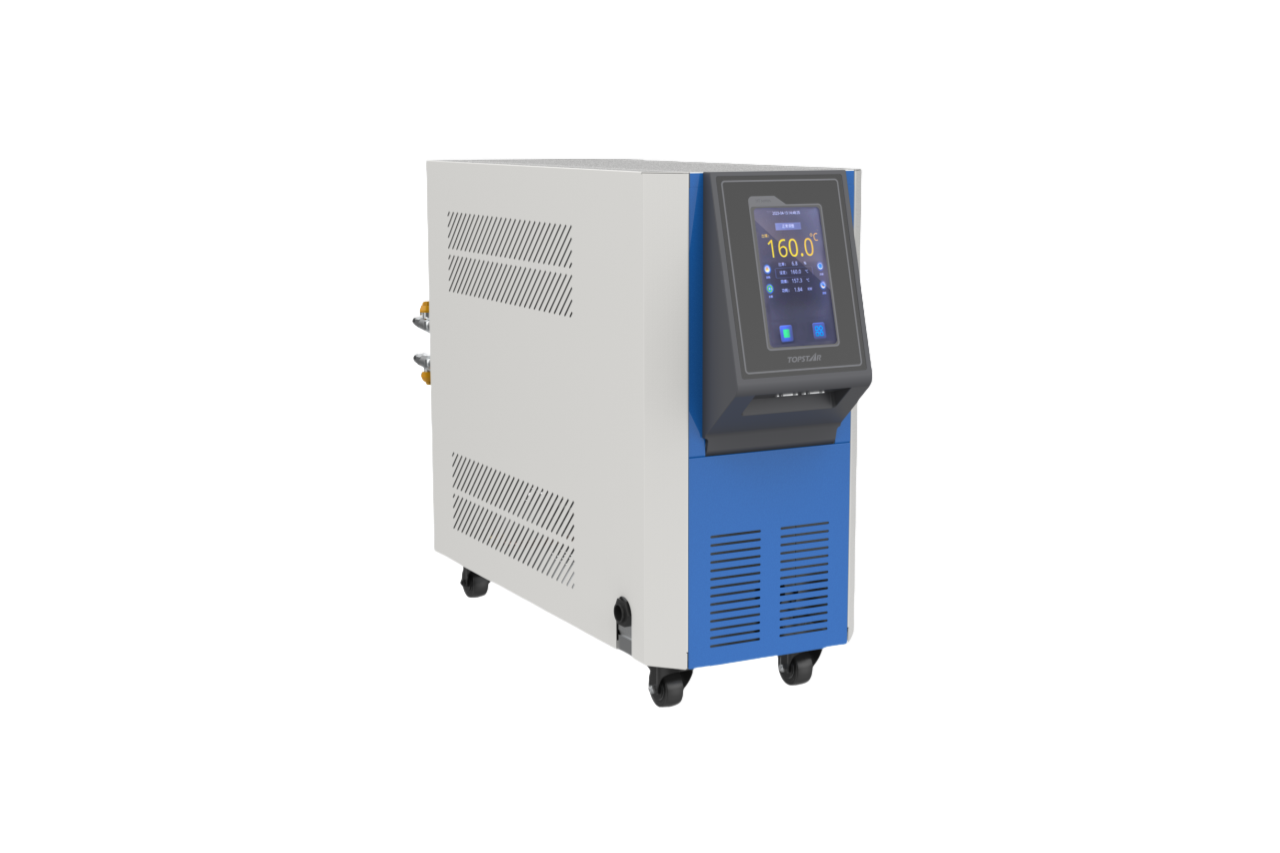
A mould temperature controller is essential equipment in injection moulding, helping to maintain consistent mould temperature to ensure part quality and operating efficiency. Most products are injected using water-type mould temperature controllers, often the most prone to common problems such as scaling and corrosion when used. It affects the performance of the equipment, resulting in poor water quality, low efficiency, easy downtime and increased maintenance. Therefore, in this article, we will share with you how to solve this problem in the Topstar fourth-generation mould temperature controller and reduce the occurrence of scaling and corrosion.
Causes of scaling and corrosion in mould temperature controller
Scaling and corrosion are common problems with many mould temperature controllers. Scaling refers to the precipitation of minerals from the water or heat transfer fluid used in the mould temperature controller. These deposits accumulate on the internal surface, reducing heat transfer efficiency and blocking the flow channel. Corrosion is the chemical reaction that deteriorates the metal parts inside, usually caused by oxygen, low pH or incompatible fluids. Poor water quality, improper maintenance, incorrect heat transfer fluids, and hardware issues can cause both problems. For example, untreated hard water is the main cause of scaling, while high temperatures and chemical contaminants exacerbate corrosion.
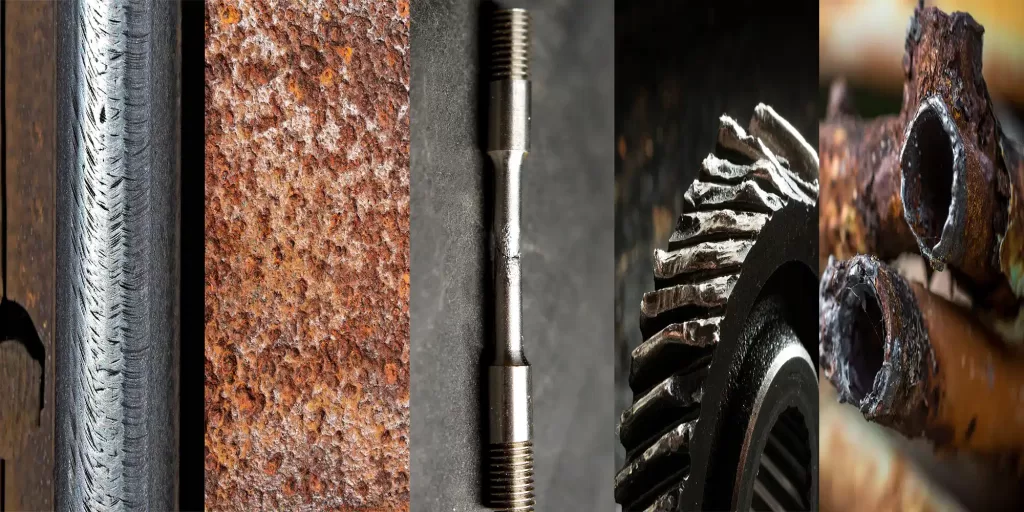
Improving water quality in preventing scaling and corrosion
Water quality plays a key role in preventing scaling and corrosion of mould temperature controllers. Topstar’s mould temperature controller series will have a dedicated pure water series that can come with its water tank. It will use pure water as a circulating medium and a closed circulation system to prevent metal ions from corroding the mould and scale from clogging it. Reduce the requirements for water quality, in addition to avoiding scaling and corrosion, using pure water as a circulating medium has many advantages. Pure water can maintain consistent heat transfer performance without interference from dissolved minerals or suspended particles, improving the system’s thermal efficiency. This allows for more precise temperature control, essential for achieving consistent product quality in applications that require precision, such as the automotive, medical, and electronics industries.
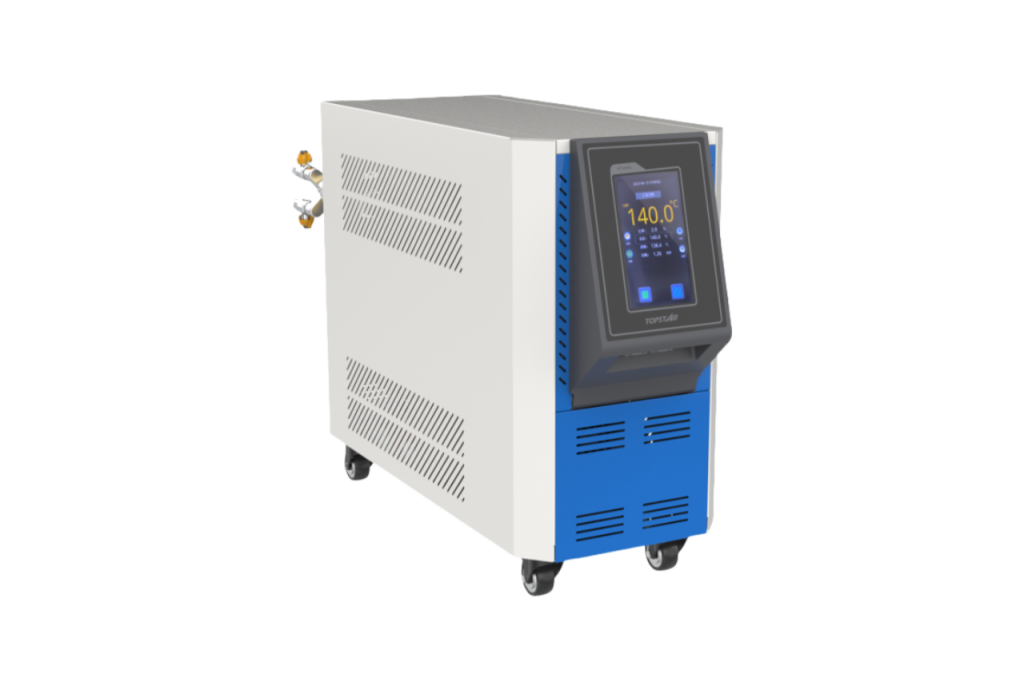
Reduce damage to components such as water pumps, pipes, solenoid valves, etc.
In the daily operation of the mould temperature controller, the temperature changes that occur when metal pipe parts undergo continuous heating and cooling cycles can easily lead to metal fatigue, resulting in structural damage to the pipe parts. Topstar installs a gas collector in the mould temperature controller to mitigate these damages. They play a dual role in protecting system components. First, it acts as a buffer, absorbing the additional pressure generated by the thermal expansion and contraction of the water in the system. By balancing pressure fluctuations, the gas collector prevents sudden pressure peaks that could otherwise strain and damage sensitive components such as water pumps and solenoid valves.
Second, the gas collector also solves another problem in the mould temperature controller: accumulating dissolved gases in the circulating water. During the heating process, the gases naturally dissolved in the water are released, forming bubbles, which can cause cavitation in the pump and other flow interruptions in the pipeline. The gas collector provides a designated space for these released gases to accumulate, preventing them from recirculating into the system.
Solve the problem of a mould temperature controller and mould rust
Residual media inside the mould usually causes rust or pipe blockage and reduces product yield. The mould temperature controller uses heat medium recovery technology to completely replace the residual press in the mould with high-pressure gas, thereby preventing mould damage and improving product yield. Replacing the media after each cycle can significantly reduce the risk of corrosion and blockage. This process ensures no stagnant liquid in the mould, which could otherwise become a breeding ground for rust or cause certain compounds to crystallize.
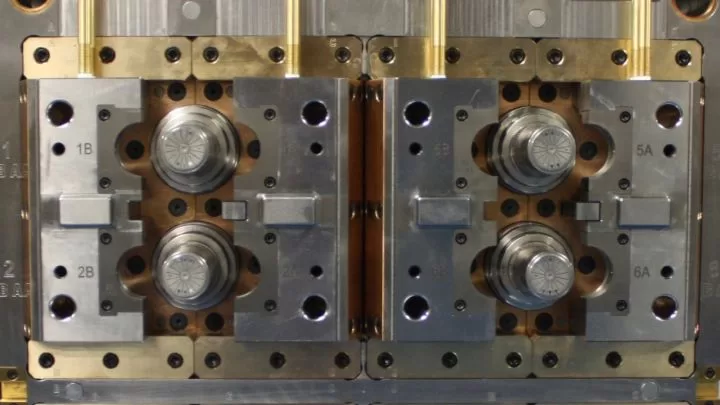
At the same time, it prevents rust, which can weaken metal structures and cause premature wear. This can lead to fewer mould changes and lower maintenance costs. In addition, this method not only cleans the mould but also prevents contamination of the circulating medium in the mould temperature controller.
Real-time monitoring of mould temperature controller parameters
Maintaining correct operating conditions is important to prevent mould temperature controller scaling and corrosion. Key parameters that need to be monitored include temperature, pressure and pH. Extreme temperatures accelerate scaling and corrosion, while pressure fluctuations stress system components. pH control is particularly important because acidic or alkaline conditions can exacerbate corrosion. Using pH-neutral heat transfer fluids and regularly testing the pH of the liquid can help maintain a stable environment within the MTC. In Topstar’s injection moulding system, a monitoring system that provides real-time data allows users to make adjustments immediately to prevent damage.
Better prevention of scaling and rusting
Scaling and corrosion are common challenges for mould temperature controllers, but they can be effectively managed through proactive measures. By maintaining water quality, heat recovery technology, etc., users can protect the mould temperature controller from damage and ensure consistent performance.
TRENDING POSTS
- What factors can cause delays in the injection molding process of plastic molding machine? 2024/11/18
- Exhibition Review| Topstar participates in InterPlas Thailand 2024 2024/11/18
- Star Case | Topstar helps Santong upgrade its intelligent plant 2024/11/18
- Topstar Special | National Science and Technology Workers Day 2024/11/18
HOT TOPIC
- .ervo motor-driven linear robots
- 3 axis robot
- 3 axis robots
- 3 in 1 Compact Dehumidifying Dryer
- 3-axis robot
- 3-axis robots
- 5-axis CNC machine
- accuracy
- Air Chillers
- all electric injection molding machine
- all electric injection molding machines
- All-electric injection molding machines
- and overall production quality. Therefore
- AP-RubberPlas
- automated injection molding machine
- Automation changed engineering
- automation of injection molding robots
- auxiliary machine
- Bench Injection Molding Machine
- Cabinet dryer manufacturers
- Cabinet dryers
- chiller
- CNC Drilling Machine
- CNC Drilling Machines
- cnc engraving machine manufacturer
- cnc laser cutting machine manufacturer
- CNC machine
- CNC Machine Center
- CNC Machine for Sale
- CNC Machine Manufacturing
- CNC Machine Tool
- CNC machine tool product
- CNC Machining Center
- CNC wood carving machine
- Cooling system
- Cross-Walking Single Axis Servo Cylinder Robot
- Cross-Walking Single-Axis Servo Cylinder Robot
- Cross-Walking Three-Axis/Five-Axis Servo Driven Robot
- cross-walking three-axis/five-axis servo-driven robot
- Dehumidifier Dryer
- Dehumidifying Dryer
- delta parallel robot
- Desktop Injection Molding Machine
- Desktop injection molding machines
- Desktop Molding Machine
- desktop plastic injection machine
- Desktop Plastic Injection Molding Machine
- direct clamp injection molding machine
- Direct clamp injection molding machines
- Dosing & mixing system
- Drilling Centers
- Drying and dehumidification system
- drying and dehumidifying equipment
- Drying and Dehumidifying System
- drying system
- effective and efficient. Cabinet dryers are also used in other industries where large quantities of material need to be dried
- efficient injection molding machine
- elbow hydraulic injection molding machines
- electric injection molding machine
- electric injection molding machines
- energy-efficient injection molding robot
- energy-saving injection molding machine
- etc. Among injection molding robots
- exhibition
- features of CNC machine
- Feeding And Conveying System
- Five Axis Machine Center
- Fully automatic injection molding machine
- Gathering Topstar
- giant injection molding machine
- GMU-600 5-Axis Machining Center
- Granulating & Recycling System
- Heavy duty injection molding machine
- High-precision electric molding machines
- high-precision plastic molding machines
- high-speed all electric injection molding machine
- Honeycomb rotor dehumidifier
- horizontal injection molding machine
- Horizontal Injection Molding Machines
- Horizontal Injection Moulding Machine
- Horizontal Mixer manufacturer
- How The CNC Machine Works
- hybrid injection molding machine
- hydraulic injection molding machine
- Hydraulic Injection Molding Machines
- in this article
- Industrial robot
- Industrial Robot Chinese brand
- industrial robot parts
- industrial robot supplier
- Industrial robots
- Industry Chain
- Injection Manipulator
- injection manipulator robot
- injection mold machines
- Injection molding
- Injection molding automation
- Injection Molding Automation Solution
- injection molding dryer
- Injection molding equipment
- injection molding hopper dryer
- Injection molding machine
- injection molding machine brand
- Injection Molding Machine Factory
- Injection Molding Machine Manufacture
- Injection molding machine manufacturer
- injection molding machine manufacturers
- Injection molding machine procurement
- injection molding machine robotic arm
- injection molding machine with a robot
- Injection molding machines
- injection molding material dehumidifying
- injection molding plant
- Injection Molding Robot
- injection molding robot arm
- Injection molding robot automation
- Injection molding robotic arm
- injection molding robots
- Injection moulding machine
- Injection Moulding Robots
- Injection Robot
- Injection robot arm
- Injection robot manufacturer
- Injection robot wholesale
- injection robots
- intelligent injection molding machines
- Introducing Injection Robot
- It is the best choice for drying large quantities of material at once. Cabinetmakers use these machines because they are fast
- large injection molding machine
- Learn what industrial automation and robotics is
- linear robot
- linear robots
- low speed sound-proof granulator
- machine plastic molding
- make sure to add some! Improvements (2) Keyphrase in introduction: Your keyphrase or its synonyms appear in the first paragraph of the copy
- manipulator machine
- manufacturing
- medical grade injection molding machines
- medical injection molding machine
- medical injection molding machines
- micro injection molding machine
- middle speed granulator
- Mini CNC machine manufacturers.
- Mold Temperature Control System
- mold temperature controller
- mold temperature controllers
- molding material Dehumidifying System
- mould temperature control system
- mould temperature controller
- mould temperature controllers
- New electric injection molding machine
- nitrogen dryer manufacturer
- nitrogen dryer system manufacturer
- Oil type mold temperature controller
- Oil type mold temperature controllers
- open day
- Outbound links: No outbound links appear in this page. Add some! Images: No images appear on this page. Add some! Internal links: No internal links appear in this page
- PET Preform injection molding
- phone case maker machine
- phone case making machine
- plastic bottle making machine
- plastic bottle manufacturing
- plastic bucket making machine
- plastic bucket manufacturing
- Plastic chair making machine
- plastic forming equipment
- plastic hopper dryer
- plastic injection machine
- plastic injection machines
- plastic injection molding
- Plastic injection molding equipment
- Plastic injection molding machine
- Plastic Injection Molding Machines
- plastic injection moulding machine
- plastic injection robot
- Plastic Molding machine
- Plastic Molding Machines
- plastic molding press
- plastic moulding machine
- plastic phone case making machine
- plastic-molding machine
- powerful granulator
- Powerful Type Sound-Proof Granulator
- precision injection molding
- precision injection molding machines
- production of plastic seats
- pure water mould temperature controller
- Robot injection molding
- robot injection molding machine
- robot manufacturing companies
- Robotic arm for injection molding machine
- robotic injection molding machines
- robotics in injection molding
- SCARA robot
- SCARA robots
- Service-oriented manufacturing
- Servo Cylinder Robot
- servo driven robot
- Servo Driven Robots
- servo injection robots
- servo motor-driven linear robots
- servo-driven 3-axis robot
- Servo-Driven Robot
- Setup of injection machine
- Silicone Injection Molding Machine
- six-axis industrial robot
- Stainless Hopper Dryer
- Stainless Hopper Dryers
- star club
- swing arm robot
- take-out robots
- the choice between servo-driven robots and hydraulic robots will have a certain impact on efficiency
- the most popular injection molding machine
- the type of injection molding robot
- toggle clamp injection molding machine
- Toggle Hydraulic Injection Molding Machines
- toggle injection molding machine
- Top 10 brands of injection robots
- Topstar
- Topstar Engineering
- Topstar Industrial Robots
- Topstar injection molding intelligent
- Topstar Scara Robots
- Useful Injection molding machine
- Vertical machining centers
- volumetric type blender
- water chiller
- water chillers
- water distributor
- water type mold temperature controller
- Water Type MoldTemperature Controller
- Water-Type Mould Temperature Controllers
- We often face choices when performing injection molding. We will choose the type of injection molding machine
- wholesale of injection molding machines
- x carve CNC