How can we improve cleanliness in plastic bottle manufacturing?
2024/07/17 By Topstar
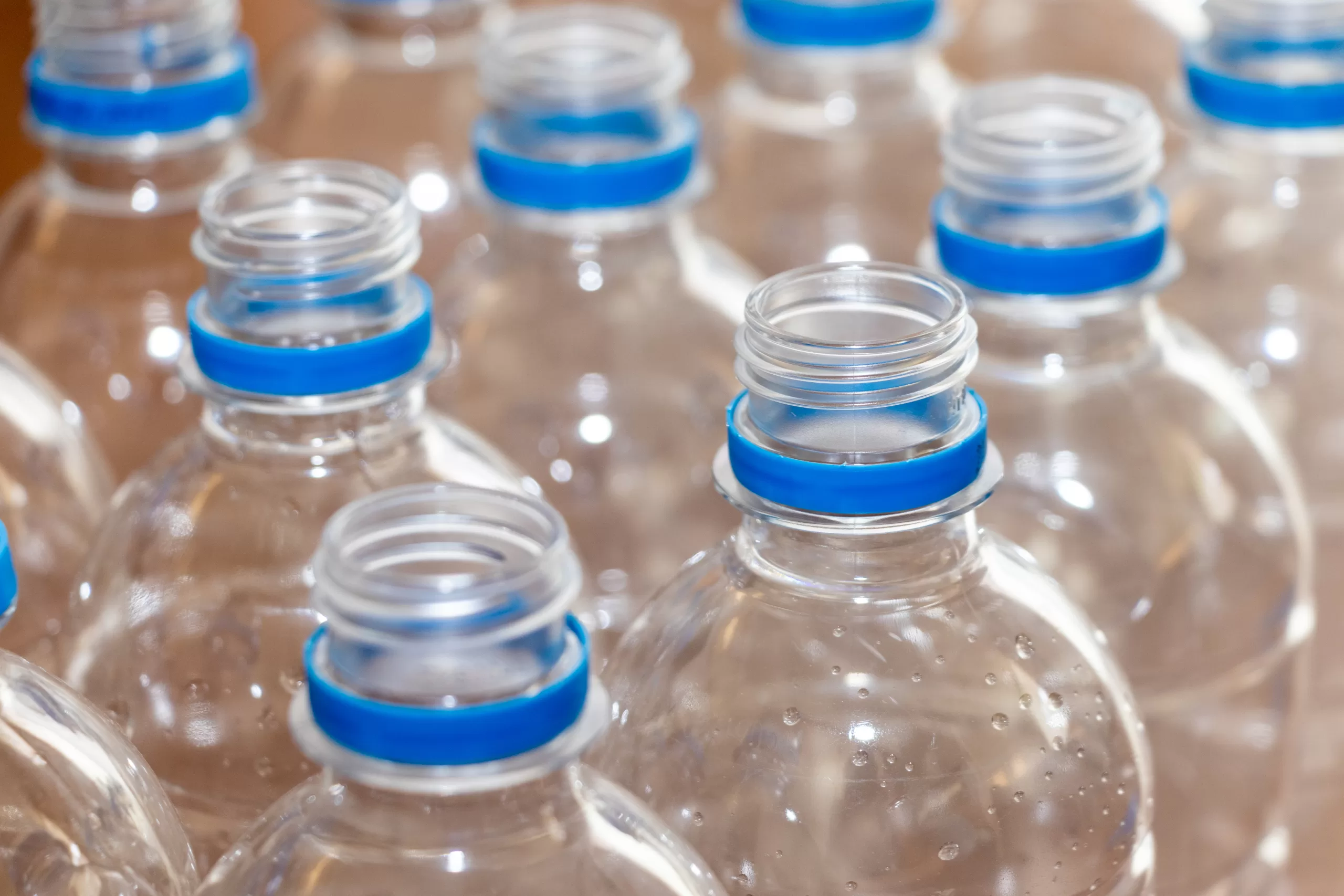
When plastic bottle manufacturing, the cleanliness of the entire injection molding process will also affect product quality, cleanliness ensures consumer safety and meets relevant regulatory standards. As a company specializing in the production of injection molding machines, Topstar will provide you with a best practice guide and technology sharing to improve the cleanliness of the manufacturing process.
Importance of Cleanliness in Plastic Bottle Manufacturing
Cleanliness in the plastic bottle manufacturing process is not only about aesthetics. It is also an issue that affects product quality, consumer safety and regulatory compliance. Contaminants throughout the injection molding process can cause defects in the final product. In addition, the presence of contaminants can also pose serious health risks, especially in bottles used to hold beverages and medicines.

In plastic bottle manufacturing, cleanliness ensures that the materials used are free of impurities that may negatively affect the performance of the plastic. This includes preventing cross-contamination from other materials and environmental contaminants such as residues from previous production cycles. High standards of cleanliness help achieve consistent product quality, and regulatory agencies such as the US FDA and EFSA have strict guidelines for cleanliness during the manufacturing process of products that come into contact with food.
Maintaining a clean plastic bottle manufacturing environment
One of the most effective ways to ensure cleanliness in plastic bottle production is to implement cleanroom standards to keep the environment clean. Cleanroom standards refer to environments where the system minimizes the concentration of particles in the air to prevent contamination.
To achieve such standards, manufacturers must invest in facilities that provide controlled environments, including appropriate filtration systems, airflow management, and temperature and humidity control. High-efficiency HEPA filters are typically used to remove particles as small as 0.3 microns, ensuring that the air in the cleanroom is free of contaminants. Relevant personnel must follow strict procedures, including wearing gloves, masks and protective clothing to minimize the entry of contaminants.
Improve cleanliness with electric injection molding machines
The advantage of using electric injection molding machines is that they do not require hydraulic oil. Traditional hydraulic injection molding machines use a lot of hydraulic oil to operate, which may bring risks of leaks and contamination. These leaks can introduce contaminants into the manufacturing environment, affecting the purity of the plastic bottles.
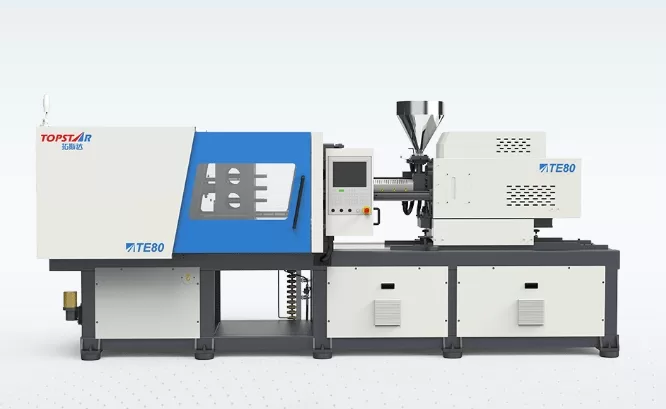
In contrast, electric injection molding machines are driven by servo motors and do not require hydraulic oil. The drive provided by the servo motor can control the injection process more accurately. The intelligent electric mold opening and closing also makes the injection molding repeatability high, the clamping is stable, and the mold opening position is accurate, thereby reducing defects such as trimming burrs or excess materials and also reducing the generation of plastic dust and debris. They are also quieter and have less vibration when operating. It can reduce the airborne particles generated during molding due to mechanical interference.
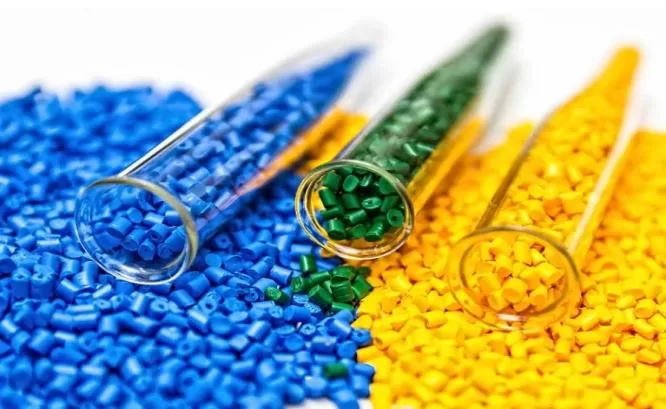
Ensure the purity of raw materials
The purity of raw materials used in plastic bottle manufacturing is also critical in maintaining cleanliness. If there are contaminants in the raw materials, it will directly lead to defects in the final product. First, when purchasing, choosing suppliers who can comply with strict quality control standards is necessary. Second, it is necessary to maintain the purity of raw materials in material handling and storage. Store them in a clean, dry and temperature-controlled environment to prevent contamination by dust, moisture and other environmental factors. Different materials also require special storage containers and handling equipment to prevent contamination.
Keep the equipment clean
Although it is recommended that you use electric injection molding machines, proper maintenance is still required. Over time, contaminants will accumulate on the surface of the equipment, causing defects in the final product and posing health risks. Include the mold, nozzle, and barrel in your regular cleaning process and check for residue or wear. Regular maintenance and calibration of your equipment will also help prevent contamination from wear, so you need to replace worn parts, lubricate moving parts, and ensure everything is operating correctly.
Make the manufactured plastic bottles safer
Product quality safety is paramount, so every critical link needs to be implemented well. We can significantly improve the cleanliness of the production process by keeping the injection molding environment clean, using electric injection molding machines, and maintaining regular cleaning to maintain the purity of raw materials.
TRENDING POSTS
- What factors can cause delays in the injection molding process of plastic molding machine? 2024/07/17
- Exhibition Review| Topstar participates in InterPlas Thailand 2024 2024/07/17
- Star Case | Topstar helps Santong upgrade its intelligent plant 2024/07/17
- Topstar Special | National Science and Technology Workers Day 2024/07/17
HOT TOPIC
- .ervo motor-driven linear robots
- 3 axis robot
- 3 axis robots
- 3 in 1 Compact Dehumidifying Dryer
- 3-axis robot
- 3-axis robots
- 5-axis CNC machine
- accuracy
- Air Chillers
- all electric injection molding machine
- all electric injection molding machines
- All-electric injection molding machines
- and overall production quality. Therefore
- AP-RubberPlas
- automated injection molding machine
- Automation changed engineering
- automation of injection molding robots
- auxiliary machine
- Bench Injection Molding Machine
- Cabinet dryer manufacturers
- Cabinet dryers
- chiller
- CNC Drilling Machine
- CNC Drilling Machines
- cnc engraving machine manufacturer
- cnc laser cutting machine manufacturer
- CNC machine
- CNC Machine Center
- CNC Machine for Sale
- CNC Machine Manufacturing
- CNC Machine Tool
- CNC machine tool product
- CNC Machining Center
- CNC wood carving machine
- Cooling system
- Cross-Walking Single Axis Servo Cylinder Robot
- Cross-Walking Single-Axis Servo Cylinder Robot
- Cross-Walking Three-Axis/Five-Axis Servo Driven Robot
- cross-walking three-axis/five-axis servo-driven robot
- Dehumidifier Dryer
- Dehumidifying Dryer
- delta parallel robot
- Desktop Injection Molding Machine
- Desktop injection molding machines
- Desktop Molding Machine
- desktop plastic injection machine
- Desktop Plastic Injection Molding Machine
- direct clamp injection molding machine
- Direct clamp injection molding machines
- Dosing & mixing system
- Drilling Centers
- Drying and dehumidification system
- drying and dehumidifying equipment
- Drying and Dehumidifying System
- drying system
- effective and efficient. Cabinet dryers are also used in other industries where large quantities of material need to be dried
- efficient injection molding machine
- elbow hydraulic injection molding machines
- electric injection molding machine
- electric injection molding machines
- energy-efficient injection molding robot
- energy-saving injection molding machine
- etc. Among injection molding robots
- exhibition
- features of CNC machine
- Feeding And Conveying System
- Five Axis Machine Center
- Fully automatic injection molding machine
- Gathering Topstar
- giant injection molding machine
- GMU-600 5-Axis Machining Center
- Granulating & Recycling System
- Heavy duty injection molding machine
- High-precision electric molding machines
- high-precision plastic molding machines
- high-speed all electric injection molding machine
- Honeycomb rotor dehumidifier
- horizontal injection molding machine
- Horizontal Injection Molding Machines
- Horizontal Injection Moulding Machine
- Horizontal Mixer manufacturer
- How The CNC Machine Works
- hybrid injection molding machine
- hydraulic injection molding machine
- Hydraulic Injection Molding Machines
- in this article
- Industrial robot
- Industrial Robot Chinese brand
- industrial robot parts
- industrial robot supplier
- Industrial robots
- Industry Chain
- Injection Manipulator
- injection manipulator robot
- injection mold machines
- Injection molding
- Injection molding automation
- Injection Molding Automation Solution
- injection molding dryer
- Injection molding equipment
- injection molding hopper dryer
- Injection molding machine
- injection molding machine brand
- Injection Molding Machine Factory
- Injection Molding Machine Manufacture
- Injection molding machine manufacturer
- injection molding machine manufacturers
- Injection molding machine procurement
- injection molding machine robotic arm
- injection molding machine with a robot
- Injection molding machines
- injection molding material dehumidifying
- injection molding plant
- Injection Molding Robot
- injection molding robot arm
- Injection molding robot automation
- Injection molding robotic arm
- injection molding robots
- Injection moulding machine
- Injection Moulding Robots
- Injection Robot
- Injection robot arm
- Injection robot manufacturer
- Injection robot wholesale
- injection robots
- intelligent injection molding machines
- Introducing Injection Robot
- It is the best choice for drying large quantities of material at once. Cabinetmakers use these machines because they are fast
- large injection molding machine
- Learn what industrial automation and robotics is
- linear robot
- linear robots
- low speed sound-proof granulator
- machine plastic molding
- make sure to add some! Improvements (2) Keyphrase in introduction: Your keyphrase or its synonyms appear in the first paragraph of the copy
- manipulator machine
- manufacturing
- medical grade injection molding machines
- medical injection molding machine
- medical injection molding machines
- micro injection molding machine
- middle speed granulator
- Mini CNC machine manufacturers.
- Mold Temperature Control System
- mold temperature controller
- mold temperature controllers
- molding material Dehumidifying System
- mould temperature control system
- mould temperature controller
- mould temperature controllers
- New electric injection molding machine
- nitrogen dryer manufacturer
- nitrogen dryer system manufacturer
- Oil type mold temperature controller
- Oil type mold temperature controllers
- open day
- Outbound links: No outbound links appear in this page. Add some! Images: No images appear on this page. Add some! Internal links: No internal links appear in this page
- PET Preform injection molding
- phone case maker machine
- phone case making machine
- plastic bottle making machine
- plastic bottle manufacturing
- plastic bucket making machine
- plastic bucket manufacturing
- Plastic chair making machine
- plastic forming equipment
- plastic hopper dryer
- plastic injection machine
- plastic injection machines
- plastic injection molding
- Plastic injection molding equipment
- Plastic injection molding machine
- Plastic Injection Molding Machines
- plastic injection moulding machine
- plastic injection robot
- Plastic Molding machine
- Plastic Molding Machines
- plastic molding press
- plastic moulding machine
- plastic phone case making machine
- plastic-molding machine
- powerful granulator
- Powerful Type Sound-Proof Granulator
- precision injection molding
- production of plastic seats
- pure water mould temperature controller
- Robot injection molding
- robot injection molding machine
- robot manufacturing companies
- Robotic arm for injection molding machine
- robotic injection molding machines
- robotics in injection molding
- SCARA robot
- SCARA robots
- Service-oriented manufacturing
- Servo Cylinder Robot
- servo driven robot
- Servo Driven Robots
- servo injection robots
- servo motor-driven linear robots
- servo-driven 3-axis robot
- Servo-Driven Robot
- Setup of injection machine
- Silicone Injection Molding Machine
- six-axis industrial robot
- Stainless Hopper Dryer
- Stainless Hopper Dryers
- star club
- swing arm robot
- take-out robots
- the choice between servo-driven robots and hydraulic robots will have a certain impact on efficiency
- the most popular injection molding machine
- the type of injection molding robot
- toggle clamp injection molding machine
- Toggle Hydraulic Injection Molding Machines
- toggle injection molding machine
- Top 10 brands of injection robots
- Topstar
- Topstar Engineering
- Topstar Industrial Robots
- Topstar injection molding intelligent
- Topstar Scara Robots
- Useful Injection molding machine
- Vertical machining centers
- volumetric type blender
- water chiller
- water chillers
- water distributor
- water type mold temperature controller
- Water Type MoldTemperature Controller
- Water-Type Mould Temperature Controllers
- We often face choices when performing injection molding. We will choose the type of injection molding machine
- wholesale of injection molding machines
- x carve CNC