How can Topstar plastic injection molding machine help European countries solve injection molding problems?
2025/02/24 By Topstar
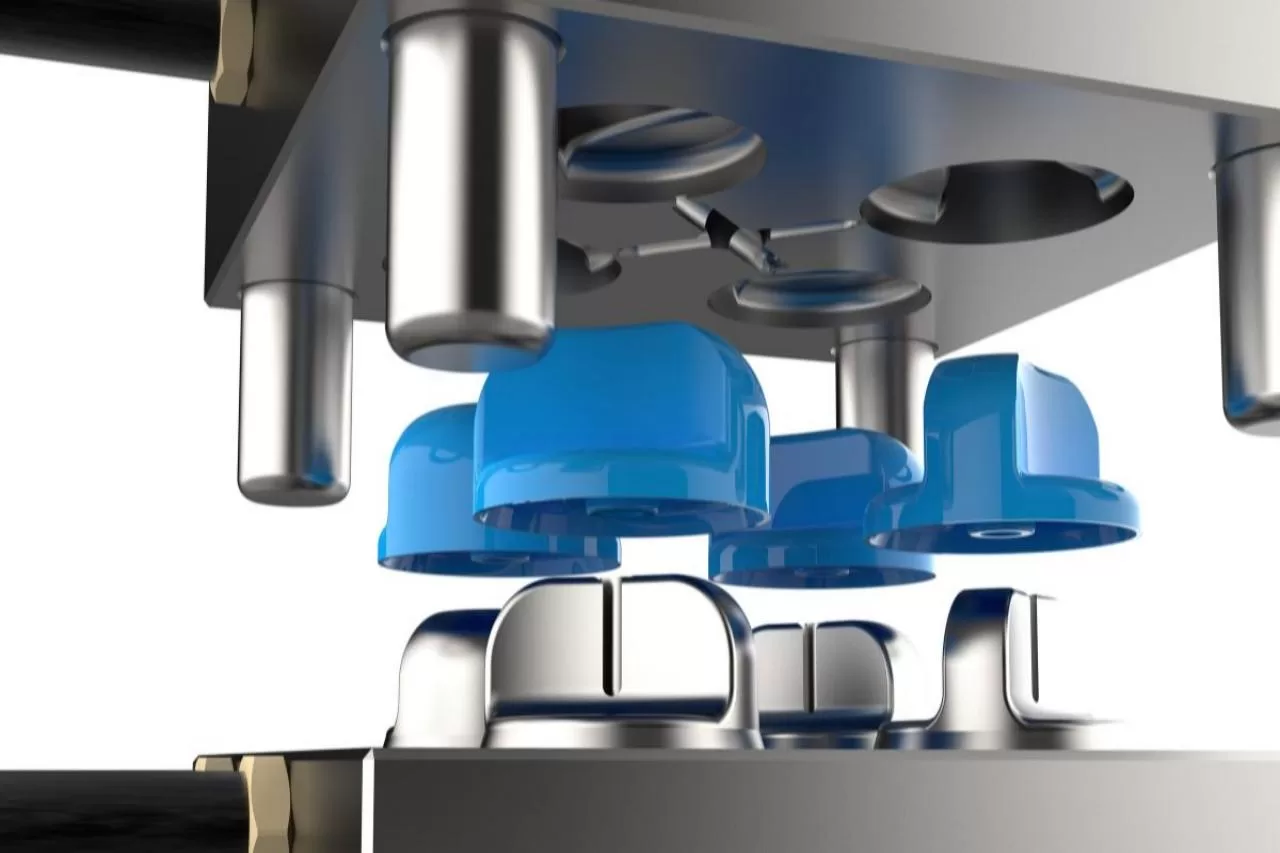
Challenges such as rising energy costs, an aging workforce, and increased competition from low-cost Asian manufacturers have put tremendous pressure on European manufacturers, especially in industries such as injection molding. Due to various environmental issues, these countries face severe economic dislocation, which has caused energy prices to soar. Injection molding is energy-intensive, and rising costs make it more difficult for manufacturers to remain profitable. At the same time, in Europe, there are high requirements for product quality, regardless of the industry. With the increasing demand for high-value customized products, manufacturers need flexible and energy-saving solutions to remain competitive. Topstar plastic injection molding machine have successfully entered the European market, and this article will also introduce how to help European manufacturers overcome these problems, especially in countries such as France and Spain.
Rising Energy Costs and the Role of Plastic Injection Molding Machine in Reducing Energy Consumption
One of the most pressing issues facing European manufacturers is rising energy prices. In the past few years, due to geopolitical instability, industrial electricity prices in France have soared by more than 300%, putting tremendous pressure on high-energy processes such as injection molding. The injection molding process involves heating plastics to high temperatures and is inherently energy-intensive. However, with rising energy prices, European manufacturers must find ways to maintain productivity without spending much money.
Topstar plastic injection molding machines have energy-saving technologies, significantly reducing overall power consumption. Topstar’s TE II series machines feature integrated chillers, discrete intelligent drive systems, and optimized heating methods, all of which help manage energy use more efficiently. By adopting this energy-saving injection molding machine, manufacturers in the French region can significantly reduce energy use without sacrificing performance or output.
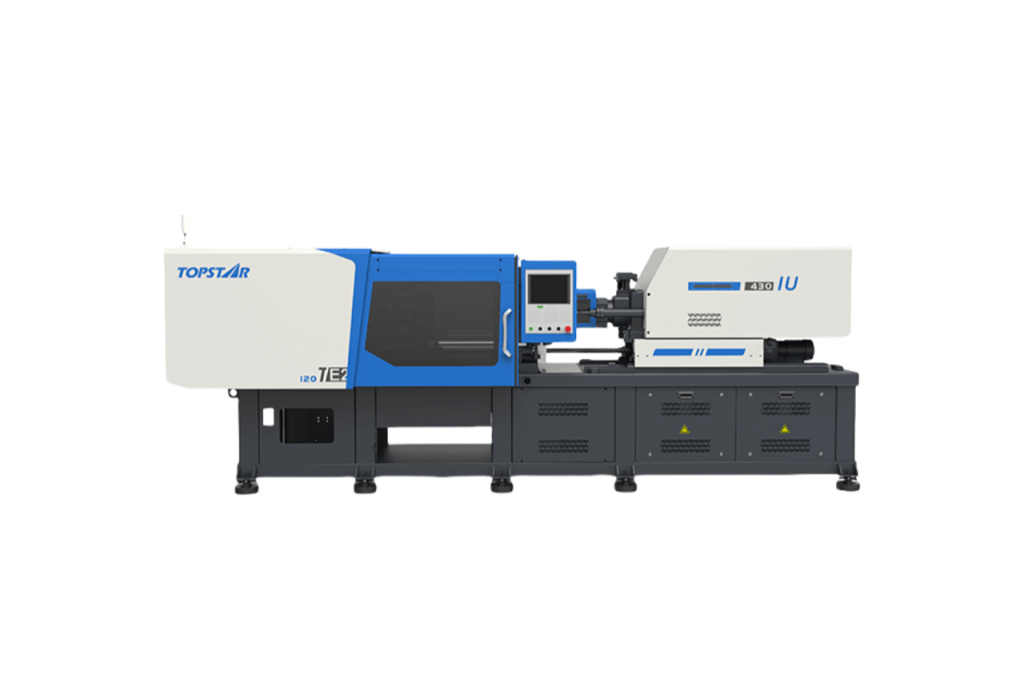
Addressing the skills gap in the manufacturing workforce
The European manufacturing industry is facing a significant challenge with an aging workforce. Skilled workers, especially in high-demand positions such as mold design and equipment operation, are retiring, and the younger generation cannot fill these positions at the same rate. In Spain, for example, where youth unemployment hovers around 30%, manufacturing is not an attractive career path for many young people.
To bridge this skills gap, Topstar plastic injection molding machines offer user-friendly intelligent automation features that simplify complex tasks for operators. Designed with an intuitive interface and automated processes, the TE II series machines reduce the need for a highly skilled workforce to manage daily operations. In addition, we have adopted the “injection molding integration” concept to integrate injection robots and auxiliary equipment into the injection molding process, allowing less experienced operators to perform tasks such as mold changes, material handling and quality control without extensive training. Compared with traditional automation, these systems reduce the dependence on skilled workers while maintaining high production standards.
Increasing competition through value-added products
Faced with the incentive competition brought by price wars from other countries in other regions, European manufacturers have gradually shifted their focus to higher value-added products. This includes precision parts in industries such as automobiles and medical devices, where quality, customization and fast delivery are crucial. However, this shift also requires greater flexibility in production processes and the ability to quickly adapt to changing customer needs. Topstar’s plastic injection molding machines have flexible and high-performance systems that can quickly switch between different product designs. The TE II series is particularly suitable for industries such as automobiles and medical device manufacturing, where precision, customization and short delivery times are essential.
For example, research on silicone headlight molding technology in Europe has achieved remarkable results. Topstar has launched dedicated solutions for silicone headlight molding technology, which can provide European automotive lighting industry customers with one-stop services from silicone raw materials, mold design, injection molding equipment and solutions.
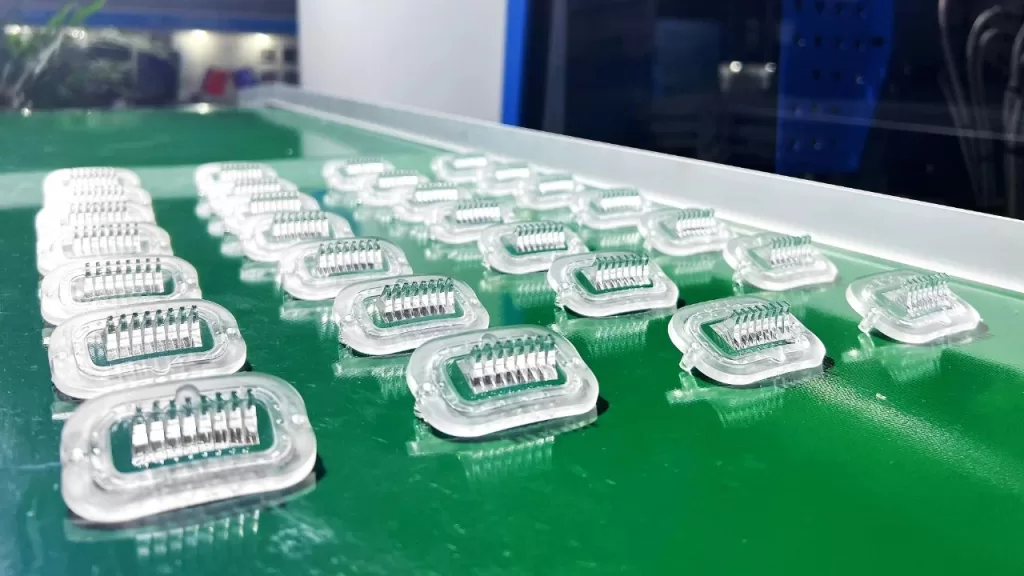
Flexibility in manufacturing and the need for customized production
With the growing customer demand for customized products and shorter delivery times, traditional mass production methods are becoming less and less viable. Therefore, European manufacturers must adopt more flexible and agile production processes to respond quickly to customer needs. The plastic injection molding machines provided by Topstar provide highly flexible manufacturing solutions that can quickly adapt to different production needs. Among them, the TE II series uses injection molding process integration, combining injection molding machines with auxiliary equipment such as robots and automation systems. This integration helps to simplify the production process, reduce setup time and improve responsiveness to customer orders. This flexible manufacturing system allows European companies to quickly adapt to changing customer needs, whether in small batches of customized medical parts or large-scale production of automotive parts.
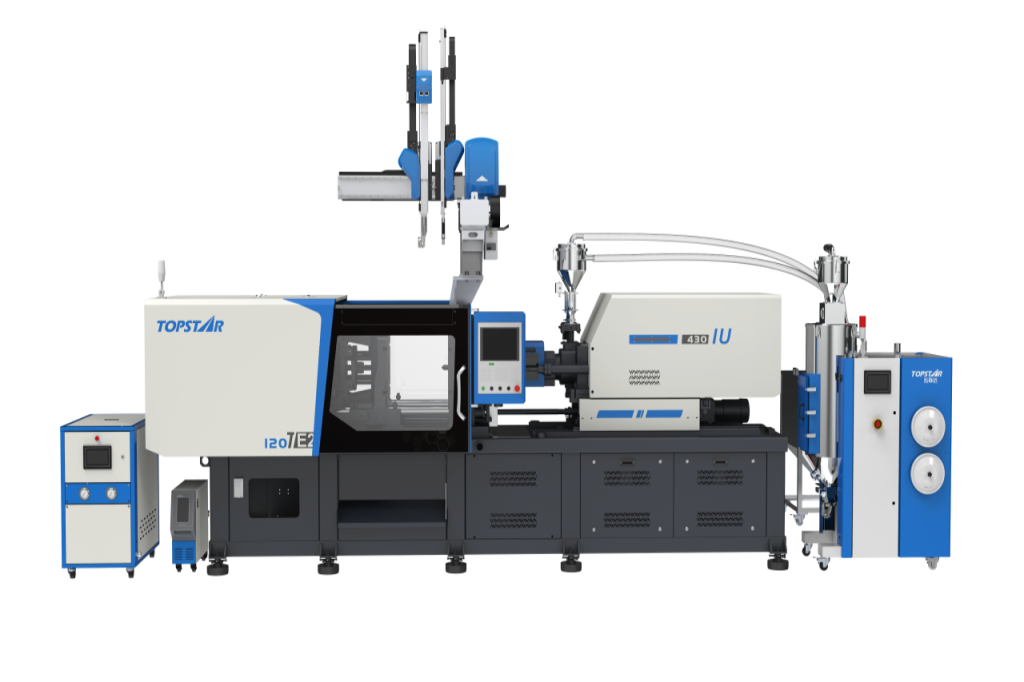
Reduce production costs with plastic injection molding machine.
In dealing with rising energy costs and labor shortages, European manufacturers are also under constant pressure to reduce production costs. Traditional injection molding processes usually involve many independent machines and systems, resulting in inefficiencies, long setup times and high operating costs. Topstar has solved this problem well through “injection molding process integration.” By integrating plastic injection molding machines with peripheral equipment such as injection molding robots and auxiliary equipment, Topstar’s machines reduce the need for complex equipment settings and the number of adjustments required during production. This simplified process helps reduce operating costs, minimize waste, and improve production efficiency.
Providing injection molding solutions for European manufacturers
Topstar’s plastic injection molding machines provide European manufacturers with the tools they need to meet challenges such as rising energy costs, labor shortages, low-price competition and increased demand for high-value products. With their flexible, energy-saving design, European companies can remain competitive in industries such as medical devices, automobiles and consumer electronics. They meet the needs of manufacturers in France, Spain and throughout Europe for today’s fast-paced, high-precision industries while reducing costs and improving production efficiency.
TRENDING POSTS
- What factors can cause delays in the injection molding process of plastic molding machine? 2025/02/24
- Exhibition Review| Topstar participates in InterPlas Thailand 2024 2025/02/24
- Star Case | Topstar helps Santong upgrade its intelligent plant 2025/02/24
- Topstar Special | National Science and Technology Workers Day 2025/02/24
HOT TOPIC
- 3 in 1 Compact Dehumidifying Dryer
- 5-axis CNC machine
- accuracy
- Air Chillers
- all electric injection molding machine
- all electric injection molding machines
- All-electric injection molding machines
- and overall production quality. Therefore
- AP-RubberPlas
- automated injection molding machine
- Automation changed engineering
- automation of injection molding robots
- auxiliary machine
- Bench Injection Molding Machine
- Cabinet dryer manufacturers
- Cabinet dryers
- chiller
- CNC Drilling Machine
- CNC Drilling Machines
- cnc engraving machine manufacturer
- cnc laser cutting machine manufacturer
- CNC machine
- CNC Machine Center
- CNC Machine for Sale
- CNC Machine Manufacturing
- CNC Machine Tool
- CNC machine tool product
- CNC Machining Center
- CNC wood carving machine
- Cooling system
- Cross-Walking Single Axis Servo Cylinder Robot
- Cross-Walking Single-Axis Servo Cylinder Robot
- Cross-Walking Three-Axis/Five-Axis Servo Driven Robot
- cross-walking three-axis/five-axis servo-driven robot
- Dehumidifier Dryer
- Dehumidifying Dryer
- delta parallel robot
- Desktop Injection Molding Machine
- Desktop injection molding machines
- Desktop Molding Machine
- desktop plastic injection machine
- Desktop Plastic Injection Molding Machine
- direct clamp injection molding machine
- Direct clamp injection molding machines
- Dosing & mixing system
- Drilling Centers
- Drying and dehumidification system
- drying and dehumidifying equipment
- Drying and Dehumidifying System
- drying system
- effective and efficient. Cabinet dryers are also used in other industries where large quantities of material need to be dried
- efficient injection molding machine
- elbow hydraulic injection molding machines
- electric injection molding machine
- electric injection molding machines
- energy-saving injection molding machine
- etc. Among injection molding robots
- exhibition
- features of CNC machine
- Feeding And Conveying System
- Five Axis Machine Center
- Fully automatic injection molding machine
- Gathering Topstar
- giant injection molding machine
- GMU-600 5-Axis Machining Center
- Granulating & Recycling System
- Heavy duty injection molding machine
- Honeycomb rotor dehumidifier
- horizontal injection molding machine
- Horizontal Injection Molding Machines
- Horizontal Injection Moulding Machine
- Horizontal Mixer manufacturer
- How The CNC Machine Works
- hybrid injection molding machine
- hydraulic injection molding machine
- Hydraulic Injection Molding Machines
- in this article
- Industrial robot
- Industrial Robot Chinese brand
- industrial robot parts
- industrial robot supplier
- Industrial robots
- Industry Chain
- Injection Manipulator
- injection mold machines
- Injection molding
- Injection molding automation
- Injection Molding Automation Solution
- injection molding dryer
- Injection molding equipment
- injection molding hopper dryer
- Injection molding machine
- injection molding machine brand
- Injection Molding Machine Factory
- Injection Molding Machine Manufacture
- Injection molding machine manufacturer
- injection molding machine manufacturers
- Injection molding machine procurement
- injection molding machine robotic arm
- injection molding machine with a robot
- Injection molding machines
- injection molding material dehumidifying
- injection molding plant
- Injection Molding Robot
- injection molding robot arm
- Injection molding robot automation
- Injection molding robotic arm
- injection molding robots
- Injection Moulding Robots
- Injection Robot
- Injection robot arm
- Injection robot manufacturer
- Injection robot wholesale
- injection robots
- intelligent injection molding machines
- Introducing Injection Robot
- It is the best choice for drying large quantities of material at once. Cabinetmakers use these machines because they are fast
- large injection molding machine
- Learn what industrial automation and robotics is
- linear robot
- low speed sound-proof granulator
- machine plastic molding
- make sure to add some! Improvements (2) Keyphrase in introduction: Your keyphrase or its synonyms appear in the first paragraph of the copy
- manipulator machine
- manufacturing
- micro injection molding machine
- middle speed granulator
- Mini CNC machine manufacturers.
- Mold Temperature Control System
- mold temperature controller
- molding material Dehumidifying System
- mould temperature controller
- mould temperature controllers
- New electric injection molding machine
- nitrogen dryer manufacturer
- nitrogen dryer system manufacturer
- Oil type mold temperature controller
- open day
- Outbound links: No outbound links appear in this page. Add some! Images: No images appear on this page. Add some! Internal links: No internal links appear in this page
- PET Preform injection molding
- phone case maker machine
- phone case making machine
- plastic bottle making machine
- plastic bottle manufacturing
- plastic bucket making machine
- plastic bucket manufacturing
- Plastic chair making machine
- plastic forming equipment
- plastic hopper dryer
- plastic injection machine
- plastic injection machines
- plastic injection molding
- Plastic injection molding equipment
- Plastic injection molding machine
- Plastic Injection Molding Machines
- plastic injection robot
- Plastic Molding machine
- Plastic Molding Machines
- plastic molding press
- plastic phone case making machine
- plastic-molding machine
- powerful granulator
- Powerful Type Sound-Proof Granulator
- production of plastic seats
- Robot injection molding
- robot injection molding machine
- robot manufacturing companies
- Robotic arm for injection molding machine
- robotic injection molding machines
- robotics in injection molding
- SCARA robot
- SCARA robots
- Service-oriented manufacturing
- Servo Cylinder Robot
- servo driven robot
- Servo Driven Robots
- servo injection robots
- Servo-Driven Robot
- Setup of injection machine
- Silicone Injection Molding Machine
- six-axis industrial robot
- Stainless Hopper Dryer
- Stainless Hopper Dryers
- star club
- swing arm robot
- the choice between servo-driven robots and hydraulic robots will have a certain impact on efficiency
- the most popular injection molding machine
- the type of injection molding robot
- toggle clamp injection molding machine
- Toggle Hydraulic Injection Molding Machines
- toggle injection molding machine
- Top 10 brands of injection robots
- Topstar
- Topstar Engineering
- Topstar Industrial Robots
- Topstar injection molding intelligent
- Topstar Scara Robots
- Useful Injection molding machine
- Vertical machining centers
- volumetric type blender
- water chiller
- water chillers
- water distributor
- Water Type MoldTemperature Controller
- We often face choices when performing injection molding. We will choose the type of injection molding machine
- wholesale of injection molding machines
- x carve CNC