Main applications of granulator that you can’t expect!
2022/05/23 By Topstar
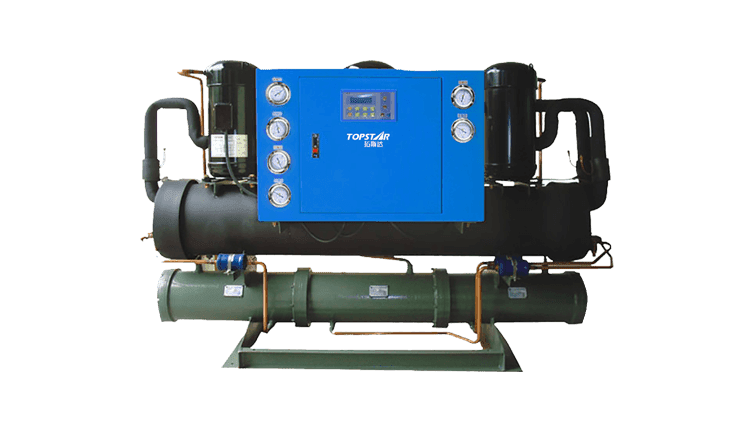
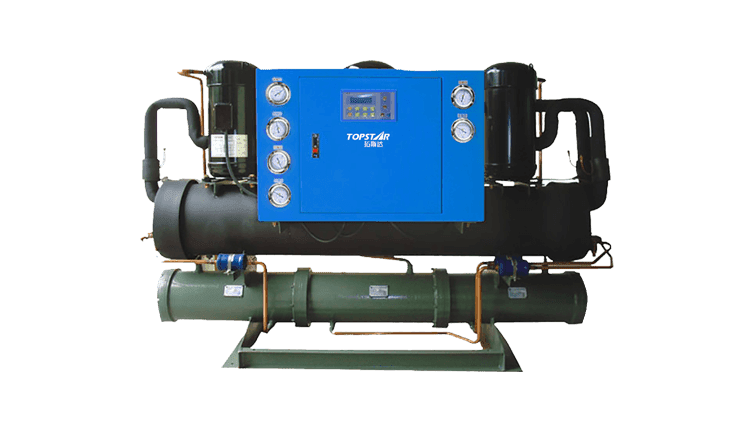
What is a plastic granulator?
Plastic granulators are consumable products that make recycled plastic granules from consumable products. Plastic granulator is usually a seamless and self-contained product. Moreover, after feeding raw materials into the machine, the machine will automatically complete and produce recycled plastic granules.
Most recycled plastic granules are polymer molecules with high molecular weight and different regeneration properties. So, the plastic granulator is also named after the product properties such as pp, PVC, and pe plastic granulator.
How much does it cost to buy where?
To save production costs, all businesses are equipped with plastic granulators instead of hiring or outsourcing before manufacturing. Moreover, with increasing demand, the types of plastic granulators have also become more popular and famous. Customers are also easier to learn and choose.
- PET PLASTIC granulator
- PP, PE, nylon shredder machine
- Pet plastic shredder, plastic bottle shell
- HDPE plastic shredder
- ABS, PS plastic shredder
- PVC shredder.
Application of plastic granulator
+ Application: PVC granulator. Plastic granulators can use raw plastic products or scrap, recovered plastic, recycled plastic, PVC, PET, PP, PE, HDPE, PS, ABS, PA, PET bottle flakes, PP, PE film, etc.
Moreover, plastic granulators have many good points, such as beautiful shape, round and bright. It can add as many colors as possible, high quality, and high output. Tan Hung Plastic Granules Company specializes in supplying PVC, PP, PPR, PE, HDPE, PS, ABS plastic machines… as follows:
- Plastic injection machine
- Distribution line for PVC/HDPE/PPR pipes, aluminum-plastic composite pipes
- Production line for coiled pipes, chicken intestines, corrugated pipes, ribbed pipes, mesh pipes, electrical conduit
Moreover, the plastic granulator is a kind of plastic extrusion equipment. It heats the plastic raw material back to liquid under the device’s pressure. It continuously extrudes through the extrusion die and then cools down to a state. In addition, thick filament glass, passing through a bead cutter, is cut into cylindrical or elliptical plastic beads.
Construction of plastic granulator
The main motor of plastic granulators (Server)
The main engine of the plastic granulator is the extruder, which is composed of an extrusion system. Moreover, there is a transmission system, a heating and cooling system, and a feeding system. Strong development of resources recycles and turns waste into treasure.
Extrusion system: consists of barrel, screw, mold, and filter. It melts plastic materials into pieces, granules, powders, blocks, or other shapes. And then stabilized at temperature and pressure, measured by the screw, and extruded from the mold.
Drive system. It is mainly composed of a motor, reducer, and belt. Its function is to drive the screw and make the screw achieve the parameter uniform torque and rotation speed of granulators. Given numbers (such as temperature, pressure, rate, etc.). Thereby extruding the product we want.
Heating and cooling system. It is mainly composed of a heater outside the barrel. A cooling element is installed inside the screw. In addition, the function of this system is to heat or cool the screw barrel. Moreover, it ensures the extrusion temperature of the product as required by the specification.
Feeding system. It is mainly composed of a hopper and an automatic feeding device. It has the function of supplying the necessary materials for the extrusion system stably and continuously.
Auxiliary granulating machine (sub-granulator)
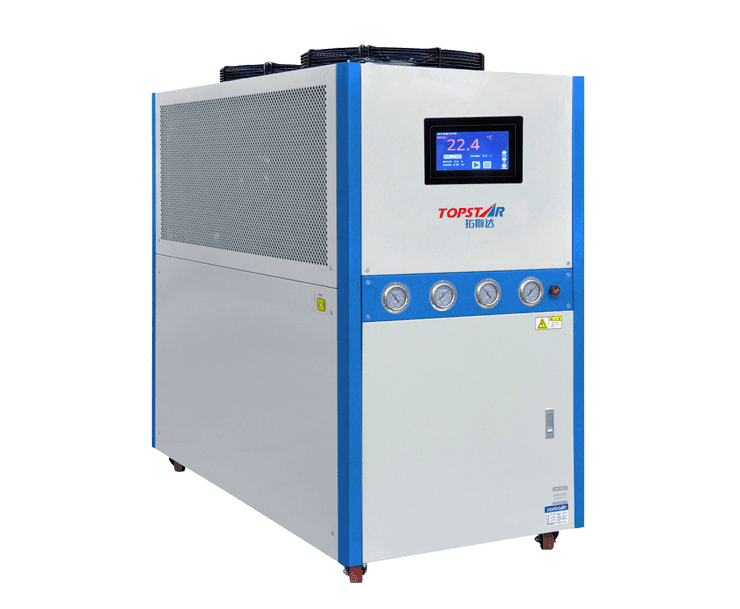
The main structure of the plastic granulator auxiliary machine is similar to the main engine. Its function is to continue the extrusion step and extrude the homogenous material.
Moreover, the difference lies in the plastic granulating mold, divided into two types: manual and automatic. The granulator needs to change the filter regularly to remove impurities. The extrusion mold usually has 18 holes. After the filter is blocked, the pressure of the extruder will be very high.
In addition, manually replacing the filter mesh will be more complex than automatic. Using an electric mold instead of a manual mold will save us more time and effort. The mold construction of Auxiliary machines with diverse and rich models.
Uses of the granulators
With unique screw designs and different configurations, it is possible to produce plastic types: PP, PE, PS, ABS, PA, PVC, PC, POM, EVA, LCP, PET, PMMA, and other plastic for recycling and color mixing granulation. In addition, the reduction gearbox adopts a high torque design, making the machine work stably and without noise.
Moreover, the screw barrel specially hardens, is wear-resistant, has good mixing efficiency and high output. The vacuum exhaust pipe design, or the design of the standard pipe mouth, can release moisture and exhaust gas during the process. The production process makes the discharge material more stable. The plastic particles are more durable and ensure the excellent quality of the product.
Plastic granulators are mainly used to process waste plastic film (industrial packaging film, agricultural film, greenhouse film, beer bags, bags, etc.). Moreover, this is the most widely used and popular plastic recycling processing machine type in the waste plastic recycling industry.
There are two ways to save energy. One is to keep the power part, and the other is to hold in the heating part.
Energy saving in power part: Mostly using an inverter, save energy through residual energy of the motor. For example, the real power of granulators is 50 Hz. In addition, you only need 30 Hz for production. The unspent energy will be wasted. So, the inverter will change the motor output power to achieve an energy-saving effect.
Energy saving in the heating section mainly uses an electromagnetic heating device. Moreover, the energy-saving rate is about 30%-70% compared with the old-fashioned resistor coil.
Features of plastic pelletizing machine
All recycled materials produced after sorting, crushing, and cleaning will not need to be shaken, dried, or sun-dried. And can be used directly for both dry and wet purposes;
- From raw material crushing, cleaning, feeding, and finally, granulating is automated.
- Make full use of a high-pressure frictionless heating system in granulators to automatically generate heat, avoid continuous heating, and save electricity and energy;
- Moreover, using an automatic power distribution system to different places to ensure the regular and safe operation of the engine;
- In addition, the screw barrel set is made of high quality and high strength carbon structural imported steel, with high strength;
TRENDING POSTS
- What factors can cause delays in the injection molding process of plastic molding machine? 2022/05/23
- Exhibition Review| Topstar participates in InterPlas Thailand 2024 2022/05/23
- Star Case | Topstar helps Santong upgrade its intelligent plant 2022/05/23
- Topstar Special | National Science and Technology Workers Day 2022/05/23
HOT TOPIC
- 3 in 1 Compact Dehumidifying Dryer
- 5-axis CNC machine
- accuracy
- Air Chillers
- all electric injection molding machine
- All-electric injection molding machines
- and overall production quality. Therefore
- AP-RubberPlas
- automated injection molding machine
- Automation changed engineering
- automation of injection molding robots
- auxiliary machine
- Bench Injection Molding Machine
- Cabinet dryer manufacturers
- Cabinet dryers
- chiller
- CNC Drilling Machine
- CNC Drilling Machines
- cnc engraving machine manufacturer
- cnc laser cutting machine manufacturer
- CNC machine
- CNC Machine Center
- CNC Machine for Sale
- CNC Machine Manufacturing
- CNC Machine Tool
- CNC machine tool product
- CNC Machining Center
- CNC wood carving machine
- Cooling system
- Cross-Walking Single Axis Servo Cylinder Robot
- Cross-Walking Single-Axis Servo Cylinder Robot
- Cross-Walking Three-Axis/Five-Axis Servo Driven Robot
- cross-walking three-axis/five-axis servo-driven robot
- Dehumidifier Dryer
- Dehumidifying Dryer
- delta parallel robot
- Desktop Injection Molding Machine
- Desktop injection molding machines
- Desktop Molding Machine
- desktop plastic injection machine
- Desktop Plastic Injection Molding Machine
- direct clamp injection molding machine
- Direct clamp injection molding machines
- Dosing & mixing system
- Drilling Centers
- Drying and dehumidification system
- drying and dehumidifying equipment
- Drying and Dehumidifying System
- drying system
- effective and efficient. Cabinet dryers are also used in other industries where large quantities of material need to be dried
- efficient injection molding machine
- elbow hydraulic injection molding machines
- electric injection molding machine
- electric injection molding machines
- etc. Among injection molding robots
- exhibition
- features of CNC machine
- Feeding And Conveying System
- Five Axis Machine Center
- Fully automatic injection molding machine
- Gathering Topstar
- giant injection molding machine
- GMU-600 5-Axis Machining Center
- Granulating & Recycling System
- Heavy duty injection molding machine
- Honeycomb rotor dehumidifier
- horizontal injection molding machine
- Horizontal Injection Molding Machines
- Horizontal Injection Moulding Machine
- Horizontal Mixer manufacturer
- How The CNC Machine Works
- hybrid injection molding machine
- hydraulic injection molding machine
- Hydraulic Injection Molding Machines
- in this article
- Industrial robot
- Industrial Robot Chinese brand
- industrial robot parts
- industrial robot supplier
- Industrial robots
- Industry Chain
- Injection Manipulator
- injection mold machines
- Injection molding
- Injection molding automation
- Injection Molding Automation Solution
- injection molding dryer
- Injection molding equipment
- injection molding hopper dryer
- Injection molding machine
- injection molding machine brand
- Injection Molding Machine Factory
- Injection Molding Machine Manufacture
- Injection molding machine manufacturer
- injection molding machine manufacturers
- Injection molding machine procurement
- injection molding machine robotic arm
- injection molding machine with a robot
- Injection molding machines
- injection molding material dehumidifying
- injection molding plant
- Injection Molding Robot
- injection molding robot arm
- Injection molding robot automation
- Injection molding robotic arm
- injection molding robots
- Injection Moulding Robots
- Injection Robot
- Injection robot arm
- Injection robot manufacturer
- Injection robot wholesale
- injection robots
- intelligent injection molding machines
- Introducing Injection Robot
- It is the best choice for drying large quantities of material at once. Cabinetmakers use these machines because they are fast
- large injection molding machine
- Learn what industrial automation and robotics is
- low speed sound-proof granulator
- machine plastic molding
- make sure to add some! Improvements (2) Keyphrase in introduction: Your keyphrase or its synonyms appear in the first paragraph of the copy
- manipulator machine
- manufacturing
- micro injection molding machine
- middle speed granulator
- Mini CNC machine manufacturers.
- Mold Temperature Control System
- mold temperature controller
- molding material Dehumidifying System
- mould temperature controller
- mould temperature controllers
- New electric injection molding machine
- nitrogen dryer manufacturer
- nitrogen dryer system manufacturer
- Oil type mold temperature controller
- open day
- Outbound links: No outbound links appear in this page. Add some! Images: No images appear on this page. Add some! Internal links: No internal links appear in this page
- PET Preform injection molding
- phone case maker machine
- phone case making machine
- plastic bottle making machine
- plastic bottle manufacturing
- plastic bucket making machine
- plastic bucket manufacturing
- Plastic chair making machine
- plastic forming equipment
- plastic hopper dryer
- plastic injection machine
- plastic injection machines
- plastic injection molding
- Plastic injection molding equipment
- Plastic injection molding machine
- Plastic Injection Molding Machines
- plastic injection robot
- Plastic Molding machine
- Plastic Molding Machines
- plastic molding press
- plastic phone case making machine
- plastic-molding machine
- powerful granulator
- Powerful Type Sound-Proof Granulator
- production of plastic seats
- Robot injection molding
- robot injection molding machine
- robot manufacturing companies
- Robotic arm for injection molding machine
- robotic injection molding machines
- robotics in injection molding
- SCARA robot
- SCARA robots
- Service-oriented manufacturing
- Servo Cylinder Robot
- servo driven robot
- Servo Driven Robots
- servo injection robots
- Servo-Driven Robot
- Setup of injection machine
- Silicone Injection Molding Machine
- six-axis industrial robot
- Stainless Hopper Dryer
- Stainless Hopper Dryers
- star club
- swing arm robot
- the choice between servo-driven robots and hydraulic robots will have a certain impact on efficiency
- the most popular injection molding machine
- the type of injection molding robot
- toggle clamp injection molding machine
- Toggle Hydraulic Injection Molding Machines
- toggle injection molding machine
- Top 10 brands of injection robots
- Topstar
- Topstar Engineering
- Topstar Industrial Robots
- Topstar injection molding intelligent
- Topstar Scara Robots
- Useful Injection molding machine
- Vertical machining centers
- volumetric type blender
- water chiller
- water chillers
- water distributor
- Water Type MoldTemperature Controller
- We often face choices when performing injection molding. We will choose the type of injection molding machine
- wholesale of injection molding machines
- x carve CNC