Electric injection molding machines that save energy and reduce costs for medical companies
2025/01/10 By Topstar
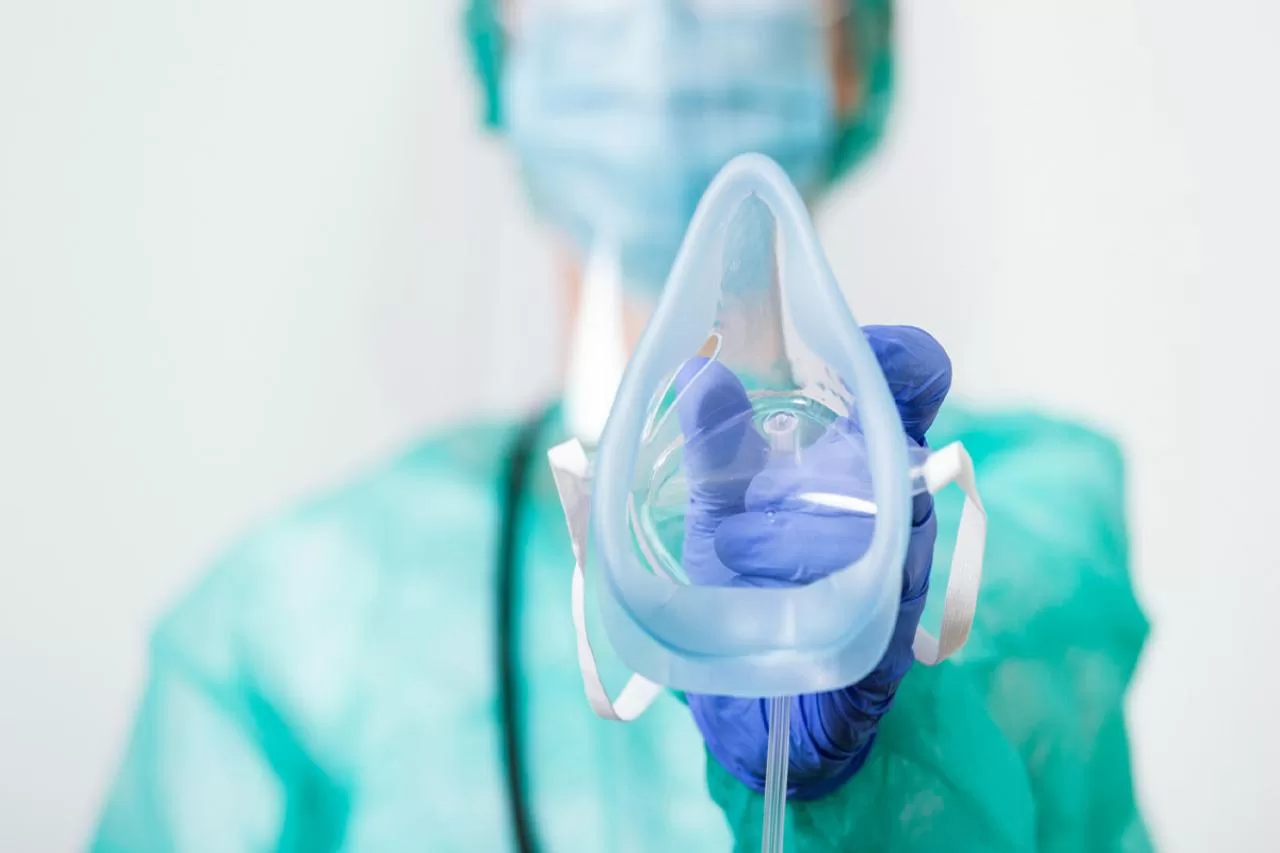
Medical products are sterile and clean, so their production environment must be a dust-free workshop. At the same time, in the current economic environment, medical companies are looking for a “cost-reducing and efficiency-increasing” production method. For manufacturing companies, reasonable energy layouts and effective management of production processes are essential to reduce operating costs, and low-energy production equipment is the tool to implement this method. After fully understanding the precision injection molding needs and dust-free workshop standards of medical products, Topstar launched an electric injection molding solution with TEⅡ electric injection molding machine as the core, which can take into account the complex indicators of dust-free workshops and the needs of product precision injection molding, and electric injection molding machines also have significant effects in energy saving and cost reduction.
Energy saving: the core advantage of electric injection molding machines
As the core of the entire electric injection molding solution, electric injection molding machines can bring excellent energy efficiency. Unlike traditional hydraulic molding machines, electric injection molding machines are operated by electric motors that use energy only when needed. It can save at least 50% of electricity compared to hydraulic presses and up to 60%. Equipment power-saving data is of great significance to the energy control of the production process of medical product companies. In addition, in terms of improving efficiency, the TEⅡ electric injection molding machine has high precision and stable equipment under the core control of an intelligent electric drive, and the production efficiency has increased by about 10% compared with the past. The high degree of intelligence of the whole machine also makes it easy for technicians to operate.
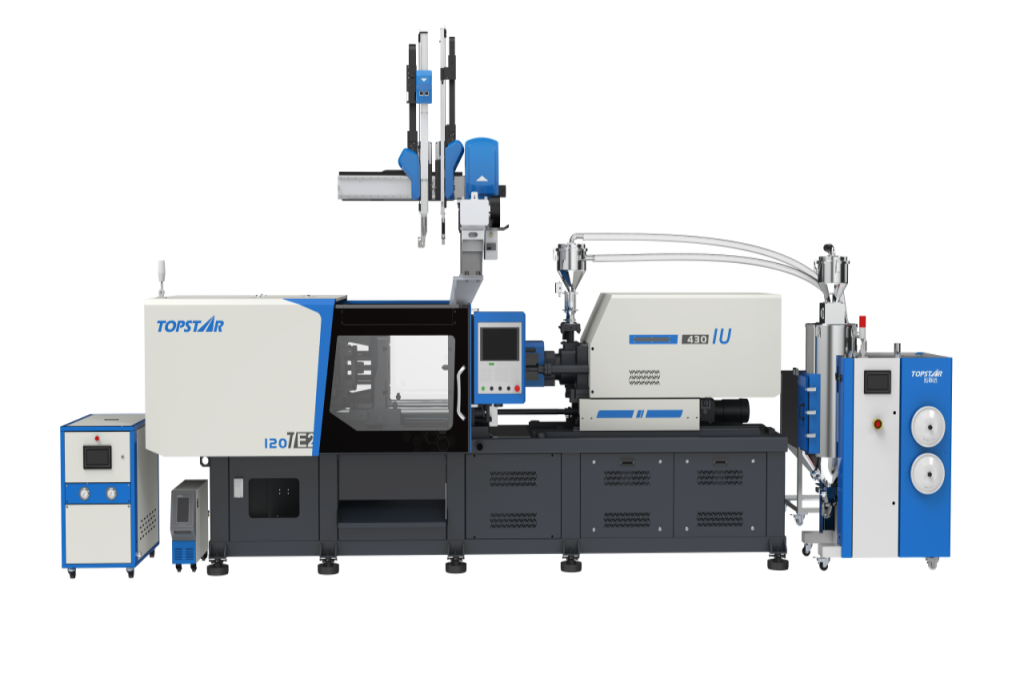
Pollution-free environment brought by electric injection molding machines
A clean and safe production environment is the most basic standard in the medical industry. Pollutants such as oil leakage or smoke emissions can seriously affect the quality of the product. Topstar’s electric injection molding machine adopts a simplified hydraulic configuration design, eliminating the risk of oil leakage and not polluting the environment. The extraordinary grease lubrication ensures smooth operation while keeping the mold area clean. Since there is no oil or hydraulic oil overflow, the risk of contamination is significantly reduced, which helps to create a cleaner production environment. The pollution-free characteristics of electric injection molding machines are also an ideal injection molding solution for medical companies seeking to meet high environmental standards while ensuring a cleaner and safer production area.
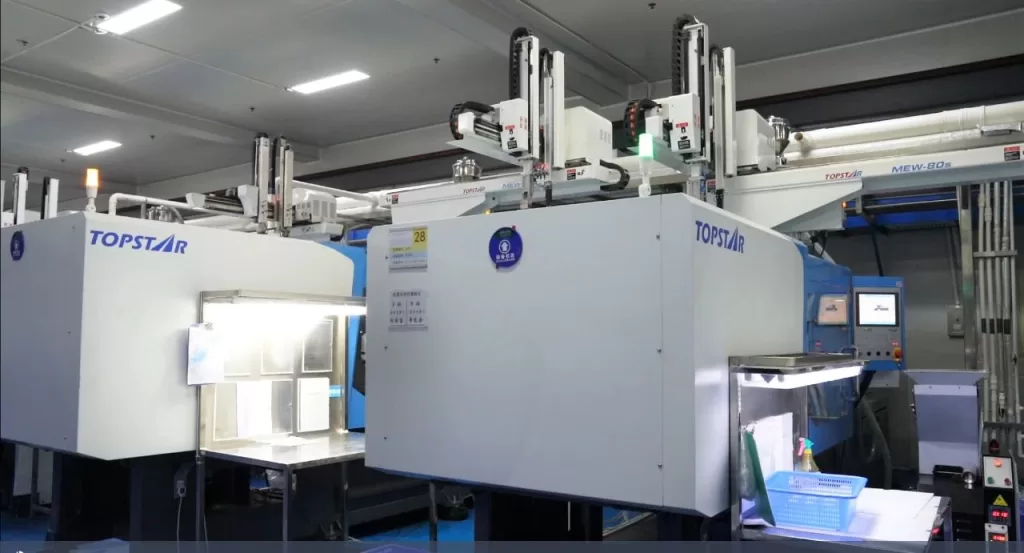
Compact size design
The clean room environment is an integral part of medical device manufacturing. In addition to the highly controlled environment, the height and width of the clean workshop are also strictly required. Generally, hydraulic injection molding machines are more significant than electric injection molding machines. This compact size design is more straightforward to integrate into the limited space of clean rooms. When designing electric injection molding machines, Topstar engineers took into account the strict height and width restrictions on the size of equipment in these fields. In addition, by adding wide support feet without sacrificing size, even compact size can provide stable dynamic support, making mold opening and closing smooth and better protecting the mold.
There is no need for separate lubrication to improve cleanliness and safety
Another significant advantage of electric injection molding machines is that they do not require separate lubrication, which is essential to keep the mold area clean. The second plate and guide pillar of Topstar’s TEⅡ electric injection molding machine are designed without contact, and no separate lubrication is required. This feature ensures that the mold area remains clean and free of oil or other contaminants. By eliminating the need for separate lubrication, medical companies can reduce the complexity of maintenance procedures while minimizing the risk of contamination. This also reduces the need for frequent inspections and maintenance of lubrication systems, which are time-consuming and expensive.
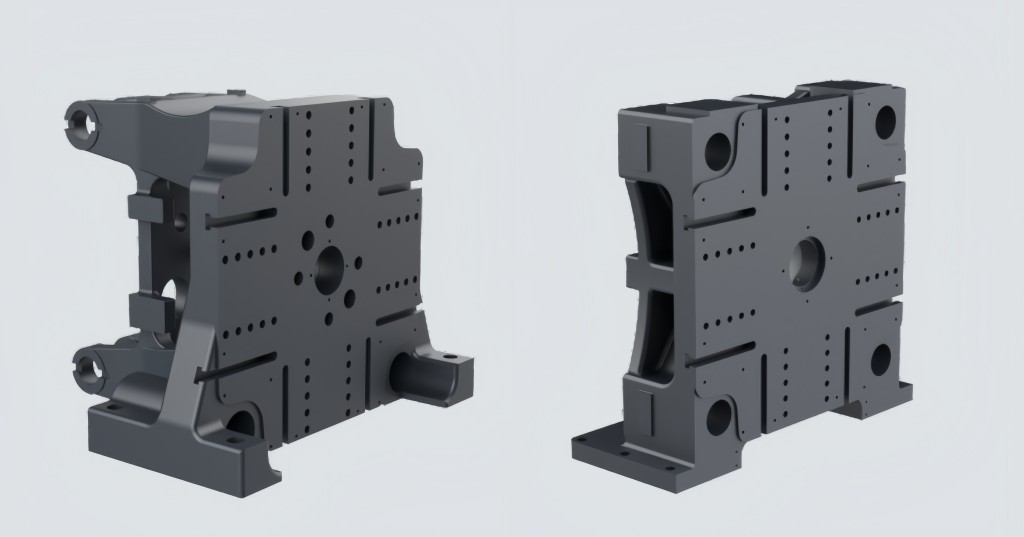
Bring more precise and accurate production
In the medical industry, precision is a necessity. The electric injection molding machines provided by Topstar use an integrated injection seat, which has high rigidity, stable structure, and more precise control. At the same time, they also use linear guides, which make low damping, more sensitive pressure detection, and more accurate pressure control. They are outstanding in providing high precision and accuracy, making them ideal for producing medical parts that require strict tolerances and precise specifications. They can enhance the control of the injection molding process, allowing manufacturers to produce parts with minimal defects, high dimensional accuracy, and stable quality. Whether you create complex surgical instruments or respiratory medical supplies, the precision of these machines ensures that each part meets the required specifications.
Electric injection molding machine is the best choice for medical companies
The energy-saving, pollution-free, compact design, and high precision of the electric injection molding machine make the injection molding process of medical devices more precise and accurate. These advantages make electric injection molding machines a wise choice for medical companies that want to reduce costs, improve product quality, and maintain a cleaner and safer production environment.
TRENDING POSTS
- What factors can cause delays in the injection molding process of plastic molding machine? 2025/01/10
- Exhibition Review| Topstar participates in InterPlas Thailand 2024 2025/01/10
- Star Case | Topstar helps Santong upgrade its intelligent plant 2025/01/10
- Topstar Special | National Science and Technology Workers Day 2025/01/10
HOT TOPIC
- .ervo motor-driven linear robots
- 1.0 guangdong topstar technology co. ltd
- 1.0 topstar china
- 1.0 topstar robot
- 11
- 2
- 21
- 23
- 3 axis robot
- 3 axis robots
- 3 in 1 Compact Dehumidifying Dryer
- 3-axis robot
- 3-axis robots
- 39
- 41
- 5-axis CNC machine
- 62
- accuracy
- Air Chillers
- all electric injection molding machine
- all electric injection molding machines
- All-electric injection molding machines
- and overall production quality. Therefore
- AP-RubberPlas
- automated injection molding machine
- Automation changed engineering
- automation of injection molding robots
- auxiliary machine
- Bench Injection Molding Machine
- Cabinet dryer manufacturers
- Cabinet dryers
- chiller
- CNC Drilling Machine
- CNC Drilling Machines
- cnc engraving machine manufacturer
- cnc laser cutting machine manufacturer
- CNC machine
- CNC Machine Center
- CNC Machine for Sale
- CNC Machine Manufacturing
- CNC Machine Tool
- CNC machine tool product
- CNC Machining Center
- CNC wood carving machine
- Cooling system
- Cross-Walking Single Axis Servo Cylinder Robot
- Cross-Walking Single-Axis Servo Cylinder Robot
- Cross-Walking Three-Axis/Five-Axis Servo Driven Robot
- cross-walking three-axis/five-axis servo-driven robot
- Dehumidifier Dryer
- Dehumidifying Dryer
- delta parallel robot
- Desktop Injection Molding Machine
- Desktop injection molding machines
- Desktop Molding Machine
- desktop plastic injection machine
- Desktop Plastic Injection Molding Machine
- direct clamp injection molding machine
- Direct clamp injection molding machines
- Dosing & mixing system
- Drilling Centers
- Drying and dehumidification system
- drying and dehumidifying equipment
- Drying and Dehumidifying System
- drying system
- effective and efficient. Cabinet dryers are also used in other industries where large quantities of material need to be dried
- efficient injection molding machine
- elbow hydraulic injection molding machines
- electric injection molding machine
- electric injection molding machines
- energy-efficient injection molding robot
- energy-saving injection molding machine
- etc. Among injection molding robots
- exhibition
- features of CNC machine
- Feeding And Conveying System
- Five Axis Machine Center
- Fully automatic injection molding machine
- Gathering Topstar
- giant injection molding machine
- GMU-600 5-Axis Machining Center
- Granulating & Recycling System
- Heavy duty injection molding machine
- High-precision electric molding machines
- high-precision plastic molding machines
- high-speed all electric injection molding machine
- Honeycomb rotor dehumidifier
- horizontal injection molding machine
- Horizontal Injection Molding Machines
- Horizontal Injection Moulding Machine
- Horizontal Mixer manufacturer
- How The CNC Machine Works
- hybrid injection molding machine
- hydraulic injection molding machine
- Hydraulic Injection Molding Machines
- in this article
- Industrial robot
- Industrial Robot Chinese brand
- industrial robot parts
- industrial robot supplier
- Industrial robots
- Industry Chain
- Injection Manipulator
- injection manipulator robot
- injection mold machines
- Injection molding
- Injection molding automation
- Injection Molding Automation Solution
- injection molding dryer
- Injection molding equipment
- injection molding hopper dryer
- Injection molding machine
- injection molding machine brand
- Injection Molding Machine Factory
- Injection Molding Machine Manufacture
- Injection molding machine manufacturer
- injection molding machine manufacturers
- Injection molding machine procurement
- injection molding machine robotic arm
- injection molding machine with a robot
- Injection molding machines
- injection molding material dehumidifying
- injection molding plant
- Injection Molding Robot
- injection molding robot arm
- Injection molding robot automation
- Injection molding robotic arm
- injection molding robots
- Injection moulding machine
- Injection Moulding Robots
- Injection Robot
- Injection robot arm
- Injection robot manufacturer
- Injection robot wholesale
- injection robots
- intelligent injection molding machines
- Introducing Injection Robot
- It is the best choice for drying large quantities of material at once. Cabinetmakers use these machines because they are fast
- large injection molding machine
- large injection molding machines
- Learn what industrial automation and robotics is
- linear robot
- linear robots
- low speed sound-proof granulator
- machine plastic molding
- make sure to add some! Improvements (2) Keyphrase in introduction: Your keyphrase or its synonyms appear in the first paragraph of the copy
- manipulator machine
- manufacturing
- medical grade injection molding machines
- medical injection molding machine
- medical injection molding machines
- micro injection molding machine
- middle speed granulator
- Mini CNC machine manufacturers.
- Mold Temperature Control System
- mold temperature controller
- mold temperature controllers
- molding material Dehumidifying System
- mould temperature control system
- mould temperature controller
- mould temperature controllers
- New electric injection molding machine
- nitrogen dryer manufacturer
- nitrogen dryer system manufacturer
- Oil type mold temperature controller
- Oil type mold temperature controllers
- open day
- Outbound links: No outbound links appear in this page. Add some! Images: No images appear on this page. Add some! Internal links: No internal links appear in this page
- PET Preform injection molding
- phone case maker machine
- phone case making machine
- plastic bottle making machine
- plastic bottle manufacturing
- plastic bucket making machine
- plastic bucket manufacturing
- Plastic chair making machine
- plastic forming equipment
- plastic hopper dryer
- plastic injection machine
- plastic injection machines
- plastic injection molding
- Plastic injection molding equipment
- Plastic injection molding machine
- Plastic Injection Molding Machines
- plastic injection moulding machine
- plastic injection robot
- Plastic Molding machine
- Plastic Molding Machines
- plastic molding press
- plastic moulding machine
- plastic phone case making machine
- plastic-molding machine
- powerful granulator
- Powerful Type Sound-Proof Granulator
- precision injection molding
- precision injection molding machines
- production of plastic seats
- pure water mould temperature controller
- Robot injection molding
- robot injection molding machine
- robot manufacturing companies
- Robotic arm for injection molding machine
- robotic injection molding machines
- robotics in injection molding
- SCARA robot
- SCARA robots
- Service-oriented manufacturing
- Servo Cylinder Robot
- servo driven robot
- Servo Driven Robots
- servo injection robots
- servo motor-driven linear robots
- servo-driven 3-axis robot
- Servo-Driven Robot
- Setup of injection machine
- Silicone Injection Molding Machine
- six-axis industrial robot
- Stainless Hopper Dryer
- Stainless Hopper Dryers
- star club
- swing arm robot
- take-out robots
- the choice between servo-driven robots and hydraulic robots will have a certain impact on efficiency
- the most popular injection molding machine
- the type of injection molding robot
- toggle clamp injection molding machine
- Toggle Hydraulic Injection Molding Machines
- toggle injection molding machine
- Top 10 brands of injection robots
- Topstar
- Topstar Engineering
- Topstar Industrial Robots
- Topstar injection molding intelligent
- Topstar Scara Robots
- Useful Injection molding machine
- Vertical machining centers
- volumetric type blender
- water chiller
- water chillers
- water distributor
- water type mold temperature controller
- Water Type MoldTemperature Controller
- Water-Type Mould Temperature Controllers
- We often face choices when performing injection molding. We will choose the type of injection molding machine
- wholesale of injection molding machines
- x carve CNC
- 热门查询 点击次数 展示 排名 topstar