Direct Clamp Injection Molding Machine technical capabilities
2023/12/13 By Topstar
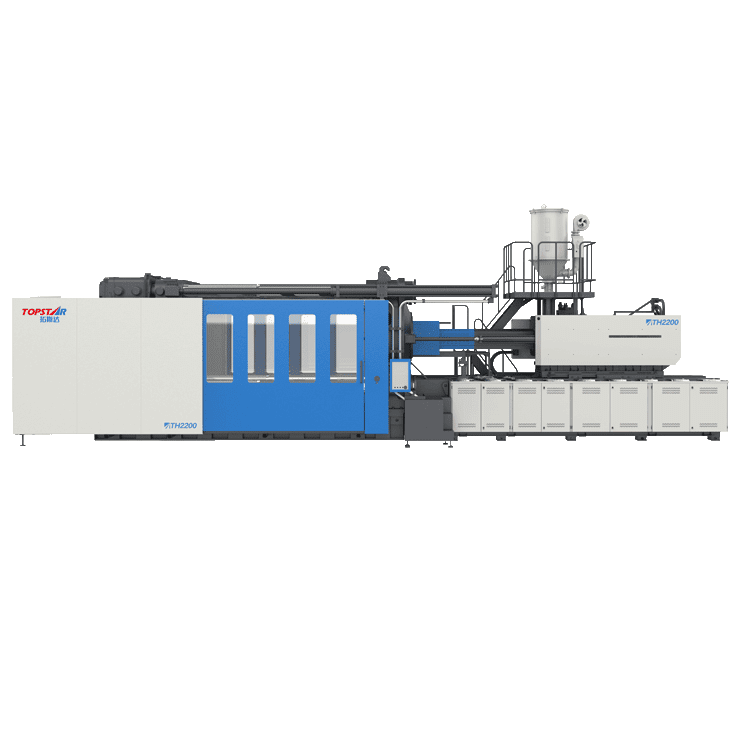
In this article, we will introduce you to the functions of the direct Clamp Injection Molding Machine and analyze its functions and advantages from multiple aspects. From basic operations to advanced functions, we will introduce them individually in this article. You can gain something if you are a professional injection molding machine operator or a production line worker.
Technical structure of direct clamping mold injection molding machine
First, let everyone know the technical design of the direct clamping injection molding machine from three aspects.
Mold accuracy:
The mold accuracy of a direct clamp injection molding machine is a crucial factor affecting the quality and consistency of molded products. Provides superior mold accuracy through advanced design and manufacturing technology. Our molds are designed using state-of-the-art CAD/CAM technology to ensure tight tolerances and dimensional accuracy. This allows the mold to produce high-quality, defect-free plastic parts consistently. Our machines prioritize mold stability during mold closing, minimizing mold wear and ensuring reliable, repeatable production runs.
Clamping mechanism:
In direct clamp injection molding machines, the accuracy of the clamping mechanism is essential for mold alignment, reducing wear on mold components, and ensuring long-term durability. They close the mold quickly and forcefully, enhancing stability during the injection phase. The system maintains precise mold alignment, producing defect-free parts during long production runs. This is, therefore, particularly important for industries such as automotive and electronics that require high-quality plastic products.
Mold cooling technology:
Mold cooling technology in direct clamp Injection Molding Machines includes conformal cooling and cooling channels strategically embedded within the mold to follow the part’s contours precisely. It can ensure uniform temperature distribution throughout the mold, reducing thermal changes and warpage of the final product. This can significantly improve production efficiency.
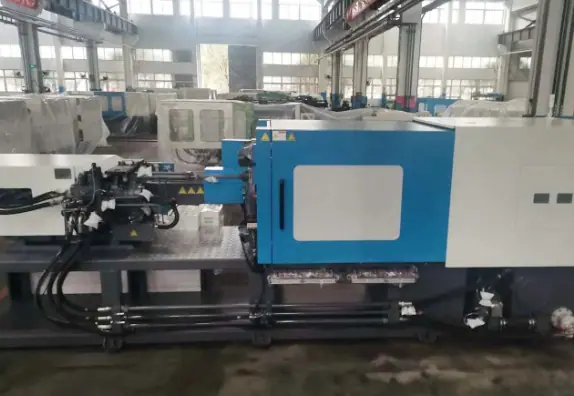
Advantages of direct clamping injection molding
At the same time, their material compatibility demonstrates versatility and adaptability in thermoplastics and engineering resins. Direct clamp injection molding is designed to seamlessly process a wide range of thermoplastic materials, from common polymers like polyethylene and polypropylene to high-performance resins like polycarbonate. In nanoscale molding, direct clamp injection molding machines can create components with dimensions in the nanometer range. Advanced control systems in the device provide nanometer resolution capabilities, allowing operators to finely control injection parameters at the nanometer level, creating micro- and nanoscale parts with exceptional repeatability. This capability is critical for developing advanced materials, nanoelectronics, and biomedical devices, all requiring extremely high precision.
Advanced process monitoring
Our direct clamp injection molding machine uses state-of-the-art sensors and control mechanisms to continuously monitor critical parameters such as temperature, pressure, and cycle time. This feature enables the detection and prevention of potential defects. Through the continuous analysis of process variables, deviations from the required parameters can be quickly identified, allowing immediate corrective measures to be taken. This proactive defect prevention increases overall production efficiency and minimizes waste.
Vision system for defect detection
The direct clamp injection molding machine’s vision system is equipped with high-resolution cameras and intelligent lighting to capture detailed images of each molded product. The system’s algorithms analyze these images in real-time, detecting defects such as surface imperfections, color changes, and dimensional irregularities. Defect inspection systems can address a range of potential defects, from common surface blemishes to more complex flaws. Its sensitivity to minute details prompts the identification of even minor deviations from the required specifications.
Integration with injection robots
Direct clamp injection molding machines and robots increase production efficiency by automating material handling, part extraction, and packaging tasks. The robot’s speed and precision help reduce cycle times and increase throughput. They can also handle various functions during the injection molding, from inserting inserts and removing finished parts to performing quality checks and sorting. It also simplifies the entire production cycle, a flexibility particularly beneficial in industries with diverse product lines and changing manufacturing requirements. As shown below:
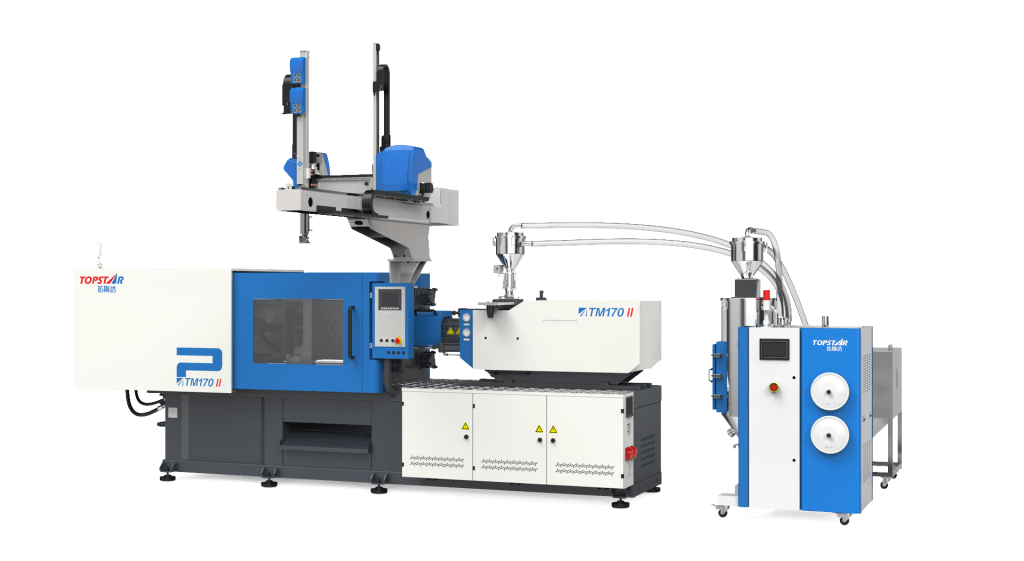
We have previously introduced you to the comprehensive capabilities of direct clamping injection molding machines. From their structure, monitoring system, and combination with injection robots, you know this injection molding machine is very worthy of your choice. No matter what industry you are in, it can help you. As a professional injection molding machine manufacturer, we provide high-quality and reliable machines.
TRENDING POSTS
- What factors can cause delays in the injection molding process of plastic molding machine? 2023/12/13
- Exhibition Review| Topstar participates in InterPlas Thailand 2024 2023/12/13
- Star Case | Topstar helps Santong upgrade its intelligent plant 2023/12/13
- Topstar Special | National Science and Technology Workers Day 2023/12/13
HOT TOPIC
- 3 in 1 Compact Dehumidifying Dryer
- 5-axis CNC machine
- accuracy
- Air Chillers
- all electric injection molding machine
- All-electric injection molding machines
- and overall production quality. Therefore
- AP-RubberPlas
- automated injection molding machine
- Automation changed engineering
- automation of injection molding robots
- auxiliary machine
- Bench Injection Molding Machine
- Cabinet dryer manufacturers
- Cabinet dryers
- chiller
- CNC Drilling Machine
- CNC Drilling Machines
- cnc engraving machine manufacturer
- cnc laser cutting machine manufacturer
- CNC machine
- CNC Machine Center
- CNC Machine for Sale
- CNC Machine Manufacturing
- CNC Machine Tool
- CNC machine tool product
- CNC Machining Center
- CNC wood carving machine
- Cooling system
- Cross-Walking Single Axis Servo Cylinder Robot
- Cross-Walking Single-Axis Servo Cylinder Robot
- Cross-Walking Three-Axis/Five-Axis Servo Driven Robot
- cross-walking three-axis/five-axis servo-driven robot
- Dehumidifier Dryer
- Dehumidifying Dryer
- delta parallel robot
- Desktop Injection Molding Machine
- Desktop injection molding machines
- Desktop Molding Machine
- desktop plastic injection machine
- Desktop Plastic Injection Molding Machine
- direct clamp injection molding machine
- Direct clamp injection molding machines
- Dosing & mixing system
- Drilling Centers
- Drying and dehumidification system
- drying and dehumidifying equipment
- Drying and Dehumidifying System
- drying system
- effective and efficient. Cabinet dryers are also used in other industries where large quantities of material need to be dried
- efficient injection molding machine
- elbow hydraulic injection molding machines
- electric injection molding machine
- electric injection molding machines
- etc. Among injection molding robots
- exhibition
- features of CNC machine
- Feeding And Conveying System
- Five Axis Machine Center
- Fully automatic injection molding machine
- Gathering Topstar
- giant injection molding machine
- GMU-600 5-Axis Machining Center
- Granulating & Recycling System
- Heavy duty injection molding machine
- Honeycomb rotor dehumidifier
- horizontal injection molding machine
- Horizontal Injection Molding Machines
- Horizontal Injection Moulding Machine
- Horizontal Mixer manufacturer
- How The CNC Machine Works
- hybrid injection molding machine
- hydraulic injection molding machine
- Hydraulic Injection Molding Machines
- in this article
- Industrial robot
- Industrial Robot Chinese brand
- industrial robot parts
- industrial robot supplier
- Industrial robots
- Industry Chain
- Injection Manipulator
- injection mold machines
- Injection molding
- Injection molding automation
- Injection Molding Automation Solution
- injection molding dryer
- Injection molding equipment
- injection molding hopper dryer
- Injection molding machine
- injection molding machine brand
- Injection Molding Machine Factory
- Injection Molding Machine Manufacture
- Injection molding machine manufacturer
- injection molding machine manufacturers
- Injection molding machine procurement
- injection molding machine robotic arm
- injection molding machine with a robot
- Injection molding machines
- injection molding material dehumidifying
- injection molding plant
- Injection Molding Robot
- injection molding robot arm
- Injection molding robot automation
- Injection molding robotic arm
- injection molding robots
- Injection Moulding Robots
- Injection Robot
- Injection robot arm
- Injection robot manufacturer
- Injection robot wholesale
- injection robots
- intelligent injection molding machines
- Introducing Injection Robot
- It is the best choice for drying large quantities of material at once. Cabinetmakers use these machines because they are fast
- large injection molding machine
- Learn what industrial automation and robotics is
- low speed sound-proof granulator
- machine plastic molding
- make sure to add some! Improvements (2) Keyphrase in introduction: Your keyphrase or its synonyms appear in the first paragraph of the copy
- manipulator machine
- manufacturing
- micro injection molding machine
- middle speed granulator
- Mini CNC machine manufacturers.
- Mold Temperature Control System
- mold temperature controller
- molding material Dehumidifying System
- mould temperature controller
- mould temperature controllers
- New electric injection molding machine
- nitrogen dryer manufacturer
- nitrogen dryer system manufacturer
- Oil type mold temperature controller
- open day
- Outbound links: No outbound links appear in this page. Add some! Images: No images appear on this page. Add some! Internal links: No internal links appear in this page
- PET Preform injection molding
- phone case maker machine
- phone case making machine
- plastic bottle making machine
- plastic bottle manufacturing
- plastic bucket making machine
- plastic bucket manufacturing
- Plastic chair making machine
- plastic forming equipment
- plastic hopper dryer
- plastic injection machine
- plastic injection machines
- plastic injection molding
- Plastic injection molding equipment
- Plastic injection molding machine
- Plastic Injection Molding Machines
- plastic injection robot
- Plastic Molding machine
- Plastic Molding Machines
- plastic molding press
- plastic phone case making machine
- plastic-molding machine
- powerful granulator
- Powerful Type Sound-Proof Granulator
- production of plastic seats
- Robot injection molding
- robot injection molding machine
- robot manufacturing companies
- Robotic arm for injection molding machine
- robotic injection molding machines
- robotics in injection molding
- SCARA robot
- SCARA robots
- Service-oriented manufacturing
- Servo Cylinder Robot
- servo driven robot
- Servo Driven Robots
- servo injection robots
- Servo-Driven Robot
- Setup of injection machine
- Silicone Injection Molding Machine
- six-axis industrial robot
- Stainless Hopper Dryer
- Stainless Hopper Dryers
- star club
- swing arm robot
- the choice between servo-driven robots and hydraulic robots will have a certain impact on efficiency
- the most popular injection molding machine
- the type of injection molding robot
- toggle clamp injection molding machine
- Toggle Hydraulic Injection Molding Machines
- toggle injection molding machine
- Top 10 brands of injection robots
- Topstar
- Topstar Engineering
- Topstar Industrial Robots
- Topstar injection molding intelligent
- Topstar Scara Robots
- Useful Injection molding machine
- Vertical machining centers
- volumetric type blender
- water chiller
- water chillers
- water distributor
- Water Type MoldTemperature Controller
- We often face choices when performing injection molding. We will choose the type of injection molding machine
- wholesale of injection molding machines
- x carve CNC