Common mold clamping device fault repair of plastic injection molding machine
2025/04/14 By Topstar
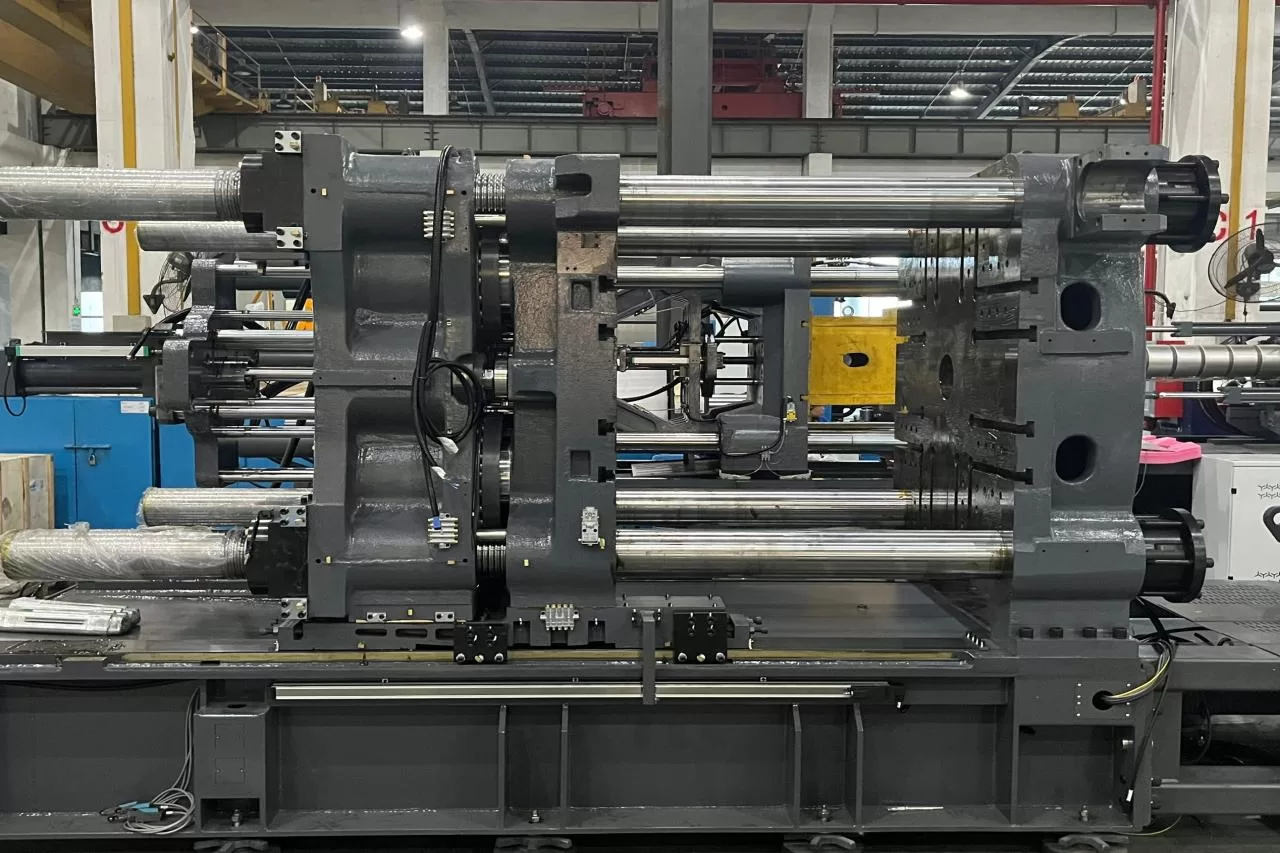
The clamping device is one of the most critical components of the plastic injection molding machine during the molding process. The clamping device is essential for maintaining precise alignment, constant clamping force, and synchronous operation of the two halves of the mold during the injection cycle. When this system fails, it may cause problems such as insufficient clamping force, stuck or damaged second mold, mechanical failure, or unlocked mold creep. These failures not only affect the quality of the final product but also lead to increased downtime and rising maintenance costs. This guide will detail practical repair methods to deal with these challenges based on Topstar engineers’ experience.
Solutions to the insufficient clamping force of plastic injection molding machine
Insufficient clamping force is one of the most common problems of plastic injection molding machines. This failure occurs when the clamping force provided by the mold clamping device during the injection process is insufficient to close the two halves of the mold firmly. This will cause flashing and excess material to seep between the two halves of the mold. In more serious cases, it will cause defects in the molded parts, ultimately increasing scrap and rework rates. Improper machine settings, worn hydraulic components, or loose connections within the clamping system typically cause this problem.
To solve the problem of insufficient clamping force, the hydraulic system and mechanical fasteners need to be thoroughly checked. Vibration and continuous operation can cause fasteners to loosen over time, gradually reducing clamping pressure. In addition, wear or leakage of components can significantly reduce clamping efficiency. It may be necessary to replace worn parts or recalibrate hydraulic pressure.
So first check:
- All screws, bolts, and fixtures are adequately tightened to ensure that the mold is firmly fixed to the clamping device.
- Hydraulic seals and cylinders are carefully inspected and replaced in time if they are worn.
The second mold is stuck, or the template is damaged
The second mold stuck, or template damage is also a common and troublesome failure in the clamping device. “Second mold” refers to the half mold that keeps moving during the molding cycle. When this portion of the clamping device gets stuck or releases improperly, it can cause mold parts to become misaligned or even physically damaged. Template damage usually manifests as bent or cracked edges caused by excessive force or uneven pressure distribution during clamping.
To solve these problems, the cause of mold sticking must first be diagnosed. These include:
- Misalignment of the moving mold halves;
- Obstruction of the clamping path;
- Failure of the hydraulic system causing unsmooth operation;
Then, the wear and alignment accuracy of the moving parts will be checked. Simple adjustments, cleaning and lubricating the sliding surfaces, or realigning the mold can solve the sticking problem. Special attention must be paid to the guide pins or rails that ensure the correct movement of the second mold.
Damage to the mold plate usually requires a more detailed assessment, checking for signs of excessive pressure in the damaged area and recalibrating the clamping device to ensure that the two mold halves are correctly synchronized. If necessary, the damaged mold plate should be repaired or replaced, primarily if the damage affects the dimensional accuracy of the molded part.
Resolving mechanical failures in the clamping device
Mechanical failures in the mold clamping device of a plastic injection molding machine can seriously affect production quality and machine life. These failures may include:
- Damage or wear of components such as hinges, locking mechanisms, or guide components;
- Occurring due to long-term use, insufficient maintenance, or improper operation;
Failure of mechanical components usually leads to reduced clamping pressure, misalignment between the two halves of the mold, or even complete system shutdown, resulting in production delays and increased scrap rates. To repair mechanical failures effectively, the entire clamping assembly must be carefully inspected.
- Check all moving parts for signs of wear, cracks, or deformation, and confirm that all connection points are firm and reliable;
- The overall design of the mechanical system identifies any design defects;
In many cases, worn parts must be replaced to restore full functionality. For example, suppose the locking mechanism cannot engage properly due to wear. In this case, new parts that meet the specifications should be replaced. If there are problems with the overall design, optimizing the component geometry and replacing it with a higher grade material is recommended.
Troubleshooting mold creep problems
Mold creep refers to the inability of the mold of the plastic injection molding machine to demold or accidentally slip during the mold opening and closing process, resulting in serious misalignment, resulting in part defects, increased wear of mold components, and other problems.
To solve the mold creep problem, first thoroughly evaluate the mechanical and automation components of the clamping system and carefully inspect the clamping components and guides. Generally speaking, loose mounting components or insufficient system tension will exacerbate such issues. In many cases, the creeping problem can be solved by simply tightening the screws and recalibrating the clamping device. In addition, the hydraulic system should be diagnostically tested to verify that it provides continuous and stable pressure. Inconsistent hydraulic pressure can also lead to incomplete unlocking or unexpected slipping during operation. Therefore, it is necessary to replace or repair defective hydraulic seals and ensure that the control valve is operating normally.
How to ensure the stability of the clamping device of the plastic injection molding machine?
Topstar’s plastic injection molding machines have highly wear-resistant copper sliding feet to ensure long-term operation even under high pressure. In addition, our machines are equipped with double sliding feet, which significantly facilitates the adjustment of the platen parallelism. This dual support maintains even clamping force across the entire mold, reducing uneven wear.
In addition, the full range of plastic injection molding machines is equipped with a one-touch mold adjustment system, which is standard. One-touch clamping significantly reduces mold adjustment time, allowing operators to quickly and easily readjust and calibrate the mold. One-touch mold adjustment improves production efficiency and consistency, ensuring more durability and reliability.
In summary
Common problems such as insufficient clamping force, second mold stuck or mold damage, mechanical failure, and mold opening creep can be solved by firmly installing, regularly tightening screws and hardware, and thoroughly checking hydraulic devices and mechanical systems. To avoid these failures, Topstar uses a copper slide, double slide, and one-button mold adjustment system to reduce common failure
TRENDING POSTS
- What factors can cause delays in the injection molding process of plastic molding machine? 2025/04/14
- Exhibition Review| Topstar participates in InterPlas Thailand 2024 2025/04/14
- Star Case | Topstar helps Santong upgrade its intelligent plant 2025/04/14
- Topstar Special | National Science and Technology Workers Day 2025/04/14
HOT TOPIC
- 3 in 1 Compact Dehumidifying Dryer
- 5-axis CNC machine
- accuracy
- Air Chillers
- all electric injection molding machine
- All-electric injection molding machines
- and overall production quality. Therefore
- AP-RubberPlas
- automated injection molding machine
- Automation changed engineering
- automation of injection molding robots
- auxiliary machine
- Bench Injection Molding Machine
- Cabinet dryer manufacturers
- Cabinet dryers
- chiller
- CNC Drilling Machine
- CNC Drilling Machines
- cnc engraving machine manufacturer
- cnc laser cutting machine manufacturer
- CNC machine
- CNC Machine Center
- CNC Machine for Sale
- CNC Machine Manufacturing
- CNC Machine Tool
- CNC machine tool product
- CNC Machining Center
- CNC wood carving machine
- Cooling system
- Cross-Walking Single Axis Servo Cylinder Robot
- Cross-Walking Single-Axis Servo Cylinder Robot
- Cross-Walking Three-Axis/Five-Axis Servo Driven Robot
- cross-walking three-axis/five-axis servo-driven robot
- Dehumidifier Dryer
- Dehumidifying Dryer
- delta parallel robot
- Desktop Injection Molding Machine
- Desktop injection molding machines
- Desktop Molding Machine
- desktop plastic injection machine
- Desktop Plastic Injection Molding Machine
- direct clamp injection molding machine
- Direct clamp injection molding machines
- Dosing & mixing system
- Drilling Centers
- Drying and dehumidification system
- drying and dehumidifying equipment
- Drying and Dehumidifying System
- drying system
- effective and efficient. Cabinet dryers are also used in other industries where large quantities of material need to be dried
- efficient injection molding machine
- elbow hydraulic injection molding machines
- electric injection molding machine
- electric injection molding machines
- etc. Among injection molding robots
- exhibition
- features of CNC machine
- Feeding And Conveying System
- Five Axis Machine Center
- Fully automatic injection molding machine
- Gathering Topstar
- giant injection molding machine
- GMU-600 5-Axis Machining Center
- Granulating & Recycling System
- Heavy duty injection molding machine
- Honeycomb rotor dehumidifier
- horizontal injection molding machine
- Horizontal Injection Molding Machines
- Horizontal Injection Moulding Machine
- Horizontal Mixer manufacturer
- How The CNC Machine Works
- hybrid injection molding machine
- hydraulic injection molding machine
- Hydraulic Injection Molding Machines
- in this article
- Industrial robot
- Industrial Robot Chinese brand
- industrial robot parts
- industrial robot supplier
- Industrial robots
- Industry Chain
- Injection Manipulator
- injection mold machines
- Injection molding
- Injection molding automation
- Injection Molding Automation Solution
- injection molding dryer
- Injection molding equipment
- injection molding hopper dryer
- Injection molding machine
- injection molding machine brand
- Injection Molding Machine Factory
- Injection Molding Machine Manufacture
- Injection molding machine manufacturer
- injection molding machine manufacturers
- Injection molding machine procurement
- injection molding machine robotic arm
- injection molding machine with a robot
- Injection molding machines
- injection molding material dehumidifying
- injection molding plant
- Injection Molding Robot
- injection molding robot arm
- Injection molding robot automation
- Injection molding robotic arm
- injection molding robots
- Injection Moulding Robots
- Injection Robot
- Injection robot arm
- Injection robot manufacturer
- Injection robot wholesale
- injection robots
- intelligent injection molding machines
- Introducing Injection Robot
- It is the best choice for drying large quantities of material at once. Cabinetmakers use these machines because they are fast
- large injection molding machine
- Learn what industrial automation and robotics is
- low speed sound-proof granulator
- machine plastic molding
- make sure to add some! Improvements (2) Keyphrase in introduction: Your keyphrase or its synonyms appear in the first paragraph of the copy
- manipulator machine
- manufacturing
- micro injection molding machine
- middle speed granulator
- Mini CNC machine manufacturers.
- Mold Temperature Control System
- mold temperature controller
- molding material Dehumidifying System
- mould temperature controller
- mould temperature controllers
- New electric injection molding machine
- nitrogen dryer manufacturer
- nitrogen dryer system manufacturer
- Oil type mold temperature controller
- open day
- Outbound links: No outbound links appear in this page. Add some! Images: No images appear on this page. Add some! Internal links: No internal links appear in this page
- PET Preform injection molding
- phone case maker machine
- phone case making machine
- plastic bottle making machine
- plastic bottle manufacturing
- plastic bucket making machine
- plastic bucket manufacturing
- Plastic chair making machine
- plastic forming equipment
- plastic hopper dryer
- plastic injection machine
- plastic injection machines
- plastic injection molding
- Plastic injection molding equipment
- Plastic injection molding machine
- Plastic Injection Molding Machines
- plastic injection robot
- Plastic Molding machine
- Plastic Molding Machines
- plastic molding press
- plastic phone case making machine
- plastic-molding machine
- powerful granulator
- Powerful Type Sound-Proof Granulator
- production of plastic seats
- Robot injection molding
- robot injection molding machine
- robot manufacturing companies
- Robotic arm for injection molding machine
- robotic injection molding machines
- robotics in injection molding
- SCARA robot
- SCARA robots
- Service-oriented manufacturing
- Servo Cylinder Robot
- servo driven robot
- Servo Driven Robots
- servo injection robots
- Servo-Driven Robot
- Setup of injection machine
- Silicone Injection Molding Machine
- six-axis industrial robot
- Stainless Hopper Dryer
- Stainless Hopper Dryers
- star club
- swing arm robot
- the choice between servo-driven robots and hydraulic robots will have a certain impact on efficiency
- the most popular injection molding machine
- the type of injection molding robot
- toggle clamp injection molding machine
- Toggle Hydraulic Injection Molding Machines
- toggle injection molding machine
- Top 10 brands of injection robots
- Topstar
- Topstar Engineering
- Topstar Industrial Robots
- Topstar injection molding intelligent
- Topstar Scara Robots
- Useful Injection molding machine
- Vertical machining centers
- volumetric type blender
- water chiller
- water chillers
- water distributor
- Water Type MoldTemperature Controller
- We often face choices when performing injection molding. We will choose the type of injection molding machine
- wholesale of injection molding machines
- x carve CNC