Choosing the right Dosing & Mixing System for thermoplastics
2023/11/17 By Topstar
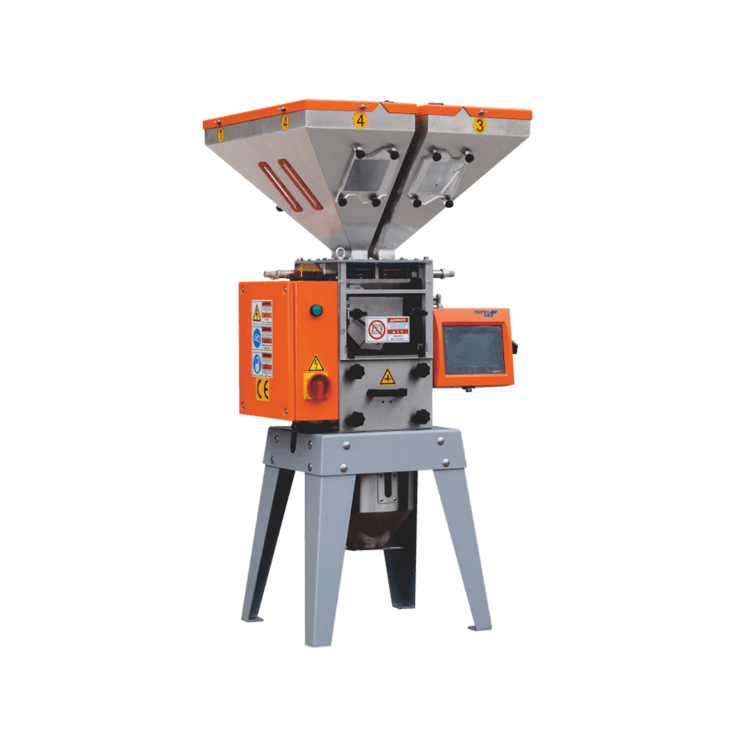
Choosing the right Dosing & Mixing System for thermoplastics is a critical decision that directly affects manufacturing efficiency and product quality. This guide looks in-depth at thermoplastic Dosing & Mixing Systems, exploring key considerations, advanced technologies, and the critical role these systems play in modern production processes. As industries increasingly embrace the versatility of thermoplastics, finding the proper dosing and mixing solutions becomes vital to achieving precision, consistency, and optimal performance.
Learn about thermoplastics
Before delving into the Dosing & Mixing Systems, it is critical to understand the properties of thermoplastics. The properties of thermoplastics enhance their ability to soften and deform when heated, making them ideal for various manufacturing applications. Thermoplastics are a class of polymers with unique properties that have gained prominence in various industries due to their exceptional versatility. The ability to undergo reversible melting and solidification processes makes it ideal for complex forming, extrusion, and reshaping applications. Examples of thermoplastics include polyethylene, polypropylene, and other high-performance polymers.
Manufacturers can optimize dosing & mixing parameters for precise control during processing. The key is understanding how different thermoplastics respond to changes in temperature. Melt flow rate, glass transition temperature, and viscosity changes are important factors that influence dosing and mixing strategies. For example, some high-performance thermoplastics may exhibit narrow processing windows that require precise control to achieve desired material properties.
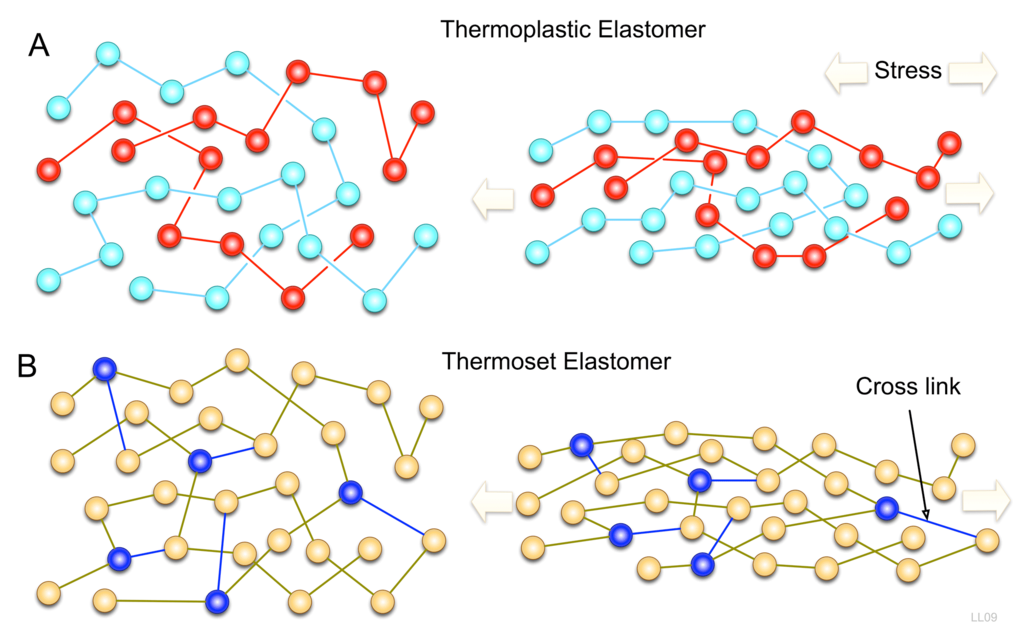
Thermoplastic Dosing & Mixing System selection factors
Material properties:
Thermoplastic Types: Different thermoplastics have different processing requirements. Consider the specific properties of the material you are working with, such as melt temperature, viscosity, and shear sensitivity.
Throughput requirements:
Throughput: Determines the throughput required for the production process. Dosing and mixing systems should be able to achieve the necessary productivity without compromising quality.
Accuracy and precision:
Batching accuracy: The system should provide accurate and precise batching to ensure consistent proportions of materials. Small changes in dosage can lead to product defects and quality issues.
Mixing efficiency:
Uniformity: Achieving a uniform mix is critical to the quality of the final product. Mixing systems should be designed to evenly distribute additives, colorants, or other materials throughout the thermoplastic.
Process control:
Automation and monitoring: Look for metering and mixing systems with advanced process control capabilities. Automation and real-time monitoring help maintain consistent processing conditions and quickly identify and correct any deviations.
Integration: Ensure dosing and mixing systems integrate seamlessly with your existing processing equipment. Compatibility is crucial for smooth operation.
Material changes: Consider whether the system allows easy and quick changes. This is important if you frequently switch between different thermoplastics or formulations.
Technological Advances in Thermoplastic Dosing & Mixing System!
Rapid advances in manufacturing technology have significantly impacted the Dosing & Mixing System.
Precision measurement technology:
Dose accuracy and precision may be improved through advanced sensors, improved algorithms, and closed-loop control systems. Ensures that the correct amount of additive or colorant is consistently added to the thermoplastic.
Intelligent interconnected system:
Intelligent technologies such as IoT monitor and control real-time Dosing & mixing processes. This enables remote monitoring, predictive maintenance, and data-driven decision-making.
Industry 4.0 integration:
Increased integration with Industry 4.0 principles, incorporating capabilities such as data exchange, automation, and cyber-physical systems to improve production processes’ overall efficiency and responsiveness.
Automatic material conversion:
The improved system enables fast, automated material changeovers, allowing manufacturers to switch between different thermoplastics or formulations more efficiently, reducing downtime.
Advanced Mixing Technology:
We at Topstar develop innovative mixing technologies to ensure better dispersion of additives and uniformity of the final product. This includes static mixers, dynamic mixing elements, or other advanced mechanisms.
Customization and flexibility:
More customizable dosing and mixing systems to accommodate a broader range of thermoplastics, formulations, and production requirements. This includes a modular design that can be easily extended or modified.
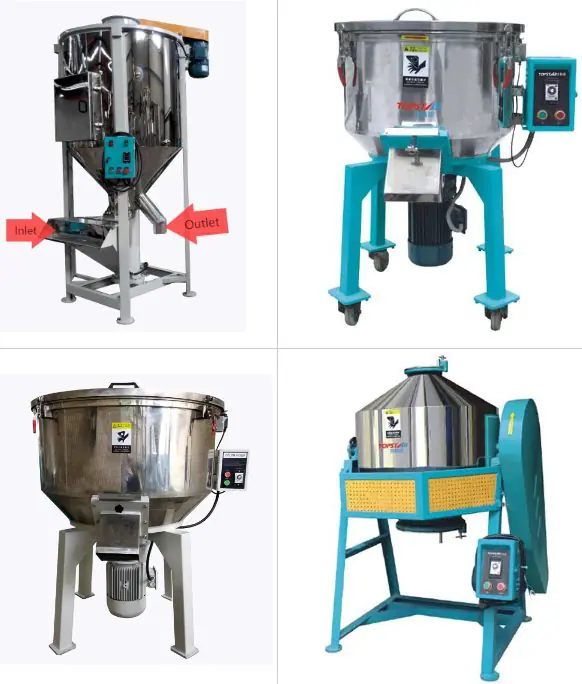
Customized Dosing & Mixing Systems for thermoplastic applications
No two manufacturing processes are the same, and this is true for thermoplastic applications. The customization aspect goes beyond the hardware of the dosing & mixing system. Software interfaces and control mechanisms enable seamless integration with existing production setups. The user-friendly interface enables easy recipe management, fast changeovers, and adaptive control strategies, allowing plastics manufacturers to respond quickly to changing production requirements. The ability to scale up or down based on production needs provides manufacturers with varying processing requirements and a flexible and cost-effective solution. Modular systems allow for easy upgrades and expansion as technology advances, ensuring a future-proof dosing and blending infrastructure.

Quality control of thermoplastic compounding and mixing
In thermoplastic processing, maintaining precise material proportions and uniform dispersion is critical. From accurate weight measurement to real-time consistency monitoring, these capabilities play a crucial role in ensuring the production of high-quality thermoplastic parts. Focusing on quality control not only reduces waste but also improves the overall reliability of the manufacturing process. These technologies provide real-time insights into material properties, allowing dosing and mixing parameters to be instantly adjusted to maintain desired product quality. Additionally, compliance with international quality standards such as ISO certification reinforces our commitment to providing the highest quality thermoplastic products. Integrating quality control data into a more extensive data analytics framework enables predictive quality assurance, minimizing defects and ensuring continuous improvement of the thermoplastic manufacturing process.
Choosing the best batching and mixing system
Plastic manufacturers can confidently select compounding and mixing systems that enhance their thermoplastic processing capabilities by considering key factors, understanding technological advancements, and emphasizing customization and quality control.
TRENDING POSTS
- What factors can cause delays in the injection molding process of plastic molding machine? 2023/11/17
- Exhibition Review| Topstar participates in InterPlas Thailand 2024 2023/11/17
- Star Case | Topstar helps Santong upgrade its intelligent plant 2023/11/17
- Topstar Special | National Science and Technology Workers Day 2023/11/17
HOT TOPIC
- 3 in 1 Compact Dehumidifying Dryer
- 5-axis CNC machine
- accuracy
- Air Chillers
- all electric injection molding machine
- all electric injection molding machines
- All-electric injection molding machines
- and overall production quality. Therefore
- AP-RubberPlas
- automated injection molding machine
- Automation changed engineering
- automation of injection molding robots
- auxiliary machine
- Bench Injection Molding Machine
- Cabinet dryer manufacturers
- Cabinet dryers
- chiller
- CNC Drilling Machine
- CNC Drilling Machines
- cnc engraving machine manufacturer
- cnc laser cutting machine manufacturer
- CNC machine
- CNC Machine Center
- CNC Machine for Sale
- CNC Machine Manufacturing
- CNC Machine Tool
- CNC machine tool product
- CNC Machining Center
- CNC wood carving machine
- Cooling system
- Cross-Walking Single Axis Servo Cylinder Robot
- Cross-Walking Single-Axis Servo Cylinder Robot
- Cross-Walking Three-Axis/Five-Axis Servo Driven Robot
- cross-walking three-axis/five-axis servo-driven robot
- Dehumidifier Dryer
- Dehumidifying Dryer
- delta parallel robot
- Desktop Injection Molding Machine
- Desktop injection molding machines
- Desktop Molding Machine
- desktop plastic injection machine
- Desktop Plastic Injection Molding Machine
- direct clamp injection molding machine
- Direct clamp injection molding machines
- Dosing & mixing system
- Drilling Centers
- Drying and dehumidification system
- drying and dehumidifying equipment
- Drying and Dehumidifying System
- drying system
- effective and efficient. Cabinet dryers are also used in other industries where large quantities of material need to be dried
- efficient injection molding machine
- elbow hydraulic injection molding machines
- electric injection molding machine
- electric injection molding machines
- energy-saving injection molding machine
- etc. Among injection molding robots
- exhibition
- features of CNC machine
- Feeding And Conveying System
- Five Axis Machine Center
- Fully automatic injection molding machine
- Gathering Topstar
- giant injection molding machine
- GMU-600 5-Axis Machining Center
- Granulating & Recycling System
- Heavy duty injection molding machine
- Honeycomb rotor dehumidifier
- horizontal injection molding machine
- Horizontal Injection Molding Machines
- Horizontal Injection Moulding Machine
- Horizontal Mixer manufacturer
- How The CNC Machine Works
- hybrid injection molding machine
- hydraulic injection molding machine
- Hydraulic Injection Molding Machines
- in this article
- Industrial robot
- Industrial Robot Chinese brand
- industrial robot parts
- industrial robot supplier
- Industrial robots
- Industry Chain
- Injection Manipulator
- injection mold machines
- Injection molding
- Injection molding automation
- Injection Molding Automation Solution
- injection molding dryer
- Injection molding equipment
- injection molding hopper dryer
- Injection molding machine
- injection molding machine brand
- Injection Molding Machine Factory
- Injection Molding Machine Manufacture
- Injection molding machine manufacturer
- injection molding machine manufacturers
- Injection molding machine procurement
- injection molding machine robotic arm
- injection molding machine with a robot
- Injection molding machines
- injection molding material dehumidifying
- injection molding plant
- Injection Molding Robot
- injection molding robot arm
- Injection molding robot automation
- Injection molding robotic arm
- injection molding robots
- Injection Moulding Robots
- Injection Robot
- Injection robot arm
- Injection robot manufacturer
- Injection robot wholesale
- injection robots
- intelligent injection molding machines
- Introducing Injection Robot
- It is the best choice for drying large quantities of material at once. Cabinetmakers use these machines because they are fast
- large injection molding machine
- Learn what industrial automation and robotics is
- low speed sound-proof granulator
- machine plastic molding
- make sure to add some! Improvements (2) Keyphrase in introduction: Your keyphrase or its synonyms appear in the first paragraph of the copy
- manipulator machine
- manufacturing
- micro injection molding machine
- middle speed granulator
- Mini CNC machine manufacturers.
- Mold Temperature Control System
- mold temperature controller
- molding material Dehumidifying System
- mould temperature controller
- mould temperature controllers
- New electric injection molding machine
- nitrogen dryer manufacturer
- nitrogen dryer system manufacturer
- Oil type mold temperature controller
- open day
- Outbound links: No outbound links appear in this page. Add some! Images: No images appear on this page. Add some! Internal links: No internal links appear in this page
- PET Preform injection molding
- phone case maker machine
- phone case making machine
- plastic bottle making machine
- plastic bottle manufacturing
- plastic bucket making machine
- plastic bucket manufacturing
- Plastic chair making machine
- plastic forming equipment
- plastic hopper dryer
- plastic injection machine
- plastic injection machines
- plastic injection molding
- Plastic injection molding equipment
- Plastic injection molding machine
- Plastic Injection Molding Machines
- plastic injection robot
- Plastic Molding machine
- Plastic Molding Machines
- plastic molding press
- plastic phone case making machine
- plastic-molding machine
- powerful granulator
- Powerful Type Sound-Proof Granulator
- production of plastic seats
- Robot injection molding
- robot injection molding machine
- robot manufacturing companies
- Robotic arm for injection molding machine
- robotic injection molding machines
- robotics in injection molding
- SCARA robot
- SCARA robots
- Service-oriented manufacturing
- Servo Cylinder Robot
- servo driven robot
- Servo Driven Robots
- servo injection robots
- Servo-Driven Robot
- Setup of injection machine
- Silicone Injection Molding Machine
- six-axis industrial robot
- Stainless Hopper Dryer
- Stainless Hopper Dryers
- star club
- swing arm robot
- the choice between servo-driven robots and hydraulic robots will have a certain impact on efficiency
- the most popular injection molding machine
- the type of injection molding robot
- toggle clamp injection molding machine
- Toggle Hydraulic Injection Molding Machines
- toggle injection molding machine
- Top 10 brands of injection robots
- Topstar
- Topstar Engineering
- Topstar Industrial Robots
- Topstar injection molding intelligent
- Topstar Scara Robots
- Useful Injection molding machine
- Vertical machining centers
- volumetric type blender
- water chiller
- water chillers
- water distributor
- Water Type MoldTemperature Controller
- We often face choices when performing injection molding. We will choose the type of injection molding machine
- wholesale of injection molding machines
- x carve CNC