Best Hydraulic Injection Molding Machines for Bulk Purchase
2024/05/29 By Topstar
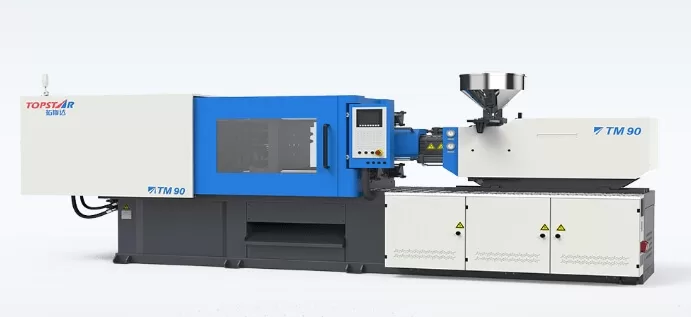
For high-volume production, efficiency, reliability, and cost are key considerations for manufacturers. Because precision and consistency of plastic products are essential during the production process. For the plastic manufacturing industry, hydraulic injection molding machines are an integral part of the production process, have numerous advantages, and are ideal for large-volume purchases. This guide will dive deeply into the best hydraulic injection molding machines for large-volume purchases.
The benefits of ordering hydraulic injection molding machines in bulk
It is worth understanding the benefits of large-scale purchases before understanding the most suitable hydraulic injection molding machines for bulk purchases. In the manufacturing industry, especially this kind of large machinery, buying it individually is very uneconomical for injection molding machine manufacturers. Then, for plastic manufacturers, large-scale purchases can meet the needs of your multiple production lines. Large-scale purchases enable manufacturers to streamline production processes. Instead of handling multiple small orders, companies can consolidate procurement work and streamline logistics to improve operational efficiency. This streamlined approach can shorten delivery time and ensure timely delivery of equipment.
Hydraulic injection molding machines suitable for bulk purchases
The TM hydraulic injection molding machine series is the most suitable for bulk purchases. We have comprehensively upgraded their injection molding, clamping, hydraulic systems, and machine parameters. The template design can balance the force and is suitable for most products, which is one of the reasons why they are suitable for batch purchases. In addition, the new machine hinge design can ensure the smooth movement of the whole machine and is not easy to vibrate in combination with motion simulation and simulation. While improving energy efficiency, it also greatly extends the life of mechanical parts and molds and reduces downtime accidents caused by parts wear and failure. This is very important for large-scale manufacturing.
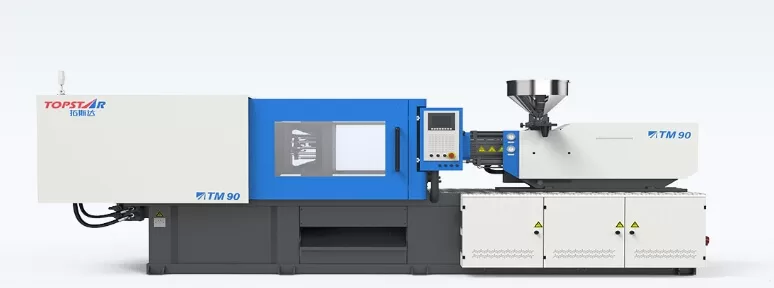
Adopting a new hinge design concept
The core of the new hinge design concept is the use of an inverted five-point hinge structure. The oblique five-point hinge design has a high load-bearing capacity, compact structure, good motion performance, and fast speed, which can reliably ensure the stability of the injection molding machine operation process and ensure product quality and work efficiency. At the same time, it can reduce gaps and deflections so that accurate mold movement and consistent part quality can be achieved throughout the production cycle. The newly designed hinge structure provides smoother operation and easier access to key components, making machine setup, operation, and maintenance more intuitive and efficient.
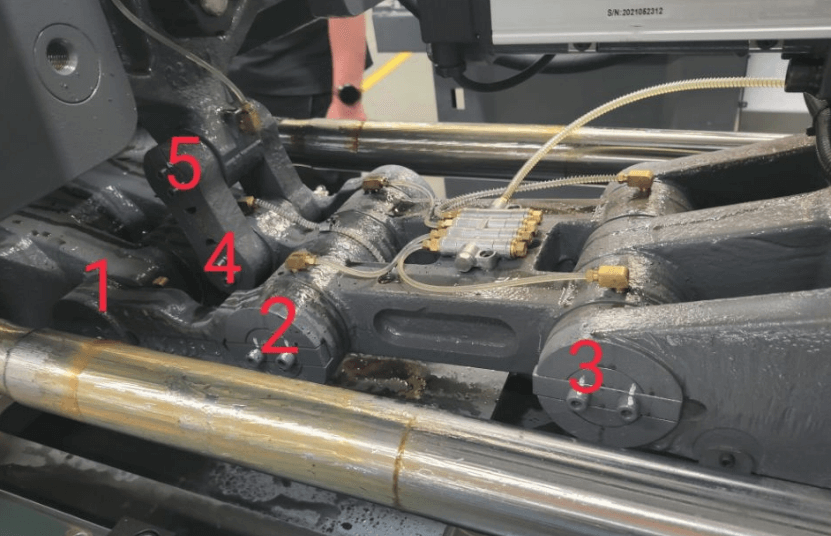
Super Strong Platen Design
The super strong platen design implements balanced force distribution. By evenly distributing the force on the mold, this design minimizes the risk of uneven pressure distribution, reducing defects and ensuring consistent part quality throughout production. In addition, the versatility brought by the balanced force design makes this hydraulic injection molding machine ideal for a variety of products, and you don’t need to worry about their limitations when you buy in large quantities. Therefore, manufacturers can rely on this machine to obtain product consistency results in automotive parts, consumer goods, or electronic housings.
Core pulling oil valve with modular design
In the hydraulic system, the core pulling oil valve with modular design can be freely matched with the number of core pulling groups as needed. This adaptability ensures compatibility with various molds and production settings, enhances versatility, and maximizes operational efficiency. In addition, the modularity of the core pulling oil valve simplifies maintenance and troubleshooting procedures because individual modules can be easily accessed and replaced without extensive disassembly. This can reduce downtime and optimize productivity.
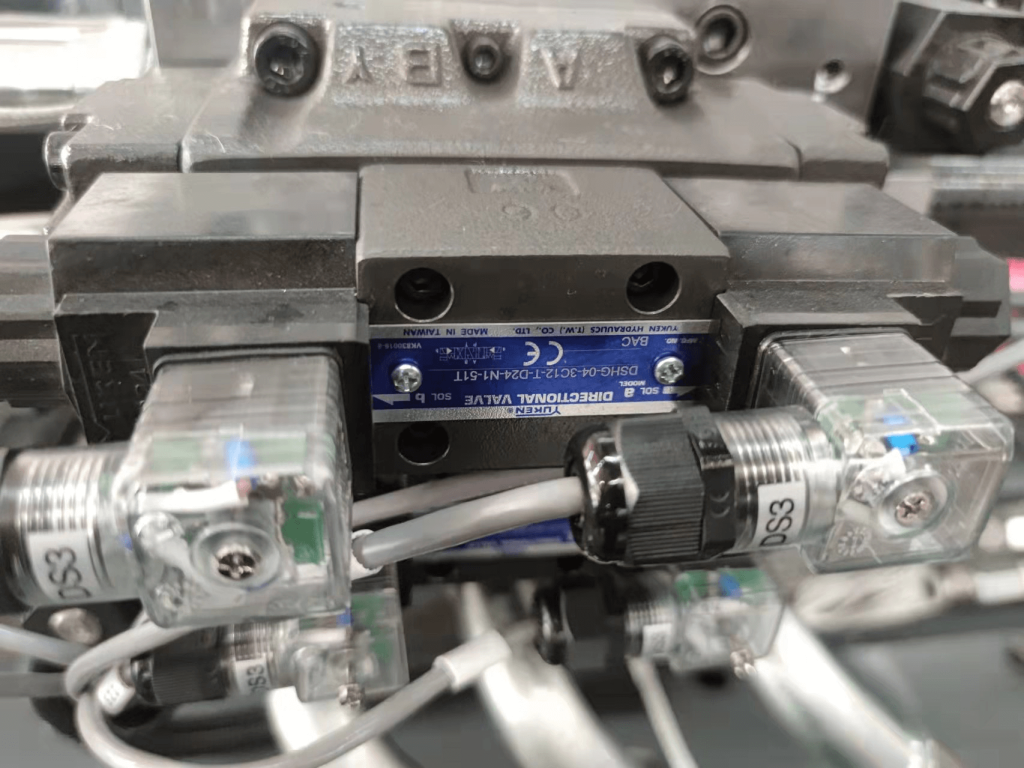
Make your mass production more efficient
Hydraulic injection molding machines are still the first choice for mass production in various industries. Their superb template design and modular core-pulling oil valves make them indispensable for the mass production of high-quality parts. Manufacturers can also simplify the production process by purchasing hydraulic injection molding machines in bulk.
TRENDING POSTS
- What factors can cause delays in the injection molding process of plastic molding machine? 2024/05/29
- Exhibition Review| Topstar participates in InterPlas Thailand 2024 2024/05/29
- Star Case | Topstar helps Santong upgrade its intelligent plant 2024/05/29
- Topstar Special | National Science and Technology Workers Day 2024/05/29
HOT TOPIC
- .ervo motor-driven linear robots
- 1.0 guangdong topstar technology co. ltd
- 1.0 topstar china
- 1.0 topstar robot
- 11
- 2
- 21
- 23
- 3 axis robot
- 3 axis robots
- 3 in 1 Compact Dehumidifying Dryer
- 3-axis robot
- 3-axis robots
- 39
- 41
- 5-axis CNC machine
- 62
- accuracy
- Air Chillers
- all electric injection molding machine
- all electric injection molding machines
- All-electric injection molding machines
- and overall production quality. Therefore
- AP-RubberPlas
- automated injection molding machine
- Automation changed engineering
- automation of injection molding robots
- auxiliary machine
- Bench Injection Molding Machine
- Cabinet dryer manufacturers
- Cabinet dryers
- chiller
- CNC Drilling Machine
- CNC Drilling Machines
- cnc engraving machine manufacturer
- cnc laser cutting machine manufacturer
- CNC machine
- CNC Machine Center
- CNC Machine for Sale
- CNC Machine Manufacturing
- CNC Machine Tool
- CNC machine tool product
- CNC Machining Center
- CNC wood carving machine
- Cooling system
- Cross-Walking Single Axis Servo Cylinder Robot
- Cross-Walking Single-Axis Servo Cylinder Robot
- Cross-Walking Three-Axis/Five-Axis Servo Driven Robot
- cross-walking three-axis/five-axis servo-driven robot
- Dehumidifier Dryer
- Dehumidifying Dryer
- delta parallel robot
- Desktop Injection Molding Machine
- Desktop injection molding machines
- Desktop Molding Machine
- desktop plastic injection machine
- Desktop Plastic Injection Molding Machine
- direct clamp injection molding machine
- Direct clamp injection molding machines
- Dosing & mixing system
- Drilling Centers
- Drying and dehumidification system
- drying and dehumidifying equipment
- Drying and Dehumidifying System
- drying system
- effective and efficient. Cabinet dryers are also used in other industries where large quantities of material need to be dried
- efficient injection molding machine
- elbow hydraulic injection molding machines
- electric injection molding machine
- electric injection molding machines
- energy-efficient injection molding robot
- energy-saving injection molding machine
- etc. Among injection molding robots
- exhibition
- features of CNC machine
- Feeding And Conveying System
- Five Axis Machine Center
- Fully automatic injection molding machine
- Gathering Topstar
- giant injection molding machine
- GMU-600 5-Axis Machining Center
- Granulating & Recycling System
- Heavy duty injection molding machine
- High-precision electric molding machines
- high-precision plastic molding machines
- high-speed all electric injection molding machine
- Honeycomb rotor dehumidifier
- horizontal injection molding machine
- Horizontal Injection Molding Machines
- Horizontal Injection Moulding Machine
- Horizontal Mixer manufacturer
- How The CNC Machine Works
- hybrid injection molding machine
- hydraulic injection molding machine
- Hydraulic Injection Molding Machines
- in this article
- Industrial robot
- Industrial Robot Chinese brand
- industrial robot parts
- industrial robot supplier
- Industrial robots
- Industry Chain
- Injection Manipulator
- injection manipulator robot
- injection mold machines
- Injection molding
- Injection molding automation
- Injection Molding Automation Solution
- injection molding dryer
- Injection molding equipment
- injection molding hopper dryer
- Injection molding machine
- injection molding machine brand
- Injection Molding Machine Factory
- Injection Molding Machine Manufacture
- Injection molding machine manufacturer
- injection molding machine manufacturers
- Injection molding machine procurement
- injection molding machine robotic arm
- injection molding machine with a robot
- Injection molding machines
- injection molding material dehumidifying
- injection molding plant
- Injection Molding Robot
- injection molding robot arm
- Injection molding robot automation
- Injection molding robotic arm
- injection molding robots
- Injection moulding machine
- Injection Moulding Robots
- Injection Robot
- Injection robot arm
- Injection robot manufacturer
- Injection robot wholesale
- injection robots
- intelligent injection molding machines
- Introducing Injection Robot
- It is the best choice for drying large quantities of material at once. Cabinetmakers use these machines because they are fast
- large injection molding machine
- large injection molding machines
- Learn what industrial automation and robotics is
- linear robot
- linear robots
- low speed sound-proof granulator
- machine plastic molding
- make sure to add some! Improvements (2) Keyphrase in introduction: Your keyphrase or its synonyms appear in the first paragraph of the copy
- manipulator machine
- manufacturing
- medical grade injection molding machines
- medical injection molding machine
- medical injection molding machines
- micro injection molding machine
- middle speed granulator
- Mini CNC machine manufacturers.
- Mold Temperature Control System
- mold temperature controller
- mold temperature controllers
- molding material Dehumidifying System
- mould temperature control system
- mould temperature controller
- mould temperature controllers
- New electric injection molding machine
- nitrogen dryer manufacturer
- nitrogen dryer system manufacturer
- Oil type mold temperature controller
- Oil type mold temperature controllers
- open day
- Outbound links: No outbound links appear in this page. Add some! Images: No images appear on this page. Add some! Internal links: No internal links appear in this page
- PET Preform injection molding
- phone case maker machine
- phone case making machine
- plastic bottle making machine
- plastic bottle manufacturing
- plastic bucket making machine
- plastic bucket manufacturing
- Plastic chair making machine
- plastic forming equipment
- plastic hopper dryer
- plastic injection machine
- plastic injection machines
- plastic injection molding
- Plastic injection molding equipment
- Plastic injection molding machine
- Plastic Injection Molding Machines
- plastic injection moulding machine
- plastic injection robot
- Plastic Molding machine
- Plastic Molding Machines
- plastic molding press
- plastic moulding machine
- plastic phone case making machine
- plastic-molding machine
- powerful granulator
- Powerful Type Sound-Proof Granulator
- precision injection molding
- precision injection molding machines
- production of plastic seats
- pure water mould temperature controller
- Robot injection molding
- robot injection molding machine
- robot manufacturing companies
- Robotic arm for injection molding machine
- robotic injection molding machines
- robotics in injection molding
- SCARA robot
- SCARA robots
- Service-oriented manufacturing
- Servo Cylinder Robot
- servo driven robot
- Servo Driven Robots
- servo injection robots
- servo motor-driven linear robots
- servo-driven 3-axis robot
- Servo-Driven Robot
- Setup of injection machine
- Silicone Injection Molding Machine
- six-axis industrial robot
- Stainless Hopper Dryer
- Stainless Hopper Dryers
- star club
- swing arm robot
- take-out robots
- the choice between servo-driven robots and hydraulic robots will have a certain impact on efficiency
- the most popular injection molding machine
- the type of injection molding robot
- toggle clamp injection molding machine
- Toggle Hydraulic Injection Molding Machines
- toggle injection molding machine
- Top 10 brands of injection robots
- Topstar
- Topstar Engineering
- Topstar Industrial Robots
- Topstar injection molding intelligent
- Topstar Scara Robots
- Useful Injection molding machine
- Vertical machining centers
- volumetric type blender
- water chiller
- water chillers
- water distributor
- water type mold temperature controller
- Water Type MoldTemperature Controller
- Water-Type Mould Temperature Controllers
- We often face choices when performing injection molding. We will choose the type of injection molding machine
- wholesale of injection molding machines
- x carve CNC
- 热门查询 点击次数 展示 排名 topstar