Auxiliary equipment: Drying and Dehumidifying System
2024/02/09 By Topstar
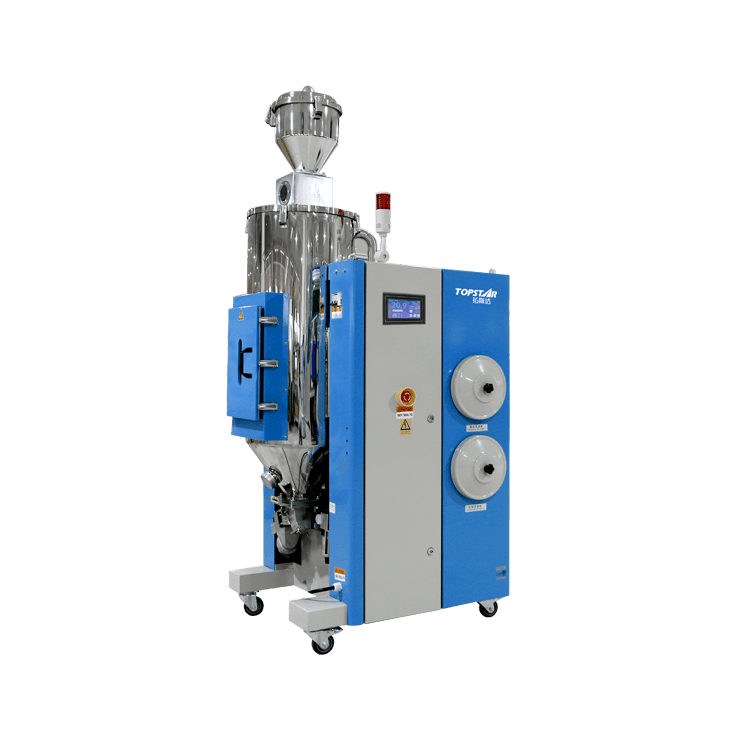
The complete injection molding process usually includes injection molding machine robots, injection molding machines, and auxiliary equipment. The drying and dehumidifying system is a type of auxiliary equipment and is mainly used for drying and transporting injection molding raw materials. This guide will introduce you to the detailed features of drying and dehumidification systems.
Drying and Dehumidifying System usually include integrated
Drying and dehumidification functions and the two-stage feeding merge the three essential functions into a whole.
Dehumidification is a critical point in injection molding, which is the removal of moisture from the injection molding raw material because excessive humidity can damage the quality of the plastic material, causing defects in the final product and affecting its structural integrity and surface finish. Its drying barrel adopts full mirror stainless steel double-layer insulation and down-blowing air duct design, which can improve drying efficiency and achieve more consistent and reliable production results. It adopts a two-stage feeding structure and is equipped with a cut-off valve to ensure that there is no residual raw material in the material pipe, avoids the moisture resurgence of raw materials, improves the accuracy and control of material transportation, and optimizes the overall efficiency of the production cycle. Precise material transport results in consistent product quality and reduced waste.
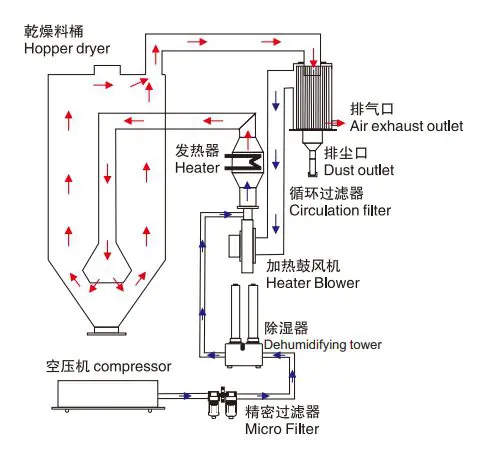
Low power consumption of drying and Dehumidifying System
I designed the drying and dehumidification system with energy efficiency in mind. These systems use our self-developed control system to minimize power usage (power consumption is 0.6 kilowatt hours per hour, compared to 2.5 kilowatt hours for traditional models), which helps save costs using energy-saving components and processes. Utilizing technologies such as heat recovery improves efficiency by recovering energy from the drying process to supplement heating needs. Additionally, proactive regulation by intelligent sensors and automation ensures power usage when necessary.
Adopt all stainless steel feeding systems.
The stainless steel construction of the upper and lower feeding systems offers multiple advantages. First, it ensures corrosion resistance and prevents equipment from rusting. More importantly, using stainless steel in the feeding system solves the critical problem of material contamination. Plastics are susceptible to impurities, and any foreign particles introduced during the feeding process can compromise the integrity of the final product. The stainless steel surface is smooth, non-reactive, and easy to clean, minimizing the risk of contaminants adhering to or penetrating the plastic material. Avoiding material contamination is particularly important for industries such as medical and automotive manufacturing.
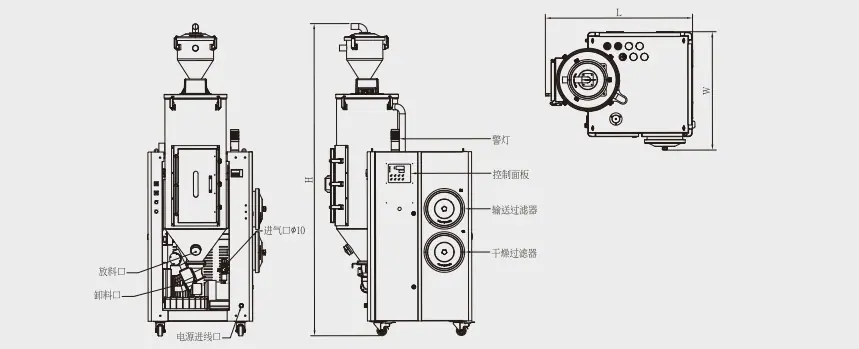
Down-blowing air duct design
The double-layer insulated drying hopper of the drying and dehumidification system adopts a down-blowing air duct design, which can optimize the distribution of hot air in the drying hopper. Introducing hot air from the bottom ensures that the heat is evenly distributed among the plastic pellets in the system. This prevents the formation of temperature gradients that could lead to uneven product quality due to over- or under-drying certain areas. One of the main advantages of this design is its ability to prevent heat energy loss during the drying process, effectively guiding hot air upward through the plastic pellets reducing the spillage of heat energy at the top of the hopper, thereby improving drying efficiency.
Use intelligent fault alarms and brilliant time reservations
Intelligent fault alerts for drying and dehumidification systems enable proactive maintenance and problem resolution, using sensors and diagnostics to monitor the performance of drying and dehumidification components continuously. In the event of any deviation from optimal operating conditions or potential failure, the device triggers automatic alarms. This reduces downtime and prevents potential damage to the machine. In addition, the operator can preset when the drying and dehumidification processes start or end. This scheduling feature enables efficient use of energy resources by aligning equipment operations with production schedules.
Ultimately
It is precisely because our customers pointed out to me that traditional drying and dehumidification systems are not efficient enough and are prone to contamination, so we independently developed a drying and dehumidification system that integrates three functions. This is an innovative and efficient way to improve our injection molding efficiency and product quality integrity.
TRENDING POSTS
- What factors can cause delays in the injection molding process of plastic molding machine? 2024/02/09
- Exhibition Review| Topstar participates in InterPlas Thailand 2024 2024/02/09
- Star Case | Topstar helps Santong upgrade its intelligent plant 2024/02/09
- Topstar Special | National Science and Technology Workers Day 2024/02/09
HOT TOPIC
- 3 in 1 Compact Dehumidifying Dryer
- 5-axis CNC machine
- accuracy
- Air Chillers
- all electric injection molding machine
- All-electric injection molding machines
- and overall production quality. Therefore
- AP-RubberPlas
- automated injection molding machine
- Automation changed engineering
- automation of injection molding robots
- auxiliary machine
- Bench Injection Molding Machine
- Cabinet dryer manufacturers
- Cabinet dryers
- chiller
- CNC Drilling Machine
- CNC Drilling Machines
- cnc engraving machine manufacturer
- cnc laser cutting machine manufacturer
- CNC machine
- CNC Machine Center
- CNC Machine for Sale
- CNC Machine Manufacturing
- CNC Machine Tool
- CNC machine tool product
- CNC Machining Center
- CNC wood carving machine
- Cooling system
- Cross-Walking Single Axis Servo Cylinder Robot
- Cross-Walking Single-Axis Servo Cylinder Robot
- Cross-Walking Three-Axis/Five-Axis Servo Driven Robot
- cross-walking three-axis/five-axis servo-driven robot
- Dehumidifier Dryer
- Dehumidifying Dryer
- delta parallel robot
- Desktop Injection Molding Machine
- Desktop injection molding machines
- Desktop Molding Machine
- desktop plastic injection machine
- Desktop Plastic Injection Molding Machine
- direct clamp injection molding machine
- Direct clamp injection molding machines
- Dosing & mixing system
- Drilling Centers
- Drying and dehumidification system
- drying and dehumidifying equipment
- Drying and Dehumidifying System
- drying system
- effective and efficient. Cabinet dryers are also used in other industries where large quantities of material need to be dried
- efficient injection molding machine
- elbow hydraulic injection molding machines
- electric injection molding machine
- electric injection molding machines
- etc. Among injection molding robots
- exhibition
- features of CNC machine
- Feeding And Conveying System
- Five Axis Machine Center
- Fully automatic injection molding machine
- Gathering Topstar
- giant injection molding machine
- GMU-600 5-Axis Machining Center
- Granulating & Recycling System
- Heavy duty injection molding machine
- Honeycomb rotor dehumidifier
- horizontal injection molding machine
- Horizontal Injection Molding Machines
- Horizontal Injection Moulding Machine
- Horizontal Mixer manufacturer
- How The CNC Machine Works
- hybrid injection molding machine
- hydraulic injection molding machine
- Hydraulic Injection Molding Machines
- in this article
- Industrial robot
- Industrial Robot Chinese brand
- industrial robot parts
- industrial robot supplier
- Industrial robots
- Industry Chain
- Injection Manipulator
- injection mold machines
- Injection molding
- Injection molding automation
- Injection Molding Automation Solution
- injection molding dryer
- Injection molding equipment
- injection molding hopper dryer
- Injection molding machine
- injection molding machine brand
- Injection Molding Machine Factory
- Injection Molding Machine Manufacture
- Injection molding machine manufacturer
- injection molding machine manufacturers
- Injection molding machine procurement
- injection molding machine robotic arm
- injection molding machine with a robot
- Injection molding machines
- injection molding material dehumidifying
- injection molding plant
- Injection Molding Robot
- injection molding robot arm
- Injection molding robot automation
- Injection molding robotic arm
- injection molding robots
- Injection Moulding Robots
- Injection Robot
- Injection robot arm
- Injection robot manufacturer
- Injection robot wholesale
- injection robots
- intelligent injection molding machines
- Introducing Injection Robot
- It is the best choice for drying large quantities of material at once. Cabinetmakers use these machines because they are fast
- large injection molding machine
- Learn what industrial automation and robotics is
- low speed sound-proof granulator
- machine plastic molding
- make sure to add some! Improvements (2) Keyphrase in introduction: Your keyphrase or its synonyms appear in the first paragraph of the copy
- manipulator machine
- manufacturing
- micro injection molding machine
- middle speed granulator
- Mini CNC machine manufacturers.
- Mold Temperature Control System
- mold temperature controller
- molding material Dehumidifying System
- mould temperature controller
- mould temperature controllers
- New electric injection molding machine
- nitrogen dryer manufacturer
- nitrogen dryer system manufacturer
- Oil type mold temperature controller
- open day
- Outbound links: No outbound links appear in this page. Add some! Images: No images appear on this page. Add some! Internal links: No internal links appear in this page
- PET Preform injection molding
- phone case maker machine
- phone case making machine
- plastic bottle making machine
- plastic bottle manufacturing
- plastic bucket making machine
- plastic bucket manufacturing
- Plastic chair making machine
- plastic forming equipment
- plastic hopper dryer
- plastic injection machine
- plastic injection machines
- plastic injection molding
- Plastic injection molding equipment
- Plastic injection molding machine
- Plastic Injection Molding Machines
- plastic injection robot
- Plastic Molding machine
- Plastic Molding Machines
- plastic molding press
- plastic phone case making machine
- plastic-molding machine
- powerful granulator
- Powerful Type Sound-Proof Granulator
- production of plastic seats
- Robot injection molding
- robot injection molding machine
- robot manufacturing companies
- Robotic arm for injection molding machine
- robotic injection molding machines
- robotics in injection molding
- SCARA robot
- SCARA robots
- Service-oriented manufacturing
- Servo Cylinder Robot
- servo driven robot
- Servo Driven Robots
- servo injection robots
- Servo-Driven Robot
- Setup of injection machine
- Silicone Injection Molding Machine
- six-axis industrial robot
- Stainless Hopper Dryer
- Stainless Hopper Dryers
- star club
- swing arm robot
- the choice between servo-driven robots and hydraulic robots will have a certain impact on efficiency
- the most popular injection molding machine
- the type of injection molding robot
- toggle clamp injection molding machine
- Toggle Hydraulic Injection Molding Machines
- toggle injection molding machine
- Top 10 brands of injection robots
- Topstar
- Topstar Engineering
- Topstar Industrial Robots
- Topstar injection molding intelligent
- Topstar Scara Robots
- Useful Injection molding machine
- Vertical machining centers
- volumetric type blender
- water chiller
- water chillers
- water distributor
- Water Type MoldTemperature Controller
- We often face choices when performing injection molding. We will choose the type of injection molding machine
- wholesale of injection molding machines
- x carve CNC