What is the function of Arburg injection molding machine?
2021/12/31 By Topstar
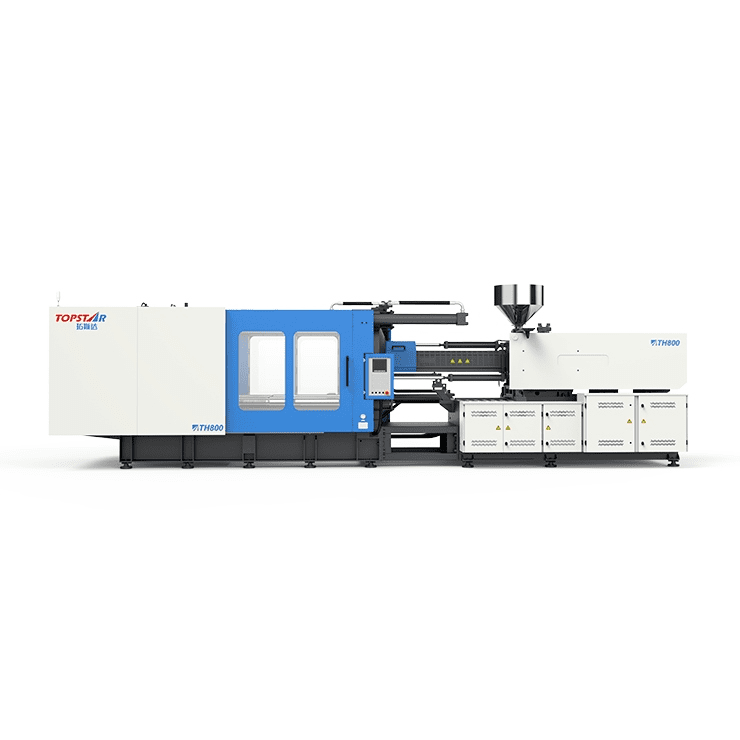
TH Series Direct Press Type Injection Molding Machine (130T-1400T)
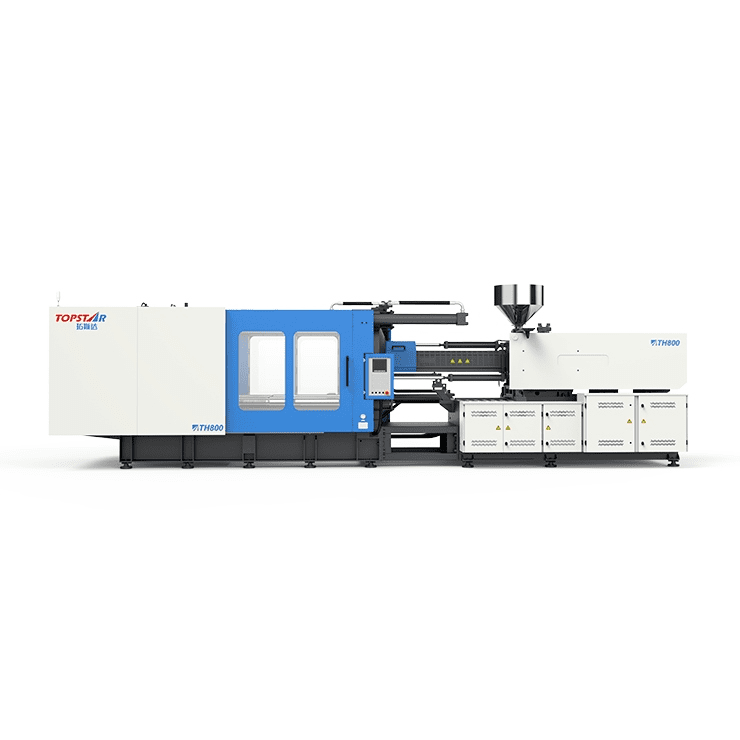
Arburg injection molding machine is the most essential machinery equipment standard in plastic injection processing. In this article, we take a closer look at the structure of the injection molding machine and the parameters of plastic injection molding.
Structure details of the injection molding machine
In general, an ordinary injection molding machine consists of 5 systems. These are:
- Injection molding support system
- Moreover, injection system
- Similarly, the clamping system
- Furthermore, mold system and control system.
Injection molding support system
The injection molding support system consists of 4 subsystems, each with its function.
Body: is the part that has the function of linking the systems of the plastic injection machine together
Electrical System: includes electrical cabinets and wires. Moreover, arburg injection molding machine provides power. In addition, it helps the motor to operate. The electrical system needs to be scientifically designed, helping to ensure the operator’s safety.
Hydraulic System: composes of pump, valve, pipe system, and motor… is the place to generate resources for closing and opening the mold, clamping force, creating a passion for push pin, rotating action of the screw, and sliding movement of the surface core.
The cooling system of the Arburg injection molding machine
The cooling Sy, which is to cool the mold with water or Ethylene Glycol solu, helps the plastic material to harden into the desired shape. It happens before ejection. Furthermore, it solidifies the plastic into a form before the product is ejected from the mold.
Spray system
The Arburg injection molding machine melts the plastic material under temperature. Similarly, it maintains the temperature of the liquefied plastic and compresses and degasses it during the injection of the plastic into the mold cavity and the shaping of the product.
Components of Arburg injection molding machine
The injection system comprises a plastic feed hopper, a plastic container, heating rings, a screw, a nozzle, and a self-opening return unit. During operation, when the screw moves backward, the wedge-shaped barrier moves towards the nozzle, at which time the molten plastic will flow in front of the screw head.
A clamping system with mold opening and closing function helps to hold the mold firmly while waiting for cooling and opens to push the product out of the mold.
The clamping system comes from the following:
- pusher assembly
- Moreover, the clamp assembly,
- Similarly, the connecting rods
- Furthermore, the movable plate and the fixed plate.
Mold system of Arburg injection molding machine
The mold system is a plastic product-forming injection molding system with a fixed and movable half. The fixed part carries the mold cavity (female mold), and the movable part takes the mold core (male mold).
Generally, the mold system with a very complex structure includes the following components:
Guide and positioning system: including guide pin, guide bearing, positioner, positioning ring…
The System of leading plastic into the mold cavity: including the nozzle silver, plastic channel, nozzle…
Product pushing System: including push pin, return pin, support pin, support pin bearing, push plate, retaining plate, support block…
Cooling system: including water lines, grooves, heat pipes, connectors (hollow shaft pipes, faucets)…
Arburg injection molding machine Control system
The Arburg injection molding machine control system is like the machine’s Operating system. Injection molding parameters such as temperature, pressure, injection molding speed, and position of hydraulic system parts… are displayed on the control panel.
The parameters adjust through the control panel displayed on the computer screen. Injection molding parameters are set and must not be changed while the injection molding machine is in operation. The control system is the basis for the injection molding machine’s functions during the entire pressing cycle.
Parameters of injection molding
Generally, different types of Arburg injection molding machines will have other injection molding processing parameters. Some common characteristics in the parameters that the plastic injection machine operator should understand include:
Spray speed
The injection speed has a direct impact on the shape, determining the characteristic properties of the product. It is necessary to set the standard injection molding speed based on the characteristics of the plastic injection machine and the plastic product you want to form.
If the pressing speed is too high, the product will not be aesthetically pleasing, glossy, surface blurred, or seam floating…
If the Arburg injection molding machine speed is too low, it will cause the mold not to fill. Similarly, it causes a lack of material, shrinkage, deformation, and failure to meet the required size standards.
Injection molding speed must also be based on the actual rate, not simply parameters displayed on the control panel.
Injection pressure
Just like injection molding speed, injection pressure affects the operation of the injection molding machine and the characteristics of the formed product.
Injection pressure is an injection molding machine parameter. It comes on calculations by the characteristics of:
- mold structure
- type of plastic material commons
- Temperature and time of the injection molding process.
If the injection molding pressure k adjusts reasonably, it will affect the quality and aesthetics of the formed product. High injection pressure is a standard in producing parts that require thin walls, and high pressure is normal for thick product walls.
The press area of the Arburg injection molding machine
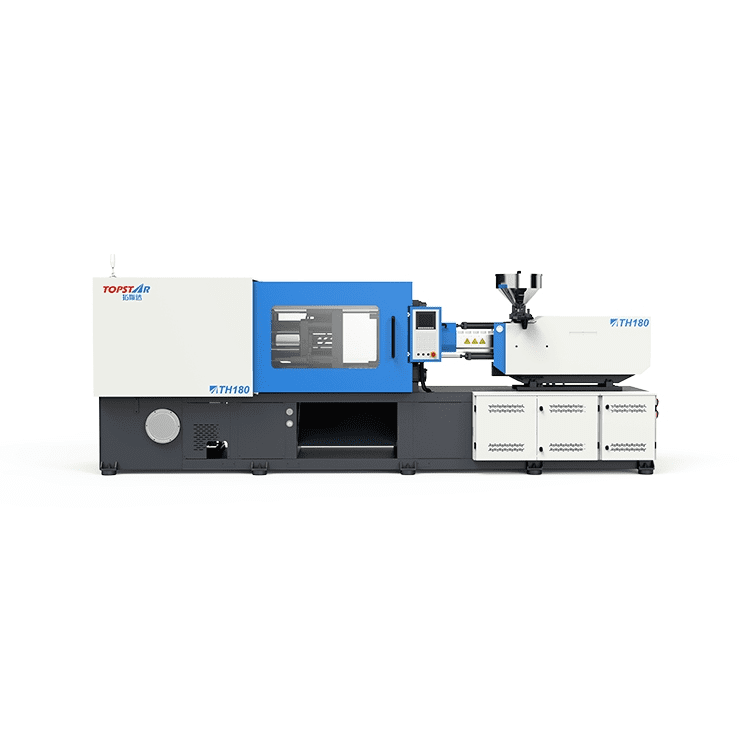
Products with different technical requirements require other injection molding areas. The pressing area is clearly defined, and the setting is reasonable during the injection molding.
The injection area is an injection molding machine parameter that can affect the plastic injection machine’s clamping force, mold size, and technical parameters.
The above article refers to the injection molding machine structure and plastic injection processing parameters. Operating an injection molding machine requires a lot of skills and experience. It is to be able to produce plastic products with the expected quality and high aesthetics.
The technology and advantages of plastic injection molding
Injection molding is manufacturing plastic products by injecting a polymer melts into an injection mold and then cooling it down. Most of the world’s plastic products come in injection molding machines – injection molding machines. Such a technological process is standard for large-scale and small-scale production.
Applications
Arburg injection molding machine has been standard in mass production for over 50 years. This made it possible to produce various plastic products of different sizes, weights, structures, and thicknesses.
Injection molding machines and types of casting
There are several injection molding machines and several methods of injection molding plastics. Moreover, the choice will depend on what products plan to reproduce.
TRENDING POSTS
- What factors can cause delays in the injection molding process of plastic molding machine? 2021/12/31
- Exhibition Review| Topstar participates in InterPlas Thailand 2024 2021/12/31
- Star Case | Topstar helps Santong upgrade its intelligent plant 2021/12/31
- Topstar Special | National Science and Technology Workers Day 2021/12/31
HOT TOPIC
- 3 in 1 Compact Dehumidifying Dryer
- 5-axis CNC machine
- accuracy
- Air Chillers
- all electric injection molding machine
- all electric injection molding machines
- All-electric injection molding machines
- and overall production quality. Therefore
- AP-RubberPlas
- automated injection molding machine
- Automation changed engineering
- automation of injection molding robots
- auxiliary machine
- Bench Injection Molding Machine
- Cabinet dryer manufacturers
- Cabinet dryers
- chiller
- CNC Drilling Machine
- CNC Drilling Machines
- cnc engraving machine manufacturer
- cnc laser cutting machine manufacturer
- CNC machine
- CNC Machine Center
- CNC Machine for Sale
- CNC Machine Manufacturing
- CNC Machine Tool
- CNC machine tool product
- CNC Machining Center
- CNC wood carving machine
- Cooling system
- Cross-Walking Single Axis Servo Cylinder Robot
- Cross-Walking Single-Axis Servo Cylinder Robot
- Cross-Walking Three-Axis/Five-Axis Servo Driven Robot
- cross-walking three-axis/five-axis servo-driven robot
- Dehumidifier Dryer
- Dehumidifying Dryer
- delta parallel robot
- Desktop Injection Molding Machine
- Desktop injection molding machines
- Desktop Molding Machine
- desktop plastic injection machine
- Desktop Plastic Injection Molding Machine
- direct clamp injection molding machine
- Direct clamp injection molding machines
- Dosing & mixing system
- Drilling Centers
- Drying and dehumidification system
- drying and dehumidifying equipment
- Drying and Dehumidifying System
- drying system
- effective and efficient. Cabinet dryers are also used in other industries where large quantities of material need to be dried
- efficient injection molding machine
- elbow hydraulic injection molding machines
- electric injection molding machine
- electric injection molding machines
- energy-saving injection molding machine
- etc. Among injection molding robots
- exhibition
- features of CNC machine
- Feeding And Conveying System
- Five Axis Machine Center
- Fully automatic injection molding machine
- Gathering Topstar
- giant injection molding machine
- GMU-600 5-Axis Machining Center
- Granulating & Recycling System
- Heavy duty injection molding machine
- Honeycomb rotor dehumidifier
- horizontal injection molding machine
- Horizontal Injection Molding Machines
- Horizontal Injection Moulding Machine
- Horizontal Mixer manufacturer
- How The CNC Machine Works
- hybrid injection molding machine
- hydraulic injection molding machine
- Hydraulic Injection Molding Machines
- in this article
- Industrial robot
- Industrial Robot Chinese brand
- industrial robot parts
- industrial robot supplier
- Industrial robots
- Industry Chain
- Injection Manipulator
- injection manipulator robot
- injection mold machines
- Injection molding
- Injection molding automation
- Injection Molding Automation Solution
- injection molding dryer
- Injection molding equipment
- injection molding hopper dryer
- Injection molding machine
- injection molding machine brand
- Injection Molding Machine Factory
- Injection Molding Machine Manufacture
- Injection molding machine manufacturer
- injection molding machine manufacturers
- Injection molding machine procurement
- injection molding machine robotic arm
- injection molding machine with a robot
- Injection molding machines
- injection molding material dehumidifying
- injection molding plant
- Injection Molding Robot
- injection molding robot arm
- Injection molding robot automation
- Injection molding robotic arm
- injection molding robots
- Injection Moulding Robots
- Injection Robot
- Injection robot arm
- Injection robot manufacturer
- Injection robot wholesale
- injection robots
- intelligent injection molding machines
- Introducing Injection Robot
- It is the best choice for drying large quantities of material at once. Cabinetmakers use these machines because they are fast
- large injection molding machine
- Learn what industrial automation and robotics is
- linear robot
- low speed sound-proof granulator
- machine plastic molding
- make sure to add some! Improvements (2) Keyphrase in introduction: Your keyphrase or its synonyms appear in the first paragraph of the copy
- manipulator machine
- manufacturing
- micro injection molding machine
- middle speed granulator
- Mini CNC machine manufacturers.
- Mold Temperature Control System
- mold temperature controller
- molding material Dehumidifying System
- mould temperature controller
- mould temperature controllers
- New electric injection molding machine
- nitrogen dryer manufacturer
- nitrogen dryer system manufacturer
- Oil type mold temperature controller
- open day
- Outbound links: No outbound links appear in this page. Add some! Images: No images appear on this page. Add some! Internal links: No internal links appear in this page
- PET Preform injection molding
- phone case maker machine
- phone case making machine
- plastic bottle making machine
- plastic bottle manufacturing
- plastic bucket making machine
- plastic bucket manufacturing
- Plastic chair making machine
- plastic forming equipment
- plastic hopper dryer
- plastic injection machine
- plastic injection machines
- plastic injection molding
- Plastic injection molding equipment
- Plastic injection molding machine
- Plastic Injection Molding Machines
- plastic injection robot
- Plastic Molding machine
- Plastic Molding Machines
- plastic molding press
- plastic phone case making machine
- plastic-molding machine
- powerful granulator
- Powerful Type Sound-Proof Granulator
- production of plastic seats
- Robot injection molding
- robot injection molding machine
- robot manufacturing companies
- Robotic arm for injection molding machine
- robotic injection molding machines
- robotics in injection molding
- SCARA robot
- SCARA robots
- Service-oriented manufacturing
- Servo Cylinder Robot
- servo driven robot
- Servo Driven Robots
- servo injection robots
- Servo-Driven Robot
- Setup of injection machine
- Silicone Injection Molding Machine
- six-axis industrial robot
- Stainless Hopper Dryer
- Stainless Hopper Dryers
- star club
- swing arm robot
- the choice between servo-driven robots and hydraulic robots will have a certain impact on efficiency
- the most popular injection molding machine
- the type of injection molding robot
- toggle clamp injection molding machine
- Toggle Hydraulic Injection Molding Machines
- toggle injection molding machine
- Top 10 brands of injection robots
- Topstar
- Topstar Engineering
- Topstar Industrial Robots
- Topstar injection molding intelligent
- Topstar Scara Robots
- Useful Injection molding machine
- Vertical machining centers
- volumetric type blender
- water chiller
- water chillers
- water distributor
- Water Type MoldTemperature Controller
- We often face choices when performing injection molding. We will choose the type of injection molding machine
- wholesale of injection molding machines
- x carve CNC