All-electric injection molding machines for optical components
2024/08/01 By Topstar
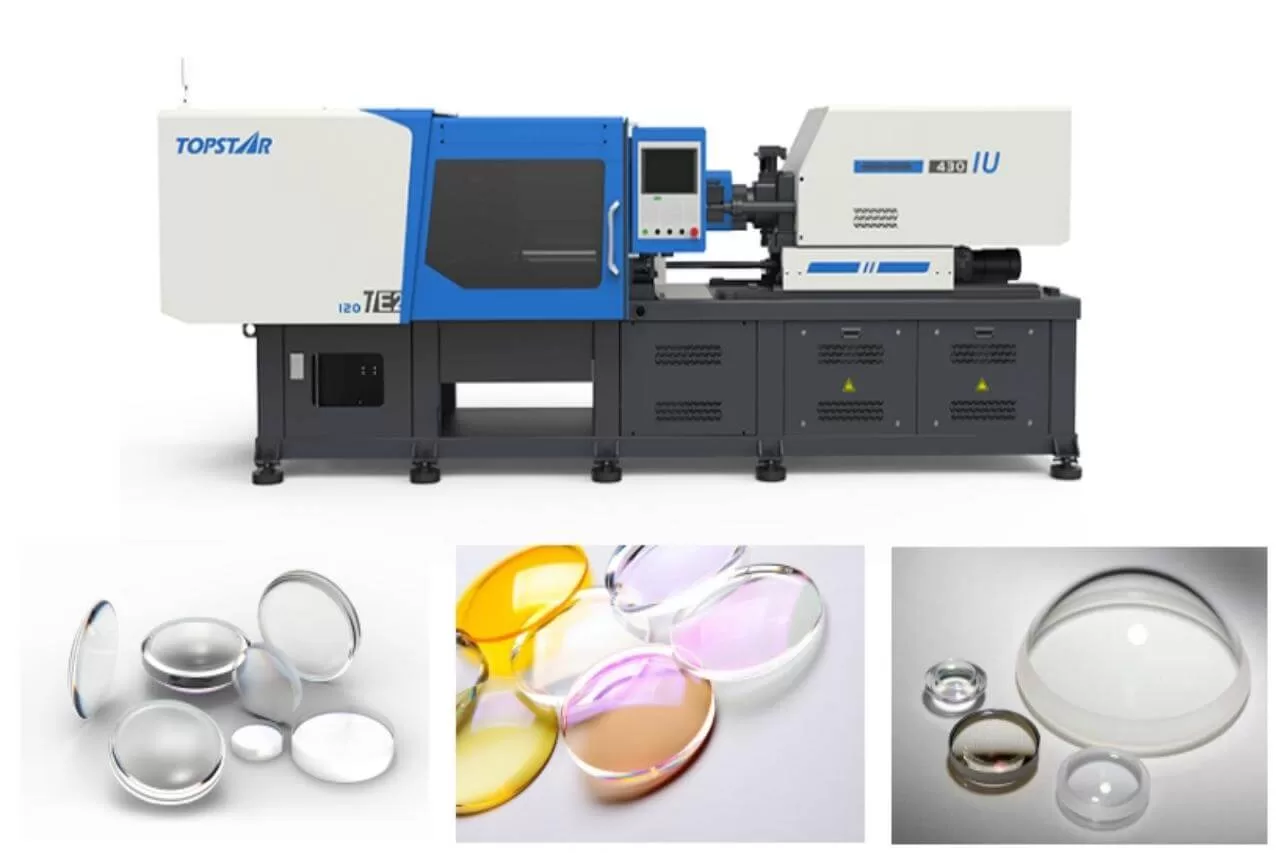
Consumer electronics, industrial machine vision, automotive, medical and other fields are constantly developing around the world, and optical components have great room for development. Under the standards of precision, high standards, high cleanliness and high efficiency, Topstar all-electric injection molding machines have gradually become the first choice for precision optical component injection molding in different regions of the world. So what are the advantages of using all-electric? Why not use other types of injection molding machines? Let’s take a look through this guide.
Advantages of using all-electric injection molding machines
Intelligent injection molding equipment
Precision and consistency are hard standards for the production of optical components such as lenses and prisms. In order to solve the problem of uneven quality control during the molding of precision injection molding products, Topstar has created a new control method and obtained patent certification. It solves the problem of product stability caused by a delay in communication with the control system. The key core is to send the molding process data to the servo drive through the main controller of the upper controller, and the servo drive generates the operation curve by itself. This intelligent drive control mode reduces the impact of communication delay on the high-speed operation of the servo motor, realizes real-time control of the servo motor, improves the accuracy of position, speed and pressure control, and increases the response speed by 8-16 times.
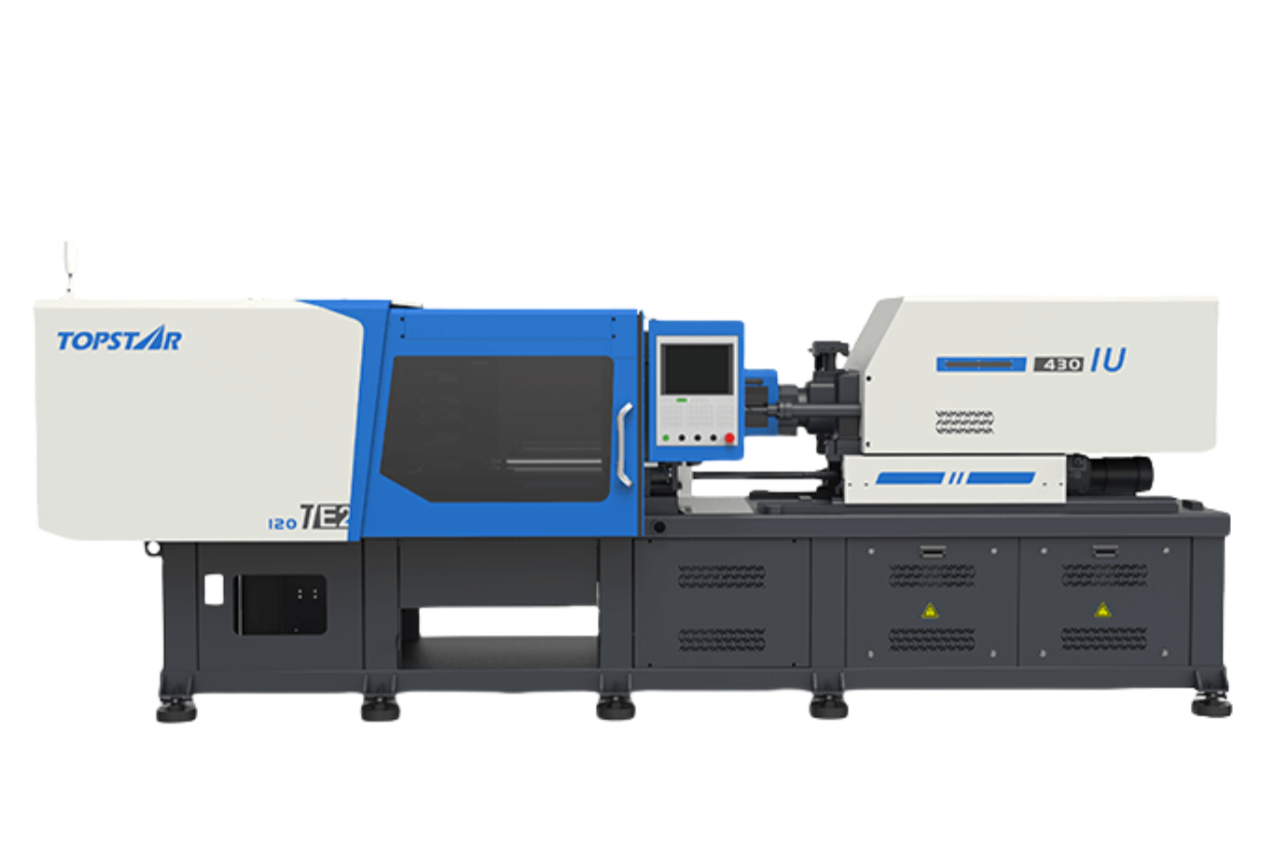
Electric drive process integrated machine
Topstar believes that all-electric injection molding machines are not single injection molding equipment, but that equipment that can solve problems for customers can make “injection molding simpler.” Therefore, Topstar uses intelligent drive control to achieve precise control and fast response of all-electric injection molding machines. Secondly, the concept of “integration of injection molding processes” is also used to give the machine intelligent characteristics such as openness, compatibility, continuous upgrading, and hardware iteration. The integration of the main machine, auxiliary machine and automatic control is realized through an integrated and open system, thereby greatly improving the efficiency of the production cycle. By integrating various links into one system, the technical compatibility of the injection molding machine with peripheral auxiliary equipment and robot automation is achieved, and the number of equipment debugging by operators is reduced, especially for those industries with clean production requirements. The effect is more significant.
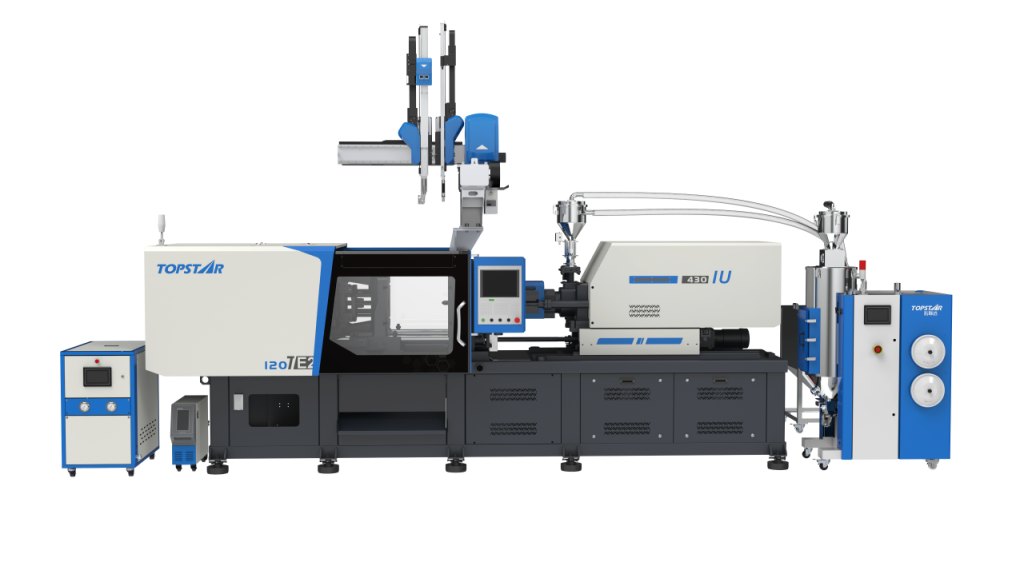
Application scenarios of all-electric injection molding machines
Topstar has a wealth of cases in the application of all-electric injection molding machines and has developed and customized solutions for medical, optical, auto parts, and other industries. For example, in the medical industry, customers save at least 50% of electricity costs after using all-electric motors up to 60%, and the production efficiency of the production line has increased by about 10% compared with the past. In order to meet the needs of customers’ enterprises’ intelligent upgrades, the all-electric series has upgraded Le’s integrated injection seat, high-rigidity body, and widened footrests for dynamic and fixed templates, making electric drive injection molding more flexible and achieving precise control of injection molding, giving customers a stable, safe, reliable and energy-saving first choice.
Why not use other types of injection molding machines?
When performing injection molding of precision optical components, the requirements for optical clarity, dimensional accuracy and surface finish are very strict, so ordinary injection molding machines cannot meet such requirements and cannot provide the necessary control of the molding process, which will lead to to uncontrollable defects in optical components, such as warping, shrinkage or surface defects. Therefore, we require specially designed all-electric injection molding machines to control tolerances precisely, maintain precise temperature control, and ensure constant pressure to produce high-quality optical lenses and components. They process materials under optimal conditions to achieve the desired optical properties and structural integrity.
Improve the quality of delivery
Before delivery, operators must continuously run the equipment for more than 48 hours and test it with a 10,000-level statistical system. They must also test the injection molding machine twice throughout the entire cycle to ensure the equipment’s quality, traceability and stability.
Topstar pays more attention to the production and operation results of customers and provides customers with standardized services for the entire equipment cycle rather than just a single device.
TRENDING POSTS
- What factors can cause delays in the injection molding process of plastic molding machine? 2024/08/01
- Exhibition Review| Topstar participates in InterPlas Thailand 2024 2024/08/01
- Star Case | Topstar helps Santong upgrade its intelligent plant 2024/08/01
- Topstar Special | National Science and Technology Workers Day 2024/08/01
HOT TOPIC
- 3 in 1 Compact Dehumidifying Dryer
- 5-axis CNC machine
- accuracy
- Air Chillers
- all electric injection molding machine
- all electric injection molding machines
- All-electric injection molding machines
- and overall production quality. Therefore
- AP-RubberPlas
- automated injection molding machine
- Automation changed engineering
- automation of injection molding robots
- auxiliary machine
- Bench Injection Molding Machine
- Cabinet dryer manufacturers
- Cabinet dryers
- chiller
- CNC Drilling Machine
- CNC Drilling Machines
- cnc engraving machine manufacturer
- cnc laser cutting machine manufacturer
- CNC machine
- CNC Machine Center
- CNC Machine for Sale
- CNC Machine Manufacturing
- CNC Machine Tool
- CNC machine tool product
- CNC Machining Center
- CNC wood carving machine
- Cooling system
- Cross-Walking Single Axis Servo Cylinder Robot
- Cross-Walking Single-Axis Servo Cylinder Robot
- Cross-Walking Three-Axis/Five-Axis Servo Driven Robot
- cross-walking three-axis/five-axis servo-driven robot
- Dehumidifier Dryer
- Dehumidifying Dryer
- delta parallel robot
- Desktop Injection Molding Machine
- Desktop injection molding machines
- Desktop Molding Machine
- desktop plastic injection machine
- Desktop Plastic Injection Molding Machine
- direct clamp injection molding machine
- Direct clamp injection molding machines
- Dosing & mixing system
- Drilling Centers
- Drying and dehumidification system
- drying and dehumidifying equipment
- Drying and Dehumidifying System
- drying system
- effective and efficient. Cabinet dryers are also used in other industries where large quantities of material need to be dried
- efficient injection molding machine
- elbow hydraulic injection molding machines
- electric injection molding machine
- electric injection molding machines
- energy-saving injection molding machine
- etc. Among injection molding robots
- exhibition
- features of CNC machine
- Feeding And Conveying System
- Five Axis Machine Center
- Fully automatic injection molding machine
- Gathering Topstar
- giant injection molding machine
- GMU-600 5-Axis Machining Center
- Granulating & Recycling System
- Heavy duty injection molding machine
- Honeycomb rotor dehumidifier
- horizontal injection molding machine
- Horizontal Injection Molding Machines
- Horizontal Injection Moulding Machine
- Horizontal Mixer manufacturer
- How The CNC Machine Works
- hybrid injection molding machine
- hydraulic injection molding machine
- Hydraulic Injection Molding Machines
- in this article
- Industrial robot
- Industrial Robot Chinese brand
- industrial robot parts
- industrial robot supplier
- Industrial robots
- Industry Chain
- Injection Manipulator
- injection mold machines
- Injection molding
- Injection molding automation
- Injection Molding Automation Solution
- injection molding dryer
- Injection molding equipment
- injection molding hopper dryer
- Injection molding machine
- injection molding machine brand
- Injection Molding Machine Factory
- Injection Molding Machine Manufacture
- Injection molding machine manufacturer
- injection molding machine manufacturers
- Injection molding machine procurement
- injection molding machine robotic arm
- injection molding machine with a robot
- Injection molding machines
- injection molding material dehumidifying
- injection molding plant
- Injection Molding Robot
- injection molding robot arm
- Injection molding robot automation
- Injection molding robotic arm
- injection molding robots
- Injection Moulding Robots
- Injection Robot
- Injection robot arm
- Injection robot manufacturer
- Injection robot wholesale
- injection robots
- intelligent injection molding machines
- Introducing Injection Robot
- It is the best choice for drying large quantities of material at once. Cabinetmakers use these machines because they are fast
- large injection molding machine
- Learn what industrial automation and robotics is
- low speed sound-proof granulator
- machine plastic molding
- make sure to add some! Improvements (2) Keyphrase in introduction: Your keyphrase or its synonyms appear in the first paragraph of the copy
- manipulator machine
- manufacturing
- micro injection molding machine
- middle speed granulator
- Mini CNC machine manufacturers.
- Mold Temperature Control System
- mold temperature controller
- molding material Dehumidifying System
- mould temperature controller
- mould temperature controllers
- New electric injection molding machine
- nitrogen dryer manufacturer
- nitrogen dryer system manufacturer
- Oil type mold temperature controller
- open day
- Outbound links: No outbound links appear in this page. Add some! Images: No images appear on this page. Add some! Internal links: No internal links appear in this page
- PET Preform injection molding
- phone case maker machine
- phone case making machine
- plastic bottle making machine
- plastic bottle manufacturing
- plastic bucket making machine
- plastic bucket manufacturing
- Plastic chair making machine
- plastic forming equipment
- plastic hopper dryer
- plastic injection machine
- plastic injection machines
- plastic injection molding
- Plastic injection molding equipment
- Plastic injection molding machine
- Plastic Injection Molding Machines
- plastic injection robot
- Plastic Molding machine
- Plastic Molding Machines
- plastic molding press
- plastic phone case making machine
- plastic-molding machine
- powerful granulator
- Powerful Type Sound-Proof Granulator
- production of plastic seats
- Robot injection molding
- robot injection molding machine
- robot manufacturing companies
- Robotic arm for injection molding machine
- robotic injection molding machines
- robotics in injection molding
- SCARA robot
- SCARA robots
- Service-oriented manufacturing
- Servo Cylinder Robot
- servo driven robot
- Servo Driven Robots
- servo injection robots
- Servo-Driven Robot
- Setup of injection machine
- Silicone Injection Molding Machine
- six-axis industrial robot
- Stainless Hopper Dryer
- Stainless Hopper Dryers
- star club
- swing arm robot
- the choice between servo-driven robots and hydraulic robots will have a certain impact on efficiency
- the most popular injection molding machine
- the type of injection molding robot
- toggle clamp injection molding machine
- Toggle Hydraulic Injection Molding Machines
- toggle injection molding machine
- Top 10 brands of injection robots
- Topstar
- Topstar Engineering
- Topstar Industrial Robots
- Topstar injection molding intelligent
- Topstar Scara Robots
- Useful Injection molding machine
- Vertical machining centers
- volumetric type blender
- water chiller
- water chillers
- water distributor
- Water Type MoldTemperature Controller
- We often face choices when performing injection molding. We will choose the type of injection molding machine
- wholesale of injection molding machines
- x carve CNC