A new large injection molding machine dramatically improves production efficiency
2023/02/15 By Topstar
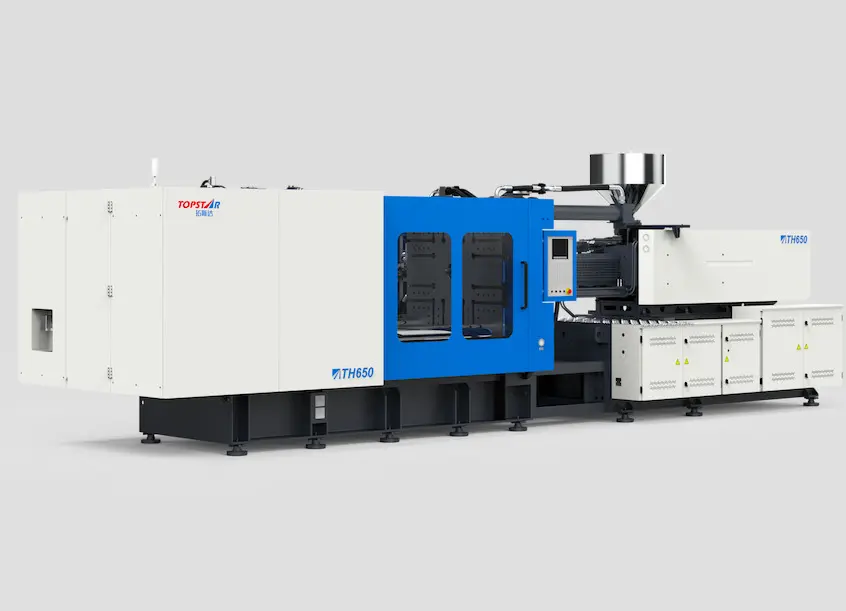
A new large injection molding machine dramatically improves production efficiency
Injection molding has been around for a long time. It is well-known for producing high-quality components with excellent repeatability, from essential plastic parts and components to complex plastic assemblies. Many industries have used injection molding for decades. Injection molding is a process that uses high-pressure hydraulic or screws pumps to push molten material into the cavity of a preheated tool. Once the material fills the hole, it cools down and solidifies immediately after being ejected from the machine’s gate.
Significantly improved production efficiency
The new machine has a larger molding cavity, which means it can produce more significant parts. It also has more complicated molds, which means it can make more complex pieces because of its speed and precision. The new machine can produce more complex molds with higher quality than any other injection molding machine on the market today.
One of the most popular manufacturing processes in the industry
Injection molding in plastics is one of the most popular manufacturing processes used in the industry. This technique has been around for a long time and is well-known for producing high-quality components with excellent repeatability. Plastic injection molding machines manufacture everything from toys to medical devices. But they’re also used to make automotive parts such as bumpers and dashboards. The process involves injecting heated plastic into molds preheated with steam or hot water.
Famous for producing high-quality components
Injection molding is a standard manufacturing process in which plastic parts are produced by injecting molten plastic into a mold cavity. The mold gets its name because it contains two halves that can be clamped around a metal core or runner. Injection molds come in all shapes and sizes, with many different features depending on the component you want to manufacture.
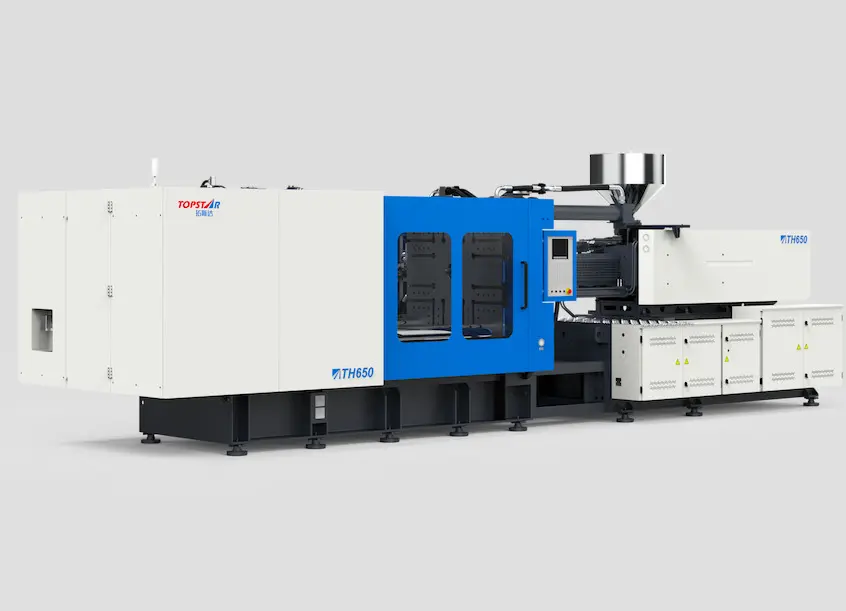
Injection molding machines are very efficient at producing large numbers of parts quickly and cost-effectively–and they’re also great for making small batches! There are many different types available depending on your needs: vertical screw machines tend to be faster than horizontal screw machines but have less precision; single shot vs. multi-cavity molds allow you more flexibility in what kind of products you can produce; single shot vs. multi-cavity molds allow you more flexibility in what kind of products you can have.
Can produce parts from small to large, light to heavy
Injection molding can produce amounts ranging from small to large and soft to rich. The only limit is your imagination.
Injection molding is a manufacturing process that involves forcing molten material into a mold cavity, where it cools and hardens into a final part shape. The resulting products are usually more robust than other processes (such as casting or machining). Because they are made of solid materials rather than hollow cores, they have no structural integrity. And there is no seam between the two halves of the molded part (for example, if you cut two pieces of metal).
It can produce large parts at a low cost.
One of the most significant benefits of using an injection molding machine is that it can produce large parts at a low cost. Injection molding is a standard cost process, and because of this, it’s popular among manufacturers. The ability to produce large quantities at low prices makes injection molding ideal for manufacturing consumer goods such as toys and electronics.
However, there are some points to be noted.
But no matter how efficient an injection molding machine is. There will always be limitations on production due to size constraints, cycle time, and tool complexity.
For example, if you’re trying to produce a part more significant than your current machine’s handle. You may need to look at different devices or processes altogether.
Similarly, suppose yousupposeave complex geometry in your design, and it requires multiple shots with different tools–or even various molds–in t. This will increase costs per part and overall cycle time, so looking at other options might also be needed here!
It is impossible to produce more complex parts in specific applications without changing the manufacturing process. For instance, if a position requires more cavities than your injection molding machine can accommodate at once. You might be able to use two devices instead of one with an adapter plate that allows you to run multiple cavities at once.
Suppose you want more return from the injection molding equipment investment to improve productivity and reduce costs. So this method is ideal!
To sum up
In conclusion, injection molding is a great way to produce high-quality parts at a low cost. Hcreatingnt or more complicated amounts can be challenging without changing the manufacturing process.
TRENDING POSTS
- What factors can cause delays in the injection molding process of plastic molding machine? 2023/02/15
- Exhibition Review| Topstar participates in InterPlas Thailand 2024 2023/02/15
- Star Case | Topstar helps Santong upgrade its intelligent plant 2023/02/15
- Topstar Special | National Science and Technology Workers Day 2023/02/15
HOT TOPIC
- 3 in 1 Compact Dehumidifying Dryer
- 5-axis CNC machine
- accuracy
- Air Chillers
- all electric injection molding machine
- All-electric injection molding machines
- and overall production quality. Therefore
- AP-RubberPlas
- automated injection molding machine
- Automation changed engineering
- automation of injection molding robots
- auxiliary machine
- Bench Injection Molding Machine
- Cabinet dryer manufacturers
- Cabinet dryers
- chiller
- CNC Drilling Machine
- CNC Drilling Machines
- cnc engraving machine manufacturer
- cnc laser cutting machine manufacturer
- CNC machine
- CNC Machine Center
- CNC Machine for Sale
- CNC Machine Manufacturing
- CNC Machine Tool
- CNC machine tool product
- CNC Machining Center
- CNC wood carving machine
- Cooling system
- Cross-Walking Single Axis Servo Cylinder Robot
- Cross-Walking Single-Axis Servo Cylinder Robot
- Cross-Walking Three-Axis/Five-Axis Servo Driven Robot
- cross-walking three-axis/five-axis servo-driven robot
- Dehumidifier Dryer
- Dehumidifying Dryer
- delta parallel robot
- Desktop Injection Molding Machine
- Desktop injection molding machines
- Desktop Molding Machine
- desktop plastic injection machine
- Desktop Plastic Injection Molding Machine
- direct clamp injection molding machine
- Direct clamp injection molding machines
- Dosing & mixing system
- Drilling Centers
- Drying and dehumidification system
- drying and dehumidifying equipment
- Drying and Dehumidifying System
- drying system
- effective and efficient. Cabinet dryers are also used in other industries where large quantities of material need to be dried
- efficient injection molding machine
- elbow hydraulic injection molding machines
- electric injection molding machine
- electric injection molding machines
- etc. Among injection molding robots
- exhibition
- features of CNC machine
- Feeding And Conveying System
- Five Axis Machine Center
- Fully automatic injection molding machine
- Gathering Topstar
- giant injection molding machine
- GMU-600 5-Axis Machining Center
- Granulating & Recycling System
- Heavy duty injection molding machine
- Honeycomb rotor dehumidifier
- horizontal injection molding machine
- Horizontal Injection Molding Machines
- Horizontal Injection Moulding Machine
- Horizontal Mixer manufacturer
- How The CNC Machine Works
- hybrid injection molding machine
- hydraulic injection molding machine
- Hydraulic Injection Molding Machines
- in this article
- Industrial robot
- Industrial Robot Chinese brand
- industrial robot parts
- industrial robot supplier
- Industrial robots
- Industry Chain
- Injection Manipulator
- injection mold machines
- Injection molding
- Injection molding automation
- Injection Molding Automation Solution
- injection molding dryer
- Injection molding equipment
- injection molding hopper dryer
- Injection molding machine
- injection molding machine brand
- Injection Molding Machine Factory
- Injection Molding Machine Manufacture
- Injection molding machine manufacturer
- injection molding machine manufacturers
- Injection molding machine procurement
- injection molding machine robotic arm
- injection molding machine with a robot
- Injection molding machines
- injection molding material dehumidifying
- injection molding plant
- Injection Molding Robot
- injection molding robot arm
- Injection molding robot automation
- Injection molding robotic arm
- injection molding robots
- Injection Moulding Robots
- Injection Robot
- Injection robot arm
- Injection robot manufacturer
- Injection robot wholesale
- injection robots
- intelligent injection molding machines
- Introducing Injection Robot
- It is the best choice for drying large quantities of material at once. Cabinetmakers use these machines because they are fast
- large injection molding machine
- Learn what industrial automation and robotics is
- low speed sound-proof granulator
- machine plastic molding
- make sure to add some! Improvements (2) Keyphrase in introduction: Your keyphrase or its synonyms appear in the first paragraph of the copy
- manipulator machine
- manufacturing
- micro injection molding machine
- middle speed granulator
- Mini CNC machine manufacturers.
- Mold Temperature Control System
- mold temperature controller
- molding material Dehumidifying System
- mould temperature controller
- mould temperature controllers
- New electric injection molding machine
- nitrogen dryer manufacturer
- nitrogen dryer system manufacturer
- Oil type mold temperature controller
- open day
- Outbound links: No outbound links appear in this page. Add some! Images: No images appear on this page. Add some! Internal links: No internal links appear in this page
- PET Preform injection molding
- phone case maker machine
- phone case making machine
- plastic bottle making machine
- plastic bottle manufacturing
- plastic bucket making machine
- plastic bucket manufacturing
- Plastic chair making machine
- plastic forming equipment
- plastic hopper dryer
- plastic injection machine
- plastic injection machines
- plastic injection molding
- Plastic injection molding equipment
- Plastic injection molding machine
- Plastic Injection Molding Machines
- plastic injection robot
- Plastic Molding machine
- Plastic Molding Machines
- plastic molding press
- plastic phone case making machine
- plastic-molding machine
- powerful granulator
- Powerful Type Sound-Proof Granulator
- production of plastic seats
- Robot injection molding
- robot injection molding machine
- robot manufacturing companies
- Robotic arm for injection molding machine
- robotic injection molding machines
- robotics in injection molding
- SCARA robot
- SCARA robots
- Service-oriented manufacturing
- Servo Cylinder Robot
- servo driven robot
- Servo Driven Robots
- servo injection robots
- Servo-Driven Robot
- Setup of injection machine
- Silicone Injection Molding Machine
- six-axis industrial robot
- Stainless Hopper Dryer
- Stainless Hopper Dryers
- star club
- swing arm robot
- the choice between servo-driven robots and hydraulic robots will have a certain impact on efficiency
- the most popular injection molding machine
- the type of injection molding robot
- toggle clamp injection molding machine
- Toggle Hydraulic Injection Molding Machines
- toggle injection molding machine
- Top 10 brands of injection robots
- Topstar
- Topstar Engineering
- Topstar Industrial Robots
- Topstar injection molding intelligent
- Topstar Scara Robots
- Useful Injection molding machine
- Vertical machining centers
- volumetric type blender
- water chiller
- water chillers
- water distributor
- Water Type MoldTemperature Controller
- We often face choices when performing injection molding. We will choose the type of injection molding machine
- wholesale of injection molding machines
- x carve CNC