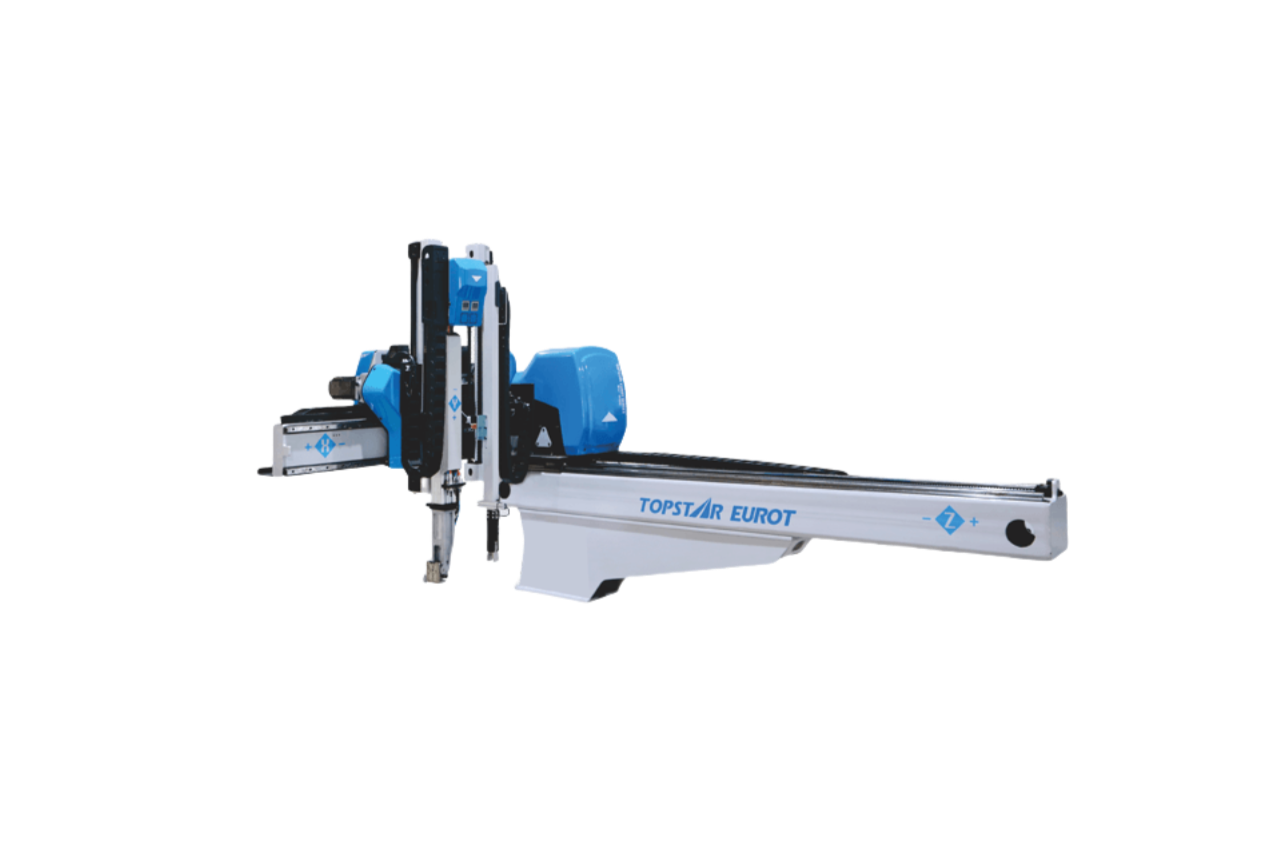
In industrial manufacturing, linear robot guides ensure smooth, precise motion, especially when integrated into injection molding. Conventional designs often use frequent lubrication to keep friction low and prevent premature wear. However, lubrication failure can still occur due to high cycle rates, contamination, or lubricant failure, resulting in system downtime and increased maintenance costs. To address this issue, Topstar uses high-rigidity precision slides and high-strength steel belt drives on its linear robots, reducing metal-to-metal contact and further improving the system’s robustness. And minimize the reliance on lubricant films.
Achieving high speed, low noise, and long life in a linear robot
In injection molding, linear robots can also be called injection molding robots. Its primary goals are high-speed, low-noise gripping work and long service life. Topstar combines high-rigidity precision slides with high-strength steel belt drives to achieve fast acceleration and deceleration without the backlash or vibration common in ball screw systems. This makes its motion trajectory smoother and can meet the stringent cycle time requirements in injection molding robot applications.
Noise reduction is another key advantage. Steel belt systems generate less mechanical noise than more complex gear trains or lead screw mechanisms. This quiet operation improves the working environment and reduces the risk of errors caused by vibration in precision molding processes. In addition, the wear resistance of precision slides and steel belts ensures longer maintenance intervals, often doubling or tripling the service life compared to traditional guideway assemblies. Operators can maximize uptime and maintain high production levels by significantly reducing the frequency of lubrication interventions and mechanical overhauls.
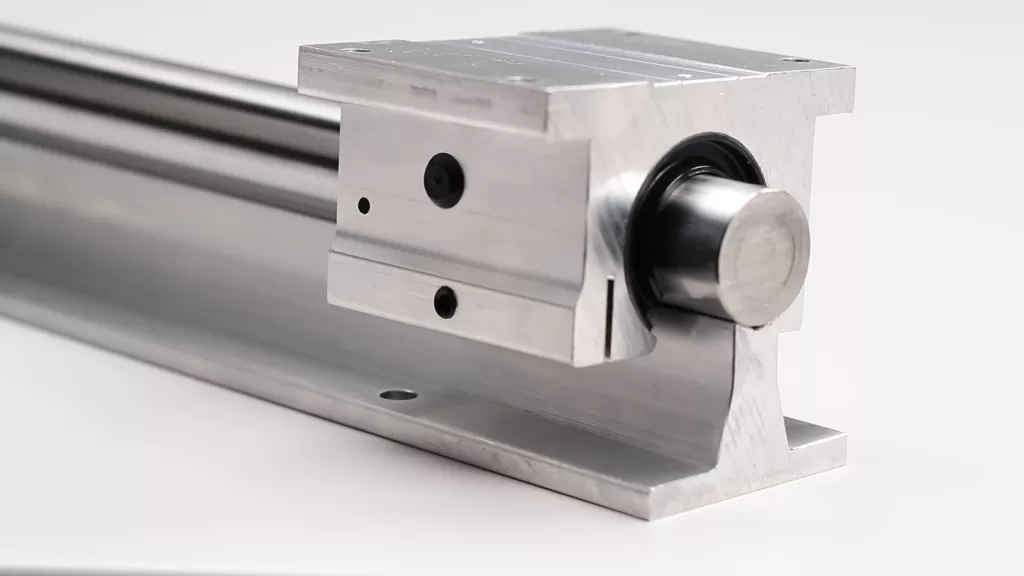
Preventing kinematic interference collisions in a linear robot
Maintaining the reliable operation of linear robot systems requires sturdy guides and effective management of complex kinematics to prevent collisions and mechanical interference. Topstar’s R&D team has obtained over 60 technical patents for injection molding robots. One notable invention is the “Servo robot and its mechanical origin return method,” which ensures that the multi-axis system automatically returns to a known safe position after a power outage or emergency stop. This patent-protected method minimizes configuration drift and eliminates the need for manual recalibration.
In addition, other patents, such as the “Arched Drive Wheel” mechanism, use a curved gear profile to maintain constant contact under variable loads. This feature prevents slippage and misalignment, reducing mechanical stress on guides and transmission components. Combining these patented robot innovations with the linear robot architecture achieves seamless motion coordination, eliminating unexpected collisions and part interference.
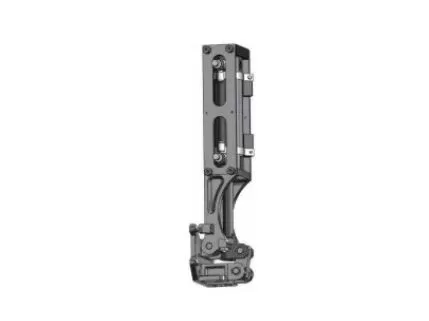
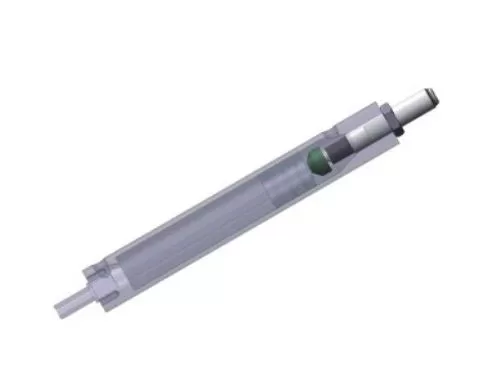
Achieving “Fast Pick-up and Gentle Placement”
Using high speed to handle fragile parts requires extra care to avoid problems such as missed grasping. Topstar’s “Pick and Place Integrated Robot” patent has revolutionized the performance of linear robots by incorporating variable speed descent curves into the robot’s control algorithm. During the pick-up phase inside the mold cavity, the linear robot descends quickly to reduce cycle time. Once the part is grabbed and lifted, the system switches to a slower controlled descent speed and gently delivers it to a collection tray or downstream station outside the mold. This dual-speed solution optimizes throughput and protects delicate molded parts from impact damage. At the same time, the linear robot uses synchronous servo control to achieve high repeatability, ensuring that each part is handled with consistent precision.
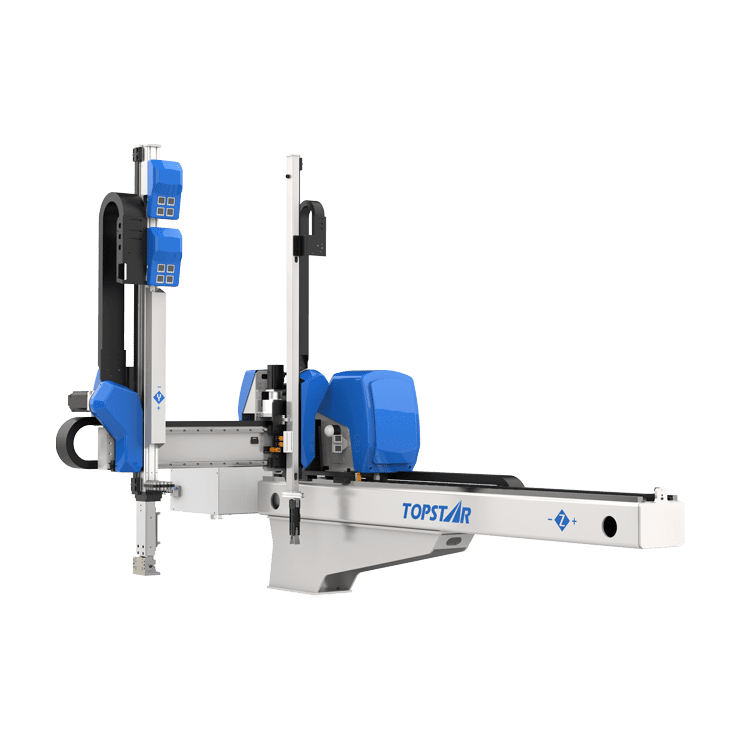
Control system for continuous performance optimization
Topstar applies its control system to linear robots to maintain optimal gripping performance. The system can capture real-time operating data such as position error, cycle time, and torque load. Over time, the system continuously optimizes motion trajectories, predictive maintenance plans, and adaptive torque limits to optimize performance for specific customer workloads. For example, suppose the linear robot exhibits micro-vibration at a certain speed during molding, or a slight accuracy drift occurs during long-term operation. In that case, the control system will autonomously adjust the servo gain, acceleration ramp, and friction compensation parameters. This closed-loop self-optimization method improves accuracy and extends component life by dynamically adapting to wear patterns.
Ultimately
The use of high-rigidity precision slides, high-strength steel belt drives, and innovative technologies ensures that the linear robot can operate at high speed, low noise, and long life to avoid guide lubrication failures. At the same time, under Topstar’s control system, performance evolves in sync with customer needs, thereby providing consistent part quality and maximized uptime.
TRENDING POSTS
- What factors can cause delays in the injection molding process of plastic molding machine? 2025/04/23
- Exhibition Review| Topstar participates in InterPlas Thailand 2024 2025/04/23
- Star Case | Topstar helps Santong upgrade its intelligent plant 2025/04/23
- Topstar Special | National Science and Technology Workers Day 2025/04/23
HOT TOPIC
- 3 in 1 Compact Dehumidifying Dryer
- 5-axis CNC machine
- accuracy
- Air Chillers
- all electric injection molding machine
- all electric injection molding machines
- All-electric injection molding machines
- and overall production quality. Therefore
- AP-RubberPlas
- automated injection molding machine
- Automation changed engineering
- automation of injection molding robots
- auxiliary machine
- Bench Injection Molding Machine
- Cabinet dryer manufacturers
- Cabinet dryers
- chiller
- CNC Drilling Machine
- CNC Drilling Machines
- cnc engraving machine manufacturer
- cnc laser cutting machine manufacturer
- CNC machine
- CNC Machine Center
- CNC Machine for Sale
- CNC Machine Manufacturing
- CNC Machine Tool
- CNC machine tool product
- CNC Machining Center
- CNC wood carving machine
- Cooling system
- Cross-Walking Single Axis Servo Cylinder Robot
- Cross-Walking Single-Axis Servo Cylinder Robot
- Cross-Walking Three-Axis/Five-Axis Servo Driven Robot
- cross-walking three-axis/five-axis servo-driven robot
- Dehumidifier Dryer
- Dehumidifying Dryer
- delta parallel robot
- Desktop Injection Molding Machine
- Desktop injection molding machines
- Desktop Molding Machine
- desktop plastic injection machine
- Desktop Plastic Injection Molding Machine
- direct clamp injection molding machine
- Direct clamp injection molding machines
- Dosing & mixing system
- Drilling Centers
- Drying and dehumidification system
- drying and dehumidifying equipment
- Drying and Dehumidifying System
- drying system
- effective and efficient. Cabinet dryers are also used in other industries where large quantities of material need to be dried
- efficient injection molding machine
- elbow hydraulic injection molding machines
- electric injection molding machine
- electric injection molding machines
- energy-saving injection molding machine
- etc. Among injection molding robots
- exhibition
- features of CNC machine
- Feeding And Conveying System
- Five Axis Machine Center
- Fully automatic injection molding machine
- Gathering Topstar
- giant injection molding machine
- GMU-600 5-Axis Machining Center
- Granulating & Recycling System
- Heavy duty injection molding machine
- High-precision electric molding machines
- high-precision plastic molding machines
- Honeycomb rotor dehumidifier
- horizontal injection molding machine
- Horizontal Injection Molding Machines
- Horizontal Injection Moulding Machine
- Horizontal Mixer manufacturer
- How The CNC Machine Works
- hybrid injection molding machine
- hydraulic injection molding machine
- Hydraulic Injection Molding Machines
- in this article
- Industrial robot
- Industrial Robot Chinese brand
- industrial robot parts
- industrial robot supplier
- Industrial robots
- Industry Chain
- Injection Manipulator
- injection manipulator robot
- injection mold machines
- Injection molding
- Injection molding automation
- Injection Molding Automation Solution
- injection molding dryer
- Injection molding equipment
- injection molding hopper dryer
- Injection molding machine
- injection molding machine brand
- Injection Molding Machine Factory
- Injection Molding Machine Manufacture
- Injection molding machine manufacturer
- injection molding machine manufacturers
- Injection molding machine procurement
- injection molding machine robotic arm
- injection molding machine with a robot
- Injection molding machines
- injection molding material dehumidifying
- injection molding plant
- Injection Molding Robot
- injection molding robot arm
- Injection molding robot automation
- Injection molding robotic arm
- injection molding robots
- Injection Moulding Robots
- Injection Robot
- Injection robot arm
- Injection robot manufacturer
- Injection robot wholesale
- injection robots
- intelligent injection molding machines
- Introducing Injection Robot
- It is the best choice for drying large quantities of material at once. Cabinetmakers use these machines because they are fast
- large injection molding machine
- Learn what industrial automation and robotics is
- linear robot
- low speed sound-proof granulator
- machine plastic molding
- make sure to add some! Improvements (2) Keyphrase in introduction: Your keyphrase or its synonyms appear in the first paragraph of the copy
- manipulator machine
- manufacturing
- micro injection molding machine
- middle speed granulator
- Mini CNC machine manufacturers.
- Mold Temperature Control System
- mold temperature controller
- molding material Dehumidifying System
- mould temperature controller
- mould temperature controllers
- New electric injection molding machine
- nitrogen dryer manufacturer
- nitrogen dryer system manufacturer
- Oil type mold temperature controller
- open day
- Outbound links: No outbound links appear in this page. Add some! Images: No images appear on this page. Add some! Internal links: No internal links appear in this page
- PET Preform injection molding
- phone case maker machine
- phone case making machine
- plastic bottle making machine
- plastic bottle manufacturing
- plastic bucket making machine
- plastic bucket manufacturing
- Plastic chair making machine
- plastic forming equipment
- plastic hopper dryer
- plastic injection machine
- plastic injection machines
- plastic injection molding
- Plastic injection molding equipment
- Plastic injection molding machine
- Plastic Injection Molding Machines
- plastic injection robot
- Plastic Molding machine
- Plastic Molding Machines
- plastic molding press
- plastic phone case making machine
- plastic-molding machine
- powerful granulator
- Powerful Type Sound-Proof Granulator
- precision injection molding
- production of plastic seats
- Robot injection molding
- robot injection molding machine
- robot manufacturing companies
- Robotic arm for injection molding machine
- robotic injection molding machines
- robotics in injection molding
- SCARA robot
- SCARA robots
- Service-oriented manufacturing
- Servo Cylinder Robot
- servo driven robot
- Servo Driven Robots
- servo injection robots
- Servo-Driven Robot
- Setup of injection machine
- Silicone Injection Molding Machine
- six-axis industrial robot
- Stainless Hopper Dryer
- Stainless Hopper Dryers
- star club
- swing arm robot
- the choice between servo-driven robots and hydraulic robots will have a certain impact on efficiency
- the most popular injection molding machine
- the type of injection molding robot
- toggle clamp injection molding machine
- Toggle Hydraulic Injection Molding Machines
- toggle injection molding machine
- Top 10 brands of injection robots
- Topstar
- Topstar Engineering
- Topstar Industrial Robots
- Topstar injection molding intelligent
- Topstar Scara Robots
- Useful Injection molding machine
- Vertical machining centers
- volumetric type blender
- water chiller
- water chillers
- water distributor
- Water Type MoldTemperature Controller
- We often face choices when performing injection molding. We will choose the type of injection molding machine
- wholesale of injection molding machines
- x carve CNC