The role of discrete intelligent drive in energy-saving injection molding machine
2025/04/21 By Topstar
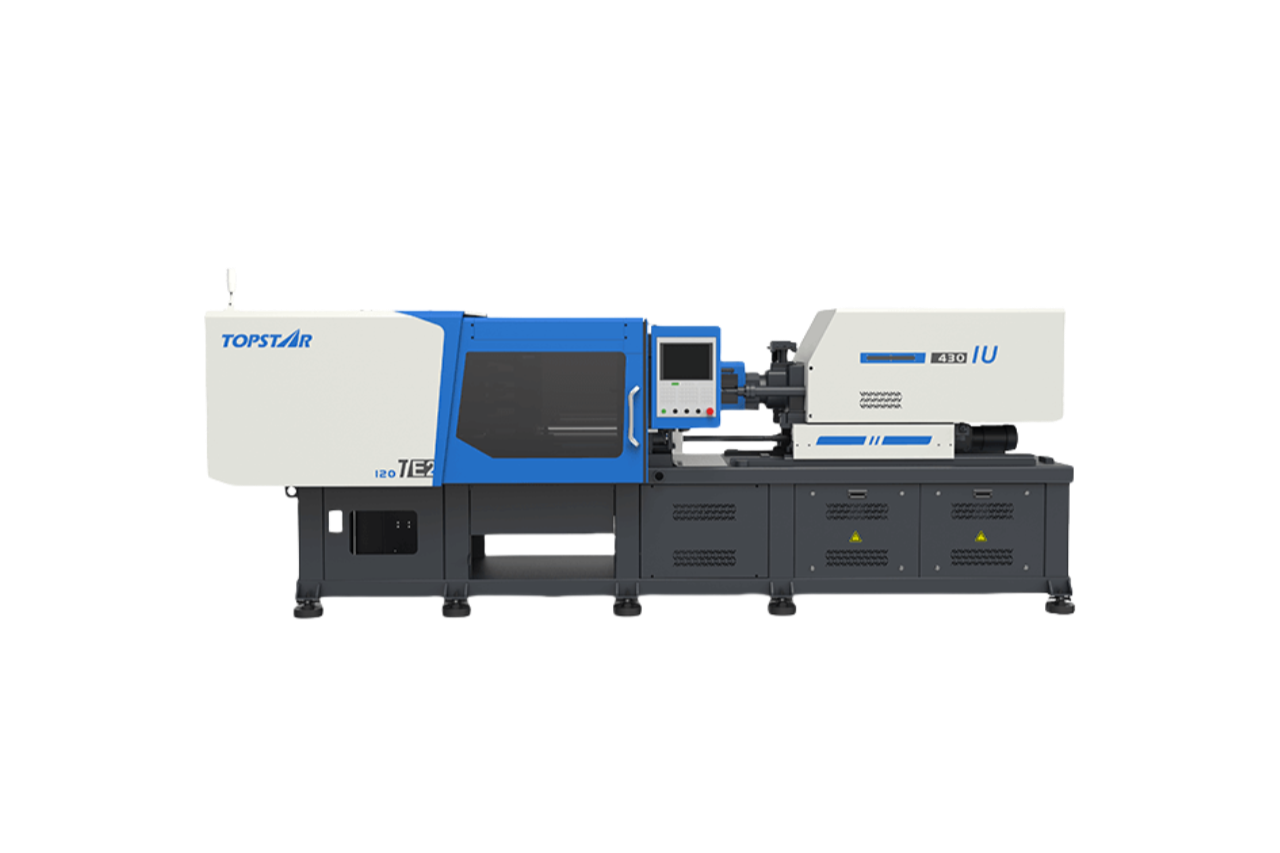
In the current global economic environment, energy efficiency is a primary concern for every manufacturer in the plastics manufacturing industry, especially in some European countries. To make injection molding machines more energy-efficient, Topstar uses discrete intelligent drives in the control system of the energy-saving injection molding machine represented by all electric injection molding machines. This control strategy fundamentally changes how servo motors respond and execute molding cycles. Discrete intelligent drives no longer rely on continuous feedback loops mediated by central controllers; instead, they delegate real-time trajectory generation and motion control directly to servo drives. This architectural shift significantly reduces communication latency, improves speed and accuracy, and makes molding more energy-efficient.
Precise control of energy-saving injection molding machines through decentralized control
Discrete intelligent drives redefine motion control of energy-saving injection molding machines. Unlike traditional centralized systems, they allow drives to operate independently, reducing dependence on continuous communication with the central controller. During the molding cycle, the servo drive generates its operating curve based on preloaded parameters, enabling instant adjustments to position, speed, and pressure. This autonomy eliminates the delay caused by round-trip data transmission and increases response speed by 8 to 16 times. For example, during high-speed clamping or injection phases, the drive can correct deviations immediately without waiting for external commands. The result? Compared to traditional hydraulic systems, smoother operation, tighter tolerances, and up to 30% energy savings.
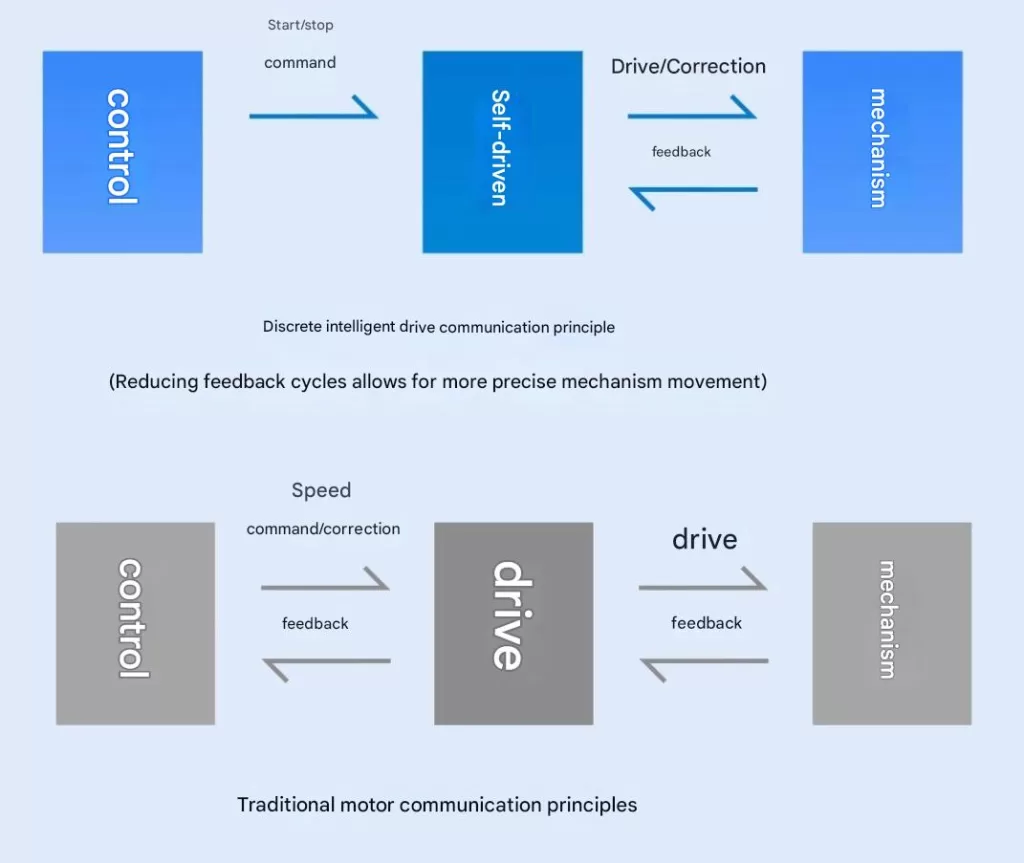
Solving communication delay issues for energy-saving injection molding machines
Traditional control systems have latency issues when transmitting data between the central controller and the servo motor. Discrete intelligent drives solve this problem by storing key parameters, such as mold temperature thresholds or injection pressure limits, directly in their internal memory. Once the initial setup is complete, the drive executes the pre-programmed profile autonomously in every cycle.
For all-electric injection molding machines, this means:
- There is no need to wait for real-time speed instructions from the controller.
- Maintain consistent repeatability over thousands of cycles.
- Eliminate timing mismatches during multi-axis operations.
This approach is particularly effective in high-speed applications such as thin-wall packaging and preform production, where defects caused by microsecond delays can be avoided.
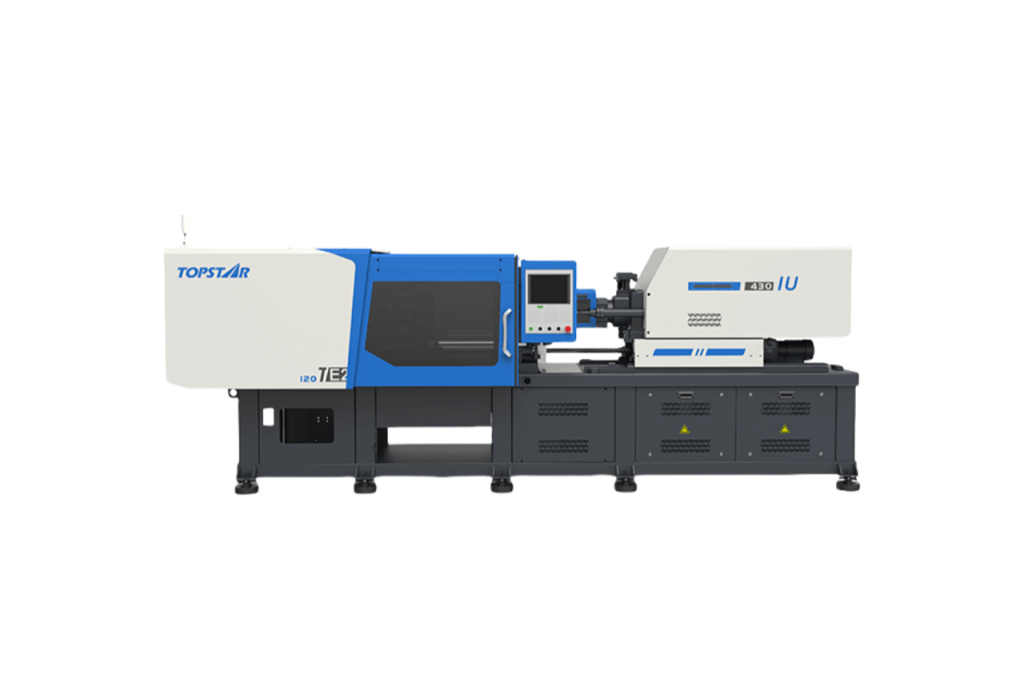
Servo motor real-time control
In a discrete intelligent drive architecture, the servo drive continuously monitors its internal state and executes predefined motion profiles with microsecond accuracy. This decentralized control model enables energy-saving injection molding machines to manage complex movements such as screw reciprocation and injection curves on their own without relying on high-frequency data exchange with the central controller. This makes the system very stable and can respond instantly to minor disturbances, such as changes in material viscosity or slight changes in mold temperature, without waiting for other instructions. With instant decision-making, discrete intelligent drives achieve consistent, high-fidelity servo performance, directly translating into improved part consistency and reduced scrap rates.
The main advantages can be achieved:
- Pressure control accuracy within ±0.5%.
- Position repeatability within 0.01 mm.
- Adaptive material viscosity changes.
When facing engineering plastics with strict cooling requirements for molding, the drive can fine-tune the ejection time without interrupting the workflow of the central controller.
8-16 times faster response speed
Response speed is a key indicator for high-throughput molding operations. Network communication speeds limit traditional centralized drives, and the response time is usually only tens of milliseconds. With discrete intelligent drives, servo controllers can bypass these delays, making the response speed 8 to 16 times faster than traditional settings. This fast response capability enables energy-saving injection molding machines to quickly switch between injection, holding, and pressure holding stages, thereby minimizing cycle time without sacrificing precision. For manufacturers, this means higher productivity and lower energy consumption per unit part because the motor idle time is reduced and production efficiency is higher. At the same time, the enhanced response speed improves the machine’s ability to maintain consistent melt buffer and back pressure, further stabilizing the injection quality.
Intelligent parameter latching to improve cycle efficiency
In discrete intelligent drive systems, parameter latching is key to efficient cycle execution. After the servo drive of the energy-saving injection molding machine receives the set parameters (such as speed segment, dwell time, and pressure set value), it stores these values in its internal latch memory. In each reciprocating cycle, the drive instantly retrieves the latched parameters and dynamically generates the motor speed and torque curve. This eliminates the need for the upper controller to transmit data repeatedly in each cycle, reduces bus traffic, and allows the drive to focus on motion execution. The result is a more streamlined control architecture that speeds up each molding cycle and reduces energy waste associated with unnecessary communication overhead. By simplifying this process, discrete intelligent drives can improve all-electric injection molding machines’ overall availability and throughput.
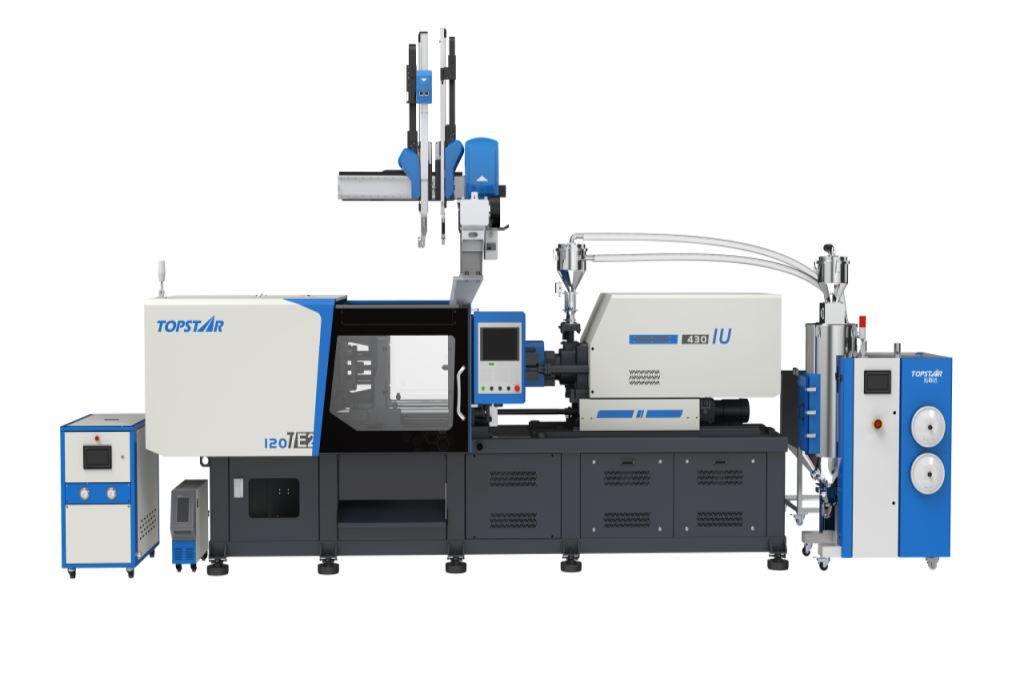
Bring sustainable production benefits.
Using discrete intelligent drive technology on energy-saving injection molding machines such as all-electric and electric injection molding machines can achieve higher precision, faster response time, and significant energy savings. By decentralizing the control logic and authorizing the servo drive to generate its motion profile based on latched parameters, plastic manufacturers can almost eliminate communication delays, increase cycle rates by up to 16 times, enhance the accuracy of position, speed, and pressure control, minimize energy waste, and improve operational efficiency.
TRENDING POSTS
- What factors can cause delays in the injection molding process of plastic molding machine? 2025/04/21
- Exhibition Review| Topstar participates in InterPlas Thailand 2024 2025/04/21
- Star Case | Topstar helps Santong upgrade its intelligent plant 2025/04/21
- Topstar Special | National Science and Technology Workers Day 2025/04/21
HOT TOPIC
- 3 in 1 Compact Dehumidifying Dryer
- 5-axis CNC machine
- accuracy
- Air Chillers
- all electric injection molding machine
- all electric injection molding machines
- All-electric injection molding machines
- and overall production quality. Therefore
- AP-RubberPlas
- automated injection molding machine
- Automation changed engineering
- automation of injection molding robots
- auxiliary machine
- Bench Injection Molding Machine
- Cabinet dryer manufacturers
- Cabinet dryers
- chiller
- CNC Drilling Machine
- CNC Drilling Machines
- cnc engraving machine manufacturer
- cnc laser cutting machine manufacturer
- CNC machine
- CNC Machine Center
- CNC Machine for Sale
- CNC Machine Manufacturing
- CNC Machine Tool
- CNC machine tool product
- CNC Machining Center
- CNC wood carving machine
- Cooling system
- Cross-Walking Single Axis Servo Cylinder Robot
- Cross-Walking Single-Axis Servo Cylinder Robot
- Cross-Walking Three-Axis/Five-Axis Servo Driven Robot
- cross-walking three-axis/five-axis servo-driven robot
- Dehumidifier Dryer
- Dehumidifying Dryer
- delta parallel robot
- Desktop Injection Molding Machine
- Desktop injection molding machines
- Desktop Molding Machine
- desktop plastic injection machine
- Desktop Plastic Injection Molding Machine
- direct clamp injection molding machine
- Direct clamp injection molding machines
- Dosing & mixing system
- Drilling Centers
- Drying and dehumidification system
- drying and dehumidifying equipment
- Drying and Dehumidifying System
- drying system
- effective and efficient. Cabinet dryers are also used in other industries where large quantities of material need to be dried
- efficient injection molding machine
- elbow hydraulic injection molding machines
- electric injection molding machine
- electric injection molding machines
- energy-saving injection molding machine
- etc. Among injection molding robots
- exhibition
- features of CNC machine
- Feeding And Conveying System
- Five Axis Machine Center
- Fully automatic injection molding machine
- Gathering Topstar
- giant injection molding machine
- GMU-600 5-Axis Machining Center
- Granulating & Recycling System
- Heavy duty injection molding machine
- Honeycomb rotor dehumidifier
- horizontal injection molding machine
- Horizontal Injection Molding Machines
- Horizontal Injection Moulding Machine
- Horizontal Mixer manufacturer
- How The CNC Machine Works
- hybrid injection molding machine
- hydraulic injection molding machine
- Hydraulic Injection Molding Machines
- in this article
- Industrial robot
- Industrial Robot Chinese brand
- industrial robot parts
- industrial robot supplier
- Industrial robots
- Industry Chain
- Injection Manipulator
- injection mold machines
- Injection molding
- Injection molding automation
- Injection Molding Automation Solution
- injection molding dryer
- Injection molding equipment
- injection molding hopper dryer
- Injection molding machine
- injection molding machine brand
- Injection Molding Machine Factory
- Injection Molding Machine Manufacture
- Injection molding machine manufacturer
- injection molding machine manufacturers
- Injection molding machine procurement
- injection molding machine robotic arm
- injection molding machine with a robot
- Injection molding machines
- injection molding material dehumidifying
- injection molding plant
- Injection Molding Robot
- injection molding robot arm
- Injection molding robot automation
- Injection molding robotic arm
- injection molding robots
- Injection Moulding Robots
- Injection Robot
- Injection robot arm
- Injection robot manufacturer
- Injection robot wholesale
- injection robots
- intelligent injection molding machines
- Introducing Injection Robot
- It is the best choice for drying large quantities of material at once. Cabinetmakers use these machines because they are fast
- large injection molding machine
- Learn what industrial automation and robotics is
- low speed sound-proof granulator
- machine plastic molding
- make sure to add some! Improvements (2) Keyphrase in introduction: Your keyphrase or its synonyms appear in the first paragraph of the copy
- manipulator machine
- manufacturing
- micro injection molding machine
- middle speed granulator
- Mini CNC machine manufacturers.
- Mold Temperature Control System
- mold temperature controller
- molding material Dehumidifying System
- mould temperature controller
- mould temperature controllers
- New electric injection molding machine
- nitrogen dryer manufacturer
- nitrogen dryer system manufacturer
- Oil type mold temperature controller
- open day
- Outbound links: No outbound links appear in this page. Add some! Images: No images appear on this page. Add some! Internal links: No internal links appear in this page
- PET Preform injection molding
- phone case maker machine
- phone case making machine
- plastic bottle making machine
- plastic bottle manufacturing
- plastic bucket making machine
- plastic bucket manufacturing
- Plastic chair making machine
- plastic forming equipment
- plastic hopper dryer
- plastic injection machine
- plastic injection machines
- plastic injection molding
- Plastic injection molding equipment
- Plastic injection molding machine
- Plastic Injection Molding Machines
- plastic injection robot
- Plastic Molding machine
- Plastic Molding Machines
- plastic molding press
- plastic phone case making machine
- plastic-molding machine
- powerful granulator
- Powerful Type Sound-Proof Granulator
- production of plastic seats
- Robot injection molding
- robot injection molding machine
- robot manufacturing companies
- Robotic arm for injection molding machine
- robotic injection molding machines
- robotics in injection molding
- SCARA robot
- SCARA robots
- Service-oriented manufacturing
- Servo Cylinder Robot
- servo driven robot
- Servo Driven Robots
- servo injection robots
- Servo-Driven Robot
- Setup of injection machine
- Silicone Injection Molding Machine
- six-axis industrial robot
- Stainless Hopper Dryer
- Stainless Hopper Dryers
- star club
- swing arm robot
- the choice between servo-driven robots and hydraulic robots will have a certain impact on efficiency
- the most popular injection molding machine
- the type of injection molding robot
- toggle clamp injection molding machine
- Toggle Hydraulic Injection Molding Machines
- toggle injection molding machine
- Top 10 brands of injection robots
- Topstar
- Topstar Engineering
- Topstar Industrial Robots
- Topstar injection molding intelligent
- Topstar Scara Robots
- Useful Injection molding machine
- Vertical machining centers
- volumetric type blender
- water chiller
- water chillers
- water distributor
- Water Type MoldTemperature Controller
- We often face choices when performing injection molding. We will choose the type of injection molding machine
- wholesale of injection molding machines
- x carve CNC