Solving Pick and Place Challenges for North American Manufacturer Using Injection Molding Robots
2025/04/18 By Topstar
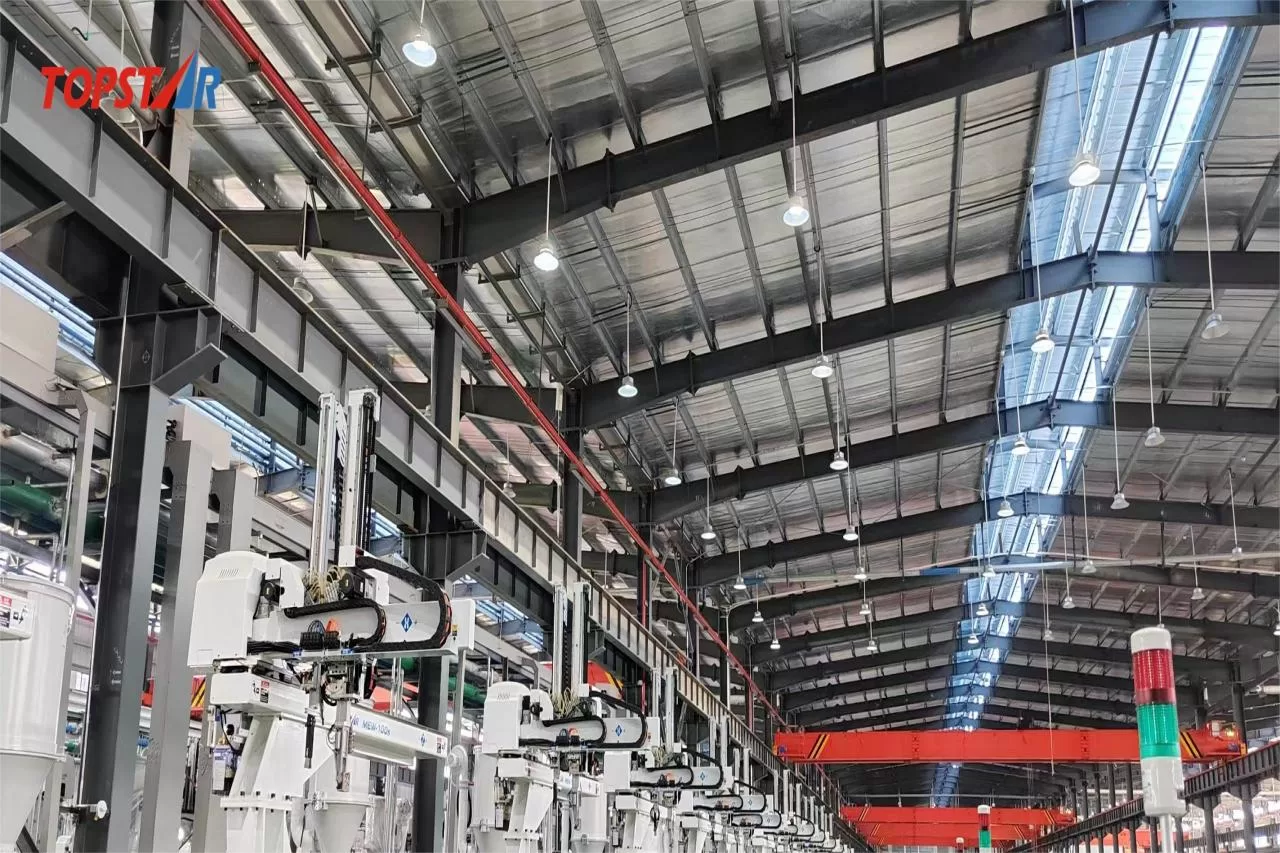
Most North American plastics manufacturers need highly automated, precise, and flexible injection molding robots, especially in the injection molding pick-and-place process in the automotive, medical, and packaging industries. At the same time, the quality requirements for finished products are very high, requiring robots to move quickly and repeat accurately when picking up parts, avoiding deformation or damage, and ensuring that the plastic parts taken out are defect-free. In addition, to adapt to the production environment of frequent mold and product changes, North American customers prefer modular, quickly deployable, and flexibly programmable robot systems, as well as sustainable development in the North American manufacturing environment, energy saving, and compliance with ANSI, OSHA, UL, and other safety standards.
Achieving seamless automation integration of injection molding robots
One of the primary requirements of North American plastics manufacturers is a high degree of automation, which can realize unmanned and less-manned production lines. Topstar’s injection molding robot is directly connected to injection molding machines, material conveyors, and downstream packaging lines through the integration of self-developed control systems.
The most important thing is:
The self-developed control platform can synchronize the robot signal with the mold cycle. Engineers embed communication protocols, such as MODBUS RTU, in the injection molding machine and robot controller to enable real-time data exchange and motion coordination.
After the injection molding robot receives the “injection completed” signal, it automatically adjusts the motion trajectory and immediately starts the pick and place task. This integrated linkage minimizes cycle gaps, reduces abnormal alarms, and ensures a continuous production process, which improves overall equipment efficiency (OEE) and reduces labor costs.

How can injection molding robots be ensured of high precision and fast response?
North American manufacturers require impeccable part quality, which depends on the ability of injection molding robots to pick and place components with high repeatability and speed. Accurately ±0.1 mm or higher is critical to avoid product deformation, flash, or scrap.
How Topstar meets it:
- These requirements are met through advanced motion control algorithms such as contour mode control, which optimizes acceleration and deceleration curves for smooth trajectories.
- The gear rack meshing transmission, both before and after the injection molding robot, ensures excellent positioning accuracy.
- Built-in vibration suppression function can further improve the robot’s stability in plug-in molding and other high-precision tasks.
Together, these features enable the robot to synchronize precisely with the mold opening, achieving consistent processing of precision parts at high cycle rates and ensuring a defect-free output.
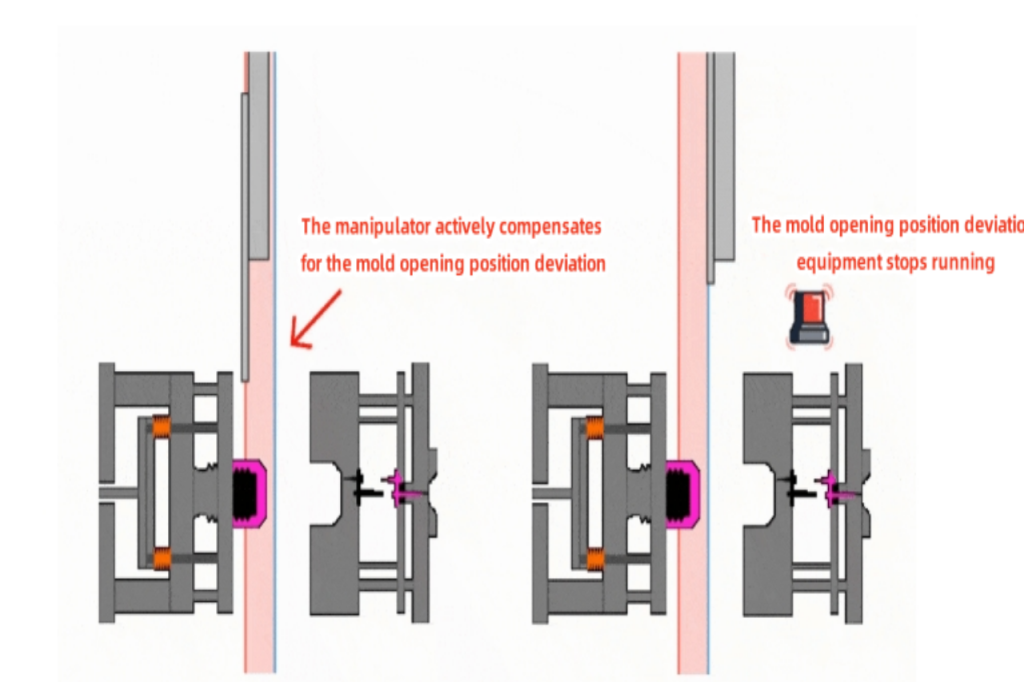
Improve energy efficiency and safety compliance.
Many manufacturing industries in North America value energy efficiency, sustainability, and safety. Therefore, injection molding robots must have energy-saving drive systems and powerful safety mechanisms. Topstar uses universal DC bus technology based on a five-in-one servo drive system to reduce energy waste during deceleration and power regeneration. This innovation can save up to 10% of energy and lower electricity bills accordingly. At the same time, Topstar’s “servo automatic shutdown” function puts the drive in standby mode when idle, further reducing power consumption by 10%.
In terms of safety:
- Equipped with manipulator protection technology (joint soft floating), it can improve the protection ability of the injection molding manipulator when facing a torque exceeding the set torque, effectively reduce potential damage to customer molds, injection molding machine ejectors, and products, and further improve production efficiency and equipment stability.
- Optional “personnel protection configuration” can reduce the risk of accidental injury due to unintentional contact with the running manipulator.
Modular design brings flexibility
Given the frequent changes in molds and products in North American manufacturing, injection molding robots must support rapid reconfiguration so that production lines can quickly switch between different parts or tools. Topstar’s modular robot system uses plug-and-play axes and standardized mounting brackets that engineers can reprogram in minutes. Each robot features a dual control system architecture, which enables seamless integration with various IT environments. In addition, with a reusable motion sequence library and a quick-change end-of-tool (EOAT) fixture, manufacturers can minimize downtime, change molds or products, maximize production line uptime, and meet tight production schedules.
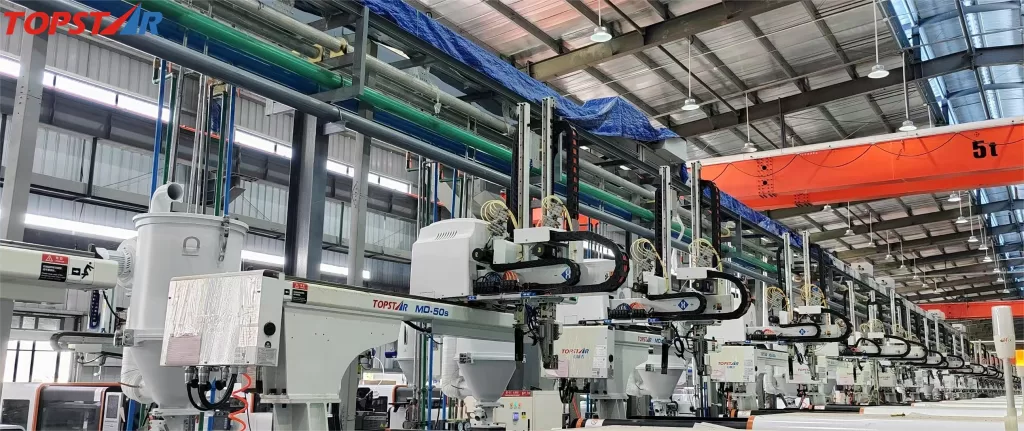
Enable remote monitoring and predictive maintenance.
Downtime is the biggest challenge and the least desired in modern manufacturing. Injection molding robots with remote monitoring and predictive maintenance functions can significantly reduce unplanned downtime. Topstar’s injection molding robots allow users to obtain operating data directly on the injection molding machine under the same control system, which is more convenient to operate and can capture data such as vibration, temperature, number of cycles, and power consumption in real time. The system transmits these data to the control panel of the injection molding machine to identify abnormal conditions and trigger automatic alarms. In addition, users can access the Topstar MES system and IOT digital platform through the reserved expansion interface. Various terminals can then monitor the automated removal process in real time and optimize it promptly to realize information management.
Enhance the competitive advantage of North American injection molding manufacturers
The key to solving the pick-and-place challenges faced by North American plastic manufacturers is to deploy injection molding robots that combine seamless integration, high precision, energy saving, flexibility, and robust remote monitoring capabilities. Topstar’s injection molding robots use a self-developed control system, a five-in-one servo drive, contour mode control, vibration suppression, and comprehensive safety and energy-saving functions to provide reliable and scalable automation solutions. By adopting these technologies, North American manufacturers can achieve unmanned or minimally manned production lines, quickly adapt to changing needs, and maintain the highest quality and sustainability standards.
TRENDING POSTS
- What factors can cause delays in the injection molding process of plastic molding machine? 2025/04/18
- Exhibition Review| Topstar participates in InterPlas Thailand 2024 2025/04/18
- Star Case | Topstar helps Santong upgrade its intelligent plant 2025/04/18
- Topstar Special | National Science and Technology Workers Day 2025/04/18
HOT TOPIC
- 3 in 1 Compact Dehumidifying Dryer
- 5-axis CNC machine
- accuracy
- Air Chillers
- all electric injection molding machine
- All-electric injection molding machines
- and overall production quality. Therefore
- AP-RubberPlas
- automated injection molding machine
- Automation changed engineering
- automation of injection molding robots
- auxiliary machine
- Bench Injection Molding Machine
- Cabinet dryer manufacturers
- Cabinet dryers
- chiller
- CNC Drilling Machine
- CNC Drilling Machines
- cnc engraving machine manufacturer
- cnc laser cutting machine manufacturer
- CNC machine
- CNC Machine Center
- CNC Machine for Sale
- CNC Machine Manufacturing
- CNC Machine Tool
- CNC machine tool product
- CNC Machining Center
- CNC wood carving machine
- Cooling system
- Cross-Walking Single Axis Servo Cylinder Robot
- Cross-Walking Single-Axis Servo Cylinder Robot
- Cross-Walking Three-Axis/Five-Axis Servo Driven Robot
- cross-walking three-axis/five-axis servo-driven robot
- Dehumidifier Dryer
- Dehumidifying Dryer
- delta parallel robot
- Desktop Injection Molding Machine
- Desktop injection molding machines
- Desktop Molding Machine
- desktop plastic injection machine
- Desktop Plastic Injection Molding Machine
- direct clamp injection molding machine
- Direct clamp injection molding machines
- Dosing & mixing system
- Drilling Centers
- Drying and dehumidification system
- drying and dehumidifying equipment
- Drying and Dehumidifying System
- drying system
- effective and efficient. Cabinet dryers are also used in other industries where large quantities of material need to be dried
- efficient injection molding machine
- elbow hydraulic injection molding machines
- electric injection molding machine
- electric injection molding machines
- etc. Among injection molding robots
- exhibition
- features of CNC machine
- Feeding And Conveying System
- Five Axis Machine Center
- Fully automatic injection molding machine
- Gathering Topstar
- giant injection molding machine
- GMU-600 5-Axis Machining Center
- Granulating & Recycling System
- Heavy duty injection molding machine
- Honeycomb rotor dehumidifier
- horizontal injection molding machine
- Horizontal Injection Molding Machines
- Horizontal Injection Moulding Machine
- Horizontal Mixer manufacturer
- How The CNC Machine Works
- hybrid injection molding machine
- hydraulic injection molding machine
- Hydraulic Injection Molding Machines
- in this article
- Industrial robot
- Industrial Robot Chinese brand
- industrial robot parts
- industrial robot supplier
- Industrial robots
- Industry Chain
- Injection Manipulator
- injection mold machines
- Injection molding
- Injection molding automation
- Injection Molding Automation Solution
- injection molding dryer
- Injection molding equipment
- injection molding hopper dryer
- Injection molding machine
- injection molding machine brand
- Injection Molding Machine Factory
- Injection Molding Machine Manufacture
- Injection molding machine manufacturer
- injection molding machine manufacturers
- Injection molding machine procurement
- injection molding machine robotic arm
- injection molding machine with a robot
- Injection molding machines
- injection molding material dehumidifying
- injection molding plant
- Injection Molding Robot
- injection molding robot arm
- Injection molding robot automation
- Injection molding robotic arm
- injection molding robots
- Injection Moulding Robots
- Injection Robot
- Injection robot arm
- Injection robot manufacturer
- Injection robot wholesale
- injection robots
- intelligent injection molding machines
- Introducing Injection Robot
- It is the best choice for drying large quantities of material at once. Cabinetmakers use these machines because they are fast
- large injection molding machine
- Learn what industrial automation and robotics is
- low speed sound-proof granulator
- machine plastic molding
- make sure to add some! Improvements (2) Keyphrase in introduction: Your keyphrase or its synonyms appear in the first paragraph of the copy
- manipulator machine
- manufacturing
- micro injection molding machine
- middle speed granulator
- Mini CNC machine manufacturers.
- Mold Temperature Control System
- mold temperature controller
- molding material Dehumidifying System
- mould temperature controller
- mould temperature controllers
- New electric injection molding machine
- nitrogen dryer manufacturer
- nitrogen dryer system manufacturer
- Oil type mold temperature controller
- open day
- Outbound links: No outbound links appear in this page. Add some! Images: No images appear on this page. Add some! Internal links: No internal links appear in this page
- PET Preform injection molding
- phone case maker machine
- phone case making machine
- plastic bottle making machine
- plastic bottle manufacturing
- plastic bucket making machine
- plastic bucket manufacturing
- Plastic chair making machine
- plastic forming equipment
- plastic hopper dryer
- plastic injection machine
- plastic injection machines
- plastic injection molding
- Plastic injection molding equipment
- Plastic injection molding machine
- Plastic Injection Molding Machines
- plastic injection robot
- Plastic Molding machine
- Plastic Molding Machines
- plastic molding press
- plastic phone case making machine
- plastic-molding machine
- powerful granulator
- Powerful Type Sound-Proof Granulator
- production of plastic seats
- Robot injection molding
- robot injection molding machine
- robot manufacturing companies
- Robotic arm for injection molding machine
- robotic injection molding machines
- robotics in injection molding
- SCARA robot
- SCARA robots
- Service-oriented manufacturing
- Servo Cylinder Robot
- servo driven robot
- Servo Driven Robots
- servo injection robots
- Servo-Driven Robot
- Setup of injection machine
- Silicone Injection Molding Machine
- six-axis industrial robot
- Stainless Hopper Dryer
- Stainless Hopper Dryers
- star club
- swing arm robot
- the choice between servo-driven robots and hydraulic robots will have a certain impact on efficiency
- the most popular injection molding machine
- the type of injection molding robot
- toggle clamp injection molding machine
- Toggle Hydraulic Injection Molding Machines
- toggle injection molding machine
- Top 10 brands of injection robots
- Topstar
- Topstar Engineering
- Topstar Industrial Robots
- Topstar injection molding intelligent
- Topstar Scara Robots
- Useful Injection molding machine
- Vertical machining centers
- volumetric type blender
- water chiller
- water chillers
- water distributor
- Water Type MoldTemperature Controller
- We often face choices when performing injection molding. We will choose the type of injection molding machine
- wholesale of injection molding machines
- x carve CNC