How do I troubleshoot a temperature sensor failure in a mold temperature controller?
2025/04/07 By Topstar
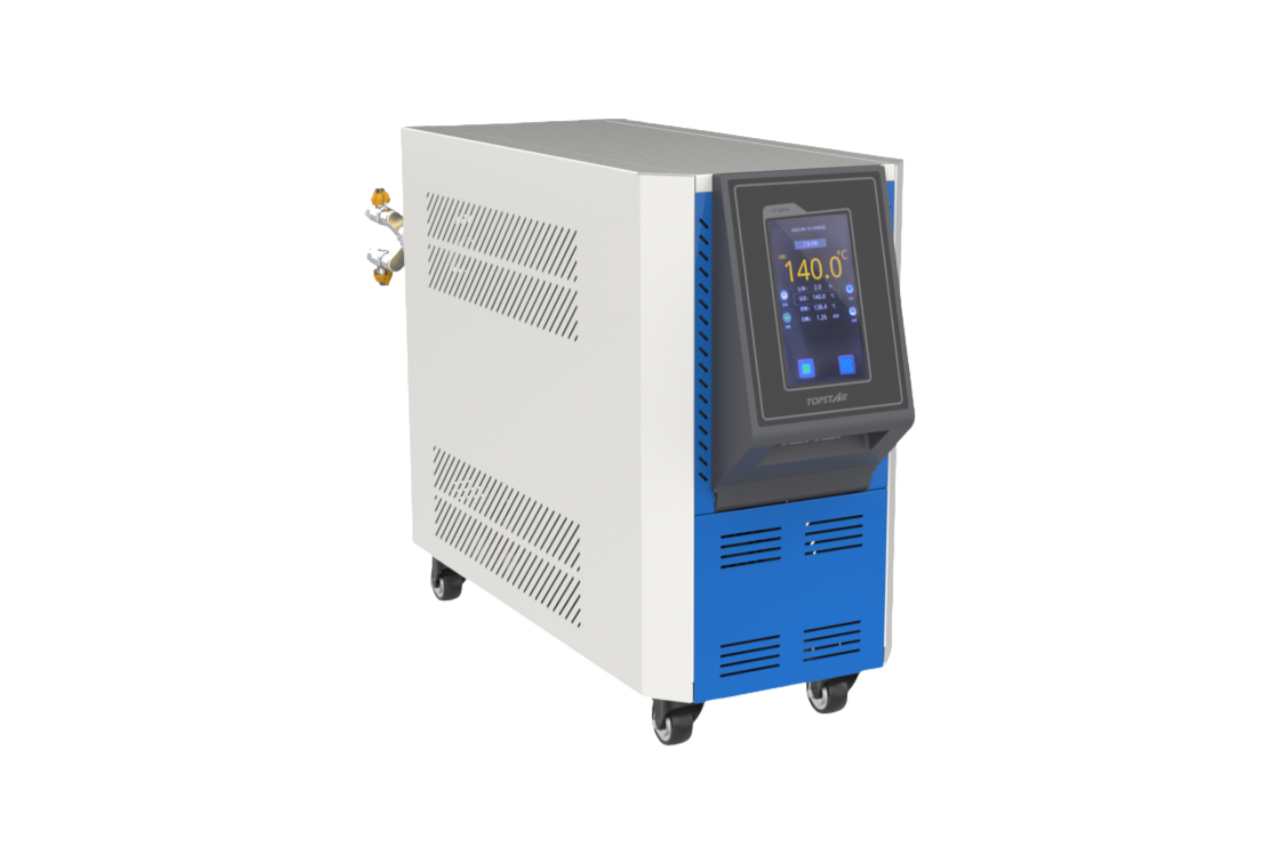
The mold temperature controller is the core of maintaining a stable and efficient injection molding process. Its temperature sensors monitor and report real-time data to the controller, allowing the controller to adjust the heating and cooling systems accordingly. However, when a temperature sensor fails, the feedback loop is interrupted, and the mold temperature control system may no longer maintain the desired set point. Troubleshooting such failures requires a systematic approach, starting with essential inspections and working up to more advanced diagnostics. To better help mold temperature controller users, we will bring you the key steps required for temperature sensor failure in this guide, including checking the wiring and connecting to diagnostic tools.
Functions and failure modes of mold temperature controller sensors
The mold temperature controller relies on sensors to accurately measure the mold temperature and transmit it to the controller’s processing unit. When the sensor is working correctly, the controller adjusts the heating or cooling element to maintain a stable temperature, thereby ensuring the quality of the molded part. However, during the use of the sensor, it may fail for various reasons. Standard failure modes include physical damage caused by wear or accidental impact, contamination caused by process fluids or debris, and electrical problems. In addition, environmental factors such as overheating or vibration can also accelerate the degradation of the sensor. Of course, the sensor’s accuracy will decrease with the increase in usage time, resulting in erroneous readings.
Understanding these failure modes is the first step in troubleshooting. If the sensor shows erratic or no readings, it could indicate a broken wire or a detached sensor element. Similarly, if the sensor consistently reports temperatures that differ significantly from the mold temperature, it could be a calibration issue. In our experience, many sensor failures in mold temperature controllers are related to electrical problems or environmental stresses rather than fundamental design flaws.
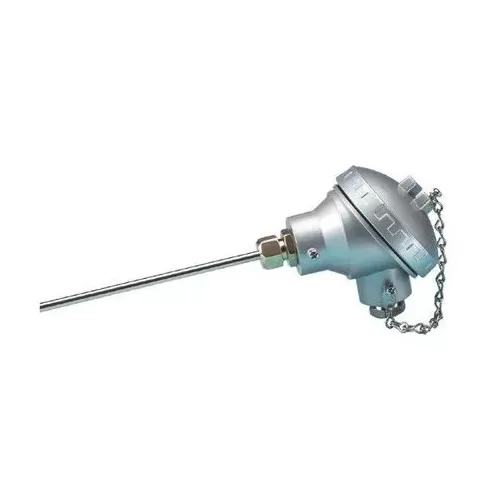
Initial Troubleshooting Steps and Inspection Procedures
When a temperature sensor in a mold temperature controller fails, the first step is to visually and physically inspect the sensor and its associated wiring.
Start by turning off the power. A visual inspection can reveal signs of damage, such as frayed or broken wires, loose connections, or corrosion on the sensor terminals. In many cases, simple problems cause sensor failures.
Next, check the wiring harness connected to the temperature sensor. Another common cause of sensor failure is a poor connection due to loose or oxidized contacts. Use a multimeter to test the continuity of the wiring to ensure there are no breaks or shorts. Also, check the sensor itself for any physical damage. Sensors subjected to mechanical stress or shock may have damaged probes and not provide accurate readings.
After visually inspecting the wiring and sensor, the next step is to verify the sensor’s calibration. Topstar’s mold temperature controllers all come with built-in calibration capabilities. You can consult the user manual or an engineer for the correct calibration procedure and use a reliable temperature source to verify that the sensor readings match the actual temperature.
Use diagnostic tools and techniques for troubleshooting.
If the initial inspection and basic troubleshooting do not solve the problem, it is time to use advanced diagnostic tools and techniques to pinpoint the exact cause of the mold temperature controller’s temperature sensor failure. Specialized equipment such as oscilloscopes and data loggers can better understand the sensor’s performance under operating conditions, allowing you to detect subtle problems that may not be discovered in a simple visual inspection.
Engineers can use oscilloscopes to analyze the electrical signals generated by temperature sensors. Connecting the sensor’s output to an oscilloscope lets you observe the waveform and verify that it is within the expected range. On the other hand, data loggers can record temperature readings over a more extended period, providing a historical view of the sensor’s performance. This is particularly useful for identifying intermittent problems that only occur under specific conditions.
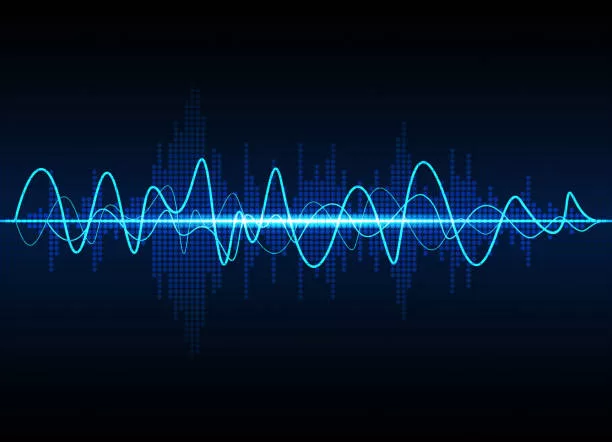
Thermal imaging cameras identify hot spots or areas where the sensor may face abnormal thermal stress by visualizing the temperature distribution of the mold and the sensor itself. Using some diagnostic tools, you can diagnose deeper problems.
Preventive Maintenance and Long-Term Reliability Strategies
A regular maintenance program helps detect potential problems before they escalate into sensor failures, minimizing downtime and ensuring smooth production line operation. We recommend a preventive maintenance program that includes routine inspections, calibration checks, and timely replacement of components that show signs of wear. By proactively addressing minor issues, you can extend the life of the temperature sensor and the entire temperature controller. A schedule for regular inspections of the temperature sensor and its wiring can be established as appropriate, requiring operators to perform regular visual inspections to identify any signs of physical damage, corrosion, or loose connections. At the same time, regularly recalibrating the sensor ensures that its readings remain accurate over time.
Troubleshooting and Ensuring Stable Temperature Controller Operation
Troubleshooting temperature sensor failures in mold temperature controllers is a critical process that requires a structured and systematic approach. By understanding the function of the temperature controller sensor, performing preliminary inspections, utilizing diagnostic tools, and best practices for replacement and calibration, sensor failures can be effectively resolved and optimal production performance restored. Of course, it is equally important to perform preventive maintenance and continuous monitoring to ensure long-term reliability and continued operation of the injection molding process.
TRENDING POSTS
- What factors can cause delays in the injection molding process of plastic molding machine? 2025/04/07
- Exhibition Review| Topstar participates in InterPlas Thailand 2024 2025/04/07
- Star Case | Topstar helps Santong upgrade its intelligent plant 2025/04/07
- Topstar Special | National Science and Technology Workers Day 2025/04/07
HOT TOPIC
- 3 in 1 Compact Dehumidifying Dryer
- 5-axis CNC machine
- accuracy
- Air Chillers
- all electric injection molding machine
- All-electric injection molding machines
- and overall production quality. Therefore
- AP-RubberPlas
- automated injection molding machine
- Automation changed engineering
- automation of injection molding robots
- auxiliary machine
- Bench Injection Molding Machine
- Cabinet dryer manufacturers
- Cabinet dryers
- chiller
- CNC Drilling Machine
- CNC Drilling Machines
- cnc engraving machine manufacturer
- cnc laser cutting machine manufacturer
- CNC machine
- CNC Machine Center
- CNC Machine for Sale
- CNC Machine Manufacturing
- CNC Machine Tool
- CNC machine tool product
- CNC Machining Center
- CNC wood carving machine
- Cooling system
- Cross-Walking Single Axis Servo Cylinder Robot
- Cross-Walking Single-Axis Servo Cylinder Robot
- Cross-Walking Three-Axis/Five-Axis Servo Driven Robot
- cross-walking three-axis/five-axis servo-driven robot
- Dehumidifier Dryer
- Dehumidifying Dryer
- delta parallel robot
- Desktop Injection Molding Machine
- Desktop injection molding machines
- Desktop Molding Machine
- desktop plastic injection machine
- Desktop Plastic Injection Molding Machine
- direct clamp injection molding machine
- Direct clamp injection molding machines
- Dosing & mixing system
- Drilling Centers
- Drying and dehumidification system
- drying and dehumidifying equipment
- Drying and Dehumidifying System
- drying system
- effective and efficient. Cabinet dryers are also used in other industries where large quantities of material need to be dried
- efficient injection molding machine
- elbow hydraulic injection molding machines
- electric injection molding machine
- electric injection molding machines
- etc. Among injection molding robots
- exhibition
- features of CNC machine
- Feeding And Conveying System
- Five Axis Machine Center
- Fully automatic injection molding machine
- Gathering Topstar
- giant injection molding machine
- GMU-600 5-Axis Machining Center
- Granulating & Recycling System
- Heavy duty injection molding machine
- Honeycomb rotor dehumidifier
- horizontal injection molding machine
- Horizontal Injection Molding Machines
- Horizontal Injection Moulding Machine
- Horizontal Mixer manufacturer
- How The CNC Machine Works
- hybrid injection molding machine
- hydraulic injection molding machine
- Hydraulic Injection Molding Machines
- in this article
- Industrial robot
- Industrial Robot Chinese brand
- industrial robot parts
- industrial robot supplier
- Industrial robots
- Industry Chain
- Injection Manipulator
- injection mold machines
- Injection molding
- Injection molding automation
- Injection Molding Automation Solution
- injection molding dryer
- Injection molding equipment
- injection molding hopper dryer
- Injection molding machine
- injection molding machine brand
- Injection Molding Machine Factory
- Injection Molding Machine Manufacture
- Injection molding machine manufacturer
- injection molding machine manufacturers
- Injection molding machine procurement
- injection molding machine robotic arm
- injection molding machine with a robot
- Injection molding machines
- injection molding material dehumidifying
- injection molding plant
- Injection Molding Robot
- injection molding robot arm
- Injection molding robot automation
- Injection molding robotic arm
- injection molding robots
- Injection Moulding Robots
- Injection Robot
- Injection robot arm
- Injection robot manufacturer
- Injection robot wholesale
- injection robots
- intelligent injection molding machines
- Introducing Injection Robot
- It is the best choice for drying large quantities of material at once. Cabinetmakers use these machines because they are fast
- large injection molding machine
- Learn what industrial automation and robotics is
- low speed sound-proof granulator
- machine plastic molding
- make sure to add some! Improvements (2) Keyphrase in introduction: Your keyphrase or its synonyms appear in the first paragraph of the copy
- manipulator machine
- manufacturing
- micro injection molding machine
- middle speed granulator
- Mini CNC machine manufacturers.
- Mold Temperature Control System
- mold temperature controller
- molding material Dehumidifying System
- mould temperature controller
- mould temperature controllers
- New electric injection molding machine
- nitrogen dryer manufacturer
- nitrogen dryer system manufacturer
- Oil type mold temperature controller
- open day
- Outbound links: No outbound links appear in this page. Add some! Images: No images appear on this page. Add some! Internal links: No internal links appear in this page
- PET Preform injection molding
- phone case maker machine
- phone case making machine
- plastic bottle making machine
- plastic bottle manufacturing
- plastic bucket making machine
- plastic bucket manufacturing
- Plastic chair making machine
- plastic forming equipment
- plastic hopper dryer
- plastic injection machine
- plastic injection machines
- plastic injection molding
- Plastic injection molding equipment
- Plastic injection molding machine
- Plastic Injection Molding Machines
- plastic injection robot
- Plastic Molding machine
- Plastic Molding Machines
- plastic molding press
- plastic phone case making machine
- plastic-molding machine
- powerful granulator
- Powerful Type Sound-Proof Granulator
- production of plastic seats
- Robot injection molding
- robot injection molding machine
- robot manufacturing companies
- Robotic arm for injection molding machine
- robotic injection molding machines
- robotics in injection molding
- SCARA robot
- SCARA robots
- Service-oriented manufacturing
- Servo Cylinder Robot
- servo driven robot
- Servo Driven Robots
- servo injection robots
- Servo-Driven Robot
- Setup of injection machine
- Silicone Injection Molding Machine
- six-axis industrial robot
- Stainless Hopper Dryer
- Stainless Hopper Dryers
- star club
- swing arm robot
- the choice between servo-driven robots and hydraulic robots will have a certain impact on efficiency
- the most popular injection molding machine
- the type of injection molding robot
- toggle clamp injection molding machine
- Toggle Hydraulic Injection Molding Machines
- toggle injection molding machine
- Top 10 brands of injection robots
- Topstar
- Topstar Engineering
- Topstar Industrial Robots
- Topstar injection molding intelligent
- Topstar Scara Robots
- Useful Injection molding machine
- Vertical machining centers
- volumetric type blender
- water chiller
- water chillers
- water distributor
- Water Type MoldTemperature Controller
- We often face choices when performing injection molding. We will choose the type of injection molding machine
- wholesale of injection molding machines
- x carve CNC