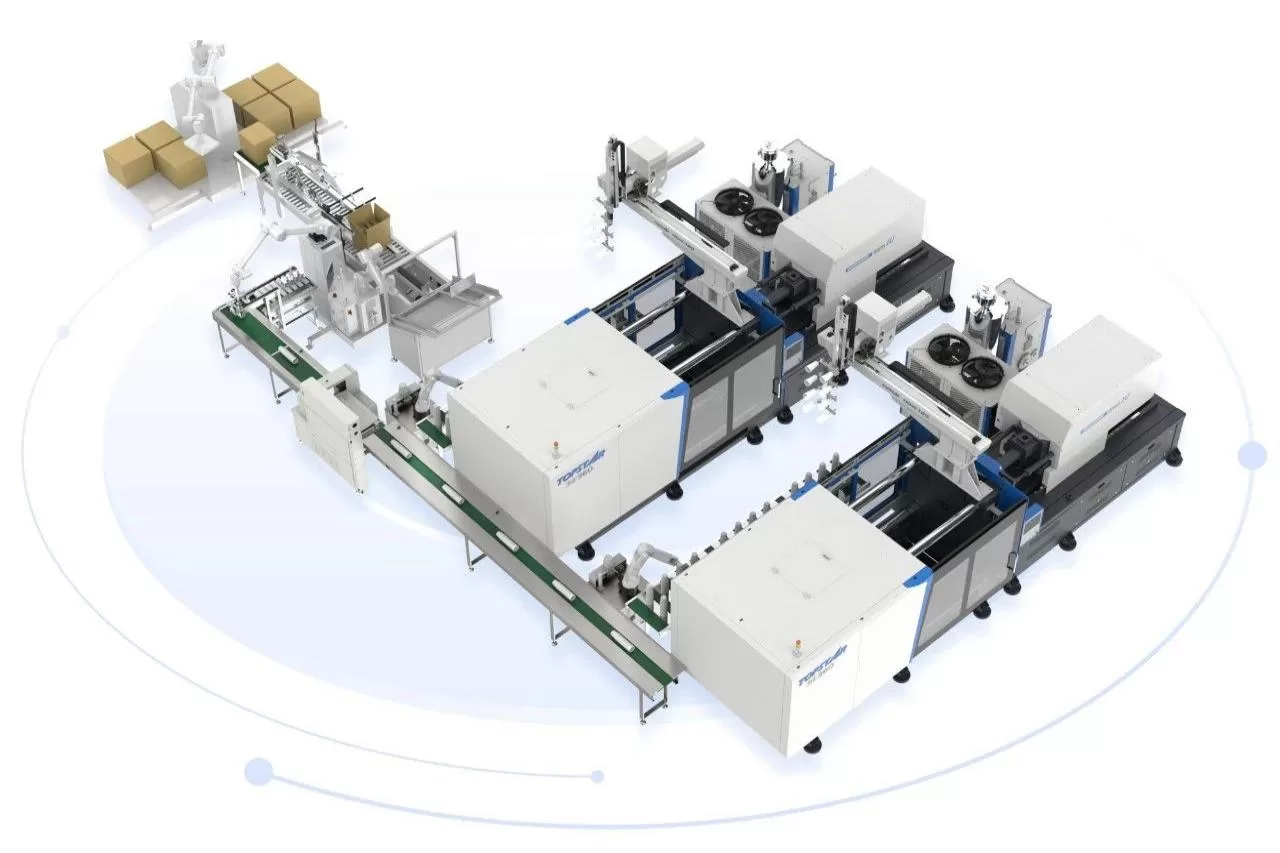
Topstar’s one-stop injection molding solution integrates multiple processes such as injection molding, material stacking, bagging and packaging, labeling, unpacking and boxing, sealing, and intelligent palletizing workstations into a cohesive production system. The system’s core is to use advanced automation technology, especially the automatic adjustment of the injection molding robot trajectory, to ensure continuous production. By controlling the equipment status in real-time and reducing the average failure response time to less than 2 hours, Topstar’s approach can minimize production delays and maximize uptime. The one-stop injection molding machine solution not only supports remote operation, but also allows for rapid troubleshooting and maintenance, which is critical in modern high-speed intelligent manufacturing environments, making users smarter, more agile, and more cost-effective in production.
High-speed injection molding machines improve production efficiency.
In the one-stop injection molding machine solution, taking the production of milk tea cups using high-speed electric injection molding machines as an example, they can run a mold with eight cavities in a cycle of only 7.2 seconds. They can produce an additional 14,400 products daily, increasing production capacity by more than 15%.
The high-speed performance of electric injection molding machines is achieved through discrete intelligent drive control, which can control the servo motor in real time to improve the accuracy of position, speed and pressure control to ensure that the material is injected and cooled at the optimal rate, thereby maximizing speed and product quality. In addition, configuring multiple high-speed injection molding machines and other equipment in the production line directly increases production capacity in a linear manner. This scalability enables manufacturers to quickly expand production to meet peak demand periods, making it easier to cope with seasonal order surges.
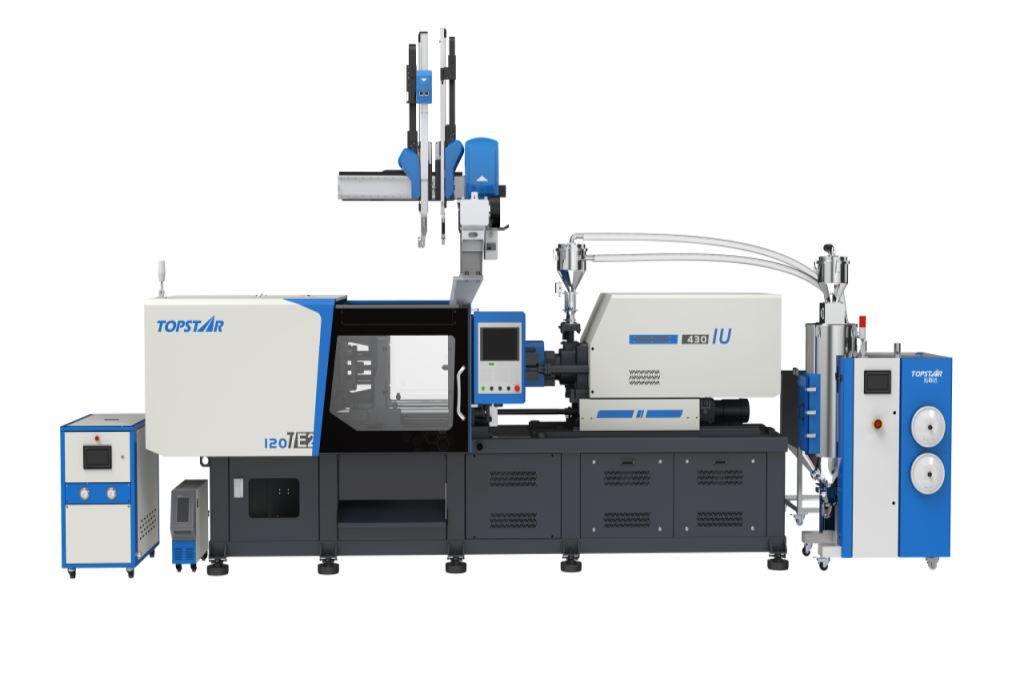
Intelligent automation promotes continuous production
A one-stop injection molding solution can help customers achieve intelligent automation upgrades of production lines, especially in the automatic adjustment of the injection molding robot trajectory. This intelligent automation technology ensures seamless and continuous production. The intelligent control system dynamically adjusts to changes in the production process, optimizing each injection cycle for optimal performance. At the same time, it also supports remote intelligent operation and maintenance, allowing engineers to monitor the status of the equipment from anywhere, thereby achieving proactive maintenance and rapid response to faults. By reducing the mean fault response time to less than 2 hours, manufacturers can significantly reduce unplanned downtime, which is a key factor in ensuring stable production output.
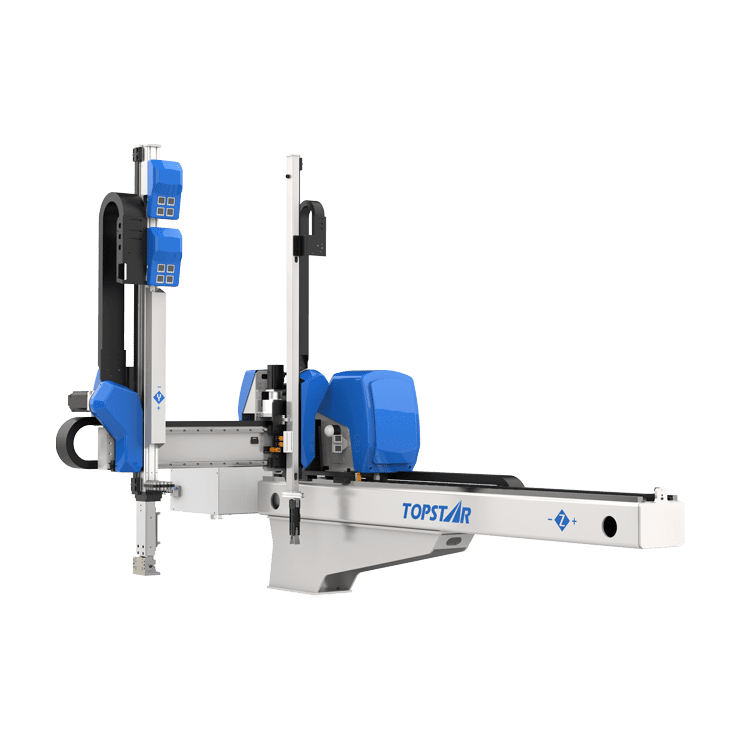
Integrated Modular Design
The integrated modular design can reduce equipment maintenance costs by 25% and reduce floor space by 50%, minimizing the physical footprint of the production line. The modular design integrates different production stages, such as injection molding machines, material stacking, and packaging, into a compact system, eliminating the need for large-scale infrastructure modifications. In addition, the modular architecture enhances overall system flexibility. As market needs evolve, manufacturers can easily add or remove modules based on the required production scale. This adaptability is very valuable during peak production seasons, and the modular design also simplifies future upgrades and maintenance, ensuring that the system is always in sync with the latest technological advances.
1-1024x682.webp)
Streamlined Material Handling and Packaging Integration
Another key aspect of Topstar’s one-stop injection molding machine solution is its comprehensive integration of downstream processes, including material stacking, bagging and packaging, labeling, unpacking, boxing, sealing and intelligent palletizing. The automated material handling functions in the solution work in coordination with the injection molding machine to ensure that raw materials and finished products move smoothly during the production process. For example, after the injection molding stage, the system automatically transfers the products to the bagging and packaging unit, where it neatly arranges and seals them, speeding up production and reducing the risk of errors associated with manual handling.
At the same time, the system integrates labeling and unpacking/packaging stages to correctly identify and organize products before they enter the final stage of the production line, further improving efficiency. The intelligent palletizing workstation adjusts the automation of finished product stacking and sorting based on real-time data from the production line, ensuring optimal pallet loading and an uninterrupted process.
Achieve a closed loop of the entire injection molding machine production process
The one-stop injection molding machine solution is a comprehensive integrated system. We change how manufacturers produce with intelligence, flexibility and efficiency as the core. Improve production capacity, efficiency and product quality by combining intelligent and advanced injection molding technology with streamlined material handling, automated packaging and intelligent remote operation.
TRENDING POSTS
- What factors can cause delays in the injection molding process of plastic molding machine? 2025/04/02
- Exhibition Review| Topstar participates in InterPlas Thailand 2024 2025/04/02
- Star Case | Topstar helps Santong upgrade its intelligent plant 2025/04/02
- Topstar Special | National Science and Technology Workers Day 2025/04/02
HOT TOPIC
- 3 in 1 Compact Dehumidifying Dryer
- 5-axis CNC machine
- accuracy
- Air Chillers
- all electric injection molding machine
- All-electric injection molding machines
- and overall production quality. Therefore
- AP-RubberPlas
- automated injection molding machine
- Automation changed engineering
- automation of injection molding robots
- auxiliary machine
- Bench Injection Molding Machine
- Cabinet dryer manufacturers
- Cabinet dryers
- chiller
- CNC Drilling Machine
- CNC Drilling Machines
- cnc engraving machine manufacturer
- cnc laser cutting machine manufacturer
- CNC machine
- CNC Machine Center
- CNC Machine for Sale
- CNC Machine Manufacturing
- CNC Machine Tool
- CNC machine tool product
- CNC Machining Center
- CNC wood carving machine
- Cooling system
- Cross-Walking Single Axis Servo Cylinder Robot
- Cross-Walking Single-Axis Servo Cylinder Robot
- Cross-Walking Three-Axis/Five-Axis Servo Driven Robot
- cross-walking three-axis/five-axis servo-driven robot
- Dehumidifier Dryer
- Dehumidifying Dryer
- delta parallel robot
- Desktop Injection Molding Machine
- Desktop injection molding machines
- Desktop Molding Machine
- desktop plastic injection machine
- Desktop Plastic Injection Molding Machine
- direct clamp injection molding machine
- Direct clamp injection molding machines
- Dosing & mixing system
- Drilling Centers
- Drying and dehumidification system
- drying and dehumidifying equipment
- Drying and Dehumidifying System
- drying system
- effective and efficient. Cabinet dryers are also used in other industries where large quantities of material need to be dried
- efficient injection molding machine
- elbow hydraulic injection molding machines
- electric injection molding machine
- electric injection molding machines
- etc. Among injection molding robots
- exhibition
- features of CNC machine
- Feeding And Conveying System
- Five Axis Machine Center
- Fully automatic injection molding machine
- Gathering Topstar
- giant injection molding machine
- GMU-600 5-Axis Machining Center
- Granulating & Recycling System
- Heavy duty injection molding machine
- Honeycomb rotor dehumidifier
- horizontal injection molding machine
- Horizontal Injection Molding Machines
- Horizontal Injection Moulding Machine
- Horizontal Mixer manufacturer
- How The CNC Machine Works
- hybrid injection molding machine
- hydraulic injection molding machine
- Hydraulic Injection Molding Machines
- in this article
- Industrial robot
- Industrial Robot Chinese brand
- industrial robot parts
- industrial robot supplier
- Industrial robots
- Industry Chain
- Injection Manipulator
- injection mold machines
- Injection molding
- Injection molding automation
- Injection Molding Automation Solution
- injection molding dryer
- Injection molding equipment
- injection molding hopper dryer
- Injection molding machine
- injection molding machine brand
- Injection Molding Machine Factory
- Injection Molding Machine Manufacture
- Injection molding machine manufacturer
- injection molding machine manufacturers
- Injection molding machine procurement
- injection molding machine robotic arm
- injection molding machine with a robot
- Injection molding machines
- injection molding material dehumidifying
- injection molding plant
- Injection Molding Robot
- injection molding robot arm
- Injection molding robot automation
- Injection molding robotic arm
- injection molding robots
- Injection Moulding Robots
- Injection Robot
- Injection robot arm
- Injection robot manufacturer
- Injection robot wholesale
- injection robots
- intelligent injection molding machines
- Introducing Injection Robot
- It is the best choice for drying large quantities of material at once. Cabinetmakers use these machines because they are fast
- large injection molding machine
- Learn what industrial automation and robotics is
- low speed sound-proof granulator
- machine plastic molding
- make sure to add some! Improvements (2) Keyphrase in introduction: Your keyphrase or its synonyms appear in the first paragraph of the copy
- manipulator machine
- manufacturing
- micro injection molding machine
- middle speed granulator
- Mini CNC machine manufacturers.
- Mold Temperature Control System
- mold temperature controller
- molding material Dehumidifying System
- mould temperature controller
- mould temperature controllers
- New electric injection molding machine
- nitrogen dryer manufacturer
- nitrogen dryer system manufacturer
- Oil type mold temperature controller
- open day
- Outbound links: No outbound links appear in this page. Add some! Images: No images appear on this page. Add some! Internal links: No internal links appear in this page
- PET Preform injection molding
- phone case maker machine
- phone case making machine
- plastic bottle making machine
- plastic bottle manufacturing
- plastic bucket making machine
- plastic bucket manufacturing
- Plastic chair making machine
- plastic forming equipment
- plastic hopper dryer
- plastic injection machine
- plastic injection machines
- plastic injection molding
- Plastic injection molding equipment
- Plastic injection molding machine
- Plastic Injection Molding Machines
- plastic injection robot
- Plastic Molding machine
- Plastic Molding Machines
- plastic molding press
- plastic phone case making machine
- plastic-molding machine
- powerful granulator
- Powerful Type Sound-Proof Granulator
- production of plastic seats
- Robot injection molding
- robot injection molding machine
- robot manufacturing companies
- Robotic arm for injection molding machine
- robotic injection molding machines
- robotics in injection molding
- SCARA robot
- SCARA robots
- Service-oriented manufacturing
- Servo Cylinder Robot
- servo driven robot
- Servo Driven Robots
- servo injection robots
- Servo-Driven Robot
- Setup of injection machine
- Silicone Injection Molding Machine
- six-axis industrial robot
- Stainless Hopper Dryer
- Stainless Hopper Dryers
- star club
- swing arm robot
- the choice between servo-driven robots and hydraulic robots will have a certain impact on efficiency
- the most popular injection molding machine
- the type of injection molding robot
- toggle clamp injection molding machine
- Toggle Hydraulic Injection Molding Machines
- toggle injection molding machine
- Top 10 brands of injection robots
- Topstar
- Topstar Engineering
- Topstar Industrial Robots
- Topstar injection molding intelligent
- Topstar Scara Robots
- Useful Injection molding machine
- Vertical machining centers
- volumetric type blender
- water chiller
- water chillers
- water distributor
- Water Type MoldTemperature Controller
- We often face choices when performing injection molding. We will choose the type of injection molding machine
- wholesale of injection molding machines
- x carve CNC