Intelligently adjust the power distribution of plastic injection molding machines
2025/03/24 By Topstar
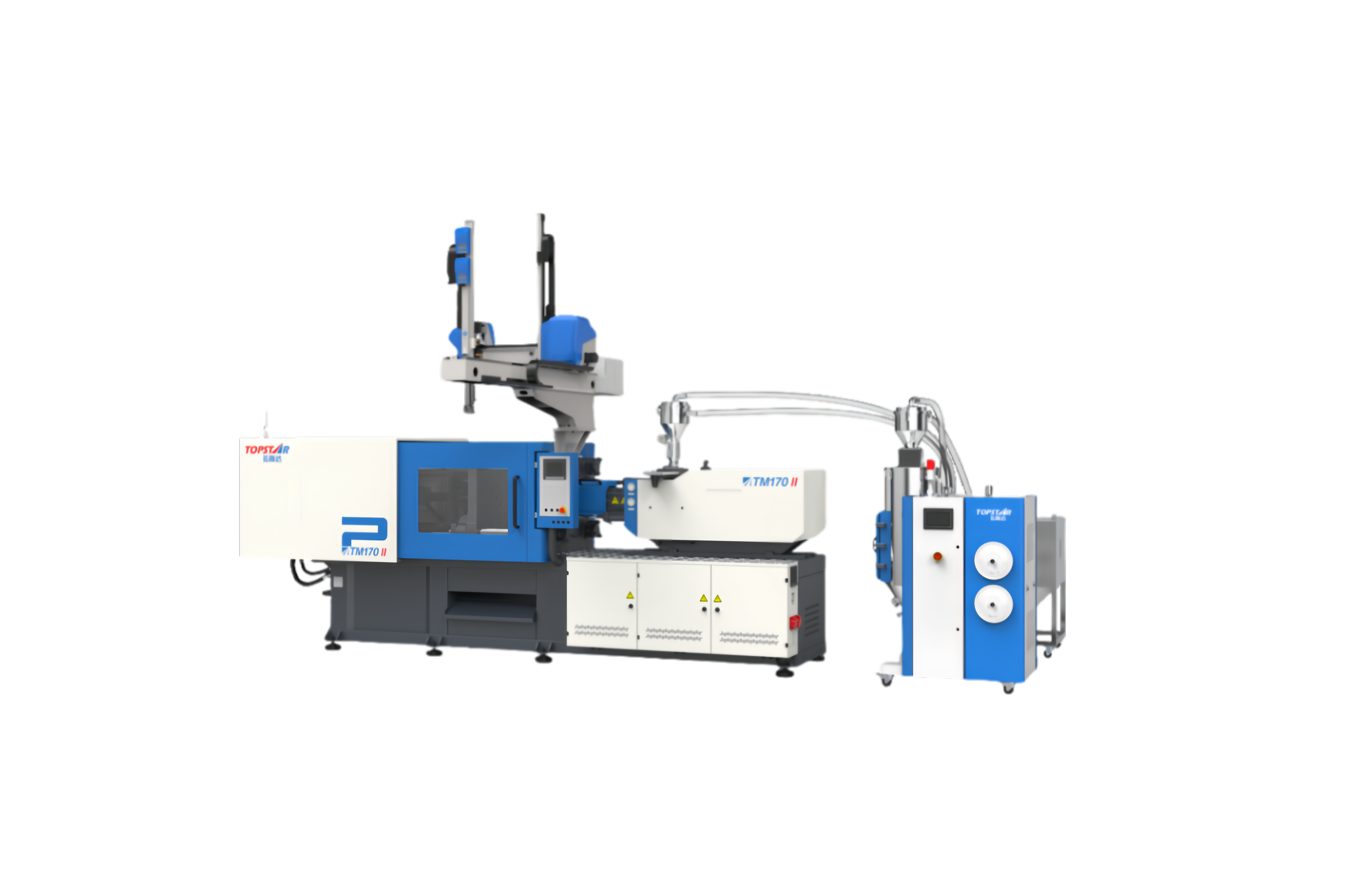
Integrating servo motor technology with plastic injection molding machines brings operational benefits beyond energy savings. One of the main benefits is enhanced control over the injection molding process. Intelligent power distribution allows operators to access real-time data and precise adjustments, promoting a more stable and predictable production environment. This level of smart control is very much needed to produce high-quality plastic parts. The core of intelligent power adjustment is that the injection molding process can be dynamically adjusted to provide just the right amount of power required for each production stage. Traditional plastic injection molding machines usually operate at a fixed power, regardless of the actual demand at each cycle stage. Servo motor technology can adjust energy output in real-time to ensure no energy is wasted.
Plastic injection molding machines adopt servo motor energy-saving technology
Traditional plastic injection molding machines consume too much energy because they use fixed-speed pumps and constant pressure maintenance. Studies indicate that industries waste 40-70% of energy during off-peak cycles. Using servo motor energy-saving technology to control energy output precisely, Topstar can fine-tune the power provided to the injection molding machine to meet the specific needs of the molding process. For example, during the mold clamping, injection, and cooling stages, the servo motor adjusts its output to ensure that optimal power is obtained at each stage without unnecessary waste. Servo motor technology is designed to respond to real-time feedback from the injection molding system. Sensors continuously monitor parameters such as temperature, pressure, and cycle time. Based on this information, the system intelligently adjusts power distribution to perform each operation efficiently.
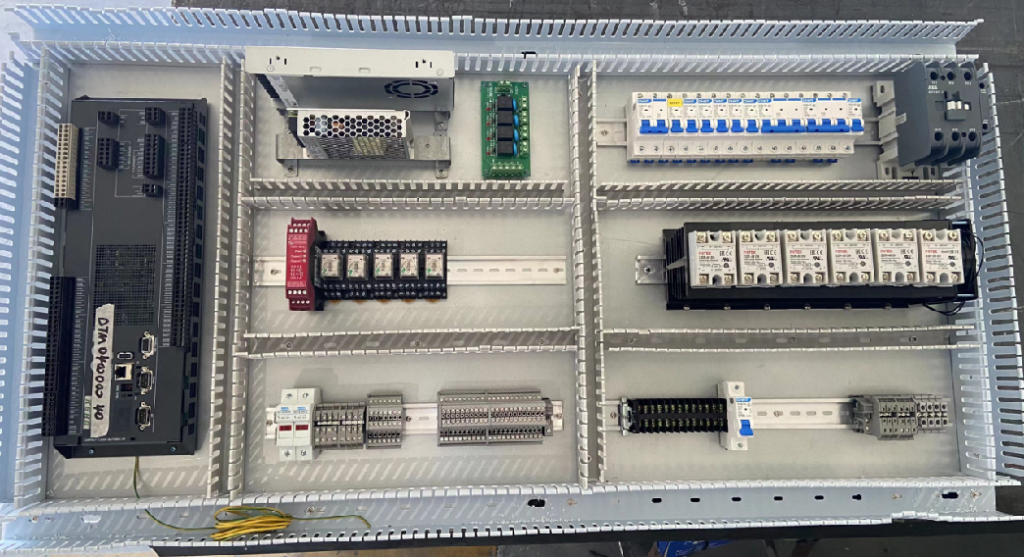
Integration and application advantages in plastic injection molding machines
The seamless integration of servo motor technology with the plastic injection molding machine brings various operational advantages. Topstar’s plastic injection molding machines have a user-friendly interface that enables operators to monitor and adjust key parameters easily. The control panel displays essential information such as energy consumption, cycle time, and system performance indicators. This transparency helps operators identify potential problems before they escalate and fine-tune machine settings for optimal performance.
In addition, the integration of servo motor technology reduces mechanical stress on injection molding machines. Traditional systems rely on hydraulic power or constant energy output, which often causes wear due to fluctuations in load and pressure. In contrast, innovative systems adjust power based on real-time demand, minimizing unnecessary stress on key components, extending the machine’s life, and reducing the frequency of maintenance and repairs, thereby reducing the total cost of ownership.
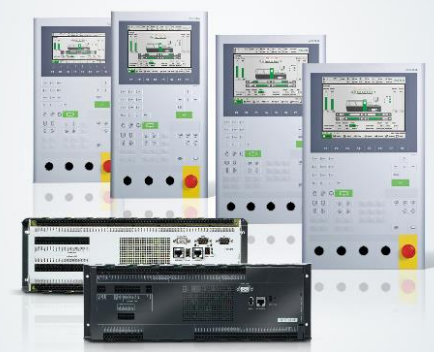
Intelligent power distribution and its impact on injection molding machine efficiency
Traditional plastic injection molding machines often use a constant energy distribution method, which means that during periods of low demand, too much power is still used, resulting in unnecessary energy consumption and higher operating costs. However, with intelligent power distribution, the system automatically adjusts power output to meet the actual needs of the process. This real-time adaptability is particularly useful when dealing with different mold sizes, materials, or production requirements. When we switch to smaller, more detailed molds in large-scale production, the intelligent power distribution system automatically recalibrates to provide the optimal power required for each new configuration. This flexibility improves the efficiency of the plastic injection molding machine and simplifies scaling up or down production as market demands change.
Compliance with global ecological standards: EU and North America
Topstar’s plastic injection molding machines can meet strict regulations:
- EU Ecodesign Directive: <0.16 kWh/kg energy efficiency threshold.
- U.S. Department of Energy Standards: Complies with 10 CFR Part 431 for industrial equipment.
- CE/UL Certification: Guaranteed safety and interoperability.
Third-party testing verifies that Topstar plastic injection molding machines emit 45% less CO2 per ton of output than the industry average. Compliance with these standards ensures market access and enhances a company’s reputation as a responsible manufacturer.
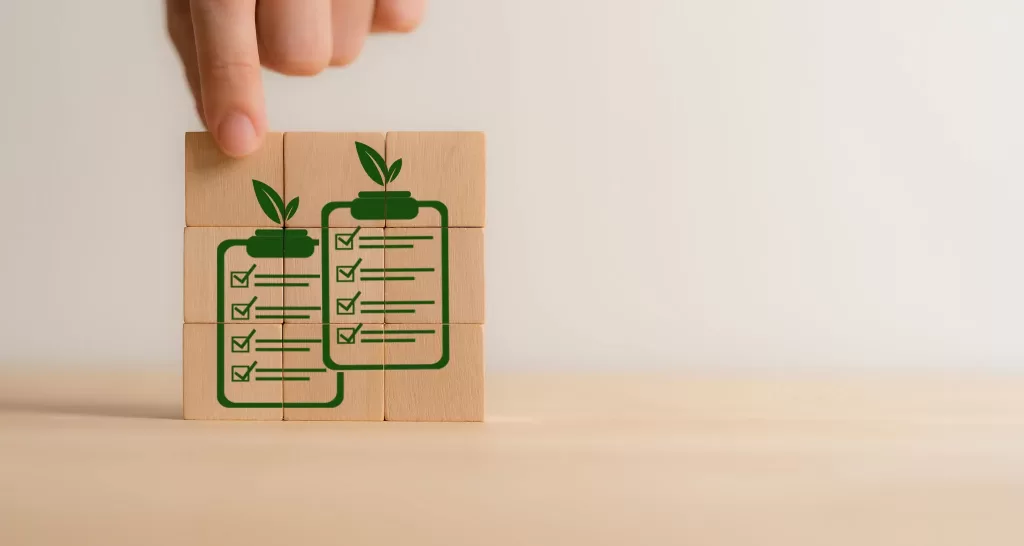
Leading to more energy-efficient and environmentally friendly production
The benefits of intelligent power distribution are evident, from enhanced control and precision to reduced mechanical stress and extended equipment life. Manufacturers that adopt these advanced plastic injection molding machines can improve production efficiency and significantly reduce energy consumption and related emissions. This enables them to meet increasingly stringent energy-saving and environmental protection standards in global markets in Europe, North America and other regions.
TRENDING POSTS
- What factors can cause delays in the injection molding process of plastic molding machine? 2025/03/24
- Exhibition Review| Topstar participates in InterPlas Thailand 2024 2025/03/24
- Star Case | Topstar helps Santong upgrade its intelligent plant 2025/03/24
- Topstar Special | National Science and Technology Workers Day 2025/03/24
HOT TOPIC
- 3 in 1 Compact Dehumidifying Dryer
- 5-axis CNC machine
- accuracy
- Air Chillers
- all electric injection molding machine
- All-electric injection molding machines
- and overall production quality. Therefore
- AP-RubberPlas
- automated injection molding machine
- Automation changed engineering
- automation of injection molding robots
- auxiliary machine
- Bench Injection Molding Machine
- Cabinet dryer manufacturers
- Cabinet dryers
- chiller
- CNC Drilling Machine
- CNC Drilling Machines
- cnc engraving machine manufacturer
- cnc laser cutting machine manufacturer
- CNC machine
- CNC Machine Center
- CNC Machine for Sale
- CNC Machine Manufacturing
- CNC Machine Tool
- CNC machine tool product
- CNC Machining Center
- CNC wood carving machine
- Cooling system
- Cross-Walking Single Axis Servo Cylinder Robot
- Cross-Walking Single-Axis Servo Cylinder Robot
- Cross-Walking Three-Axis/Five-Axis Servo Driven Robot
- cross-walking three-axis/five-axis servo-driven robot
- Dehumidifier Dryer
- Dehumidifying Dryer
- delta parallel robot
- Desktop Injection Molding Machine
- Desktop injection molding machines
- Desktop Molding Machine
- desktop plastic injection machine
- Desktop Plastic Injection Molding Machine
- direct clamp injection molding machine
- Direct clamp injection molding machines
- Dosing & mixing system
- Drilling Centers
- Drying and dehumidification system
- drying and dehumidifying equipment
- Drying and Dehumidifying System
- drying system
- effective and efficient. Cabinet dryers are also used in other industries where large quantities of material need to be dried
- efficient injection molding machine
- elbow hydraulic injection molding machines
- electric injection molding machine
- electric injection molding machines
- etc. Among injection molding robots
- exhibition
- features of CNC machine
- Feeding And Conveying System
- Five Axis Machine Center
- Fully automatic injection molding machine
- Gathering Topstar
- giant injection molding machine
- GMU-600 5-Axis Machining Center
- Granulating & Recycling System
- Heavy duty injection molding machine
- Honeycomb rotor dehumidifier
- horizontal injection molding machine
- Horizontal Injection Molding Machines
- Horizontal Injection Moulding Machine
- Horizontal Mixer manufacturer
- How The CNC Machine Works
- hybrid injection molding machine
- hydraulic injection molding machine
- Hydraulic Injection Molding Machines
- in this article
- Industrial robot
- Industrial Robot Chinese brand
- industrial robot parts
- industrial robot supplier
- Industrial robots
- Industry Chain
- Injection Manipulator
- injection mold machines
- Injection molding
- Injection molding automation
- Injection Molding Automation Solution
- injection molding dryer
- Injection molding equipment
- injection molding hopper dryer
- Injection molding machine
- injection molding machine brand
- Injection Molding Machine Factory
- Injection Molding Machine Manufacture
- Injection molding machine manufacturer
- injection molding machine manufacturers
- Injection molding machine procurement
- injection molding machine robotic arm
- injection molding machine with a robot
- Injection molding machines
- injection molding material dehumidifying
- injection molding plant
- Injection Molding Robot
- injection molding robot arm
- Injection molding robot automation
- Injection molding robotic arm
- injection molding robots
- Injection Moulding Robots
- Injection Robot
- Injection robot arm
- Injection robot manufacturer
- Injection robot wholesale
- injection robots
- intelligent injection molding machines
- Introducing Injection Robot
- It is the best choice for drying large quantities of material at once. Cabinetmakers use these machines because they are fast
- large injection molding machine
- Learn what industrial automation and robotics is
- low speed sound-proof granulator
- machine plastic molding
- make sure to add some! Improvements (2) Keyphrase in introduction: Your keyphrase or its synonyms appear in the first paragraph of the copy
- manipulator machine
- manufacturing
- micro injection molding machine
- middle speed granulator
- Mini CNC machine manufacturers.
- Mold Temperature Control System
- mold temperature controller
- molding material Dehumidifying System
- mould temperature controller
- mould temperature controllers
- New electric injection molding machine
- nitrogen dryer manufacturer
- nitrogen dryer system manufacturer
- Oil type mold temperature controller
- open day
- Outbound links: No outbound links appear in this page. Add some! Images: No images appear on this page. Add some! Internal links: No internal links appear in this page
- PET Preform injection molding
- phone case maker machine
- phone case making machine
- plastic bottle making machine
- plastic bottle manufacturing
- plastic bucket making machine
- plastic bucket manufacturing
- Plastic chair making machine
- plastic forming equipment
- plastic hopper dryer
- plastic injection machine
- plastic injection machines
- plastic injection molding
- Plastic injection molding equipment
- Plastic injection molding machine
- Plastic Injection Molding Machines
- plastic injection robot
- Plastic Molding machine
- Plastic Molding Machines
- plastic molding press
- plastic phone case making machine
- plastic-molding machine
- powerful granulator
- Powerful Type Sound-Proof Granulator
- production of plastic seats
- Robot injection molding
- robot injection molding machine
- robot manufacturing companies
- Robotic arm for injection molding machine
- robotic injection molding machines
- robotics in injection molding
- SCARA robot
- SCARA robots
- Service-oriented manufacturing
- Servo Cylinder Robot
- servo driven robot
- Servo Driven Robots
- servo injection robots
- Servo-Driven Robot
- Setup of injection machine
- Silicone Injection Molding Machine
- six-axis industrial robot
- Stainless Hopper Dryer
- Stainless Hopper Dryers
- star club
- swing arm robot
- the choice between servo-driven robots and hydraulic robots will have a certain impact on efficiency
- the most popular injection molding machine
- the type of injection molding robot
- toggle clamp injection molding machine
- Toggle Hydraulic Injection Molding Machines
- toggle injection molding machine
- Top 10 brands of injection robots
- Topstar
- Topstar Engineering
- Topstar Industrial Robots
- Topstar injection molding intelligent
- Topstar Scara Robots
- Useful Injection molding machine
- Vertical machining centers
- volumetric type blender
- water chiller
- water chillers
- water distributor
- Water Type MoldTemperature Controller
- We often face choices when performing injection molding. We will choose the type of injection molding machine
- wholesale of injection molding machines
- x carve CNC