How to Solve Uneven Drying in Injection Molding with a Dehumidifying Dryer?
2025/03/19 By Topstar
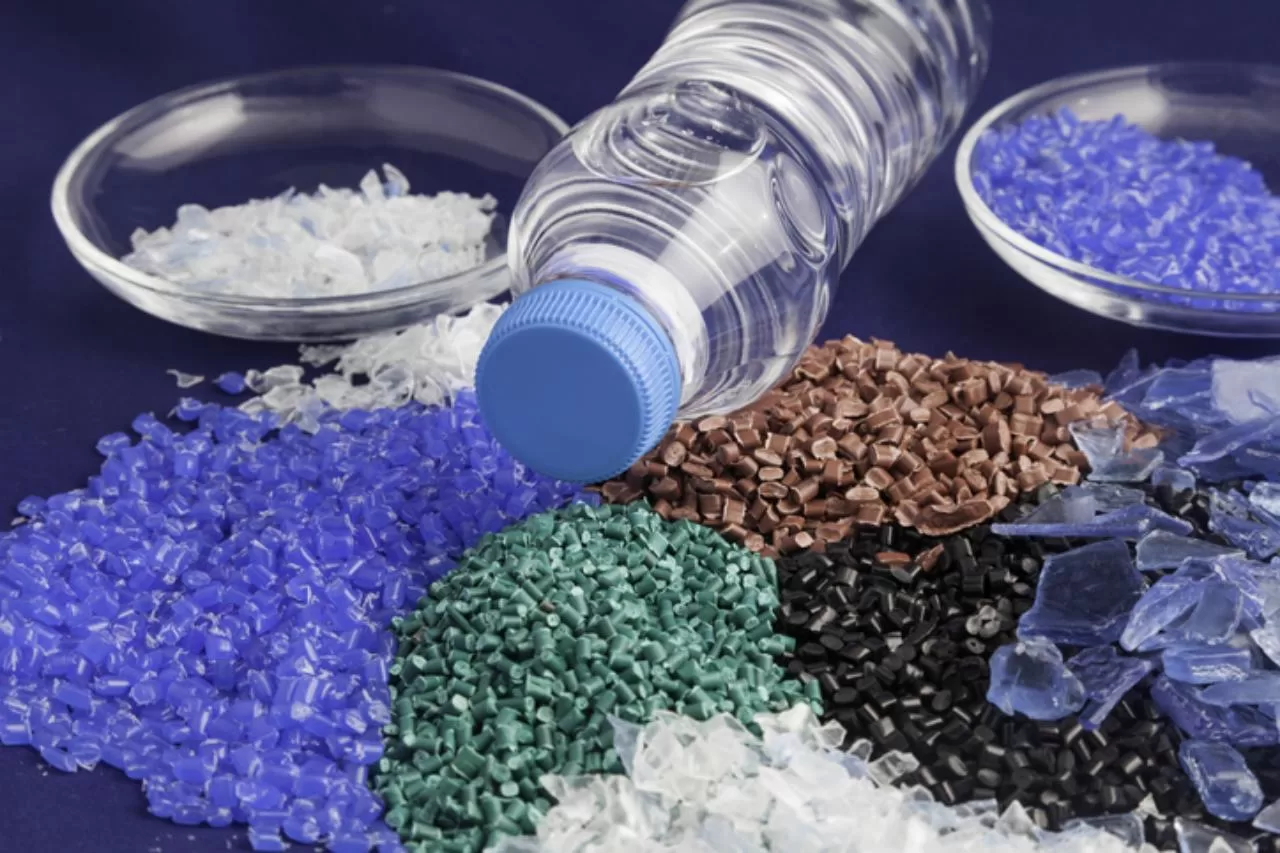
When processing engineering plastics, uneven drying can lead to defects, compromised structural integrity, and inconsistent final product performance. Traditional drying methods often rely on ambient heat or simple forced ventilation systems that do not provide consistent results, especially when processing complex engineering plastics. Variations in moisture content and temperature fluctuations can lead to uneven drying, resulting in parts that may not meet quality standards. In contrast, the dehumidifying dryer provided by Topstar provides a steady supply of dehumidified air with a dew point as low as -40°F. At the same time, it also integrates drying. The three functions of dehumidification, drying, and two-stage feeding are integrated into one, further enhancing the control of the dehumidification process and adapting to different production needs.
Problems of Uneven Drying of Dehumidifying Dryer in Injection Molding
Traditional injection molding drying methods rely on ambient conditions and basic forced ventilation systems that lack precise control. When parts are unevenly dried, they may suffer from problems such as warping, surface defects, or poor bonding, which are unacceptable in applications such as automotive, medical, or optical parts. These inconsistencies affect the aesthetic quality of the product and cause functional failures of key components.
The dehumidifying dryer supplied by Topstar ensures moisture is evenly removed from every part of the mold by delivering a steady, controlled flow of dehumidified air at a dew point of -40°F. This is essential to maintaining consistency and reliability in the injection molding process. The technology behind it enables it to precisely regulate temperature and humidity levels to create an ideal drying environment, significantly reducing the risk of defects caused by uneven moisture distribution.
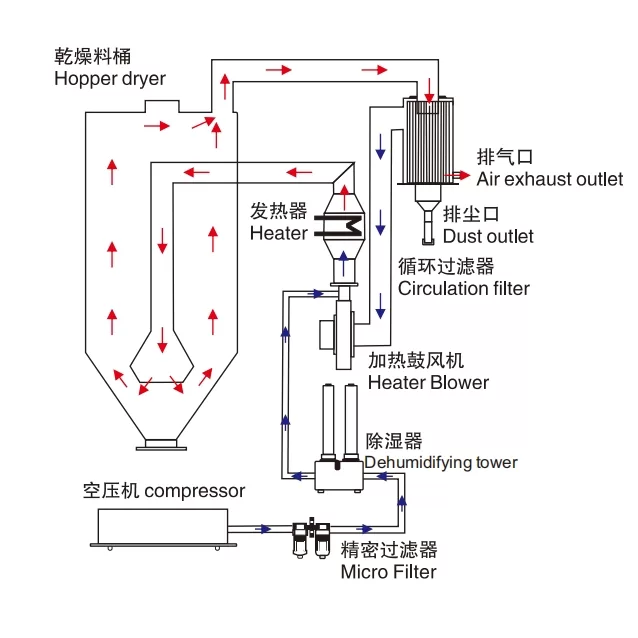
Dehumidification, drying, two-stage feeding in one
With a steady supply of dehumidified air and a dew point as low as -40°F, the dehumidifying dryer combines dehumidification, drying, and two-stage feeding in one. The system can incorporate three-stage feeding when necessary. This flexibility in material handling allows operators to customize the process to meet the specific requirements of various production runs, adjusting feeding options to precisely control the drying process and ensure even treatment of every product. In addition, the injection molding control system manages the coordinated operation of the dehumidification and drying functions, which continuously monitors and adjusts process parameters in real-time. This level of intelligence minimizes the need for manual intervention and reduces the possibility of human error. As a result, the system is highly reliable and consistently produces high-quality products under harsh conditions.
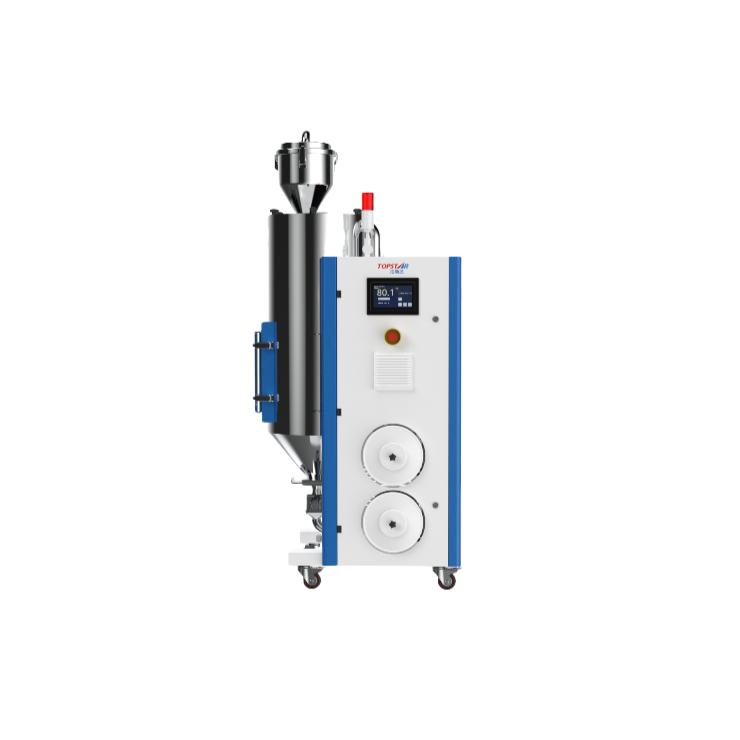
Double-layer insulation drying and down-blowing air duct design
The key to achieving uniform drying of injection molding is to control heat distribution and minimize heat loss. The dehumidifying dryer uses a double-layer insulation drying barrel and a down-blowing air duct design.
The double-layer insulation design effectively prevents heat loss. It ensures that the temperature in the drying chamber remains stable throughout the process, avoiding slight temperature fluctuations that lead to uneven product moisture removal. Maintaining a constant temperature allows the insulation drying barrel to dry any moisture on the adhesive or injection molded parts evenly. The down-blowing air duct design further improves drying uniformity by evenly directing dehumidified air to the product’s surface. It distributes the air in a controlled manner, pre-conditioning the dew point to -40°F. This targeted airflow prevents hot spots and air stagnation areas, common problems in traditional drying systems. As a result, the system exposes the entire product to the same drying conditions, ensuring a more consistent and reliable final output.
Dehumidifying Dryer with Microcomputer Control
The microcomputer control system is the core of the dryer’s operational intelligence. It continuously collects data on various parameters such as temperature, humidity, airflow, and product moisture content and then processes this data to make instant adjustments. This dynamic adjustment is essential to maintaining a consistent drying environment, directly translating into better product quality.
The user-friendly interface. It allows operators to efficiently program and adjust drying parameters according to the specific requirements of the production run. This flexibility will enable engineers to prevent defects such as warping, shrinkage, or incomplete curing according to the unique drying curves required for different engineering plastics. The micro control system automates the adjustment process and provides real-time feedback, allowing operators to monitor the dryer’s performance and make proactive decisions when anomalies occur.
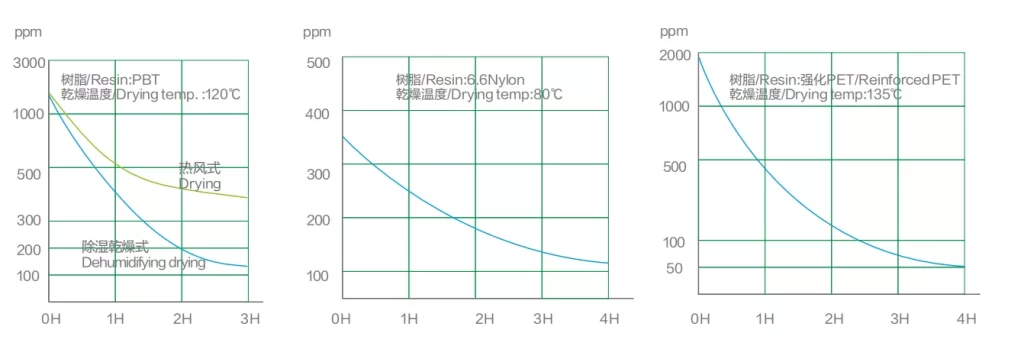
Impact on Product Quality and Production Efficiency
Uniform drying is essential to maintain the structural integrity of injection molded parts. When drying is uneven, parts may develop weak spots, dimensional inaccuracies, or defects that lead to unusable parts. Providing a steady supply of dehumidified air with a dew point of -40°F ensures that moisture is effectively and evenly removed from all product areas. This uniformity is further enhanced by advanced cooling and downdraft duct design, which prevents heat loss and maintains consistent processing conditions throughout the drying cycle. Improved product quality translates directly into increased production efficiency. With dehumidifying dryers that can reliably produce high-quality parts, manufacturers can reduce scrap rates and rework, saving costs and increasing production output. Intelligent processes controlled by microcomputer control systems minimize downtime and enable continuous operation, making production lines run more smoothly and predictably.
Ensure uniformity of drying.
The dehumidified air is supplied with a dew point of -40°F, ensuring uniform dehumidification. Its double-layer insulation and downdraft duct design prevent heat loss and improve drying efficiency. A microcomputer control system can intelligently adjust the drying curve to ensure optimal conditions for various engineering plastics. This level of intelligence minimizes human error, reduces scrap rates, and significantly improves overall production efficiency.
TRENDING POSTS
- What factors can cause delays in the injection molding process of plastic molding machine? 2025/03/19
- Exhibition Review| Topstar participates in InterPlas Thailand 2024 2025/03/19
- Star Case | Topstar helps Santong upgrade its intelligent plant 2025/03/19
- Topstar Special | National Science and Technology Workers Day 2025/03/19
HOT TOPIC
- 3 in 1 Compact Dehumidifying Dryer
- 5-axis CNC machine
- accuracy
- Air Chillers
- all electric injection molding machine
- All-electric injection molding machines
- and overall production quality. Therefore
- AP-RubberPlas
- automated injection molding machine
- Automation changed engineering
- automation of injection molding robots
- auxiliary machine
- Bench Injection Molding Machine
- Cabinet dryer manufacturers
- Cabinet dryers
- CNC Drilling Machine
- CNC Drilling Machines
- cnc engraving machine manufacturer
- cnc laser cutting machine manufacturer
- CNC machine
- CNC Machine Center
- CNC Machine for Sale
- CNC Machine Manufacturing
- CNC Machine Tool
- CNC machine tool product
- CNC Machining Center
- CNC wood carving machine
- Cooling system
- Cross-Walking Single Axis Servo Cylinder Robot
- Cross-Walking Single-Axis Servo Cylinder Robot
- Cross-Walking Three-Axis/Five-Axis Servo Driven Robot
- cross-walking three-axis/five-axis servo-driven robot
- Dehumidifier Dryer
- Dehumidifying Dryer
- delta parallel robot
- Desktop Injection Molding Machine
- Desktop injection molding machines
- Desktop Molding Machine
- desktop plastic injection machine
- Desktop Plastic Injection Molding Machine
- direct clamp injection molding machine
- Direct clamp injection molding machines
- Dosing & mixing system
- Drilling Centers
- Drying and dehumidification system
- drying and dehumidifying equipment
- Drying and Dehumidifying System
- drying system
- effective and efficient. Cabinet dryers are also used in other industries where large quantities of material need to be dried
- efficient injection molding machine
- elbow hydraulic injection molding machines
- electric injection molding machine
- electric injection molding machines
- etc. Among injection molding robots
- exhibition
- features of CNC machine
- Feeding And Conveying System
- Five Axis Machine Center
- Fully automatic injection molding machine
- Gathering Topstar
- giant injection molding machine
- GMU-600 5-Axis Machining Center
- Granulating & Recycling System
- Heavy duty injection molding machine
- Honeycomb rotor dehumidifier
- horizontal injection molding machine
- Horizontal Injection Molding Machines
- Horizontal Injection Moulding Machine
- Horizontal Mixer manufacturer
- How The CNC Machine Works
- hybrid injection molding machine
- hydraulic injection molding machine
- Hydraulic Injection Molding Machines
- in this article
- Industrial robot
- Industrial Robot Chinese brand
- industrial robot parts
- industrial robot supplier
- Industrial robots
- Industry Chain
- Injection Manipulator
- Injection molding
- Injection molding automation
- Injection Molding Automation Solution
- injection molding dryer
- Injection molding equipment
- injection molding hopper dryer
- Injection molding machine
- injection molding machine brand
- Injection Molding Machine Factory
- Injection Molding Machine Manufacture
- Injection molding machine manufacturer
- injection molding machine manufacturers
- Injection molding machine procurement
- injection molding machine robotic arm
- injection molding machine with a robot
- Injection molding machines
- injection molding material dehumidifying
- injection molding plant
- Injection Molding Robot
- injection molding robot arm
- Injection molding robot automation
- Injection molding robotic arm
- injection molding robots
- Injection Moulding Robots
- Injection Robot
- Injection robot arm
- Injection robot manufacturer
- Injection robot wholesale
- injection robots
- intelligent injection molding machines
- Introducing Injection Robot
- It is the best choice for drying large quantities of material at once. Cabinetmakers use these machines because they are fast
- large injection molding machine
- Learn what industrial automation and robotics is
- low speed sound-proof granulator
- machine plastic molding
- make sure to add some! Improvements (2) Keyphrase in introduction: Your keyphrase or its synonyms appear in the first paragraph of the copy
- manipulator machine
- manufacturing
- micro injection molding machine
- middle speed granulator
- Mini CNC machine manufacturers.
- Mold Temperature Control System
- mold temperature controller
- molding material Dehumidifying System
- mould temperature controller
- mould temperature controllers
- New electric injection molding machine
- nitrogen dryer manufacturer
- nitrogen dryer system manufacturer
- Oil type mold temperature controller
- open day
- Outbound links: No outbound links appear in this page. Add some! Images: No images appear on this page. Add some! Internal links: No internal links appear in this page
- PET Preform injection molding
- phone case maker machine
- phone case making machine
- plastic bottle making machine
- plastic bottle manufacturing
- plastic bucket making machine
- plastic bucket manufacturing
- Plastic chair making machine
- plastic forming equipment
- plastic hopper dryer
- plastic injection machine
- plastic injection machines
- plastic injection molding
- Plastic injection molding equipment
- Plastic injection molding machine
- Plastic Injection Molding Machines
- plastic injection robot
- Plastic Molding machine
- Plastic Molding Machines
- plastic molding press
- plastic phone case making machine
- plastic-molding machine
- powerful granulator
- Powerful Type Sound-Proof Granulator
- production of plastic seats
- Robot injection molding
- robot injection molding machine
- robot manufacturing companies
- Robotic arm for injection molding machine
- robotic injection molding machines
- robotics in injection molding
- SCARA robot
- SCARA robots
- Service-oriented manufacturing
- Servo Cylinder Robot
- servo driven robot
- Servo Driven Robots
- servo injection robots
- Servo-Driven Robot
- Setup of injection machine
- Silicone Injection Molding Machine
- six-axis industrial robot
- Stainless Hopper Dryer
- Stainless Hopper Dryers
- star club
- swing arm robot
- the choice between servo-driven robots and hydraulic robots will have a certain impact on efficiency
- the most popular injection molding machine
- the type of injection molding robot
- toggle clamp injection molding machine
- Toggle Hydraulic Injection Molding Machines
- toggle injection molding machine
- Top 10 brands of injection robots
- Topstar
- Topstar Engineering
- Topstar Industrial Robots
- Topstar injection molding intelligent
- Topstar Scara Robots
- Useful Injection molding machine
- Vertical machining centers
- volumetric type blender
- water chiller
- water distributor
- Water Type MoldTemperature Controller
- We often face choices when performing injection molding. We will choose the type of injection molding machine
- wholesale of injection molding machines
- x carve CNC