How do EU sustainability regulations affect the choice of plastic molding machines?
2025/03/17 By Topstar
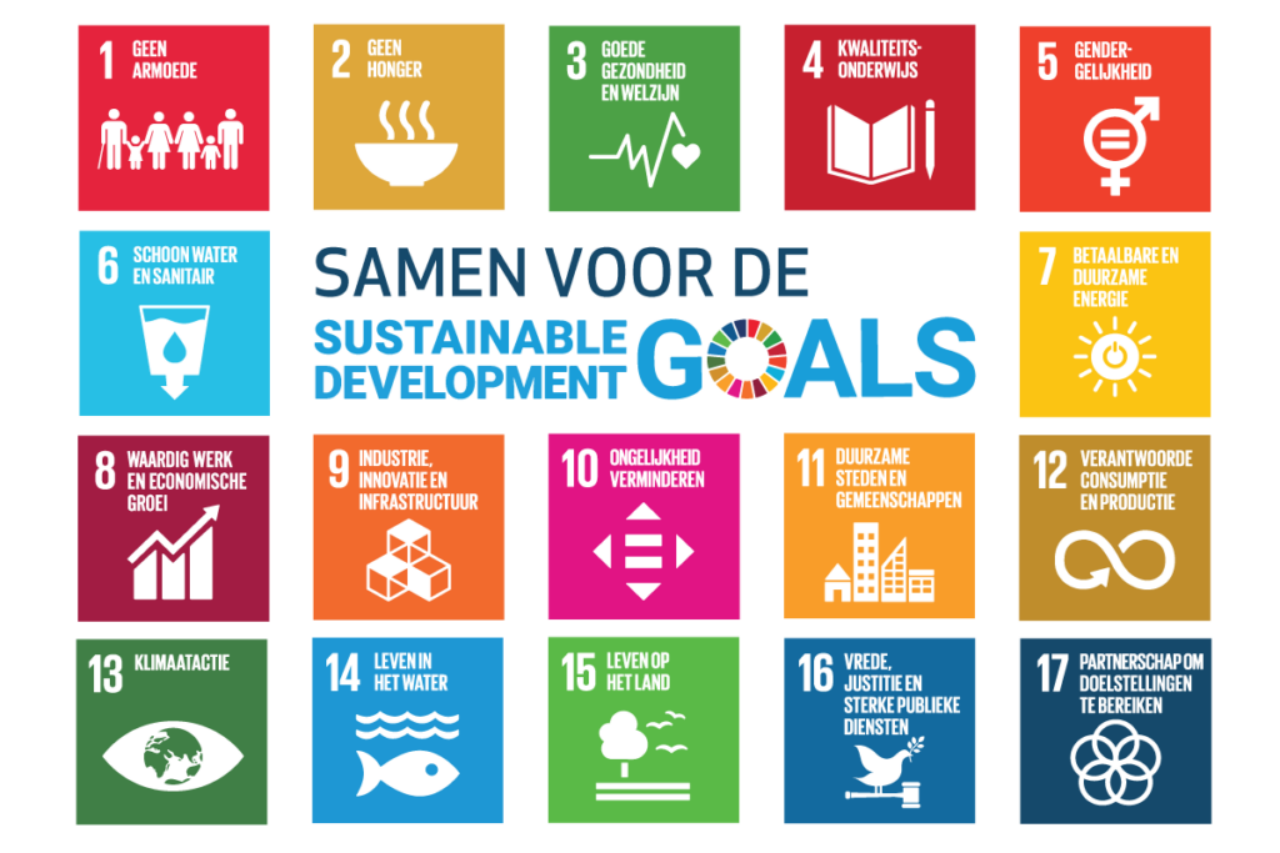
The EU Sustainable Development Directive aims to reduce environmental impact by encouraging the use of environmentally friendly materials and processes. For the plastics industry, this means a shift from traditional materials to advanced thermosets and thermoplastics that are lighter, stronger, and more recyclable. Therefore, plastic manufacturers in the European region are under pressure to innovate and adapt production methods to meet these strict guidelines. The demand for plastic molding machines that can handle these advanced materials has increased significantly. These plastic molding machines must process new sustainable polymers efficiently, reduce energy consumption, and minimize waste during production.
In addition, the new regulations directly impact the entire supply chain. Companies now have to consider the environmental impact of every stage of production—from raw material selection to final product disposal. This has led to a surge in demand for plastic molding machines that provide full transparency and control of the injection molding production process. As a result, there is a greater need for plastic molding machines that can optimize plastic consumption and reduce scrap rates while ensuring that the manufacturing process is both cost-effective and environmentally friendly.
Challenges facing the traditional plastics industry
Due to the strict EU sustainable development regulations, the traditional plastics industry faces many obstacles. The main impact is the inherent limitations of conventional molding equipment when processing newer sustainable materials. Plastic molding machines designed for traditional polymers have difficulty handling the unique properties of thermosets and advanced thermoplastics. These materials often require precise temperature control and specialized handling to avoid defects. Therefore, new technologies that can adapt to these advanced materials are needed.
Another key issue is the lack of skilled workers and production experts. The shift to sustainable materials requires higher technical expertise to operate and maintain advanced plastic molding machines. Traditional operators may lack the training to handle new processes, resulting in increased scrap rates and inefficient production. The learning curve associated with modern equipment can cause operational disruptions and increased costs, at least during the transition period.
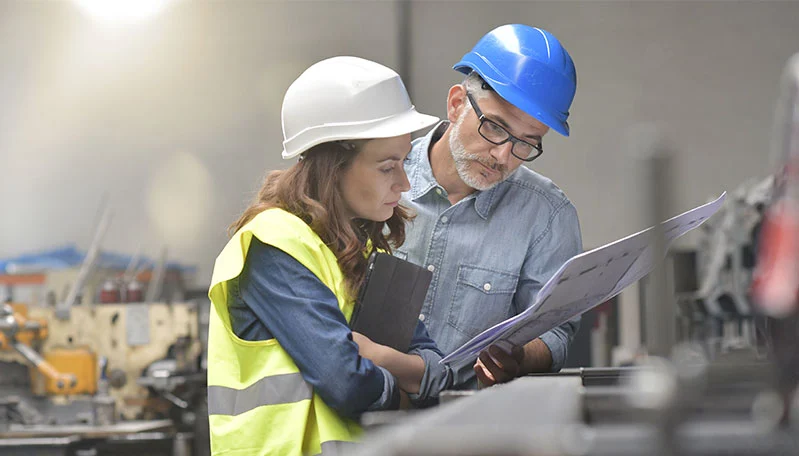
Plastic molding machines that can meet the shift to sustainable, lightweight, and efficient materials
EU sustainability regulations have driven a shift in materials used in the plastics industry. Traditional heavy polymers are being replaced by more sustainable, lighter, and more efficient alternatives. In this new landscape, plastic molding machines must be able to handle innovative materials such as advanced thermosets and specialty thermoplastics. These materials are more environmentally friendly and have enhanced performance characteristics that are important in modern applications, from automotive parts to consumer packaging. Lighter materials can reduce transportation costs and improve the overall energy efficiency of products. In automotive manufacturing, using lightweight thermoplastics can significantly save fuel and reduce emissions over the vehicle’s life. In addition, sustainable materials are often more recyclable, which aligns with the circular economy principles advocated by many EU regulations.
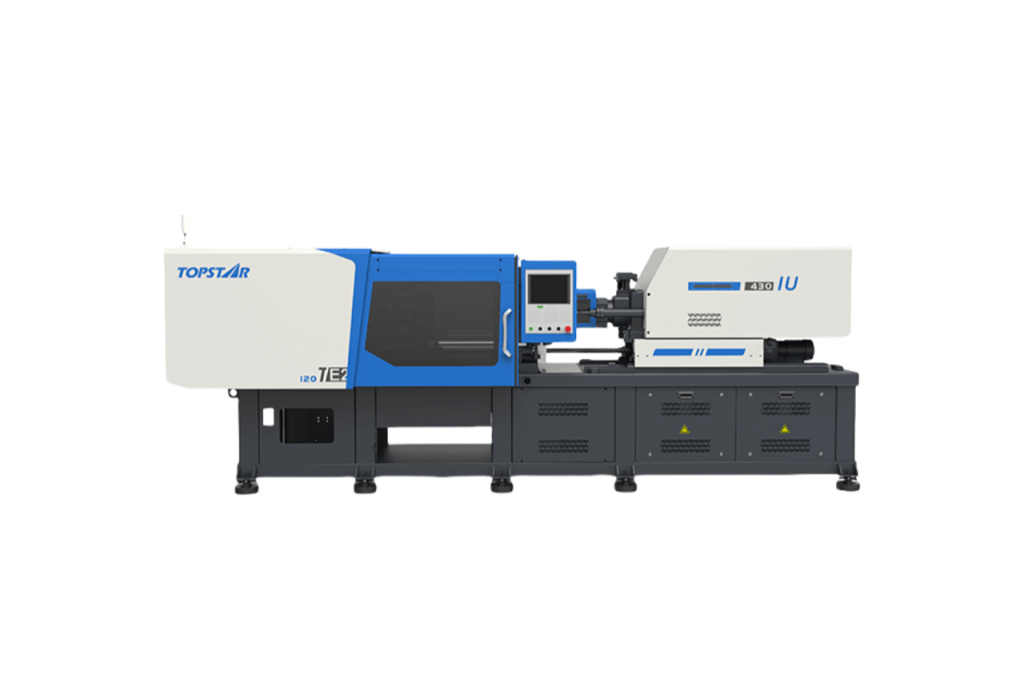
Addressing the shortage of skilled workers and reducing high scrap rates in plastic molding machines
Advanced polymers such as high-performance thermosets require precise temperature control and accurate processing conditions to achieve optimal results. Without skilled operators, the risk of defects rises, leading to high scrap rates and increased production costs. Topstar’s use of intelligent process control features in the plastic molding machine simplifies operation. These systems often include intuitive interfaces, real-time monitoring, and automatic adjustments to maintain optimal processing conditions. As a result, even operators with limited experience can consistently achieve high-quality output, thereby reducing overall scrap rates.
In addition, they are all equipped with built-in diagnostic tools and process optimization software. These features help detect inefficiencies and errors early in the production cycle so timely adjustments can be made before significant material waste occurs. By providing full transparency into the injection molding process, these machines are ensured to be closely monitored and controlled at every stage, from material feeding to cooling. This improves product quality and significantly reduces the loss of expensive sustainable materials.
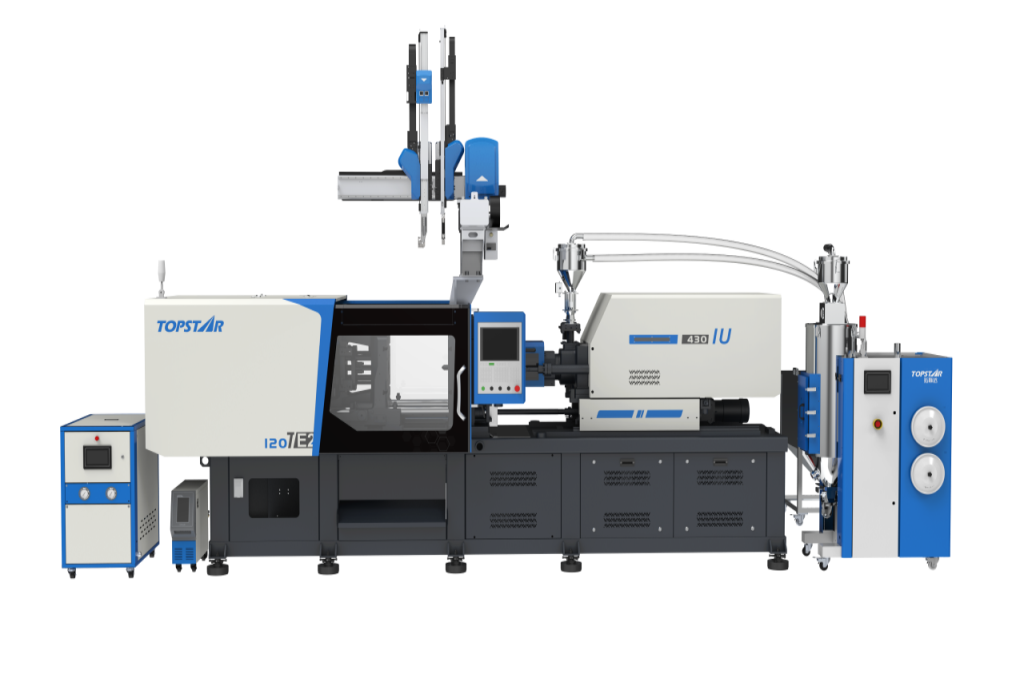
Reduce plastic consumption through innovative technology.
EU sustainability regulations emphasize using materials and processes with minimal environmental impact, prompting manufacturers to seek injection molding solutions that reduce plastic waste and improve resource efficiency. One of the most effective ways to achieve material efficiency in plastic molding machines is to control injection molding parameters precisely. The amount of plastic used in each cycle is minimized by fine-tuning variables such as injection speed, pressure, and temperature. This precision helps reduce overpackaging and material waste, common problems in traditional molding processes.
The self-developed control systems and sensors embedded in Topstar’s plastic molding machines and the ability to integrate peripheral injection molding equipment can continuously monitor the complete molding process in real-time, dynamically adjusting settings to maintain optimal material flow. The result is consistent part quality and significantly reduced scrap rates, directly saving costs. At the same time, their full transparency into the injection molding cycle also enables manufacturers to identify and eliminate inefficiencies.
Future developments in sustainable development
The ongoing shift toward sustainable materials is expected to drive further innovation in plastic molding machine design. As manufacturers increasingly adopt environmentally friendly polymers, the demand for equipment that can effectively process these materials will continue to grow. For Topstar, plastic molding machines will provide greater versatility and the ability to process a broader range of sustainable materials, allowing companies to try new formulations without significant reprocessing costs. In the future, advances in digital manufacturing, artificial intelligence, and data analytics will revolutionize plastic molding, allowing manufacturers to implement further targeted measures to reduce energy consumption and waste.
TRENDING POSTS
- What factors can cause delays in the injection molding process of plastic molding machine? 2025/03/17
- Exhibition Review| Topstar participates in InterPlas Thailand 2024 2025/03/17
- Star Case | Topstar helps Santong upgrade its intelligent plant 2025/03/17
- Topstar Special | National Science and Technology Workers Day 2025/03/17
HOT TOPIC
- 3 in 1 Compact Dehumidifying Dryer
- 5-axis CNC machine
- accuracy
- Air Chillers
- all electric injection molding machine
- All-electric injection molding machines
- and overall production quality. Therefore
- AP-RubberPlas
- automated injection molding machine
- Automation changed engineering
- automation of injection molding robots
- auxiliary machine
- Bench Injection Molding Machine
- Cabinet dryer manufacturers
- Cabinet dryers
- CNC Drilling Machine
- CNC Drilling Machines
- cnc engraving machine manufacturer
- cnc laser cutting machine manufacturer
- CNC machine
- CNC Machine Center
- CNC Machine for Sale
- CNC Machine Manufacturing
- CNC Machine Tool
- CNC machine tool product
- CNC Machining Center
- CNC wood carving machine
- Cooling system
- Cross-Walking Single Axis Servo Cylinder Robot
- Cross-Walking Single-Axis Servo Cylinder Robot
- Cross-Walking Three-Axis/Five-Axis Servo Driven Robot
- cross-walking three-axis/five-axis servo-driven robot
- Dehumidifier Dryer
- delta parallel robot
- Desktop Injection Molding Machine
- Desktop injection molding machines
- Desktop Molding Machine
- desktop plastic injection machine
- Desktop Plastic Injection Molding Machine
- direct clamp injection molding machine
- Direct clamp injection molding machines
- Dosing & mixing system
- Drilling Centers
- Drying and dehumidification system
- drying and dehumidifying equipment
- Drying and Dehumidifying System
- drying system
- effective and efficient. Cabinet dryers are also used in other industries where large quantities of material need to be dried
- efficient injection molding machine
- elbow hydraulic injection molding machines
- electric injection molding machine
- electric injection molding machines
- etc. Among injection molding robots
- exhibition
- features of CNC machine
- Feeding And Conveying System
- Five Axis Machine Center
- Fully automatic injection molding machine
- Gathering Topstar
- giant injection molding machine
- GMU-600 5-Axis Machining Center
- Granulating & Recycling System
- Heavy duty injection molding machine
- Honeycomb rotor dehumidifier
- horizontal injection molding machine
- Horizontal Injection Molding Machines
- Horizontal Injection Moulding Machine
- Horizontal Mixer manufacturer
- How The CNC Machine Works
- hybrid injection molding machine
- hydraulic injection molding machine
- Hydraulic Injection Molding Machines
- in this article
- Industrial robot
- Industrial Robot Chinese brand
- industrial robot parts
- industrial robot supplier
- Industrial robots
- Industry Chain
- Injection Manipulator
- Injection molding
- Injection molding automation
- Injection Molding Automation Solution
- injection molding dryer
- Injection molding equipment
- injection molding hopper dryer
- Injection molding machine
- injection molding machine brand
- Injection Molding Machine Factory
- Injection Molding Machine Manufacture
- Injection molding machine manufacturer
- injection molding machine manufacturers
- Injection molding machine procurement
- injection molding machine robotic arm
- injection molding machine with a robot
- Injection molding machines
- injection molding material dehumidifying
- injection molding plant
- Injection Molding Robot
- injection molding robot arm
- Injection molding robot automation
- Injection molding robotic arm
- injection molding robots
- Injection Moulding Robots
- Injection Robot
- Injection robot arm
- Injection robot manufacturer
- Injection robot wholesale
- injection robots
- intelligent injection molding machines
- Introducing Injection Robot
- It is the best choice for drying large quantities of material at once. Cabinetmakers use these machines because they are fast
- large injection molding machine
- Learn what industrial automation and robotics is
- low speed sound-proof granulator
- machine plastic molding
- make sure to add some! Improvements (2) Keyphrase in introduction: Your keyphrase or its synonyms appear in the first paragraph of the copy
- manipulator machine
- manufacturing
- micro injection molding machine
- middle speed granulator
- Mini CNC machine manufacturers.
- Mold Temperature Control System
- mold temperature controller
- molding material Dehumidifying System
- mould temperature controller
- mould temperature controllers
- New electric injection molding machine
- nitrogen dryer manufacturer
- nitrogen dryer system manufacturer
- Oil type mold temperature controller
- open day
- Outbound links: No outbound links appear in this page. Add some! Images: No images appear on this page. Add some! Internal links: No internal links appear in this page
- PET Preform injection molding
- phone case maker machine
- phone case making machine
- plastic bottle making machine
- plastic bottle manufacturing
- plastic bucket making machine
- plastic bucket manufacturing
- Plastic chair making machine
- plastic forming equipment
- plastic hopper dryer
- plastic injection machine
- plastic injection machines
- plastic injection molding
- Plastic injection molding equipment
- Plastic injection molding machine
- Plastic Injection Molding Machines
- plastic injection robot
- Plastic Molding machine
- Plastic Molding Machines
- plastic molding press
- plastic phone case making machine
- plastic-molding machine
- powerful granulator
- Powerful Type Sound-Proof Granulator
- production of plastic seats
- Robot injection molding
- robot injection molding machine
- robot manufacturing companies
- Robotic arm for injection molding machine
- robotic injection molding machines
- robotics in injection molding
- SCARA robot
- SCARA robots
- Service-oriented manufacturing
- Servo Cylinder Robot
- servo driven robot
- Servo Driven Robots
- servo injection robots
- Servo-Driven Robot
- Setup of injection machine
- Silicone Injection Molding Machine
- six-axis industrial robot
- Stainless Hopper Dryer
- Stainless Hopper Dryers
- star club
- swing arm robot
- the choice between servo-driven robots and hydraulic robots will have a certain impact on efficiency
- the most popular injection molding machine
- the type of injection molding robot
- toggle clamp injection molding machine
- Toggle Hydraulic Injection Molding Machines
- toggle injection molding machine
- Top 10 brands of injection robots
- Topstar
- Topstar Engineering
- Topstar Industrial Robots
- Topstar injection molding intelligent
- Topstar Scara Robots
- Useful Injection molding machine
- Vertical machining centers
- volumetric type blender
- water chiller
- water distributor
- Water Type MoldTemperature Controller
- We often face choices when performing injection molding. We will choose the type of injection molding machine
- wholesale of injection molding machines
- x carve CNC