How can we improve the safety of the injection robot during operation?
2025/03/14 By Topstar
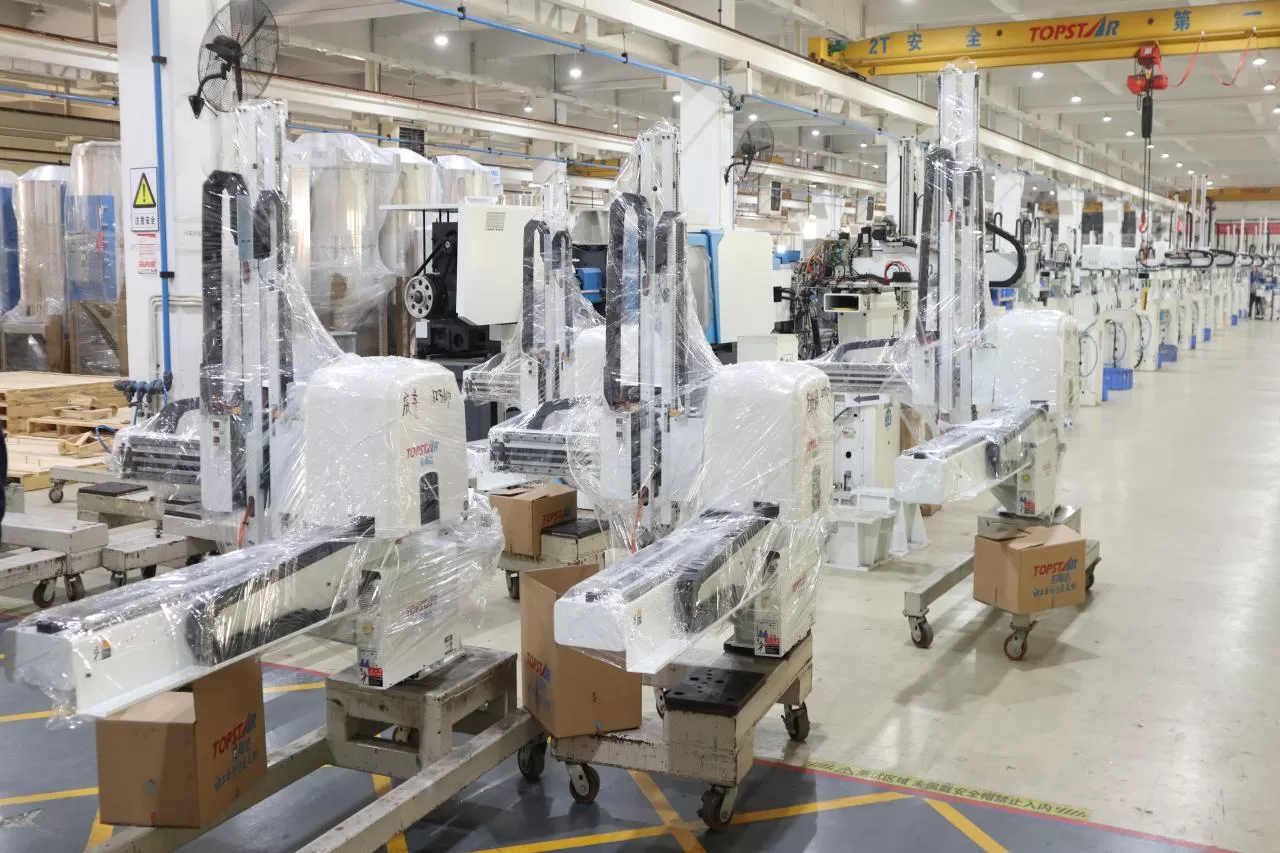
In injection molding operations that require high speed and high precision, these injection robots are prone to torque overloads – that is, the torque applied during operation exceeds the preset value. This situation can cause a series of safety issues, including potential damage to the mold, ejector pins, and even the final product itself. The risks are multiplied when injection robot encounter torque values that exceed their safe operating thresholds. Excessive torque can pressure the machine’s key components, causing premature wear or even catastrophic failure. This risk is not limited to mechanical damage but can also compromise production quality, increase downtime, and increase safety hazards for equipment and personnel.
Impact of Torque Overload of Injection Robot on Injection Molding Operations
Various adverse effects may occur when injection robots encounter torque values that exceed the set limits. First, excessive torque puts pressure on the mold, causing it to deform or even crack. The mold is one of the most expensive parts in the injection molding process, and mold damage can lead to costly repairs or replacements, not to mention production delays. In addition, excessive torque can also affect the ejector pins in the injection molding machine. Ejector pin damage hinders the demolding process and causes inaccurate final product dimensions, affecting the overall quality.
Furthermore, when torque overload occurs, it often indicates that the system is operating under conditions not anticipated during the design phase. These unexpected loads can come from material inconsistencies, operating temperature changes, or external disturbances. These factors can cause the injection molding robot to apply forces beyond its safe capabilities. Without proper protection, this situation can lead to a cascade of failures that compromise the structural integrity of the injection molding machine and the injection robot and increase the risk of injury to operators close to the faulty equipment.
Mitigating the risk of torque overload on injection robot through joint soft floating
When the injection robot faces torque values exceeding a set threshold, joint soft floating is designed to provide a controlled adaptive response, preventing excessive stress from transmitting to sensitive components. Joint soft floating allows a limited degree of movement or “float” when subjected to forces that exceed normal operating levels. This floating mechanism acts as a buffer, absorbing and redistributing excess energy from torque overload. In effect, when the injection molding robot encounters an unexpected increase in torque, the soft floating joint deforms slightly, allowing the system to withstand the excessive force temporarily. This controlled deformation helps mitigate the impact on the mold, ejector, and other critical components of the injection molding machine.
Their design combines multiple layers and damping elements to absorb shocks and reduce peak force transmission. As a result, injection robots benefit from significantly increasing their tolerance to torque overloads without compromising the structural integrity of their components.
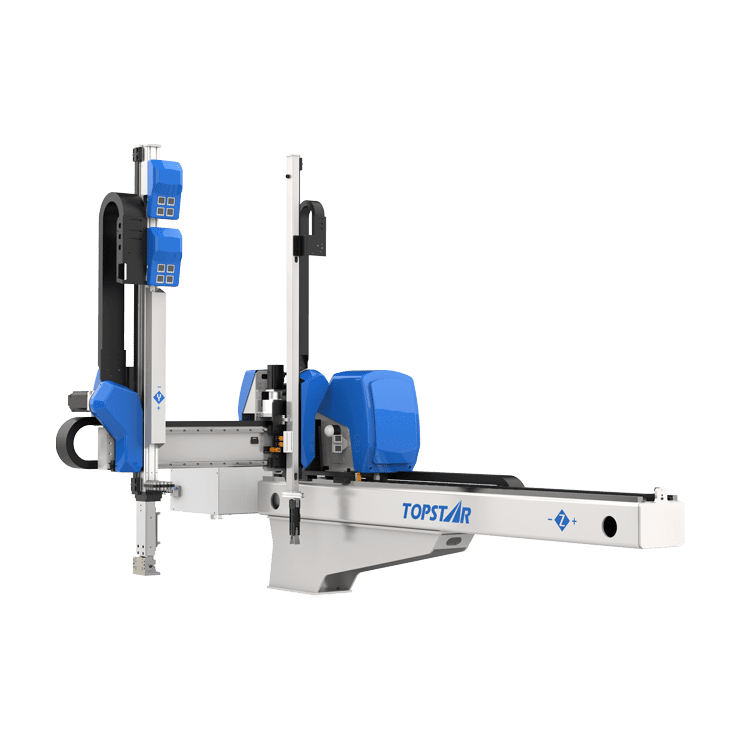
Benefits of soft floating joint protection for mold and ejector safety
When a torque overload occurs on an injection robot, the risk of mold damage is one of the main issues, as they are subject to tremendous stress during molding. Even slight deformations or cracks in the mold can lead to low production efficiency, increased scrap rates, and reduced product quality. With soft floating joints, injection molding robots absorb and mitigate the effects of torque peaks, preventing forces from being directly transmitted to the mold.
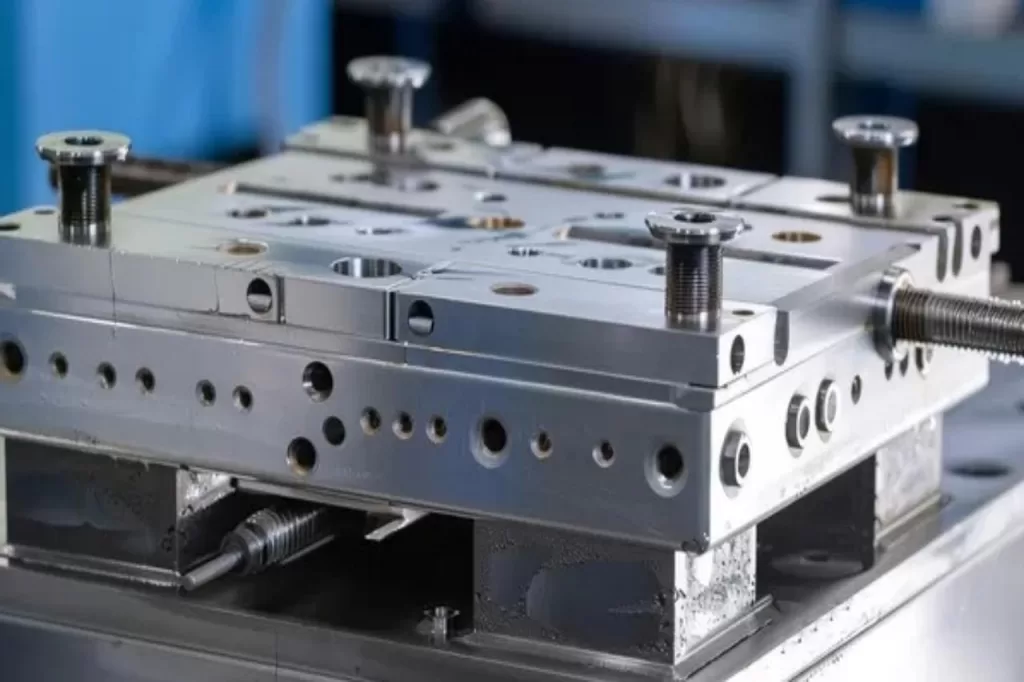
Similarly, ejectors are also susceptible to damage when torque overloads occur, whether bending, breaking, or wearing, which can disrupt molding and cause product defects. By adopting soft floating joints, injection robots can better cope with unexpected loads, minimizing the risk of ejector damage. Reducing mechanical stress maintains the ejector’s functionality and ensures consistent product quality over long-term production processes.
Improve production efficiency and equipment stability through advanced protection.
When the injection robot operates within the safe torque limit, it significantly reduces the risk of unexpected downtime or failure. This means the production line can run continuously without frequent interruptions due to equipment failure or emergency maintenance. The increase in uptime directly affects production throughput, allowing manufacturers to meet higher order volumes and reduce total cycle time. Maintaining stable, uninterrupted operations is invaluable in an industry where efficiency is a key competitive factor. The use of joint soft floating protects key components and plays a vital role in stabilizing the performance of injection molding robots over the long term. By mitigating the effects of torque overload, the joint helps maintain consistent force distribution in the mechanical system of the injection robot. This consistency reduces the accumulated stress on components such as molds and ejectors, extending their service life.
Optional personnel protection configuration to reduce accidental injuries
The safe operation of injection robots not only prevents mechanical failures but also protects operators and maintenance personnel. To better solve this problem, Topstar’s injection molding robots have optional personnel protection configurations that greatly reduce the risk of accidental injuries during operation.
Accidental contact with a moving injection robot can cause serious injuries, especially when the machine runs at high speeds and immense torque loads. Recognizing this risk, our engineering team developed and integrated a comprehensive safety suite into the design of the injection molding robot. This optional configuration includes safety interlocks, emergency stop systems, and protective barriers to prevent personnel from accidentally contacting moving parts. The intelligent sensor system continuously monitors the injection robot’s surroundings. These sensors detect the presence of human operators in restricted areas and automatically trigger safety protocols when they identify potential hazards.
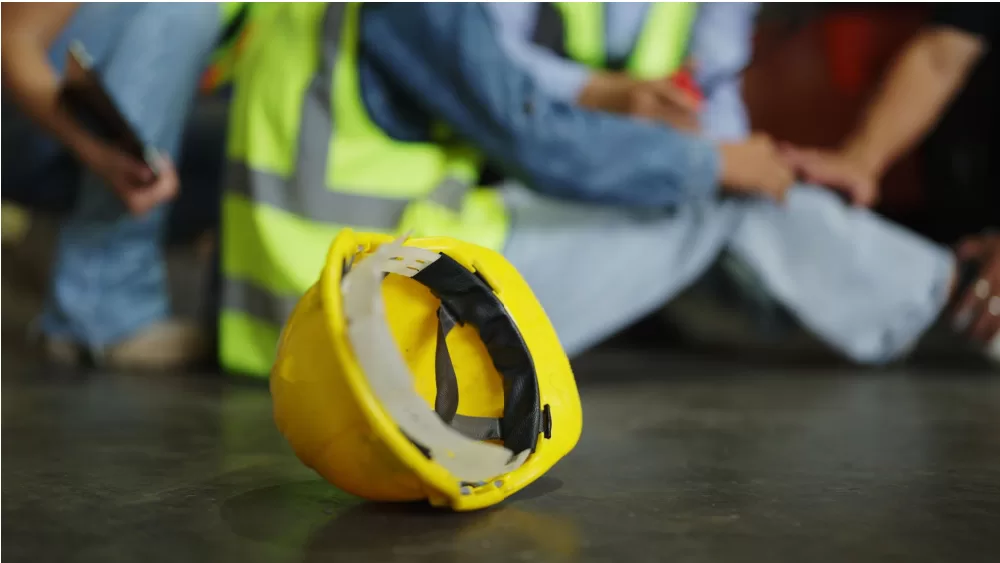
Improved operational safety
The joints’ soft floating technology effectively buffers excessive torque, thereby protecting the mold and ejector pins from excessive stress. This protection mechanism’s benefits are not limited to maintaining the integrity of the equipment; it also helps maintain stable product quality and reduce unplanned downtime. The optional personnel protection configuration further improves the safety of the working environment.
TRENDING POSTS
- What factors can cause delays in the injection molding process of plastic molding machine? 2025/03/14
- Exhibition Review| Topstar participates in InterPlas Thailand 2024 2025/03/14
- Star Case | Topstar helps Santong upgrade its intelligent plant 2025/03/14
- Topstar Special | National Science and Technology Workers Day 2025/03/14
HOT TOPIC
- 3 in 1 Compact Dehumidifying Dryer
- 5-axis CNC machine
- accuracy
- Air Chillers
- all electric injection molding machine
- All-electric injection molding machines
- and overall production quality. Therefore
- AP-RubberPlas
- automated injection molding machine
- Automation changed engineering
- automation of injection molding robots
- auxiliary machine
- Bench Injection Molding Machine
- Cabinet dryer manufacturers
- Cabinet dryers
- CNC Drilling Machine
- CNC Drilling Machines
- cnc engraving machine manufacturer
- cnc laser cutting machine manufacturer
- CNC machine
- CNC Machine Center
- CNC Machine for Sale
- CNC Machine Manufacturing
- CNC Machine Tool
- CNC machine tool product
- CNC Machining Center
- CNC wood carving machine
- Cooling system
- Cross-Walking Single Axis Servo Cylinder Robot
- Cross-Walking Single-Axis Servo Cylinder Robot
- Cross-Walking Three-Axis/Five-Axis Servo Driven Robot
- cross-walking three-axis/five-axis servo-driven robot
- Dehumidifier Dryer
- delta parallel robot
- Desktop Injection Molding Machine
- Desktop injection molding machines
- Desktop Molding Machine
- desktop plastic injection machine
- Desktop Plastic Injection Molding Machine
- direct clamp injection molding machine
- Direct clamp injection molding machines
- Dosing & mixing system
- Drilling Centers
- Drying and dehumidification system
- drying and dehumidifying equipment
- Drying and Dehumidifying System
- drying system
- effective and efficient. Cabinet dryers are also used in other industries where large quantities of material need to be dried
- efficient injection molding machine
- elbow hydraulic injection molding machines
- electric injection molding machine
- electric injection molding machines
- etc. Among injection molding robots
- exhibition
- features of CNC machine
- Feeding And Conveying System
- Five Axis Machine Center
- Fully automatic injection molding machine
- Gathering Topstar
- giant injection molding machine
- GMU-600 5-Axis Machining Center
- Granulating & Recycling System
- Heavy duty injection molding machine
- Honeycomb rotor dehumidifier
- horizontal injection molding machine
- Horizontal Injection Molding Machines
- Horizontal Injection Moulding Machine
- Horizontal Mixer manufacturer
- How The CNC Machine Works
- hybrid injection molding machine
- hydraulic injection molding machine
- Hydraulic Injection Molding Machines
- in this article
- Industrial robot
- Industrial Robot Chinese brand
- industrial robot parts
- industrial robot supplier
- Industrial robots
- Industry Chain
- Injection Manipulator
- Injection molding
- Injection molding automation
- Injection Molding Automation Solution
- injection molding dryer
- Injection molding equipment
- injection molding hopper dryer
- Injection molding machine
- injection molding machine brand
- Injection Molding Machine Factory
- Injection Molding Machine Manufacture
- Injection molding machine manufacturer
- injection molding machine manufacturers
- Injection molding machine procurement
- injection molding machine robotic arm
- injection molding machine with a robot
- Injection molding machines
- injection molding material dehumidifying
- injection molding plant
- Injection Molding Robot
- injection molding robot arm
- Injection molding robot automation
- Injection molding robotic arm
- injection molding robots
- Injection Moulding Robots
- Injection Robot
- Injection robot arm
- Injection robot manufacturer
- Injection robot wholesale
- injection robots
- intelligent injection molding machines
- Introducing Injection Robot
- It is the best choice for drying large quantities of material at once. Cabinetmakers use these machines because they are fast
- large injection molding machine
- Learn what industrial automation and robotics is
- low speed sound-proof granulator
- machine plastic molding
- make sure to add some! Improvements (2) Keyphrase in introduction: Your keyphrase or its synonyms appear in the first paragraph of the copy
- manipulator machine
- manufacturing
- micro injection molding machine
- middle speed granulator
- Mini CNC machine manufacturers.
- Mold Temperature Control System
- mold temperature controller
- molding material Dehumidifying System
- mould temperature controller
- mould temperature controllers
- New electric injection molding machine
- nitrogen dryer manufacturer
- nitrogen dryer system manufacturer
- Oil type mold temperature controller
- open day
- Outbound links: No outbound links appear in this page. Add some! Images: No images appear on this page. Add some! Internal links: No internal links appear in this page
- PET Preform injection molding
- phone case maker machine
- phone case making machine
- plastic bottle making machine
- plastic bottle manufacturing
- plastic bucket making machine
- plastic bucket manufacturing
- Plastic chair making machine
- plastic forming equipment
- plastic hopper dryer
- plastic injection machine
- plastic injection machines
- plastic injection molding
- Plastic injection molding equipment
- Plastic injection molding machine
- Plastic Injection Molding Machines
- plastic injection robot
- Plastic Molding machine
- Plastic Molding Machines
- plastic molding press
- plastic phone case making machine
- plastic-molding machine
- powerful granulator
- Powerful Type Sound-Proof Granulator
- production of plastic seats
- Robot injection molding
- robot injection molding machine
- robot manufacturing companies
- Robotic arm for injection molding machine
- robotic injection molding machines
- robotics in injection molding
- SCARA robot
- SCARA robots
- Service-oriented manufacturing
- Servo Cylinder Robot
- servo driven robot
- Servo Driven Robots
- servo injection robots
- Servo-Driven Robot
- Setup of injection machine
- Silicone Injection Molding Machine
- six-axis industrial robot
- Stainless Hopper Dryer
- Stainless Hopper Dryers
- star club
- swing arm robot
- the choice between servo-driven robots and hydraulic robots will have a certain impact on efficiency
- the most popular injection molding machine
- the type of injection molding robot
- toggle clamp injection molding machine
- Toggle Hydraulic Injection Molding Machines
- toggle injection molding machine
- Top 10 brands of injection robots
- Topstar
- Topstar Engineering
- Topstar Industrial Robots
- Topstar injection molding intelligent
- Topstar Scara Robots
- Useful Injection molding machine
- Vertical machining centers
- volumetric type blender
- water chiller
- water distributor
- Water Type MoldTemperature Controller
- We often face choices when performing injection molding. We will choose the type of injection molding machine
- wholesale of injection molding machines
- x carve CNC