Improving injection molding performance at North American sites with Topstar’s water chiller solutions
2025/03/10 By Topstar
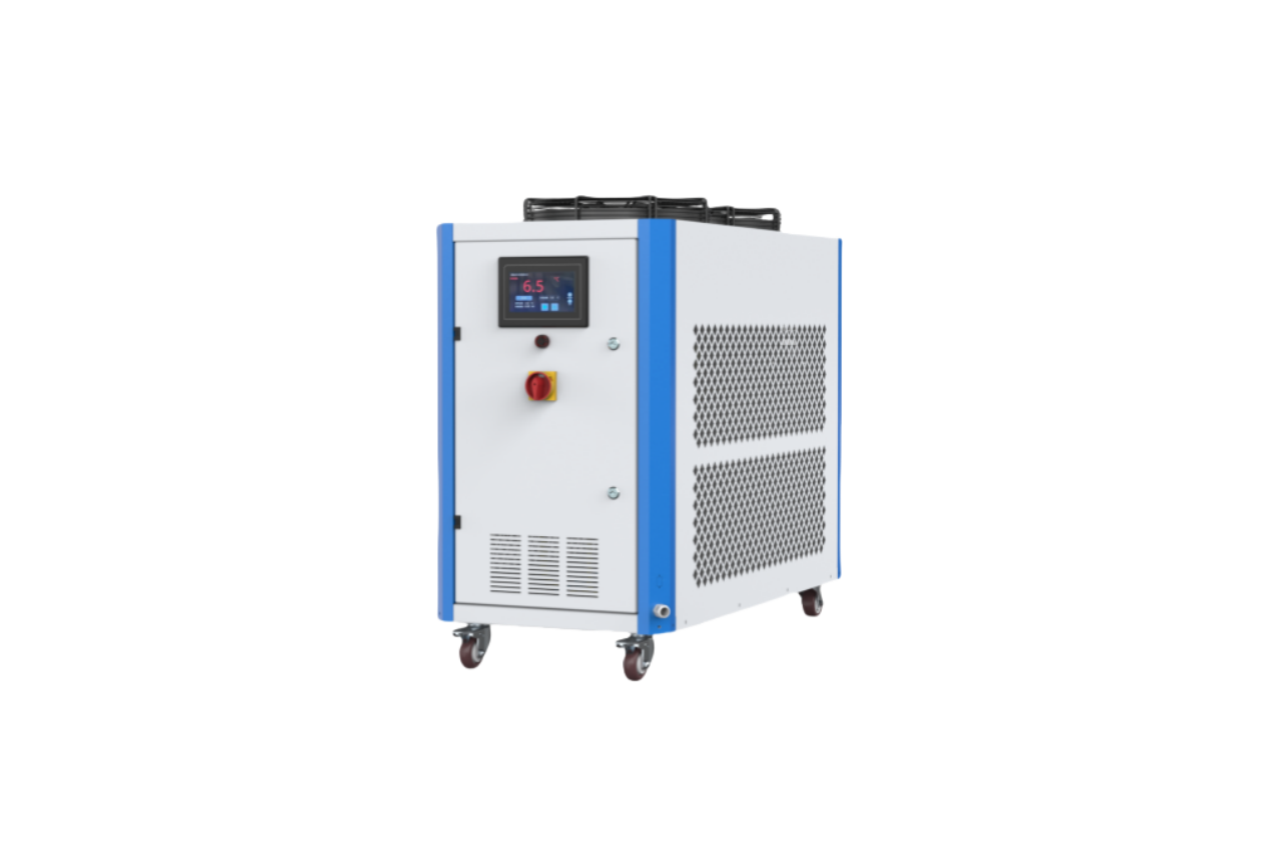
Injection molding plants across North America often face high energy costs when using water chillers. Some traditional water chillers are inefficient, resulting in a surge in operating expenses. In addition, hard water in some parts of North America (such as the Great Lakes) causes scale accumulation that results in a 20%-30% drop in heat transfer efficiency, severe pipe corrosion, and a lack of remote monitoring and inaccurate temperature control that results in temperature deviations, with downtime repairs taking an average of 4-8 hours. Topstar has designed innovative water chiller solutions specifically to address these challenges. Our systems combine precise temperature control, strong safety mechanisms, and energy-saving innovations to improve productivity in industrial environments across North America.
How do Topstar’s water chiller improve temperature stability and injection molding performance?
Continuous cooling is essential for defect-free injection molding. Topstar’s water chiller systems use fully computerized temperature controllers to keep water temperatures within a tight range of 5–35°C (±0.5°C). This eliminates thermal fluctuations that can cause warping, dents, or incomplete filling of molded parts.
The intuitive touchscreen interface allows operators to set parameters in 30 seconds and monitor cooling performance in real-time. Unlike outdated manual systems, our automated controls adapt to ambient temperature changes, material changes, or production speeds – ensuring repeatable results across shifts. The entire control system integrates seamlessly with the injection molding machine’s control system, enabling remote monitoring and data logging, further improving the reliability of the injection molding process. Operators benefit from real-time alerts and historical data, which aids in rapid troubleshooting and continuous process improvement. By consistently achieving and maintaining optimal temperatures, manufacturers can reduce downtime caused by thermal fluctuations.
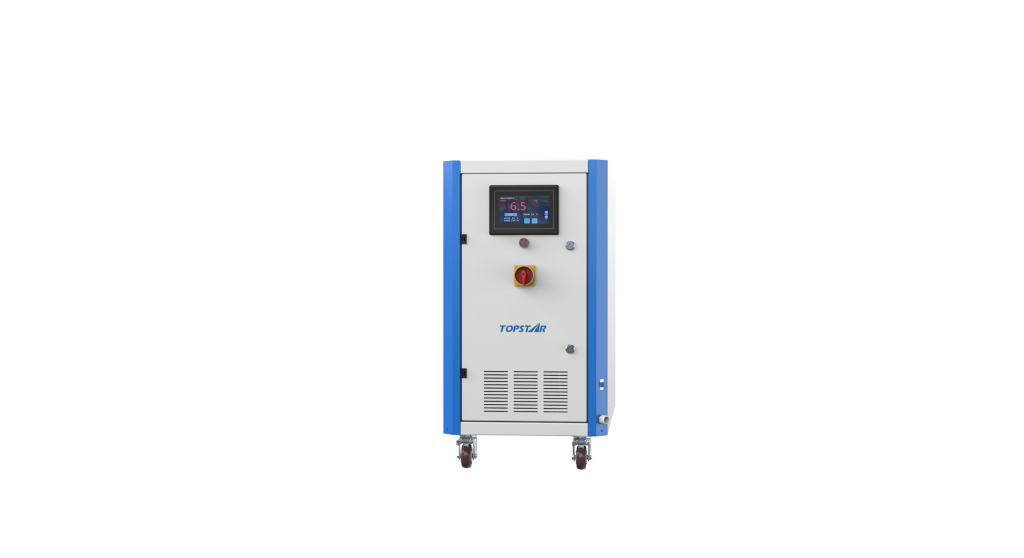
Simplified Operations with Thermostat Technology
At the heart of Topstar’s water chiller solutions is an advanced, fully computerized thermostat, which sets these systems apart from traditional cooling equipment. The computerized thermostat is programmed to maintain water temperatures between 5°C and 35°C. In injection molding, the ability to fine-tune temperature settings ensures that molten plastic cools at the correct rate, which is critical to producing parts with optimal structural integrity and surface finish. Another key benefit of a computerized thermostat is its role in energy management. The water chiller can minimize unnecessary power consumption by operating at peak efficiency without compromising performance. This is particularly beneficial in large injection molding operations, and the advanced programming capabilities of the thermostat allow for the integration of energy-saving modes that adjust cooling intensity based on real-time production requirements.
Imported high-quality compressors and pumps for improved efficiency
The high-efficiency, safe, and durable performance benefits are attributed to using imported high-quality compressors and pumps. These key components are the power source of the water chiller, ensuring that the unit operates quietly, safely, and with minimal energy consumption. The high-quality compressors used in Topstar water chillers provide stable performance even under heavy-duty operating conditions. With compression power ranging from 5HP to 50HP, these compressors operate at peak efficiency while maintaining low noise levels. In addition to the compressors, Topstar water chillers’ pumps ensure that cooling water is evenly distributed throughout the injection molding equipment. The superior design of these pumps allows them to operate with minimal vibration and noise, further contributing to a safer and more comfortable working environment. In addition, the energy-saving operation of these pumps helps reduce the water chiller’s overall power consumption.
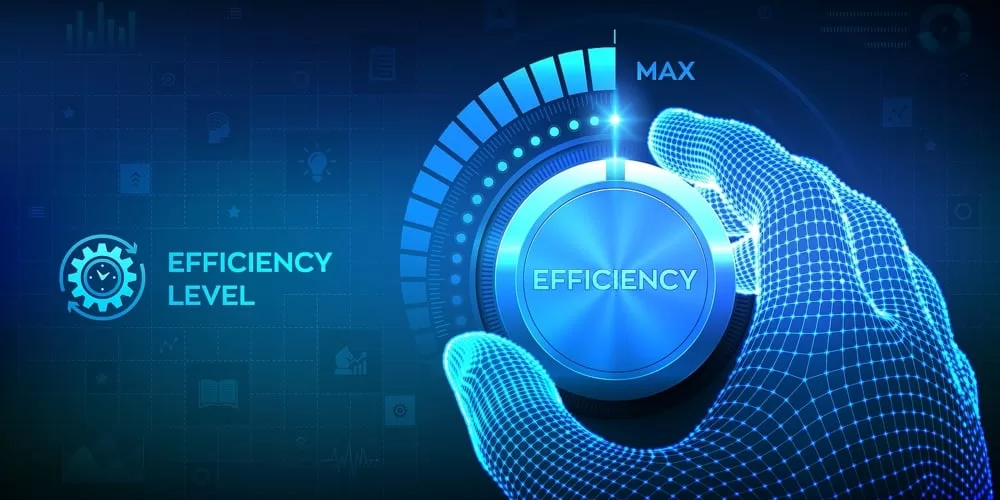
304 Stainless Steel Insulated Tanks in water chiller
The 304 stainless steel insulated tanks built into Topstar’s chillers extend the system’s life and simplify maintenance. The insulated tanks withstand harsh chemicals, UV exposure, and extreme temperatures (-20°C to 50°C). Their smooth interior surface prevents scale buildup and reduces cleaning time by 40% compared to galvanized tanks.
Insulated tanks maintain a stable water temperature throughout the cooling cycle. By reducing heat loss and protecting the water from external temperature fluctuations, the tanks help ensure that the cooling process remains efficient and consistent. From a maintenance perspective, the tanks’ 304 stainless steel construction offers significant advantages, as stainless steel is resistant to rust and corrosion and has a smooth, non-porous surface that is easy to clean and disinfect.
Built-in safety features for increased safety
Unplanned downtime in production costs North American plastics manufacturers hundreds of dollars per minute on average. In the chiller design provided by Topstar, in addition to current overload protection and voltage control, the system is equipped with an electronic time-delay safety device to prevent sudden power surges or drops from affecting performance. The current overload protection stops operation during power surges, and the electronic time-delay safety device (adjustable from 3-10 minutes) ensures stable restart after power failure. If a fault occurs, the chiller will immediately sound an alarm and display the cause of the fault, allowing the operator to take corrective measures quickly. This active fault detection system minimizes downtime and resolves problems before they affect the injection molding process. The chiller protects valuable equipment and the entire production line by maintaining a high level of process safety.
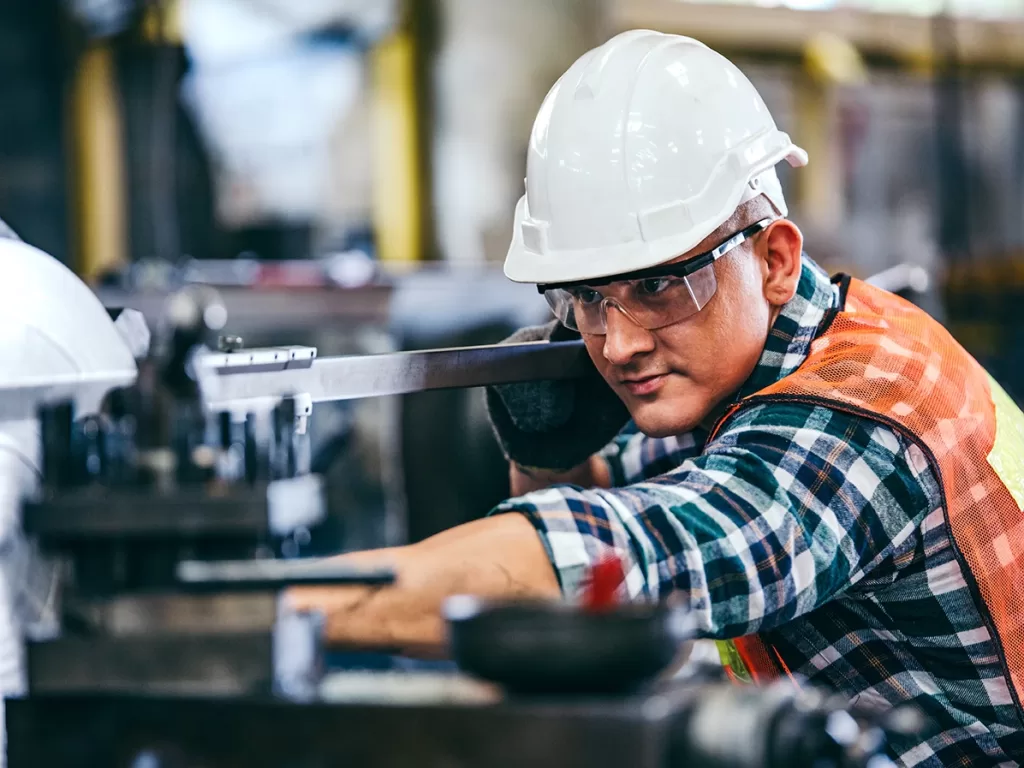
Comprehensively improve overall operational performance.
Topstar Technology’s water chiller solutions have demonstrated their ability to improve the injection molding performance of North American factories by providing precise temperature control, powerful safety features, and significant energy savings. By integrating intelligent temperature control, comprehensive protection systems, durable 304 stainless steel water tanks, and imported high-quality compressors and pumps, Topstar can comprehensively improve the efficiency and operational performance of the North American injection molding industry.
TRENDING POSTS
- What factors can cause delays in the injection molding process of plastic molding machine? 2025/03/10
- Exhibition Review| Topstar participates in InterPlas Thailand 2024 2025/03/10
- Star Case | Topstar helps Santong upgrade its intelligent plant 2025/03/10
- Topstar Special | National Science and Technology Workers Day 2025/03/10
HOT TOPIC
- 3 in 1 Compact Dehumidifying Dryer
- 5-axis CNC machine
- accuracy
- Air Chillers
- all electric injection molding machine
- All-electric injection molding machines
- and overall production quality. Therefore
- AP-RubberPlas
- automated injection molding machine
- Automation changed engineering
- automation of injection molding robots
- auxiliary machine
- Bench Injection Molding Machine
- Cabinet dryer manufacturers
- Cabinet dryers
- CNC Drilling Machine
- CNC Drilling Machines
- cnc engraving machine manufacturer
- cnc laser cutting machine manufacturer
- CNC machine
- CNC Machine Center
- CNC Machine for Sale
- CNC Machine Manufacturing
- CNC Machine Tool
- CNC machine tool product
- CNC Machining Center
- CNC wood carving machine
- Cooling system
- Cross-Walking Single Axis Servo Cylinder Robot
- Cross-Walking Single-Axis Servo Cylinder Robot
- Cross-Walking Three-Axis/Five-Axis Servo Driven Robot
- cross-walking three-axis/five-axis servo-driven robot
- Dehumidifier Dryer
- delta parallel robot
- Desktop Injection Molding Machine
- Desktop injection molding machines
- Desktop Molding Machine
- desktop plastic injection machine
- Desktop Plastic Injection Molding Machine
- direct clamp injection molding machine
- Direct clamp injection molding machines
- Dosing & mixing system
- Drilling Centers
- Drying and dehumidification system
- drying and dehumidifying equipment
- Drying and Dehumidifying System
- drying system
- effective and efficient. Cabinet dryers are also used in other industries where large quantities of material need to be dried
- efficient injection molding machine
- elbow hydraulic injection molding machines
- electric injection molding machine
- electric injection molding machines
- etc. Among injection molding robots
- exhibition
- features of CNC machine
- Feeding And Conveying System
- Five Axis Machine Center
- Fully automatic injection molding machine
- Gathering Topstar
- giant injection molding machine
- GMU-600 5-Axis Machining Center
- Granulating & Recycling System
- Heavy duty injection molding machine
- Honeycomb rotor dehumidifier
- horizontal injection molding machine
- Horizontal Injection Molding Machines
- Horizontal Injection Moulding Machine
- Horizontal Mixer manufacturer
- How The CNC Machine Works
- hybrid injection molding machine
- hydraulic injection molding machine
- Hydraulic Injection Molding Machines
- in this article
- Industrial robot
- Industrial Robot Chinese brand
- industrial robot parts
- industrial robot supplier
- Industrial robots
- Industry Chain
- Injection Manipulator
- Injection molding
- Injection molding automation
- Injection Molding Automation Solution
- injection molding dryer
- Injection molding equipment
- injection molding hopper dryer
- Injection molding machine
- injection molding machine brand
- Injection Molding Machine Factory
- Injection Molding Machine Manufacture
- Injection molding machine manufacturer
- injection molding machine manufacturers
- Injection molding machine procurement
- injection molding machine robotic arm
- injection molding machine with a robot
- Injection molding machines
- injection molding material dehumidifying
- injection molding plant
- Injection Molding Robot
- injection molding robot arm
- Injection molding robot automation
- Injection molding robotic arm
- injection molding robots
- Injection Moulding Robots
- Injection Robot
- Injection robot arm
- Injection robot manufacturer
- Injection robot wholesale
- injection robots
- intelligent injection molding machines
- Introducing Injection Robot
- It is the best choice for drying large quantities of material at once. Cabinetmakers use these machines because they are fast
- large injection molding machine
- Learn what industrial automation and robotics is
- low speed sound-proof granulator
- machine plastic molding
- make sure to add some! Improvements (2) Keyphrase in introduction: Your keyphrase or its synonyms appear in the first paragraph of the copy
- manipulator machine
- manufacturing
- micro injection molding machine
- middle speed granulator
- Mini CNC machine manufacturers.
- Mold Temperature Control System
- mold temperature controller
- molding material Dehumidifying System
- mould temperature controller
- mould temperature controllers
- New electric injection molding machine
- nitrogen dryer manufacturer
- nitrogen dryer system manufacturer
- Oil type mold temperature controller
- open day
- Outbound links: No outbound links appear in this page. Add some! Images: No images appear on this page. Add some! Internal links: No internal links appear in this page
- PET Preform injection molding
- phone case maker machine
- phone case making machine
- plastic bottle making machine
- plastic bottle manufacturing
- plastic bucket making machine
- plastic bucket manufacturing
- Plastic chair making machine
- plastic forming equipment
- plastic hopper dryer
- plastic injection machine
- plastic injection machines
- plastic injection molding
- Plastic injection molding equipment
- Plastic injection molding machine
- Plastic Injection Molding Machines
- plastic injection robot
- Plastic Molding machine
- Plastic Molding Machines
- plastic molding press
- plastic phone case making machine
- plastic-molding machine
- powerful granulator
- Powerful Type Sound-Proof Granulator
- production of plastic seats
- Robot injection molding
- robot injection molding machine
- robot manufacturing companies
- Robotic arm for injection molding machine
- robotic injection molding machines
- robotics in injection molding
- SCARA robot
- SCARA robots
- Service-oriented manufacturing
- Servo Cylinder Robot
- servo driven robot
- Servo Driven Robots
- servo injection robots
- Servo-Driven Robot
- Setup of injection machine
- Silicone Injection Molding Machine
- six-axis industrial robot
- Stainless Hopper Dryer
- Stainless Hopper Dryers
- star club
- swing arm robot
- the choice between servo-driven robots and hydraulic robots will have a certain impact on efficiency
- the most popular injection molding machine
- the type of injection molding robot
- toggle clamp injection molding machine
- Toggle Hydraulic Injection Molding Machines
- toggle injection molding machine
- Top 10 brands of injection robots
- Topstar
- Topstar Engineering
- Topstar Industrial Robots
- Topstar injection molding intelligent
- Topstar Scara Robots
- Useful Injection molding machine
- Vertical machining centers
- volumetric type blender
- water chiller
- water distributor
- Water Type MoldTemperature Controller
- We often face choices when performing injection molding. We will choose the type of injection molding machine
- wholesale of injection molding machines
- x carve CNC