Why do North American manufacturers choose Topstar mould temperature controllers for temperature control?
2025/03/05 By Topstar
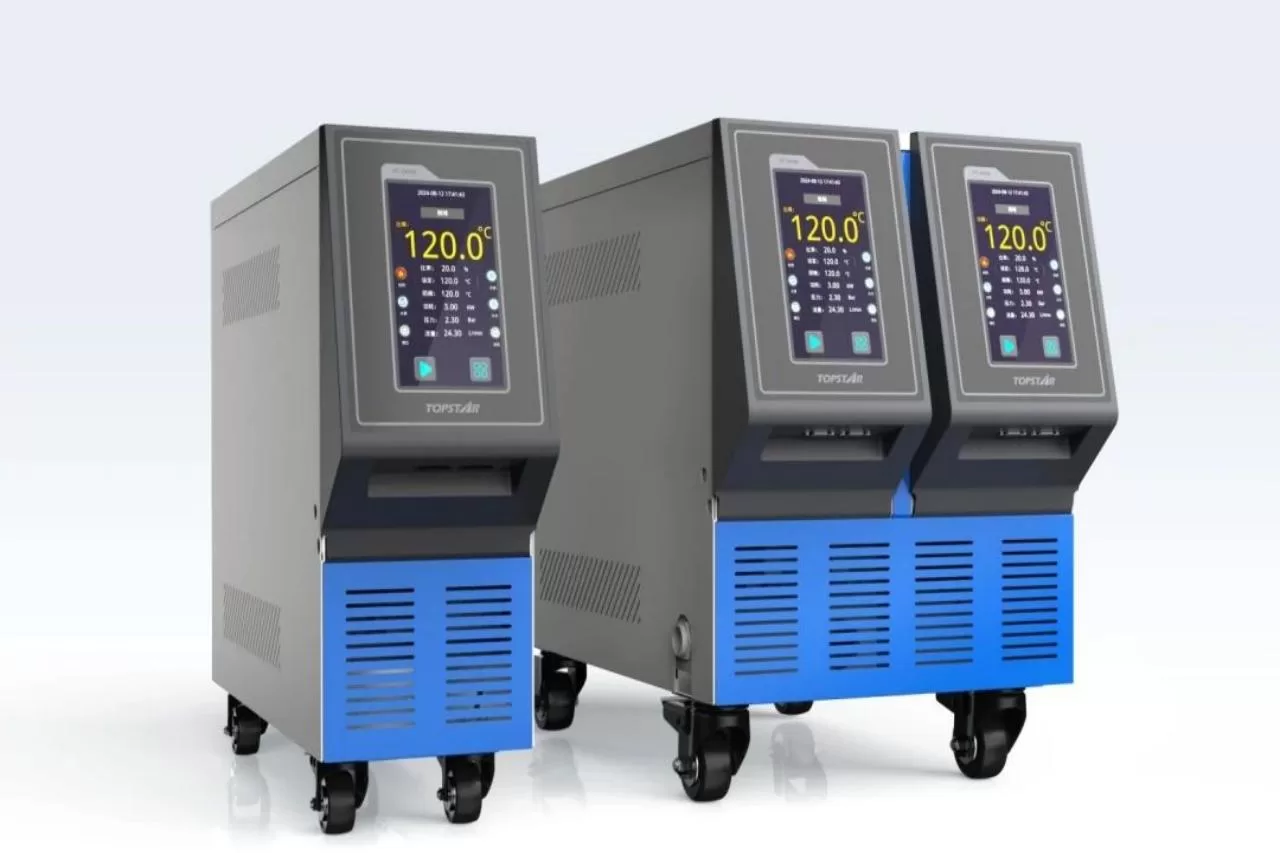
Plastics manufacturers in North America evaluate mould temperature controllers based on their ability to maintain stable temperatures during voltage fluctuations and ambient temperature changes. This level of stability is critical to avoiding product warping or shrinkage, which can lead to costly defects and production downtime. At the same time, they also require accuracy and long-term durability, and even some countries in the region will require the ability to meet the operating time of more than 30,000 hours. They also pay more attention to the anti-corrosion design elements and the intelligence of the equipment.
Stability under fluctuating conditions through the PID algorithm of the mould temperature controllers
Topstar has upgraded the traditional PID control algorithm of the mould temperature controller so that the equipment can automatically adapt to load changes and make intelligent adjustments like unmanned driving. It continuously monitors and adjusts the power supplied to the heating element to ensure that the temperature remains stable within ±0.1°C. This stability is critical to preventing defects such as warping or shrinkage in moulded parts. Even slight deviations in the heating process can cause serious quality problems and affect the structural integrity and appearance of the final product.
Using a sophisticated PID algorithm, Topstar’s mould temperature controller can quickly correct any temperature deviations to maintain uniform heat distribution in the mould. This not only improves product quality but also overall process efficiency. In addition, our system integrates solid-state relays with a response time of only 0.1 seconds, ensuring that PID adjustments are implemented almost immediately. Meet the precision and flexibility that manufacturers in North America need in their operations.
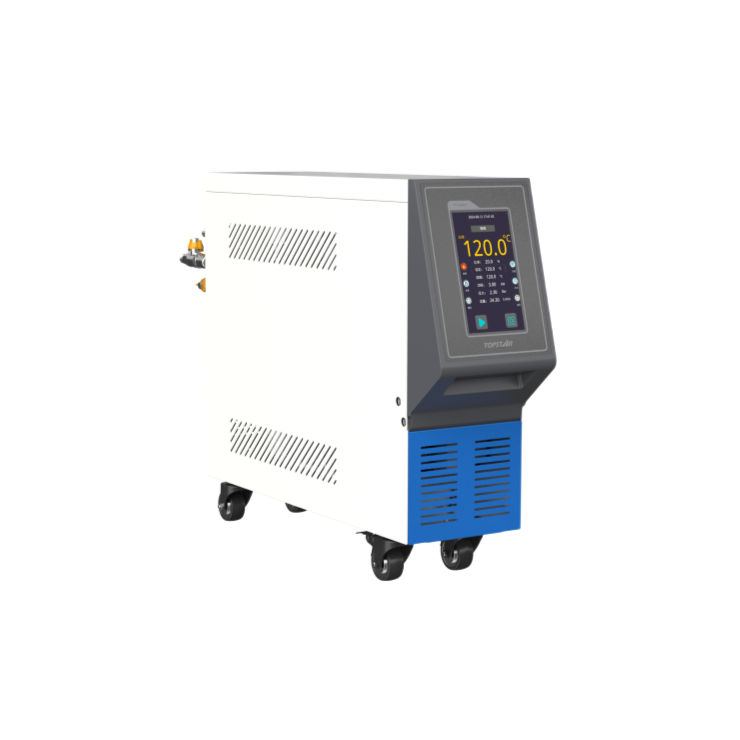
Durability and anti-corrosion design for mould temperature controllers
North American manufacturers have high requirements for equipment durability, such as mould temperature controllers. The most basic requirement is that the controller operate for more than 30,000 hours without performance degradation. Topstar’s mould temperature controllers use stainless steel components in the fluid circuit. Stainless steel pipes can resist corrosion even in environments with moisture, chemical residues or corrosive cleaning agents. This anti-corrosion design extends the system’s service life and reduces the need for frequent maintenance or replacement of components.
In addition, Topstar has newly upgraded the copper heater. Copper offers a double advantage due to its excellent ductility and superb thermal conductivity. Not only does it improve heat transfer efficiency, but impurities in water have a lower tendency to adhere to its surface. This means that even if water quality affects the system, it minimizes scaling, and the copper upgrade increases service life by about 40% and improves efficiency by about 10%.
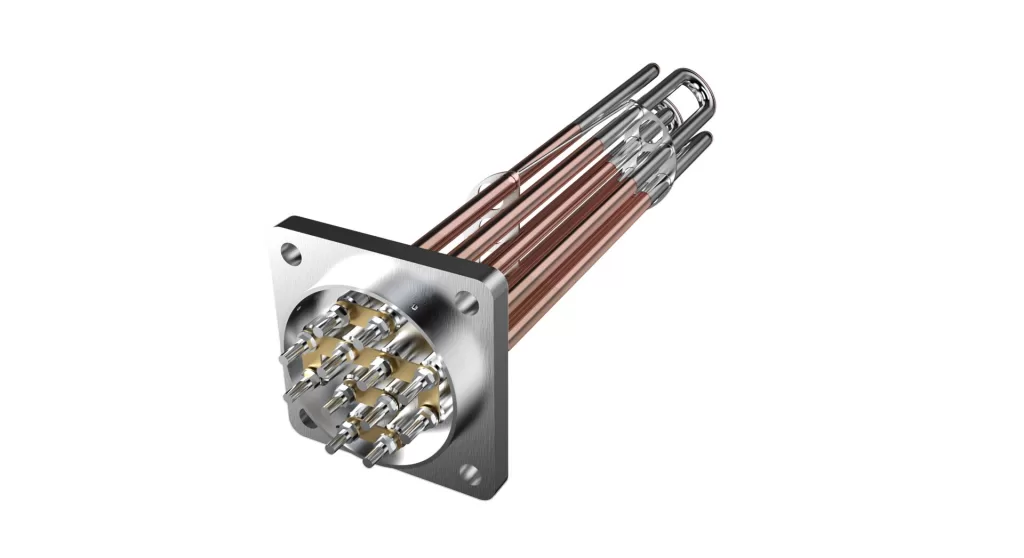
Intelligent integration and data-driven process optimization
In today’s interconnected, bright industrial environment, smart integration is essential for optimizing production processes. Topstar’s mould temperature controller can be interconnected with injection molding machines and other auxiliary equipment to form a fully integrated production system. This interconnected system allows real-time communication and coordination between the various components, ensuring that the production process (from preheating and plasticizing to molding and demolding) is synchronized and optimized. The ability to monitor and control the entire process through a unified interface not only simplifies operation but also improves the performance and reliability of the overall system.
Innovative integration capabilities extend to remote monitoring and control, enabling technical teams to access system data and make adjustments from almost anywhere. This remote access is handy in high-volume manufacturing environments, as rapid response to process deviations can avoid costly production stoppages. At the same time, the system continuously records temperature curves and energy consumption data through integrated data logging functions.
By analyzing these data sets, manufacturers can identify trends, detect anomalies, and implement process improvements to improve product quality and reduce energy consumption.

Trends in digitalization and intelligence
At the digital level, the injection molding machine interconnects with the mold temperature controller, supporting host call signals and seamlessly connecting to the Internet through a digital MES system. This means equipment data will be accessible in real-time on customers’ computers, tablets, mobile phones and other terminals, making management more convenient. In terms of intelligence, in the future, the product R&D center will use artificial intelligence technology to plan and implement equipment health assessment and prediction. Cloud models can identify potential equipment problems in advance and notify customers to perform planned maintenance, minimizing the risk of unexpected downtime and ensuring the continuity and efficiency of the production process.
Bring more precise temperature control and intelligent drive.
Combining cutting-edge hardware, intelligent systems integration, and a deep understanding of market demand, Topstar’s mould temperature controller provides North American manufacturers with robust, future-oriented solutions to meet their precision, durability and intelligent control needs. Whether it is an unstable power grid, poor water quality or endless production schedules, combining the durability of copper with precision-driven artificial intelligence can fully realize quality, efficiency and running time.
TRENDING POSTS
- What factors can cause delays in the injection molding process of plastic molding machine? 2025/03/05
- Exhibition Review| Topstar participates in InterPlas Thailand 2024 2025/03/05
- Star Case | Topstar helps Santong upgrade its intelligent plant 2025/03/05
- Topstar Special | National Science and Technology Workers Day 2025/03/05
HOT TOPIC
- 3 in 1 Compact Dehumidifying Dryer
- 5-axis CNC machine
- accuracy
- Air Chillers
- all electric injection molding machine
- All-electric injection molding machines
- and overall production quality. Therefore
- AP-RubberPlas
- automated injection molding machine
- Automation changed engineering
- automation of injection molding robots
- auxiliary machine
- Bench Injection Molding Machine
- Cabinet dryer manufacturers
- Cabinet dryers
- CNC Drilling Machine
- CNC Drilling Machines
- cnc engraving machine manufacturer
- cnc laser cutting machine manufacturer
- CNC machine
- CNC Machine Center
- CNC Machine for Sale
- CNC Machine Manufacturing
- CNC Machine Tool
- CNC machine tool product
- CNC Machining Center
- CNC wood carving machine
- Cooling system
- Cross-Walking Single Axis Servo Cylinder Robot
- Cross-Walking Single-Axis Servo Cylinder Robot
- Cross-Walking Three-Axis/Five-Axis Servo Driven Robot
- cross-walking three-axis/five-axis servo-driven robot
- Dehumidifier Dryer
- delta parallel robot
- Desktop Injection Molding Machine
- Desktop injection molding machines
- Desktop Molding Machine
- desktop plastic injection machine
- Desktop Plastic Injection Molding Machine
- direct clamp injection molding machine
- Direct clamp injection molding machines
- Dosing & mixing system
- Drilling Centers
- Drying and dehumidification system
- drying and dehumidifying equipment
- Drying and Dehumidifying System
- drying system
- effective and efficient. Cabinet dryers are also used in other industries where large quantities of material need to be dried
- efficient injection molding machine
- elbow hydraulic injection molding machines
- electric injection molding machine
- electric injection molding machines
- etc. Among injection molding robots
- exhibition
- features of CNC machine
- Feeding And Conveying System
- Five Axis Machine Center
- Fully automatic injection molding machine
- Gathering Topstar
- giant injection molding machine
- GMU-600 5-Axis Machining Center
- Granulating & Recycling System
- Heavy duty injection molding machine
- Honeycomb rotor dehumidifier
- horizontal injection molding machine
- Horizontal Injection Molding Machines
- Horizontal Injection Moulding Machine
- Horizontal Mixer manufacturer
- How The CNC Machine Works
- hybrid injection molding machine
- hydraulic injection molding machine
- Hydraulic Injection Molding Machines
- in this article
- Industrial robot
- Industrial Robot Chinese brand
- industrial robot parts
- industrial robot supplier
- Industrial robots
- Industry Chain
- Injection Manipulator
- Injection molding
- Injection molding automation
- Injection Molding Automation Solution
- injection molding dryer
- Injection molding equipment
- injection molding hopper dryer
- Injection molding machine
- injection molding machine brand
- Injection Molding Machine Factory
- Injection Molding Machine Manufacture
- Injection molding machine manufacturer
- injection molding machine manufacturers
- Injection molding machine procurement
- injection molding machine robotic arm
- injection molding machine with a robot
- Injection molding machines
- injection molding material dehumidifying
- injection molding plant
- Injection Molding Robot
- injection molding robot arm
- Injection molding robot automation
- Injection molding robotic arm
- injection molding robots
- Injection Moulding Robots
- Injection Robot
- Injection robot arm
- Injection robot manufacturer
- Injection robot wholesale
- injection robots
- intelligent injection molding machines
- Introducing Injection Robot
- It is the best choice for drying large quantities of material at once. Cabinetmakers use these machines because they are fast
- large injection molding machine
- Learn what industrial automation and robotics is
- low speed sound-proof granulator
- machine plastic molding
- make sure to add some! Improvements (2) Keyphrase in introduction: Your keyphrase or its synonyms appear in the first paragraph of the copy
- manipulator machine
- manufacturing
- micro injection molding machine
- middle speed granulator
- Mini CNC machine manufacturers.
- Mold Temperature Control System
- mold temperature controller
- molding material Dehumidifying System
- mould temperature controller
- mould temperature controllers
- New electric injection molding machine
- nitrogen dryer manufacturer
- nitrogen dryer system manufacturer
- Oil type mold temperature controller
- open day
- Outbound links: No outbound links appear in this page. Add some! Images: No images appear on this page. Add some! Internal links: No internal links appear in this page
- PET Preform injection molding
- phone case maker machine
- phone case making machine
- plastic bottle making machine
- plastic bottle manufacturing
- plastic bucket making machine
- plastic bucket manufacturing
- Plastic chair making machine
- plastic forming equipment
- plastic hopper dryer
- plastic injection machine
- plastic injection machines
- plastic injection molding
- Plastic injection molding equipment
- Plastic injection molding machine
- Plastic Injection Molding Machines
- plastic injection robot
- Plastic Molding machine
- Plastic Molding Machines
- plastic molding press
- plastic phone case making machine
- plastic-molding machine
- powerful granulator
- Powerful Type Sound-Proof Granulator
- production of plastic seats
- Robot injection molding
- robot injection molding machine
- robot manufacturing companies
- Robotic arm for injection molding machine
- robotic injection molding machines
- robotics in injection molding
- SCARA robot
- SCARA robots
- Service-oriented manufacturing
- Servo Cylinder Robot
- servo driven robot
- Servo Driven Robots
- servo injection robots
- Servo-Driven Robot
- Setup of injection machine
- Silicone Injection Molding Machine
- six-axis industrial robot
- Stainless Hopper Dryer
- Stainless Hopper Dryers
- star club
- swing arm robot
- the choice between servo-driven robots and hydraulic robots will have a certain impact on efficiency
- the most popular injection molding machine
- the type of injection molding robot
- toggle clamp injection molding machine
- Toggle Hydraulic Injection Molding Machines
- toggle injection molding machine
- Top 10 brands of injection robots
- Topstar
- Topstar Engineering
- Topstar Industrial Robots
- Topstar injection molding intelligent
- Topstar Scara Robots
- Useful Injection molding machine
- Vertical machining centers
- volumetric type blender
- water chiller
- water distributor
- Water Type MoldTemperature Controller
- We often face choices when performing injection molding. We will choose the type of injection molding machine
- wholesale of injection molding machines
- x carve CNC