Plastic Molding Machine Solutions for Faster Turnaround Times
2025/02/14 By Topstar
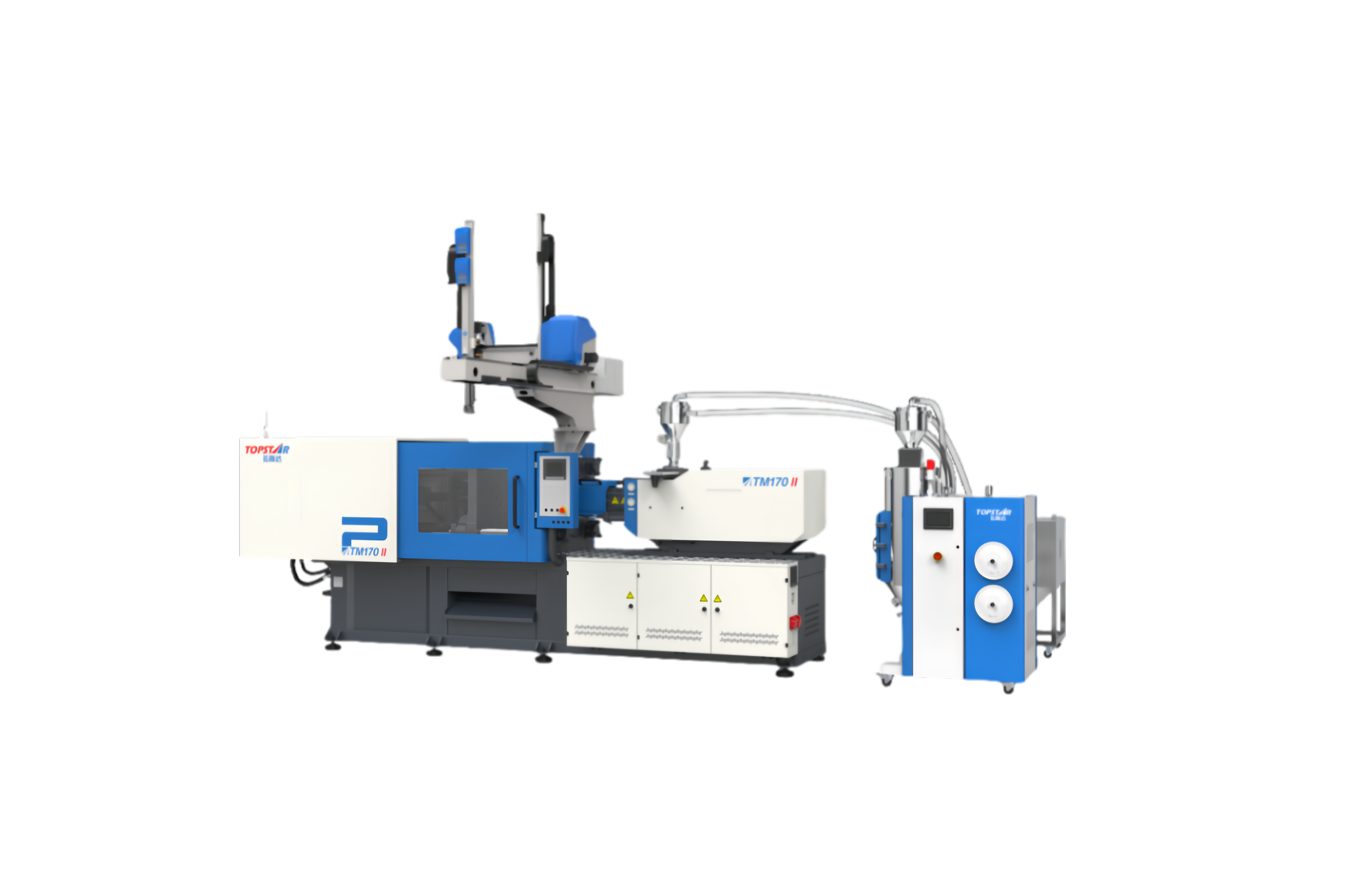
Delays in the injection molding can disrupt the supply chain and increase costs. Due to manual adjustments, traditional plastic molding machines often struggle with inconsistent cycle times, material waste, and frequent downtime. These challenges are exacerbated when customers expect a 20% or more reduction in turnaround time while also keeping defect rates below 5%. Topstar’s TM Series plastic molding machine addresses these pain points head-on. With fully upgraded injection units, clamping mechanisms, and other systems, the TM Series ensures stable, high-speed production. For example, a manufacturer of automotive lamp housings that used traditional plastic molding machines reduced cycle time by 22% and achieved a 96% yield rate after switching to the TM Series.
How does the TM Series plastic molding machine improve speed and precision?
The TM Series’ performance core lies in its fully upgraded injection unit, designed to maximize injection speed, melt speed, and pressure. On the one hand, traditional injection molding machines often suffer from slow screw recovery or uneven melting, resulting in inconsistent fill rates and defects. The TM Series solves this problem with high-torque electroplated screws. In addition, the melt speed has been increased by 10% with the upgrade of the injection station. At the same time, it also has a dynamic pressure control function, which can automatically adjust the injection pressure according to the real-time resin viscosity and mold temperature. For example, when molding thin-walled automotive connectors, the machine increases pressure during filling to prevent cavitation. Then, it reduces pressure during the pressure-holding period to avoid overflow. This adaptability ensures that the cycle time remains stable despite high molding requirements.
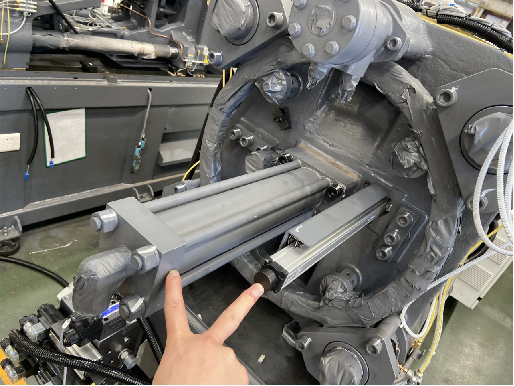
Self-developed control system: speed up the cycle of plastic molding machine
Without precision, speed is meaningless. Topstar’s TM series realizes the communication of the main machine, auxiliary machine, and automation through the self-developed control system, which can optimize each stage of the molding process. We will realize the linkage of a control interface with multiple devices based on the opening of the software system and learn the optimal control of injection molding factors such as temperature, speed, position, pressure, and time through system integration, the combination of injection molding machines and auxiliary machines, and sensor technology. At the same time, it also reduces the operator’s workload of fine-tuning and monitoring the main machine and auxiliary equipment, lowers labor costs, and improves production efficiency. Secondly, Topstar realizes the synchronous linkage of the robot and the mold opening process, shortens the molding cycle, and improves production efficiency through early arrival and precision compensation functions.
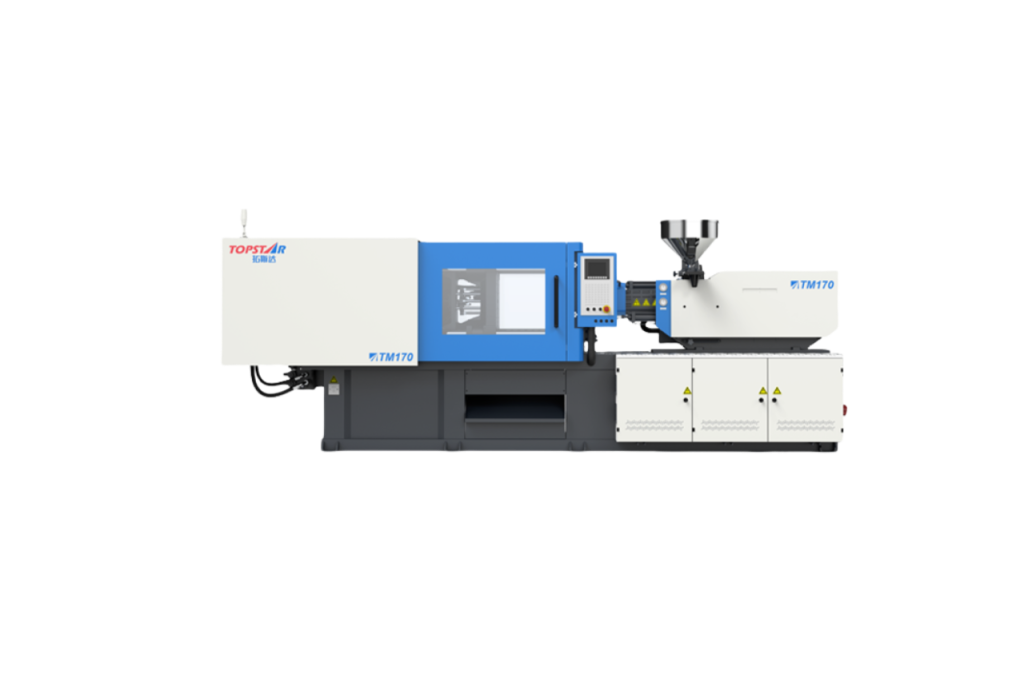
Adaptability and flexibility for different production
Another significant advantage of the TM Series plastic molding machine is its ability to handle various materials and part designs. It comes standard with a chrome-plated screw and temperature control of the feed port, which is suitable for a broader range of plastics and more stable production. Whether producing small components or more significant, complex parts, the machine’s flexibility enables manufacturers to customize the molding process to meet their needs. This flexibility is substantial in industries where product design and material types constantly change. The TM Series can quickly adapt to different requirements, allowing manufacturers to adjust parameters such as mold size, pressure, and cycle time according to the specific needs of each project. This level of customization ensures that manufacturers can meet various customer needs without investing in multiple machines or production settings.
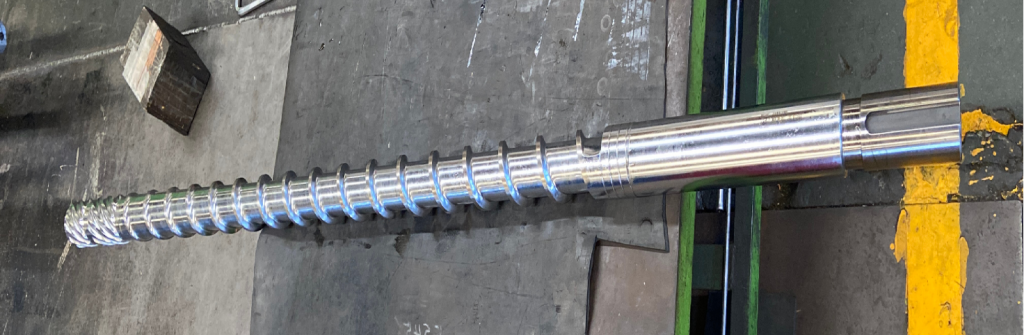
Enhanced cooling and ejection: accelerate the post-molding stage
Many manufacturers ignore the impact of cooling and ejection on the overall cycle time. The TM Series plastic molding machine has a dedicated water chiller for injection molding and a cooling channel. The ejection system has also been upgraded, which increases the ejector thrust by 20%, is conducive to the demolding of connectors and plug-in products, and has broader applicability. The servo motor positions the ejector with micron-level accuracy to minimize component stress. For a toy manufacturer producing snap-on parts, this accuracy reduced ejection-related defects from 8% to 0.5%. Faster cooling and ejection also means the mold can be reopened faster, significantly reducing idle time between cycles.
Reduce Waste in Your Workflow
Material waste is a silent killer of productivity. Conventional injection molding machines often overcompensate for inconsistencies using excess resin, resulting in increased costs and longer cycle times. The TM Series monitors melt temperature, pressure, and flow rate via sensors, feeding data back to the control unit to fine-tune screw rotation and nozzle pressure. In one case study, a packaging manufacturer reduced resin waste by 18% after adopting a TM Series injection molding machine. The machine’s precise injection control ensures that each cavity in a 64-cavity mold receives the exact amount of resin, eliminating flooding. Combined with faster screw recovery time, this efficiency enables the machine to maintain shorter cycle times without sacrificing part integrity.
Achieve Faster Molding Cycles
The TM Series plastic molding machines offer a powerful solution for manufacturers looking to reduce turnaround time and increase production efficiency. With the ability to increase output, reduce cycle time, and improve molding stability, the TM Series sets new standards for the industry. Upgrades to the injection platform, automation system, and control functions contribute to faster and more efficient production while ensuring product quality.
TRENDING POSTS
- What factors can cause delays in the injection molding process of plastic molding machine? 2025/02/14
- Exhibition Review| Topstar participates in InterPlas Thailand 2024 2025/02/14
- Star Case | Topstar helps Santong upgrade its intelligent plant 2025/02/14
- Topstar Special | National Science and Technology Workers Day 2025/02/14
HOT TOPIC
- 3 in 1 Compact Dehumidifying Dryer
- 5-axis CNC machine
- accuracy
- Air Chillers
- all electric injection molding machine
- all electric injection molding machines
- All-electric injection molding machines
- and overall production quality. Therefore
- AP-RubberPlas
- automated injection molding machine
- Automation changed engineering
- automation of injection molding robots
- auxiliary machine
- Bench Injection Molding Machine
- Cabinet dryer manufacturers
- Cabinet dryers
- chiller
- CNC Drilling Machine
- CNC Drilling Machines
- cnc engraving machine manufacturer
- cnc laser cutting machine manufacturer
- CNC machine
- CNC Machine Center
- CNC Machine for Sale
- CNC Machine Manufacturing
- CNC Machine Tool
- CNC machine tool product
- CNC Machining Center
- CNC wood carving machine
- Cooling system
- Cross-Walking Single Axis Servo Cylinder Robot
- Cross-Walking Single-Axis Servo Cylinder Robot
- Cross-Walking Three-Axis/Five-Axis Servo Driven Robot
- cross-walking three-axis/five-axis servo-driven robot
- Dehumidifier Dryer
- Dehumidifying Dryer
- delta parallel robot
- Desktop Injection Molding Machine
- Desktop injection molding machines
- Desktop Molding Machine
- desktop plastic injection machine
- Desktop Plastic Injection Molding Machine
- direct clamp injection molding machine
- Direct clamp injection molding machines
- Dosing & mixing system
- Drilling Centers
- Drying and dehumidification system
- drying and dehumidifying equipment
- Drying and Dehumidifying System
- drying system
- effective and efficient. Cabinet dryers are also used in other industries where large quantities of material need to be dried
- efficient injection molding machine
- elbow hydraulic injection molding machines
- electric injection molding machine
- electric injection molding machines
- energy-saving injection molding machine
- etc. Among injection molding robots
- exhibition
- features of CNC machine
- Feeding And Conveying System
- Five Axis Machine Center
- Fully automatic injection molding machine
- Gathering Topstar
- giant injection molding machine
- GMU-600 5-Axis Machining Center
- Granulating & Recycling System
- Heavy duty injection molding machine
- Honeycomb rotor dehumidifier
- horizontal injection molding machine
- Horizontal Injection Molding Machines
- Horizontal Injection Moulding Machine
- Horizontal Mixer manufacturer
- How The CNC Machine Works
- hybrid injection molding machine
- hydraulic injection molding machine
- Hydraulic Injection Molding Machines
- in this article
- Industrial robot
- Industrial Robot Chinese brand
- industrial robot parts
- industrial robot supplier
- Industrial robots
- Industry Chain
- Injection Manipulator
- injection mold machines
- Injection molding
- Injection molding automation
- Injection Molding Automation Solution
- injection molding dryer
- Injection molding equipment
- injection molding hopper dryer
- Injection molding machine
- injection molding machine brand
- Injection Molding Machine Factory
- Injection Molding Machine Manufacture
- Injection molding machine manufacturer
- injection molding machine manufacturers
- Injection molding machine procurement
- injection molding machine robotic arm
- injection molding machine with a robot
- Injection molding machines
- injection molding material dehumidifying
- injection molding plant
- Injection Molding Robot
- injection molding robot arm
- Injection molding robot automation
- Injection molding robotic arm
- injection molding robots
- Injection Moulding Robots
- Injection Robot
- Injection robot arm
- Injection robot manufacturer
- Injection robot wholesale
- injection robots
- intelligent injection molding machines
- Introducing Injection Robot
- It is the best choice for drying large quantities of material at once. Cabinetmakers use these machines because they are fast
- large injection molding machine
- Learn what industrial automation and robotics is
- low speed sound-proof granulator
- machine plastic molding
- make sure to add some! Improvements (2) Keyphrase in introduction: Your keyphrase or its synonyms appear in the first paragraph of the copy
- manipulator machine
- manufacturing
- micro injection molding machine
- middle speed granulator
- Mini CNC machine manufacturers.
- Mold Temperature Control System
- mold temperature controller
- molding material Dehumidifying System
- mould temperature controller
- mould temperature controllers
- New electric injection molding machine
- nitrogen dryer manufacturer
- nitrogen dryer system manufacturer
- Oil type mold temperature controller
- open day
- Outbound links: No outbound links appear in this page. Add some! Images: No images appear on this page. Add some! Internal links: No internal links appear in this page
- PET Preform injection molding
- phone case maker machine
- phone case making machine
- plastic bottle making machine
- plastic bottle manufacturing
- plastic bucket making machine
- plastic bucket manufacturing
- Plastic chair making machine
- plastic forming equipment
- plastic hopper dryer
- plastic injection machine
- plastic injection machines
- plastic injection molding
- Plastic injection molding equipment
- Plastic injection molding machine
- Plastic Injection Molding Machines
- plastic injection robot
- Plastic Molding machine
- Plastic Molding Machines
- plastic molding press
- plastic phone case making machine
- plastic-molding machine
- powerful granulator
- Powerful Type Sound-Proof Granulator
- production of plastic seats
- Robot injection molding
- robot injection molding machine
- robot manufacturing companies
- Robotic arm for injection molding machine
- robotic injection molding machines
- robotics in injection molding
- SCARA robot
- SCARA robots
- Service-oriented manufacturing
- Servo Cylinder Robot
- servo driven robot
- Servo Driven Robots
- servo injection robots
- Servo-Driven Robot
- Setup of injection machine
- Silicone Injection Molding Machine
- six-axis industrial robot
- Stainless Hopper Dryer
- Stainless Hopper Dryers
- star club
- swing arm robot
- the choice between servo-driven robots and hydraulic robots will have a certain impact on efficiency
- the most popular injection molding machine
- the type of injection molding robot
- toggle clamp injection molding machine
- Toggle Hydraulic Injection Molding Machines
- toggle injection molding machine
- Top 10 brands of injection robots
- Topstar
- Topstar Engineering
- Topstar Industrial Robots
- Topstar injection molding intelligent
- Topstar Scara Robots
- Useful Injection molding machine
- Vertical machining centers
- volumetric type blender
- water chiller
- water chillers
- water distributor
- Water Type MoldTemperature Controller
- We often face choices when performing injection molding. We will choose the type of injection molding machine
- wholesale of injection molding machines
- x carve CNC