The relationship between mould temperature controller and injection molding efficiency
2025/02/07 By Topstar
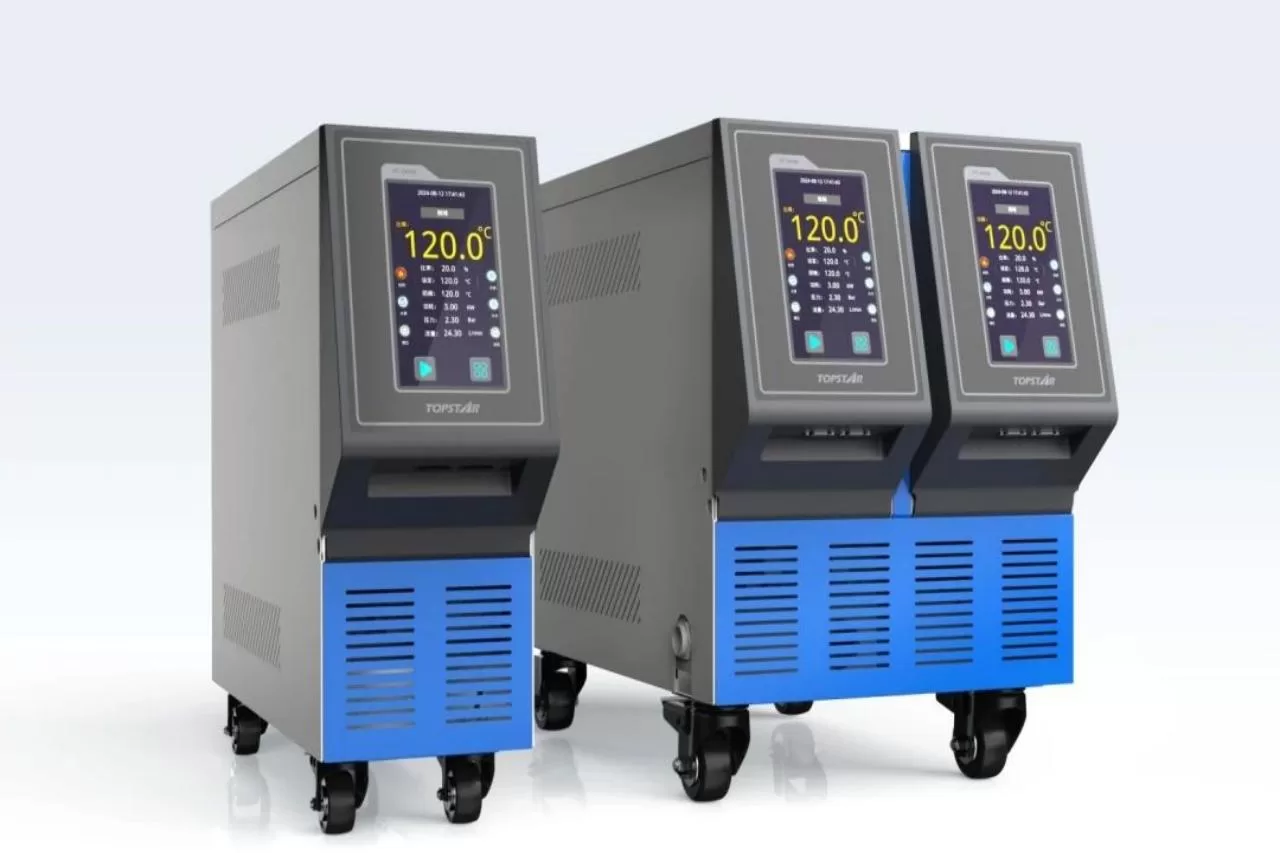
The accuracy, repeatability, and efficiency of injection moulding determine the profitability of its production. Thermal management bridges the gap between raw materials and perfect final products. A mould temperature controller is key to this thermal regulation, ensuring the mould maintains a precise temperature to optimize cycle time, reduce defects, and increase injection efficiency. Topstar’s fourth-generation mould temperature controllers use adaptive, predictive intelligence that mimics autonomous systems, subverting traditional methods. By dynamically adjusting real-time production variables, these controllers improve efficiency, reduce waste, and provide security for future manufacturing workflows.
What is the connection between the mould temperature controller and injection moulding?
Injection moulding and core injection moulding require auxiliary equipment such as mould temperature controllers, chillers, and robots. Mould temperature controllers are essential for achieving consistent part quality and operational efficiency. Their primary function is to regulate the heat exchange between the mould and the heating/cooling medium (usually water or oil) throughout the injection moulding cycle. Precise temperature control ensures uniform material flow, minimizes residual stress, and accelerates cooling without compromising structural integrity.
For example, in producing some high-precision, high-production plastic parts, even small temperature fluctuations (±2°C) can cause warping or surface defects. Therefore, high-precision mould temperature controllers maintain thermal stability to ensure that each part meets strict tolerances. In addition to quality, temperature consistency also directly affects cycle time. Faster cooling can reduce idle time between cycles, but excessive cooling can cause brittleness. Topstar’s mould temperature controllers achieve this balance by using real-time data to adjust the cooling rate based on material properties and mould geometry.
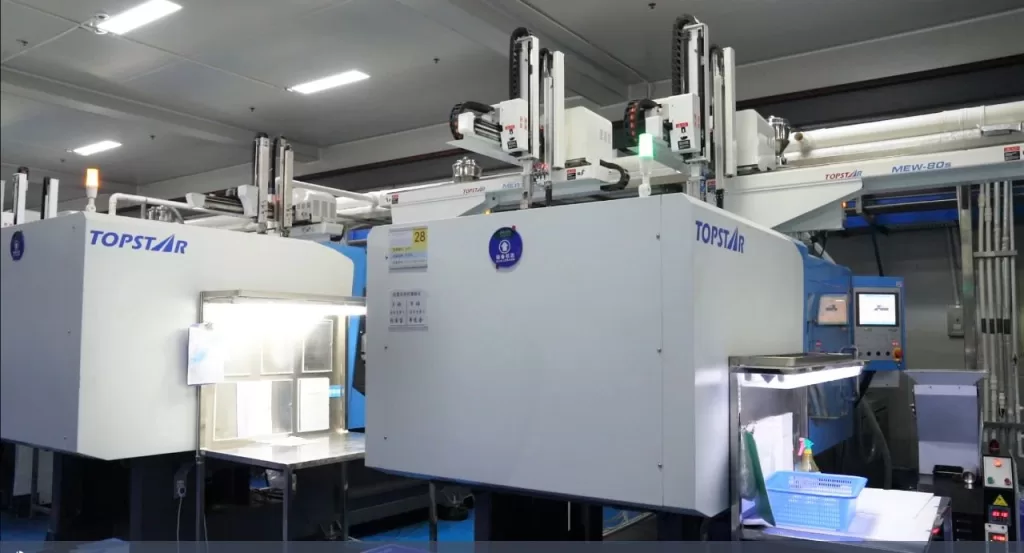
Disadvantages of Traditional PID Control Systems
Traditional PID controllers have limitations that become apparent in complex, dynamic production environments. PID systems rely on preset parameters that assume static conditions, such as constant mould temperature, uniform material viscosity, and stable ambient humidity. In actual operation, these variables fluctuate due to mould wear, seasonal temperature changes, or batch-to-batch material changes. Another key flaw of traditional PID systems is their reactivity, which only adjusts the output after detecting temperature deviations. This lag often results in over- or under-target temperatures, resulting in energy waste and extended cycle times, leading to inefficiencies. For example, in high-volume production of PET bottles, PID controllers may overcompensate during rapid cooling phases, forcing the system to reheat the mould unnecessarily. This inefficiency can cause energy costs to soar by 10-15%.
Topstar 4th Generation Mould Temperature Controller: Adaptive Intelligent Control
The Topstar 4th Generation Mould Temperature Controller replaces rigid PID logic with an upgrade to the traditional PID control algorithm. The system continuously monitors and analyzes dozens of variables in real time, including mould surface temperature (via infrared sensors), coolant flow rate, material melt temperature, ambient humidity, and more. Processing this data through machine learning models, the controller can predict changes in heat load and proactively adjust heating or cooling output.
For example, a manufacturer switches from low-viscosity polycarbonate to a high-viscosity nylon blend. Traditional PID controllers require manual recalibration, resulting in downtime. In contrast, Topstar’s system detects increased viscosity through a pressure sensor in the injection unit and automatically increases mould temperature to ensure optimal flow. Another innovation is the controller’s “learning memory,” which stores the optimal parameters for a specific mould and material. When a job is repeated, the system calls up past data to achieve the highest injection efficiency from the first cycle, eliminating trial-and-error adjustments.
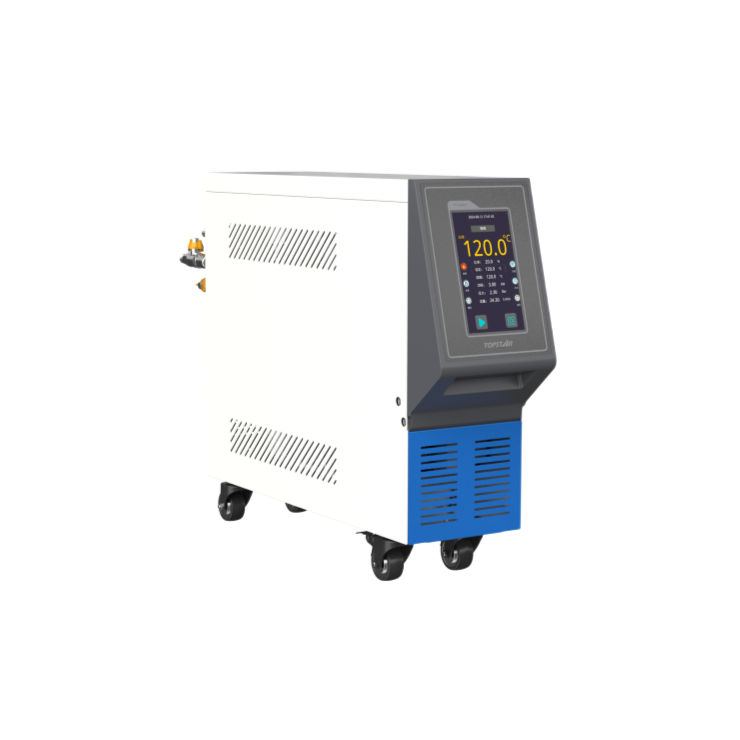
Load Adaptive Algorithm of Mould Temperature Controller
The cornerstone of Topstar technology is an adaptive control process designed to handle both gradual and sudden thermal load changes. In the initial stage, the mould temperature controller performs a “thermal fingerprint” analysis of the mould, mapping the heat distribution pattern and identifying hot spots or cooling inefficiencies.
In the second stage, real-time adjustments are made seamlessly. For example, suppose the coolant pump experiences a momentary pressure drop due to a clogged filter. In that case, it immediately compensates by adjusting the heater output or rerouting the coolant flow to maintain temperature stability. This responsiveness is critical for high-precision applications such as optical lenses or microfluidic devices. The final stage focuses on long-term optimization. Over multiple production runs, it aggregates performance data to improve its algorithms.
Integration with the Smart Manufacturing Ecosystem
Modern injection moulding equipment increasingly adopts the Industry 4.0 framework. Topstar’s mould temperature controller is interconnected with the injection moulding machine, supports host call signals, and achieves seamless connection with the Internet through a digital MES system. This enables full-factory optimization. For example, thermal performance metrics can guide predictive scheduling – if a mould cools more slowly than expected, the MES can automatically delay downstream assembly tasks to avoid bottlenecks. Remote monitoring is another key capability. Engineers can adjust temperature setpoints through a secure cloud interface or diagnose problems from anywhere in the world.
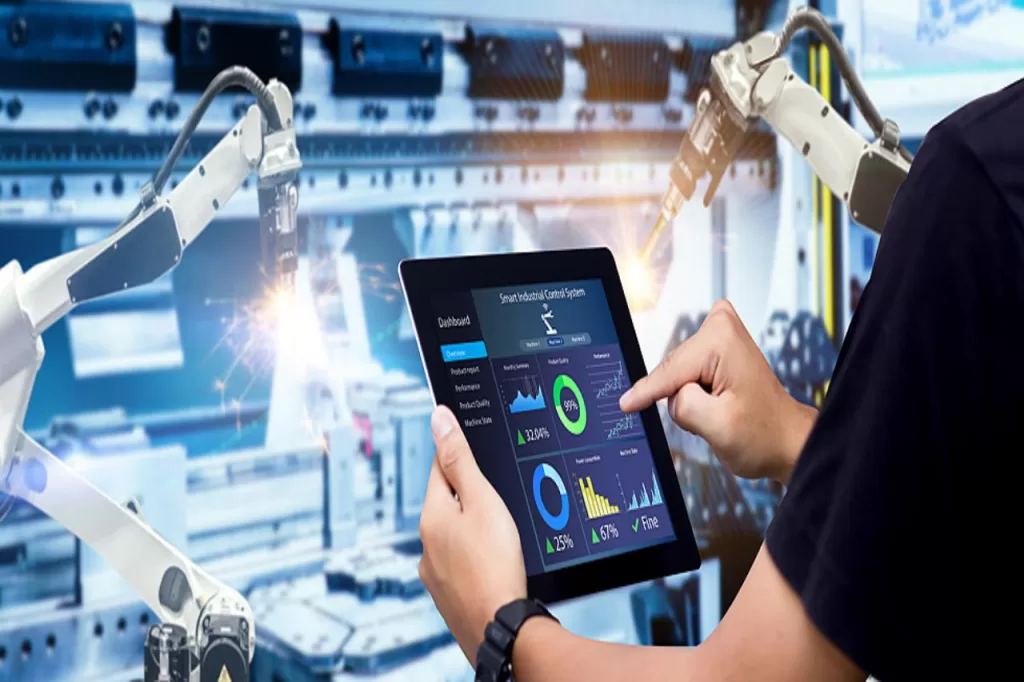
Higher efficiency through intelligent control
Topstar’s fourth-generation mould temperature controllers break through the limitations of traditional systems by combining adaptability, precision, and connectivity. By automatically making real-time thermal adjustments, these controllers can improve injection efficiency, reduce energy waste, and virtually eliminate defects by shortening cycle times.
TRENDING POSTS
- What factors can cause delays in the injection molding process of plastic molding machine? 2025/02/07
- Exhibition Review| Topstar participates in InterPlas Thailand 2024 2025/02/07
- Star Case | Topstar helps Santong upgrade its intelligent plant 2025/02/07
- Topstar Special | National Science and Technology Workers Day 2025/02/07
HOT TOPIC
- 3 in 1 Compact Dehumidifying Dryer
- 5-axis CNC machine
- accuracy
- Air Chillers
- all electric injection molding machine
- All-electric injection molding machines
- and overall production quality. Therefore
- AP-RubberPlas
- automated injection molding machine
- Automation changed engineering
- automation of injection molding robots
- auxiliary machine
- Bench Injection Molding Machine
- Cabinet dryer manufacturers
- Cabinet dryers
- chiller
- CNC Drilling Machine
- CNC Drilling Machines
- cnc engraving machine manufacturer
- cnc laser cutting machine manufacturer
- CNC machine
- CNC Machine Center
- CNC Machine for Sale
- CNC Machine Manufacturing
- CNC Machine Tool
- CNC machine tool product
- CNC Machining Center
- CNC wood carving machine
- Cooling system
- Cross-Walking Single Axis Servo Cylinder Robot
- Cross-Walking Single-Axis Servo Cylinder Robot
- Cross-Walking Three-Axis/Five-Axis Servo Driven Robot
- cross-walking three-axis/five-axis servo-driven robot
- Dehumidifier Dryer
- Dehumidifying Dryer
- delta parallel robot
- Desktop Injection Molding Machine
- Desktop injection molding machines
- Desktop Molding Machine
- desktop plastic injection machine
- Desktop Plastic Injection Molding Machine
- direct clamp injection molding machine
- Direct clamp injection molding machines
- Dosing & mixing system
- Drilling Centers
- Drying and dehumidification system
- drying and dehumidifying equipment
- Drying and Dehumidifying System
- drying system
- effective and efficient. Cabinet dryers are also used in other industries where large quantities of material need to be dried
- efficient injection molding machine
- elbow hydraulic injection molding machines
- electric injection molding machine
- electric injection molding machines
- etc. Among injection molding robots
- exhibition
- features of CNC machine
- Feeding And Conveying System
- Five Axis Machine Center
- Fully automatic injection molding machine
- Gathering Topstar
- giant injection molding machine
- GMU-600 5-Axis Machining Center
- Granulating & Recycling System
- Heavy duty injection molding machine
- Honeycomb rotor dehumidifier
- horizontal injection molding machine
- Horizontal Injection Molding Machines
- Horizontal Injection Moulding Machine
- Horizontal Mixer manufacturer
- How The CNC Machine Works
- hybrid injection molding machine
- hydraulic injection molding machine
- Hydraulic Injection Molding Machines
- in this article
- Industrial robot
- Industrial Robot Chinese brand
- industrial robot parts
- industrial robot supplier
- Industrial robots
- Industry Chain
- Injection Manipulator
- injection mold machines
- Injection molding
- Injection molding automation
- Injection Molding Automation Solution
- injection molding dryer
- Injection molding equipment
- injection molding hopper dryer
- Injection molding machine
- injection molding machine brand
- Injection Molding Machine Factory
- Injection Molding Machine Manufacture
- Injection molding machine manufacturer
- injection molding machine manufacturers
- Injection molding machine procurement
- injection molding machine robotic arm
- injection molding machine with a robot
- Injection molding machines
- injection molding material dehumidifying
- injection molding plant
- Injection Molding Robot
- injection molding robot arm
- Injection molding robot automation
- Injection molding robotic arm
- injection molding robots
- Injection Moulding Robots
- Injection Robot
- Injection robot arm
- Injection robot manufacturer
- Injection robot wholesale
- injection robots
- intelligent injection molding machines
- Introducing Injection Robot
- It is the best choice for drying large quantities of material at once. Cabinetmakers use these machines because they are fast
- large injection molding machine
- Learn what industrial automation and robotics is
- low speed sound-proof granulator
- machine plastic molding
- make sure to add some! Improvements (2) Keyphrase in introduction: Your keyphrase or its synonyms appear in the first paragraph of the copy
- manipulator machine
- manufacturing
- micro injection molding machine
- middle speed granulator
- Mini CNC machine manufacturers.
- Mold Temperature Control System
- mold temperature controller
- molding material Dehumidifying System
- mould temperature controller
- mould temperature controllers
- New electric injection molding machine
- nitrogen dryer manufacturer
- nitrogen dryer system manufacturer
- Oil type mold temperature controller
- open day
- Outbound links: No outbound links appear in this page. Add some! Images: No images appear on this page. Add some! Internal links: No internal links appear in this page
- PET Preform injection molding
- phone case maker machine
- phone case making machine
- plastic bottle making machine
- plastic bottle manufacturing
- plastic bucket making machine
- plastic bucket manufacturing
- Plastic chair making machine
- plastic forming equipment
- plastic hopper dryer
- plastic injection machine
- plastic injection machines
- plastic injection molding
- Plastic injection molding equipment
- Plastic injection molding machine
- Plastic Injection Molding Machines
- plastic injection robot
- Plastic Molding machine
- Plastic Molding Machines
- plastic molding press
- plastic phone case making machine
- plastic-molding machine
- powerful granulator
- Powerful Type Sound-Proof Granulator
- production of plastic seats
- Robot injection molding
- robot injection molding machine
- robot manufacturing companies
- Robotic arm for injection molding machine
- robotic injection molding machines
- robotics in injection molding
- SCARA robot
- SCARA robots
- Service-oriented manufacturing
- Servo Cylinder Robot
- servo driven robot
- Servo Driven Robots
- servo injection robots
- Servo-Driven Robot
- Setup of injection machine
- Silicone Injection Molding Machine
- six-axis industrial robot
- Stainless Hopper Dryer
- Stainless Hopper Dryers
- star club
- swing arm robot
- the choice between servo-driven robots and hydraulic robots will have a certain impact on efficiency
- the most popular injection molding machine
- the type of injection molding robot
- toggle clamp injection molding machine
- Toggle Hydraulic Injection Molding Machines
- toggle injection molding machine
- Top 10 brands of injection robots
- Topstar
- Topstar Engineering
- Topstar Industrial Robots
- Topstar injection molding intelligent
- Topstar Scara Robots
- Useful Injection molding machine
- Vertical machining centers
- volumetric type blender
- water chiller
- water chillers
- water distributor
- Water Type MoldTemperature Controller
- We often face choices when performing injection molding. We will choose the type of injection molding machine
- wholesale of injection molding machines
- x carve CNC