How to solve the problem of communication delay in electric injection molding machine?
2025/02/05 By Topstar
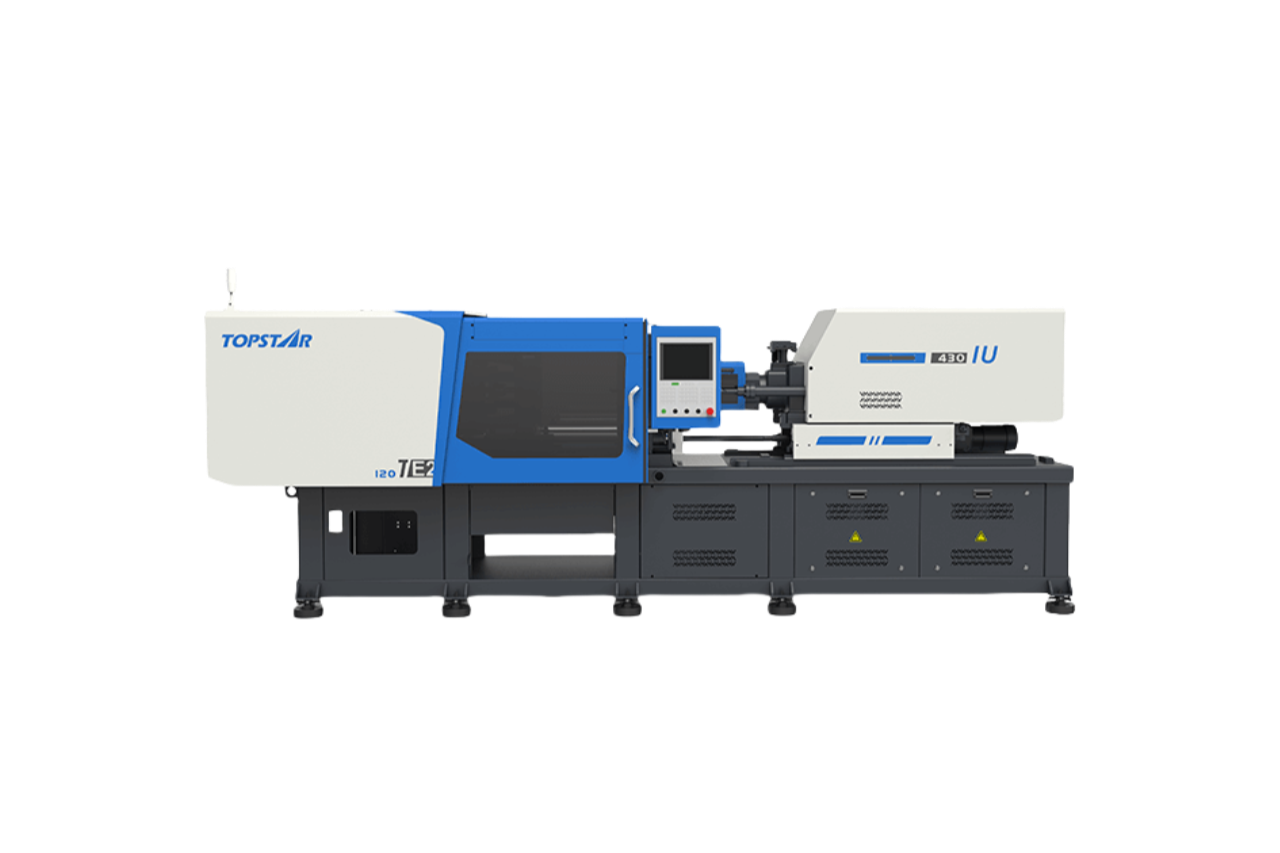
Electric injection molding machines improve the production of plastic manufacturing with precision, energy saving, and high cleanliness. However, a common problem in traditional electric injection molding machines is the communication delay between the controller and the servo drive. This bottleneck affects the quality of high-speed, high-precision applications. Even millisecond delays can lead to inconsistent part size, surface finish, or material distribution. While upgrading to a high-performance CPU is an obvious solution, this approach increases costs and complicates system design. Topstar has reimagined the control architecture with the TE Ⅱ electric injection molding machine, launching a breakthrough solution that eliminates delays without expensive hardware upgrades.
The hidden cost of communication delays in electric injection molding machines
In traditional electric injection molding machines, communication between the central controller and the servo drive relies on serial protocols such as CANopen or EtherCAT. While these systems are sufficient for general applications, they introduce inherent delays – typically 2-5 milliseconds per cycle. Then, in high-speed molding cycles, such as thin-wall packaging or medical, optical component production, this delay can cause a mismatch between command signals and actuator responses. For example, pressure overshoot during cavity filling or position errors during mold clamping can result in scrap rates as high as 5-8%.
The root cause lies in the sequential workflow: The controller calculates the motion profile, transmits it to the drive, and waits for confirmation before continuing. This communication becomes a critical bottleneck when cycle times are below 3 seconds. Manufacturers often overspecify tolerances or slow production to compensate, which can be costly.
Why a high-performance CPU is not the best solution?
Many engineers believe upgrading to multicore processors or FPGA-based controllers will solve the latency problem. While these systems can reduce calculation time by 20-30%, they bring three new issues:
Cost explosion: High-end industrial CPUs such as Intel Xeon or ARM Cortex-A72 increase controller costs by 40-60%, which weakens the return on investment of electric injection molding machines.
Thermal challenges: Dense processing units require complex cooling systems, increasing the machine’s footprint and maintenance requirements.
Software complexity: Real-time operating systems and complex code bases require specialized programming skills, which increases long-term support costs.
Topstar TE Ⅱ electric injection molding machine: decentralized intelligent control
TE Ⅱ electric injection molding machine adopts intelligent drive control architecture. The whole system no longer relies solely on the central controller but enables the servo drive to generate motion curves according to process parameters autonomously. Its working principle is as follows:
Parameter initialization: The central controller sends key process data, such as clamping force, injection speed curve, etc., to the servo drive during setup.
Localized calculation: Each drive uses a built-in DSP to calculate the real-time position, speed, and pressure trajectory.
Synchronous execution: The drive operates in a peer-to-peer network, minimizing the handshake delay with the central controller.
Through decentralized decision-making, the communication cycle is shortened from 5 milliseconds to 0.3-0.6 milliseconds, improving 8-16 times. This makes synchronous multi-axis control possible, even if the servo motor speed exceeds 3,000 RPM.
How can to improve product quality by shortening delay time?
Faster response times translate directly into tighter process control in three key areas:
1. Positioning accuracy of electric injection molding machines
During mold clamping, the TE Ⅱ electric injection molding machine’s servo drive can adjust the pressure plate’s position within a tolerance range of 0.01 mm, eliminating flash defects caused by premature mold opening.
2. Pressure consistency
Real-time pressure adjustment during injection (at intervals of 0.1 milliseconds) prevents overfilling or under-injection, critical for optical components such as light guides.
3. Speed synchronization
Simultaneous control of screw rotation and back pressure ensures uniform melt viscosity, thereby reducing sink marks in production.
Electric drive process integrated injection molding machine
The intelligent drive architecture also supports Topstar’s electric injection molding machine process integration system, which integrates auxiliary equipment such as injection molding machines, robots, and mold temperature controllers into one platform. By eliminating separate controllers for auxiliary equipment, manufacturers can get the following:
Centralized monitoring: Real-time dashboard tracks energy consumption, OEE, and predictive maintenance alerts.
Faster changeovers: Preloaded recipes for different materials. Switching from PP to PEEK reduces setup time by 65%.
Scalability: Modular drives easily integrate additional axes for insert molding or in-mold labeling.
More intelligent control, more competitive
The Topstar TE Ⅱ electric injection molding machine proves that overcoming communication delays does not require expensive hardware upgrades. By reallocating computing tasks to intelligent servo drives, Topstar achieves millisecond response speeds while keeping the controller lean. This improves precision and paves the way for a fully integrated smart factory.
TRENDING POSTS
- What factors can cause delays in the injection molding process of plastic molding machine? 2025/02/05
- Exhibition Review| Topstar participates in InterPlas Thailand 2024 2025/02/05
- Star Case | Topstar helps Santong upgrade its intelligent plant 2025/02/05
- Topstar Special | National Science and Technology Workers Day 2025/02/05
HOT TOPIC
- 3 in 1 Compact Dehumidifying Dryer
- 5-axis CNC machine
- accuracy
- Air Chillers
- all electric injection molding machine
- All-electric injection molding machines
- and overall production quality. Therefore
- AP-RubberPlas
- automated injection molding machine
- Automation changed engineering
- automation of injection molding robots
- auxiliary machine
- Bench Injection Molding Machine
- Cabinet dryer manufacturers
- Cabinet dryers
- chiller
- CNC Drilling Machine
- CNC Drilling Machines
- cnc engraving machine manufacturer
- cnc laser cutting machine manufacturer
- CNC machine
- CNC Machine Center
- CNC Machine for Sale
- CNC Machine Manufacturing
- CNC Machine Tool
- CNC machine tool product
- CNC Machining Center
- CNC wood carving machine
- Cooling system
- Cross-Walking Single Axis Servo Cylinder Robot
- Cross-Walking Single-Axis Servo Cylinder Robot
- Cross-Walking Three-Axis/Five-Axis Servo Driven Robot
- cross-walking three-axis/five-axis servo-driven robot
- Dehumidifier Dryer
- Dehumidifying Dryer
- delta parallel robot
- Desktop Injection Molding Machine
- Desktop injection molding machines
- Desktop Molding Machine
- desktop plastic injection machine
- Desktop Plastic Injection Molding Machine
- direct clamp injection molding machine
- Direct clamp injection molding machines
- Dosing & mixing system
- Drilling Centers
- Drying and dehumidification system
- drying and dehumidifying equipment
- Drying and Dehumidifying System
- drying system
- effective and efficient. Cabinet dryers are also used in other industries where large quantities of material need to be dried
- efficient injection molding machine
- elbow hydraulic injection molding machines
- electric injection molding machine
- electric injection molding machines
- etc. Among injection molding robots
- exhibition
- features of CNC machine
- Feeding And Conveying System
- Five Axis Machine Center
- Fully automatic injection molding machine
- Gathering Topstar
- giant injection molding machine
- GMU-600 5-Axis Machining Center
- Granulating & Recycling System
- Heavy duty injection molding machine
- Honeycomb rotor dehumidifier
- horizontal injection molding machine
- Horizontal Injection Molding Machines
- Horizontal Injection Moulding Machine
- Horizontal Mixer manufacturer
- How The CNC Machine Works
- hybrid injection molding machine
- hydraulic injection molding machine
- Hydraulic Injection Molding Machines
- in this article
- Industrial robot
- Industrial Robot Chinese brand
- industrial robot parts
- industrial robot supplier
- Industrial robots
- Industry Chain
- Injection Manipulator
- injection mold machines
- Injection molding
- Injection molding automation
- Injection Molding Automation Solution
- injection molding dryer
- Injection molding equipment
- injection molding hopper dryer
- Injection molding machine
- injection molding machine brand
- Injection Molding Machine Factory
- Injection Molding Machine Manufacture
- Injection molding machine manufacturer
- injection molding machine manufacturers
- Injection molding machine procurement
- injection molding machine robotic arm
- injection molding machine with a robot
- Injection molding machines
- injection molding material dehumidifying
- injection molding plant
- Injection Molding Robot
- injection molding robot arm
- Injection molding robot automation
- Injection molding robotic arm
- injection molding robots
- Injection Moulding Robots
- Injection Robot
- Injection robot arm
- Injection robot manufacturer
- Injection robot wholesale
- injection robots
- intelligent injection molding machines
- Introducing Injection Robot
- It is the best choice for drying large quantities of material at once. Cabinetmakers use these machines because they are fast
- large injection molding machine
- Learn what industrial automation and robotics is
- low speed sound-proof granulator
- machine plastic molding
- make sure to add some! Improvements (2) Keyphrase in introduction: Your keyphrase or its synonyms appear in the first paragraph of the copy
- manipulator machine
- manufacturing
- micro injection molding machine
- middle speed granulator
- Mini CNC machine manufacturers.
- Mold Temperature Control System
- mold temperature controller
- molding material Dehumidifying System
- mould temperature controller
- mould temperature controllers
- New electric injection molding machine
- nitrogen dryer manufacturer
- nitrogen dryer system manufacturer
- Oil type mold temperature controller
- open day
- Outbound links: No outbound links appear in this page. Add some! Images: No images appear on this page. Add some! Internal links: No internal links appear in this page
- PET Preform injection molding
- phone case maker machine
- phone case making machine
- plastic bottle making machine
- plastic bottle manufacturing
- plastic bucket making machine
- plastic bucket manufacturing
- Plastic chair making machine
- plastic forming equipment
- plastic hopper dryer
- plastic injection machine
- plastic injection machines
- plastic injection molding
- Plastic injection molding equipment
- Plastic injection molding machine
- Plastic Injection Molding Machines
- plastic injection robot
- Plastic Molding machine
- Plastic Molding Machines
- plastic molding press
- plastic phone case making machine
- plastic-molding machine
- powerful granulator
- Powerful Type Sound-Proof Granulator
- production of plastic seats
- Robot injection molding
- robot injection molding machine
- robot manufacturing companies
- Robotic arm for injection molding machine
- robotic injection molding machines
- robotics in injection molding
- SCARA robot
- SCARA robots
- Service-oriented manufacturing
- Servo Cylinder Robot
- servo driven robot
- Servo Driven Robots
- servo injection robots
- Servo-Driven Robot
- Setup of injection machine
- Silicone Injection Molding Machine
- six-axis industrial robot
- Stainless Hopper Dryer
- Stainless Hopper Dryers
- star club
- swing arm robot
- the choice between servo-driven robots and hydraulic robots will have a certain impact on efficiency
- the most popular injection molding machine
- the type of injection molding robot
- toggle clamp injection molding machine
- Toggle Hydraulic Injection Molding Machines
- toggle injection molding machine
- Top 10 brands of injection robots
- Topstar
- Topstar Engineering
- Topstar Industrial Robots
- Topstar injection molding intelligent
- Topstar Scara Robots
- Useful Injection molding machine
- Vertical machining centers
- volumetric type blender
- water chiller
- water chillers
- water distributor
- Water Type MoldTemperature Controller
- We often face choices when performing injection molding. We will choose the type of injection molding machine
- wholesale of injection molding machines
- x carve CNC