How do plastic injection molding machines process various plastic raw materials?
2025/01/22 By Topstar
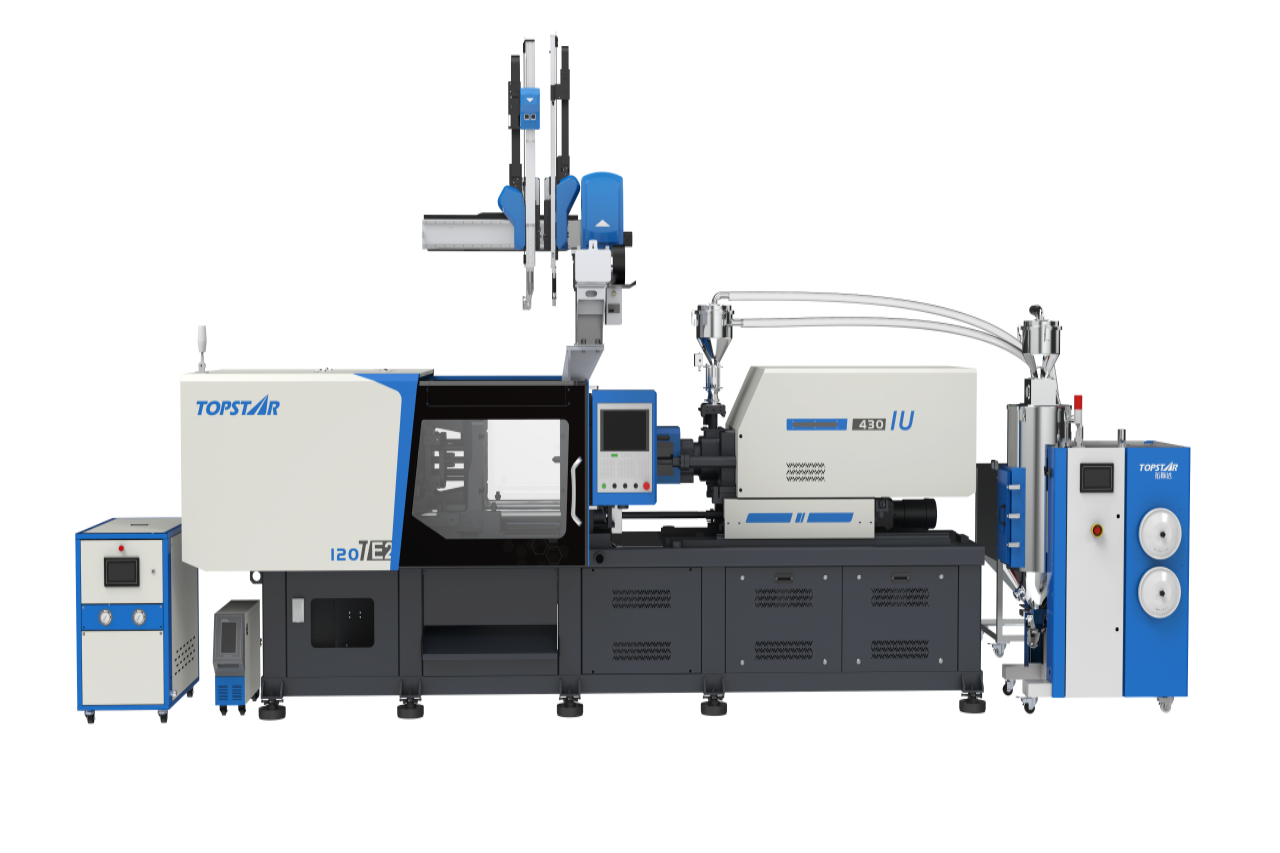
In 2024, Topstar launched special plastic injection molding machines for MIM injection molding to address the difficulties of metal injection molding. At the same time, it also launched two innovative solutions for the automotive lighting industry: automotive lighting silicone headlight dual-material and automotive PMMA thick-walled headlight injection molding unique solutions. In these two solutions, the plastic injection molding machines perfectly solved the requirements of different plastic raw materials for injection molding. Here, we will detail how plastic injection molding machines process raw plastic materials to achieve high cleanliness and high-quality product requirements, such as for various optical and medical products.
How does a plastic injection molding machine process PC raw materials?
Manufacturers widely use PC, a thermoplastic known for its strength, impact resistance, and optical transparency, to produce high-performance automotive, electronics, and optics parts.
To efficiently process a PC, manufacturers equip the plastic injection molding machine with a special screw, such as a bimetallic screw.
The screw design is essential for uniformly melting the material and preventing degradation. In addition, manufacturers must carefully control the injection pressure (typically around 1800kgf/cm²) to ensure that the molten plastic properly fills the mold cavity without causing defects. For applications that require additional strength, such as automotive structural parts, adding glass fibers can further enhance the mechanical properties of polycarbonate. You must adjust plastic injection molding machine settings, including screw speed and injection pressure, based on the percentage of glass fiber added to the material to maintain optimal flow characteristics and prevent damage to the screw or mold.
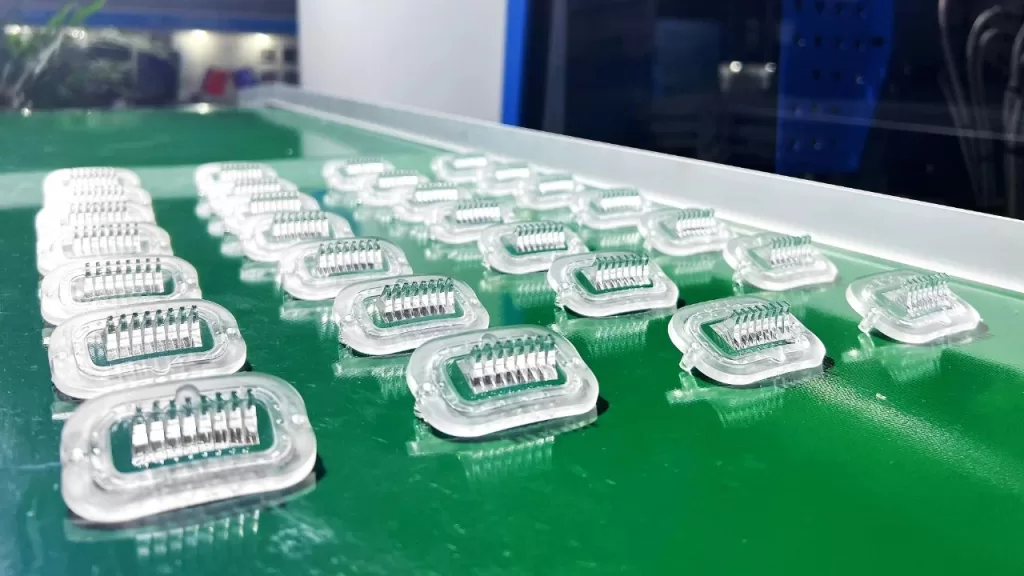
Processing ABS with Plastic Injection Molding Machine
ABS is commonly used in automotive parts, consumer goods, and electrical housings. Manufacturers process ABS in plastic injection molding machines using nitrided screws and barrels with moderate shear rates to ensure that the material fully melts. It has a relatively low melting point compared to other plastics, so the machine temperature must be between 200°C and 240°C. This ensures that the plastic reaches a viscosity suitable for molding. The injection pressure required to process ABS is generally lower than that of materials such as polycarbonate, generally around 1400kgf/cm² or more, allowing for better molding process control. In addition to temperature and pressure control, the cooling rate is essential when processing ABS, as rapid cooling can cause warping or stress inside the part. You should control the mold temperature to achieve optimal cooling without compromising the part’s integrity.
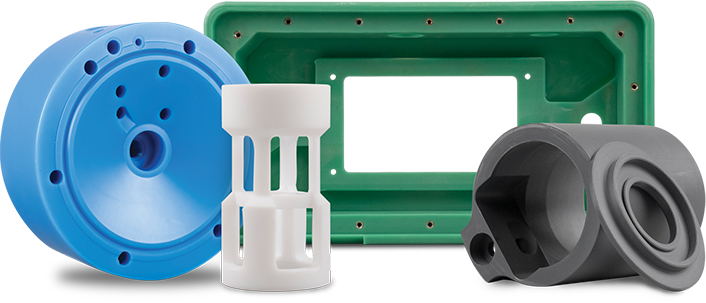
Processing PP Raw Materials Injection Molding
PP is commonly used in packaging, automotive parts, and household goods due to its chemical resistance and high flexibility. Certain factors must be considered when processing PP using a plastic injection molding machine to ensure optimal flow and performance. A key factor to consider when processing PP is the need for higher injection speeds to overcome its low viscosity. You can achieve this by selecting an injection molding machine with high injection speed capabilities. Manufacturers often use specialized screws, such as nitrided screw barrels, to improve the melting efficiency and material flow of PP. The injection pressure of PP is also usually in the range of 1400kgf/cm², depending on the complexity of the part and the mold design.
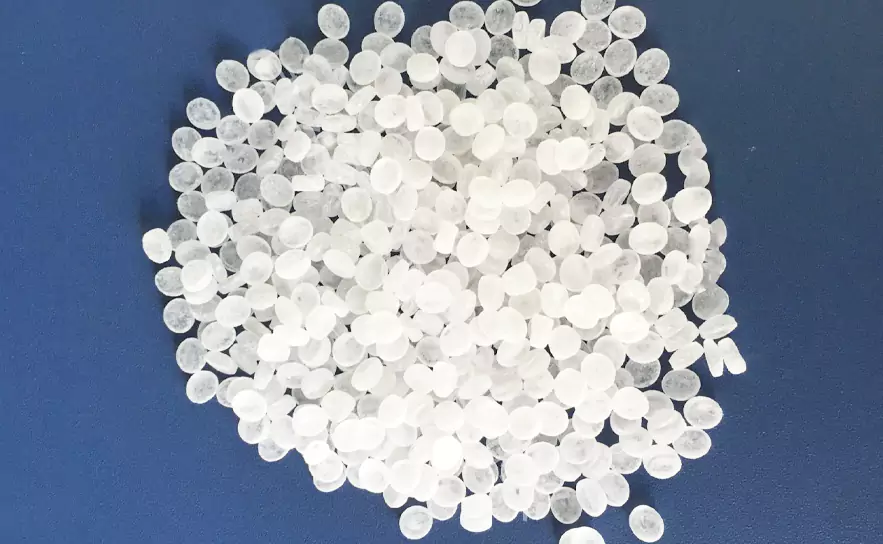
Injection molding of PMMA raw materials
PMMA is a sensitive material, especially under pressure and temperature conditions during the injection molding. Injection molding machines typically use injection pressures above 1800 kg/cm², often requiring unique components to extend the machine’s life and maintain high-quality production. Manufacturers frequently use chrome-plated screws for PMMA injection molding because they are durable and wear-resistant due to the abrasive nature of the material. The chrome plating helps prevent the surface of the screw from wearing out due to friction and heat generated during the injection molding process.
In addition, chrome-plated screws have excellent resistance to the corrosive effects of PMMA heat and moisture absorption. This is particularly important to ensure that the screw maintains its smoothness and operating efficiency, thereby improving the overall performance of the plastic injection molding machine. Using chrome-plated screws also helps minimize the risk of contamination, ensuring that the final product maintains its optical clarity and surface finish.
Processing PE Raw Materials with Plastic Injection Molding Machines
When processing PE raw materials, injection pressures above 1400 kg/cm² are often used. These high pressures help to effectively fill the mold cavity, ensuring that the material flows into all the intricate details of the mold. Such high pressures also require careful attention to temperature control, as PE is sensitive to temperature changes during the injection molding process. To alleviate the challenges of processing PE under high pressure and high-temperature conditions, plastic injection molding machines often use nitrided screw barrels to improve the wear and corrosion resistance of metal parts. In addition, nitrided screw barrels have better thermal stability than standard steel barrels, which helps maintain consistent temperature conditions during processing. At the same time, it can also improve the mechanical properties of the barrel and help reduce the risk of material contamination during the molding process.
Use different screws and injection pressures for other materials.
For injection molding of different materials, it is necessary to select the appropriate screw design, adjust the injection pressure, and carefully control the mold and barrel temperature. At the same time, Topstar can also propose dedicated plastic injection molding machine solutions according to different application products to optimize the molding process to ensure high product quality and efficient production.
TRENDING POSTS
- What factors can cause delays in the injection molding process of plastic molding machine? 2025/01/22
- Exhibition Review| Topstar participates in InterPlas Thailand 2024 2025/01/22
- Star Case | Topstar helps Santong upgrade its intelligent plant 2025/01/22
- Topstar Special | National Science and Technology Workers Day 2025/01/22
HOT TOPIC
- .ervo motor-driven linear robots
- 3 axis robot
- 3 axis robots
- 3 in 1 Compact Dehumidifying Dryer
- 3-axis robot
- 3-axis robots
- 5-axis CNC machine
- accuracy
- Air Chillers
- all electric injection molding machine
- all electric injection molding machines
- All-electric injection molding machines
- and overall production quality. Therefore
- AP-RubberPlas
- automated injection molding machine
- Automation changed engineering
- automation of injection molding robots
- auxiliary machine
- Bench Injection Molding Machine
- Cabinet dryer manufacturers
- Cabinet dryers
- chiller
- CNC Drilling Machine
- CNC Drilling Machines
- cnc engraving machine manufacturer
- cnc laser cutting machine manufacturer
- CNC machine
- CNC Machine Center
- CNC Machine for Sale
- CNC Machine Manufacturing
- CNC Machine Tool
- CNC machine tool product
- CNC Machining Center
- CNC wood carving machine
- Cooling system
- Cross-Walking Single Axis Servo Cylinder Robot
- Cross-Walking Single-Axis Servo Cylinder Robot
- Cross-Walking Three-Axis/Five-Axis Servo Driven Robot
- cross-walking three-axis/five-axis servo-driven robot
- Dehumidifier Dryer
- Dehumidifying Dryer
- delta parallel robot
- Desktop Injection Molding Machine
- Desktop injection molding machines
- Desktop Molding Machine
- desktop plastic injection machine
- Desktop Plastic Injection Molding Machine
- direct clamp injection molding machine
- Direct clamp injection molding machines
- Dosing & mixing system
- Drilling Centers
- Drying and dehumidification system
- drying and dehumidifying equipment
- Drying and Dehumidifying System
- drying system
- effective and efficient. Cabinet dryers are also used in other industries where large quantities of material need to be dried
- efficient injection molding machine
- elbow hydraulic injection molding machines
- electric injection molding machine
- electric injection molding machines
- energy-efficient injection molding robot
- energy-saving injection molding machine
- etc. Among injection molding robots
- exhibition
- features of CNC machine
- Feeding And Conveying System
- Five Axis Machine Center
- Fully automatic injection molding machine
- Gathering Topstar
- giant injection molding machine
- GMU-600 5-Axis Machining Center
- Granulating & Recycling System
- Heavy duty injection molding machine
- High-precision electric molding machines
- high-precision plastic molding machines
- high-speed all electric injection molding machine
- Honeycomb rotor dehumidifier
- horizontal injection molding machine
- Horizontal Injection Molding Machines
- Horizontal Injection Moulding Machine
- Horizontal Mixer manufacturer
- How The CNC Machine Works
- hybrid injection molding machine
- hydraulic injection molding machine
- Hydraulic Injection Molding Machines
- in this article
- Industrial robot
- Industrial Robot Chinese brand
- industrial robot parts
- industrial robot supplier
- Industrial robots
- Industry Chain
- Injection Manipulator
- injection manipulator robot
- injection mold machines
- Injection molding
- Injection molding automation
- Injection Molding Automation Solution
- injection molding dryer
- Injection molding equipment
- injection molding hopper dryer
- Injection molding machine
- injection molding machine brand
- Injection Molding Machine Factory
- Injection Molding Machine Manufacture
- Injection molding machine manufacturer
- injection molding machine manufacturers
- Injection molding machine procurement
- injection molding machine robotic arm
- injection molding machine with a robot
- Injection molding machines
- injection molding material dehumidifying
- injection molding plant
- Injection Molding Robot
- injection molding robot arm
- Injection molding robot automation
- Injection molding robotic arm
- injection molding robots
- Injection moulding machine
- Injection Moulding Robots
- Injection Robot
- Injection robot arm
- Injection robot manufacturer
- Injection robot wholesale
- injection robots
- intelligent injection molding machines
- Introducing Injection Robot
- It is the best choice for drying large quantities of material at once. Cabinetmakers use these machines because they are fast
- large injection molding machine
- Learn what industrial automation and robotics is
- linear robot
- linear robots
- low speed sound-proof granulator
- machine plastic molding
- make sure to add some! Improvements (2) Keyphrase in introduction: Your keyphrase or its synonyms appear in the first paragraph of the copy
- manipulator machine
- manufacturing
- medical grade injection molding machines
- medical injection molding machine
- medical injection molding machines
- micro injection molding machine
- middle speed granulator
- Mini CNC machine manufacturers.
- Mold Temperature Control System
- mold temperature controller
- mold temperature controllers
- molding material Dehumidifying System
- mould temperature control system
- mould temperature controller
- mould temperature controllers
- New electric injection molding machine
- nitrogen dryer manufacturer
- nitrogen dryer system manufacturer
- Oil type mold temperature controller
- Oil type mold temperature controllers
- open day
- Outbound links: No outbound links appear in this page. Add some! Images: No images appear on this page. Add some! Internal links: No internal links appear in this page
- PET Preform injection molding
- phone case maker machine
- phone case making machine
- plastic bottle making machine
- plastic bottle manufacturing
- plastic bucket making machine
- plastic bucket manufacturing
- Plastic chair making machine
- plastic forming equipment
- plastic hopper dryer
- plastic injection machine
- plastic injection machines
- plastic injection molding
- Plastic injection molding equipment
- Plastic injection molding machine
- Plastic Injection Molding Machines
- plastic injection moulding machine
- plastic injection robot
- Plastic Molding machine
- Plastic Molding Machines
- plastic molding press
- plastic moulding machine
- plastic phone case making machine
- plastic-molding machine
- powerful granulator
- Powerful Type Sound-Proof Granulator
- precision injection molding
- precision injection molding machines
- production of plastic seats
- pure water mould temperature controller
- Robot injection molding
- robot injection molding machine
- robot manufacturing companies
- Robotic arm for injection molding machine
- robotic injection molding machines
- robotics in injection molding
- SCARA robot
- SCARA robots
- Service-oriented manufacturing
- Servo Cylinder Robot
- servo driven robot
- Servo Driven Robots
- servo injection robots
- servo motor-driven linear robots
- servo-driven 3-axis robot
- Servo-Driven Robot
- Setup of injection machine
- Silicone Injection Molding Machine
- six-axis industrial robot
- Stainless Hopper Dryer
- Stainless Hopper Dryers
- star club
- swing arm robot
- take-out robots
- the choice between servo-driven robots and hydraulic robots will have a certain impact on efficiency
- the most popular injection molding machine
- the type of injection molding robot
- toggle clamp injection molding machine
- Toggle Hydraulic Injection Molding Machines
- toggle injection molding machine
- Top 10 brands of injection robots
- Topstar
- Topstar Engineering
- Topstar Industrial Robots
- Topstar injection molding intelligent
- Topstar Scara Robots
- Useful Injection molding machine
- Vertical machining centers
- volumetric type blender
- water chiller
- water chillers
- water distributor
- water type mold temperature controller
- Water Type MoldTemperature Controller
- Water-Type Mould Temperature Controllers
- We often face choices when performing injection molding. We will choose the type of injection molding machine
- wholesale of injection molding machines
- x carve CNC