Injection molding machine: Serving the Vietnamese medical consumables market
2025/01/13 By Topstar
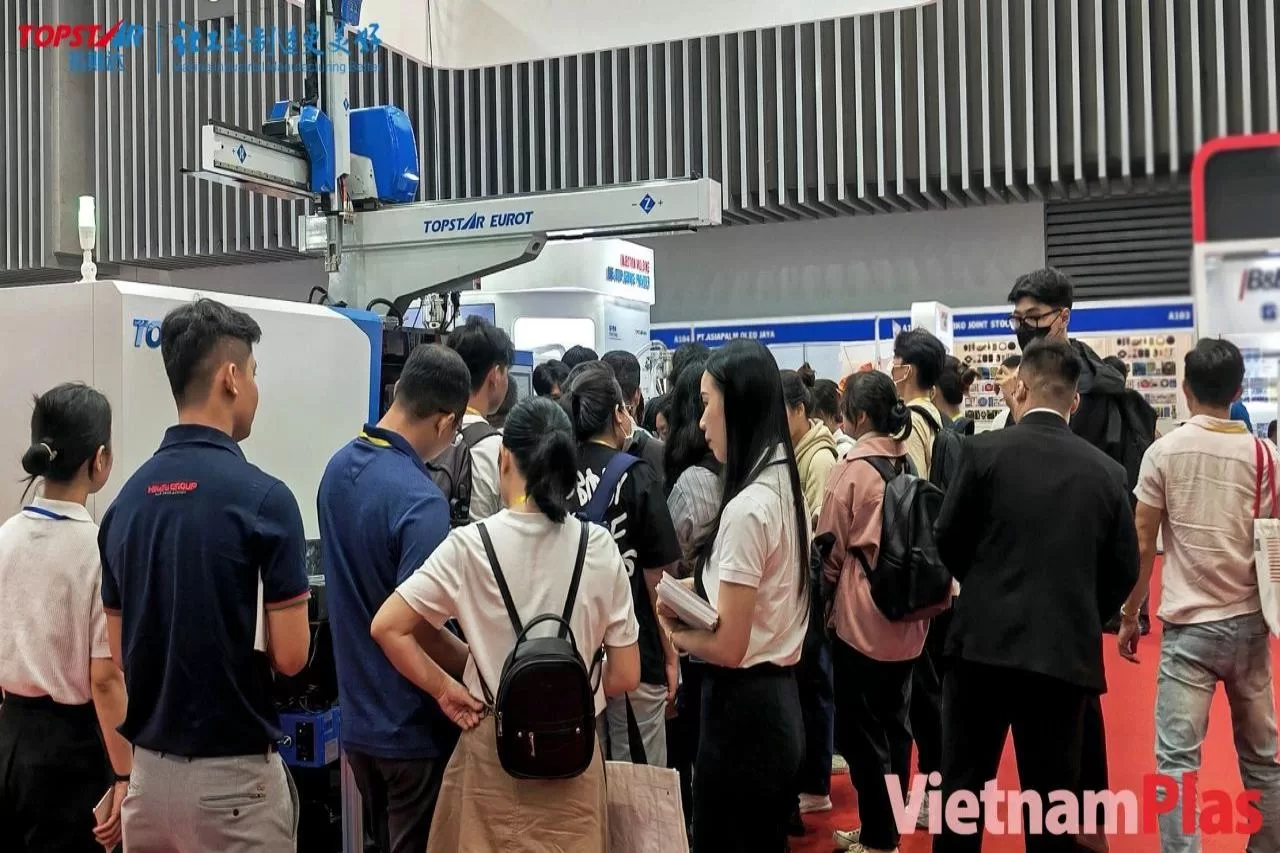
Vietnam is a crucial service point for Topstar’s overseas market localization strategy. Vietnam’s medical consumables market is growing at an annual rate of 10%. Faced with huge market demand, Topstar’s overseas operations team demonstrated efficient, precise, and reliable overall solutions for injection molding medical bottle caps in the medical consumables industry at Vietnam Plas2024. Topstar’s injection molding machine is equipped with intelligent integration technology, which integrates the injection molding process and provides unparalleled efficiency and cleanliness.
The overall solution for injection molding of medical bottle caps
The core of this solution is still an injection molding machine with an integrated injection molding process. Through the technical collaboration of TE Ⅱ electric injection molding machine and peripheral auxiliary equipment, robot + automation, data remote collection, and interaction are realized. 1 out of 32 multi-cavity molding is demonstrated, with a cycle time of 6.7 seconds/cycle. During injection molding, the robot removes the bottle cap and places it in the designated packaging area. Automating these steps reduces the risk of human error and significantly improves the overall production speed. Integration with peripheral auxiliary equipment can improve overall production efficiency. These auxiliary systems work with the injection molding machine to enhance functionality, streamline manufacturing, and ensure optimal performance.
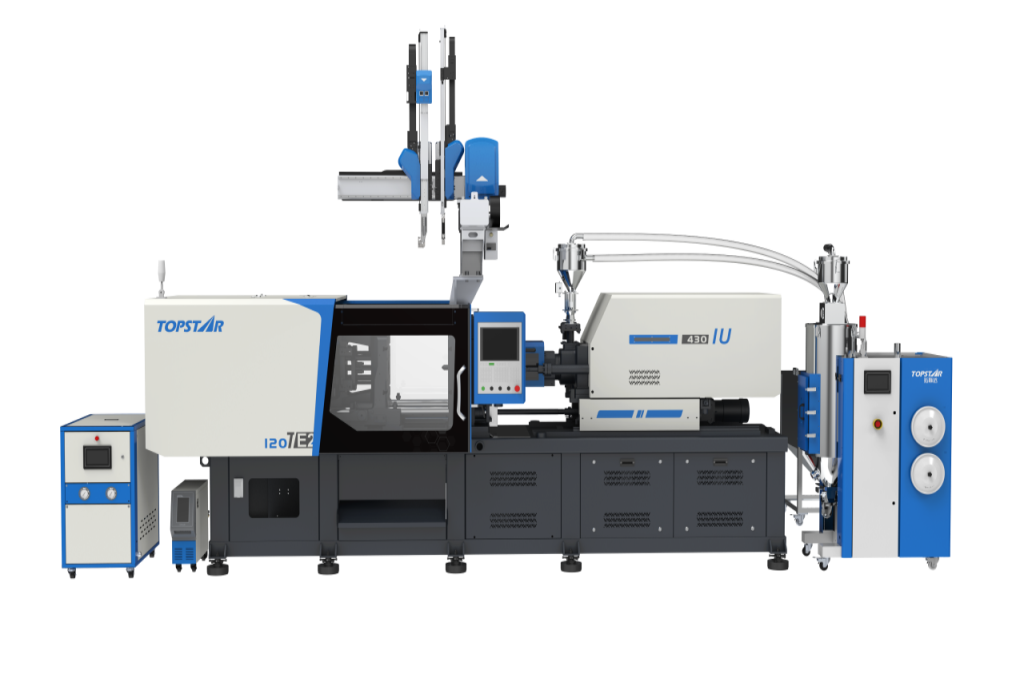
Efficiency improvement of injection molding machine
In the field of medical consumables in Vietnam, products often have to meet strict regulatory standards while being produced quickly to meet growing demand, so cycle times need to be reduced without sacrificing quality, allowing them to meet expanding market demands without compromising product quality. Topstar’s injection molding machines surpass traditional hydraulic presses in their performance. These electric machines have a production cycle reduction of more than 50%. For the Vietnamese medical consumables market, where time-sensitive production is critical, this improvement means meeting growing demand without compromising quality. Integrating robots and automation ensures consistent performance, allowing manufacturers to achieve high-volume production while reducing energy consumption and operating costs.
Remote Data Collection and Interaction
This solution collects remote data throughout the injection molding line, providing detailed insights into cycle times, temperature variations, material usage, and equipment performance. For the medical bottle cap molding process, integrated sensors and IoT-enabled devices can remotely monitor key data points such as cycle time, material usage, temperature fluctuations, and machine performance. Real-time monitoring of cycle times allows manufacturers to track production speeds and identify any inefficiencies in the molding process. Remote data collection is valuable for gathering insights and facilitating remote interaction with the injection molding process. Topstar’s injection molding system allows operators to remotely interact with the machine and adjust settings based on the collected data, ensuring that the molding process remains within optimal parameters.
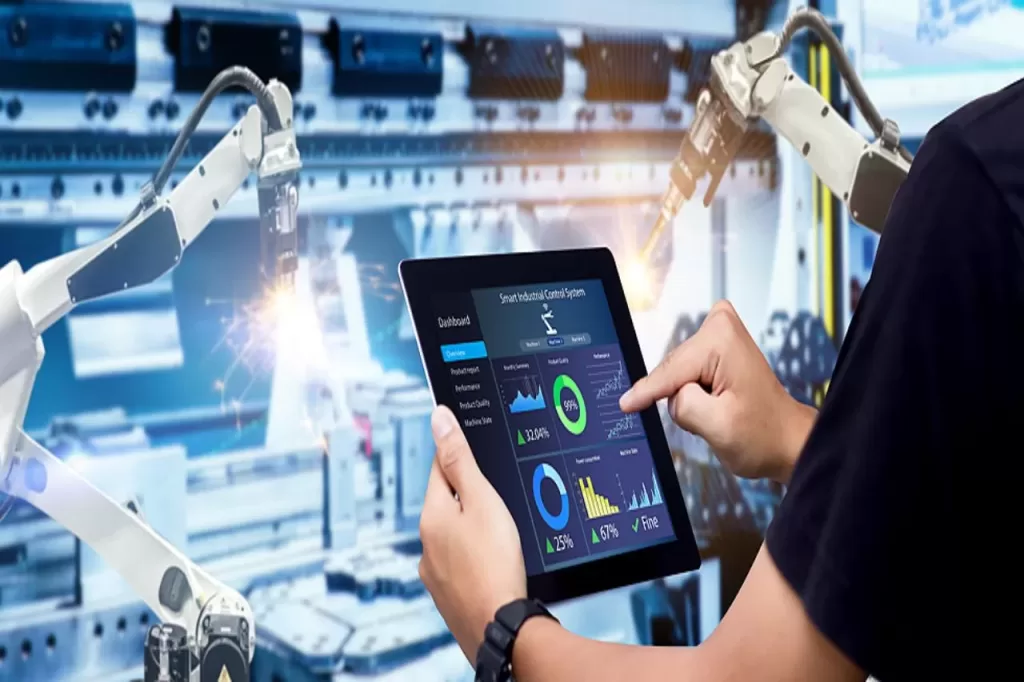
Meeting clean production standards
One of the outstanding features of TE Ⅱ electric injection molding machines is their ability to provide a high-cleanliness production environment. Even minor contamination can have profound effects on industries such as medical consumables. The design of TE Ⅱ electric injection molding machines prioritizes cleanliness and minimizes any potential contamination points that may compromise the integrity of the molded product. Since these machines do not require hydraulic oil, there is no risk of potentially harmful substances leaking or seeping into the production environment. This ensures that the production process occurs in a clean, controlled environment that meets the highest safety standards, thereby providing the final product’s safety. TE II electric injection molding machines help manufacturers comply with these strict regulations.
Advances in injection molding technology for the Vietnamese medical consumables market
Vietnam is a key service country for Topstar’s localization in the overseas market. As the Vietnamese medical consumables industry continues to develop, intelligent injection molding integration will enable manufacturers to achieve smart factories, where machines can communicate in real-time and communicate with the central control system to optimize production processes. Topstar’s injection molding machine series has system integration functions to collect data on parameters such as temperature, pressure, material usage, and cycle time. This data can monitor performance, predict maintenance needs, and optimize machine settings based on real-time conditions. The fusion of innovative technology and automation will bring significant competitive advantages to Vietnamese manufacturers, enabling them to mass-produce high-quality, cost-effective, and sterile medical consumables.
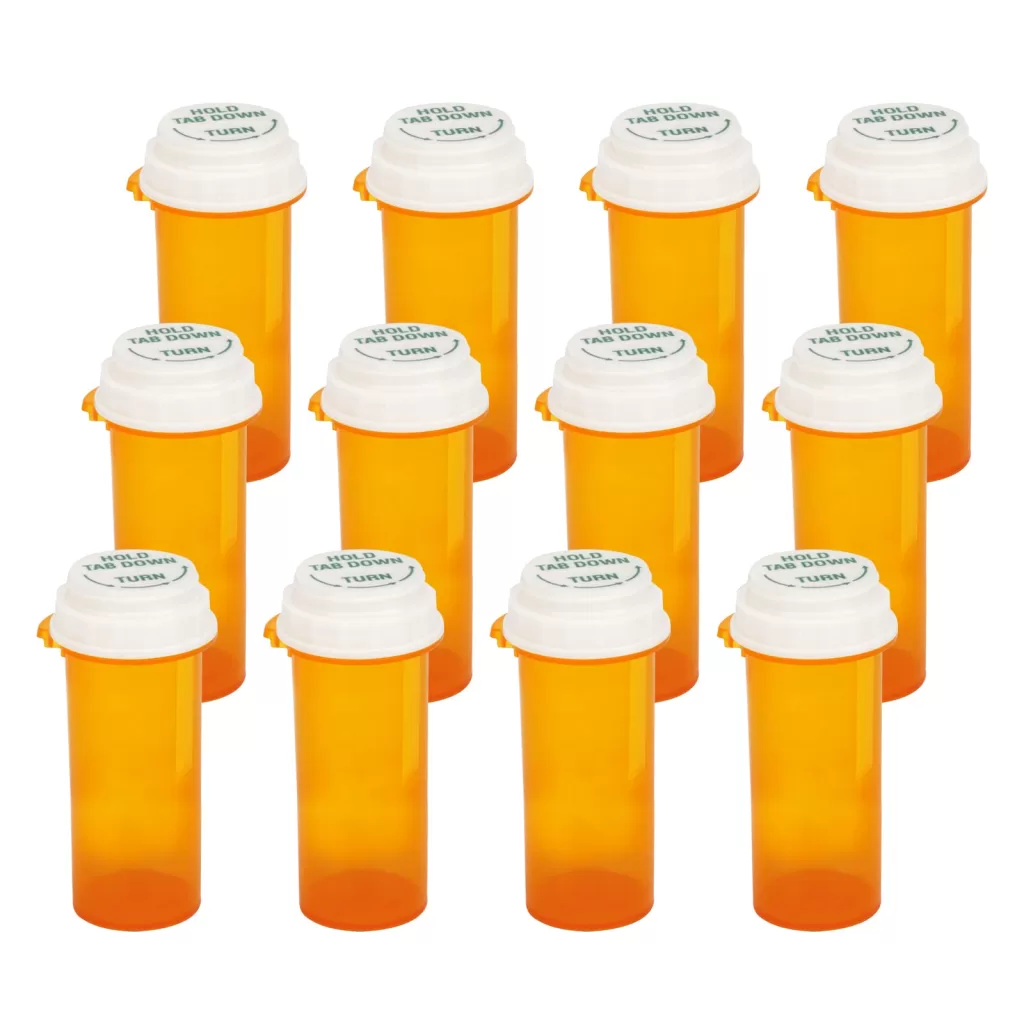
Achieve high-precision, high-quality injection molding production
Topstar’s injection molding machines combine automation and intelligence to change the Vietnamese medical consumables market. These machines meet the healthcare industry’s unique needs through process integration, automation, and advanced technology, providing a clean production environment and excellent productivity.
TRENDING POSTS
- What factors can cause delays in the injection molding process of plastic molding machine? 2025/01/13
- Exhibition Review| Topstar participates in InterPlas Thailand 2024 2025/01/13
- Star Case | Topstar helps Santong upgrade its intelligent plant 2025/01/13
- Topstar Special | National Science and Technology Workers Day 2025/01/13
HOT TOPIC
- .ervo motor-driven linear robots
- 3 axis robot
- 3 axis robots
- 3 in 1 Compact Dehumidifying Dryer
- 3-axis robot
- 3-axis robots
- 5-axis CNC machine
- accuracy
- Air Chillers
- all electric injection molding machine
- all electric injection molding machines
- All-electric injection molding machines
- and overall production quality. Therefore
- AP-RubberPlas
- automated injection molding machine
- Automation changed engineering
- automation of injection molding robots
- auxiliary machine
- Bench Injection Molding Machine
- Cabinet dryer manufacturers
- Cabinet dryers
- chiller
- CNC Drilling Machine
- CNC Drilling Machines
- cnc engraving machine manufacturer
- cnc laser cutting machine manufacturer
- CNC machine
- CNC Machine Center
- CNC Machine for Sale
- CNC Machine Manufacturing
- CNC Machine Tool
- CNC machine tool product
- CNC Machining Center
- CNC wood carving machine
- Cooling system
- Cross-Walking Single Axis Servo Cylinder Robot
- Cross-Walking Single-Axis Servo Cylinder Robot
- Cross-Walking Three-Axis/Five-Axis Servo Driven Robot
- cross-walking three-axis/five-axis servo-driven robot
- Dehumidifier Dryer
- Dehumidifying Dryer
- delta parallel robot
- Desktop Injection Molding Machine
- Desktop injection molding machines
- Desktop Molding Machine
- desktop plastic injection machine
- Desktop Plastic Injection Molding Machine
- direct clamp injection molding machine
- Direct clamp injection molding machines
- Dosing & mixing system
- Drilling Centers
- Drying and dehumidification system
- drying and dehumidifying equipment
- Drying and Dehumidifying System
- drying system
- effective and efficient. Cabinet dryers are also used in other industries where large quantities of material need to be dried
- efficient injection molding machine
- elbow hydraulic injection molding machines
- electric injection molding machine
- electric injection molding machines
- energy-efficient injection molding robot
- energy-saving injection molding machine
- etc. Among injection molding robots
- exhibition
- features of CNC machine
- Feeding And Conveying System
- Five Axis Machine Center
- Fully automatic injection molding machine
- Gathering Topstar
- giant injection molding machine
- GMU-600 5-Axis Machining Center
- Granulating & Recycling System
- Heavy duty injection molding machine
- High-precision electric molding machines
- high-precision plastic molding machines
- high-speed all electric injection molding machine
- Honeycomb rotor dehumidifier
- horizontal injection molding machine
- Horizontal Injection Molding Machines
- Horizontal Injection Moulding Machine
- Horizontal Mixer manufacturer
- How The CNC Machine Works
- hybrid injection molding machine
- hydraulic injection molding machine
- Hydraulic Injection Molding Machines
- in this article
- Industrial robot
- Industrial Robot Chinese brand
- industrial robot parts
- industrial robot supplier
- Industrial robots
- Industry Chain
- Injection Manipulator
- injection manipulator robot
- injection mold machines
- Injection molding
- Injection molding automation
- Injection Molding Automation Solution
- injection molding dryer
- Injection molding equipment
- injection molding hopper dryer
- Injection molding machine
- injection molding machine brand
- Injection Molding Machine Factory
- Injection Molding Machine Manufacture
- Injection molding machine manufacturer
- injection molding machine manufacturers
- Injection molding machine procurement
- injection molding machine robotic arm
- injection molding machine with a robot
- Injection molding machines
- injection molding material dehumidifying
- injection molding plant
- Injection Molding Robot
- injection molding robot arm
- Injection molding robot automation
- Injection molding robotic arm
- injection molding robots
- Injection moulding machine
- Injection Moulding Robots
- Injection Robot
- Injection robot arm
- Injection robot manufacturer
- Injection robot wholesale
- injection robots
- intelligent injection molding machines
- Introducing Injection Robot
- It is the best choice for drying large quantities of material at once. Cabinetmakers use these machines because they are fast
- large injection molding machine
- Learn what industrial automation and robotics is
- linear robot
- linear robots
- low speed sound-proof granulator
- machine plastic molding
- make sure to add some! Improvements (2) Keyphrase in introduction: Your keyphrase or its synonyms appear in the first paragraph of the copy
- manipulator machine
- manufacturing
- medical grade injection molding machines
- medical injection molding machine
- medical injection molding machines
- micro injection molding machine
- middle speed granulator
- Mini CNC machine manufacturers.
- Mold Temperature Control System
- mold temperature controller
- mold temperature controllers
- molding material Dehumidifying System
- mould temperature control system
- mould temperature controller
- mould temperature controllers
- New electric injection molding machine
- nitrogen dryer manufacturer
- nitrogen dryer system manufacturer
- Oil type mold temperature controller
- Oil type mold temperature controllers
- open day
- Outbound links: No outbound links appear in this page. Add some! Images: No images appear on this page. Add some! Internal links: No internal links appear in this page
- PET Preform injection molding
- phone case maker machine
- phone case making machine
- plastic bottle making machine
- plastic bottle manufacturing
- plastic bucket making machine
- plastic bucket manufacturing
- Plastic chair making machine
- plastic forming equipment
- plastic hopper dryer
- plastic injection machine
- plastic injection machines
- plastic injection molding
- Plastic injection molding equipment
- Plastic injection molding machine
- Plastic Injection Molding Machines
- plastic injection moulding machine
- plastic injection robot
- Plastic Molding machine
- Plastic Molding Machines
- plastic molding press
- plastic moulding machine
- plastic phone case making machine
- plastic-molding machine
- powerful granulator
- Powerful Type Sound-Proof Granulator
- precision injection molding
- precision injection molding machines
- production of plastic seats
- pure water mould temperature controller
- Robot injection molding
- robot injection molding machine
- robot manufacturing companies
- Robotic arm for injection molding machine
- robotic injection molding machines
- robotics in injection molding
- SCARA robot
- SCARA robots
- Service-oriented manufacturing
- Servo Cylinder Robot
- servo driven robot
- Servo Driven Robots
- servo injection robots
- servo motor-driven linear robots
- servo-driven 3-axis robot
- Servo-Driven Robot
- Setup of injection machine
- Silicone Injection Molding Machine
- six-axis industrial robot
- Stainless Hopper Dryer
- Stainless Hopper Dryers
- star club
- swing arm robot
- take-out robots
- the choice between servo-driven robots and hydraulic robots will have a certain impact on efficiency
- the most popular injection molding machine
- the type of injection molding robot
- toggle clamp injection molding machine
- Toggle Hydraulic Injection Molding Machines
- toggle injection molding machine
- Top 10 brands of injection robots
- Topstar
- Topstar Engineering
- Topstar Industrial Robots
- Topstar injection molding intelligent
- Topstar Scara Robots
- Useful Injection molding machine
- Vertical machining centers
- volumetric type blender
- water chiller
- water chillers
- water distributor
- water type mold temperature controller
- Water Type MoldTemperature Controller
- Water-Type Mould Temperature Controllers
- We often face choices when performing injection molding. We will choose the type of injection molding machine
- wholesale of injection molding machines
- x carve CNC