What is a Linear guide, and why is it important in plastic injection molding machines?
2024/12/23 By Topstar
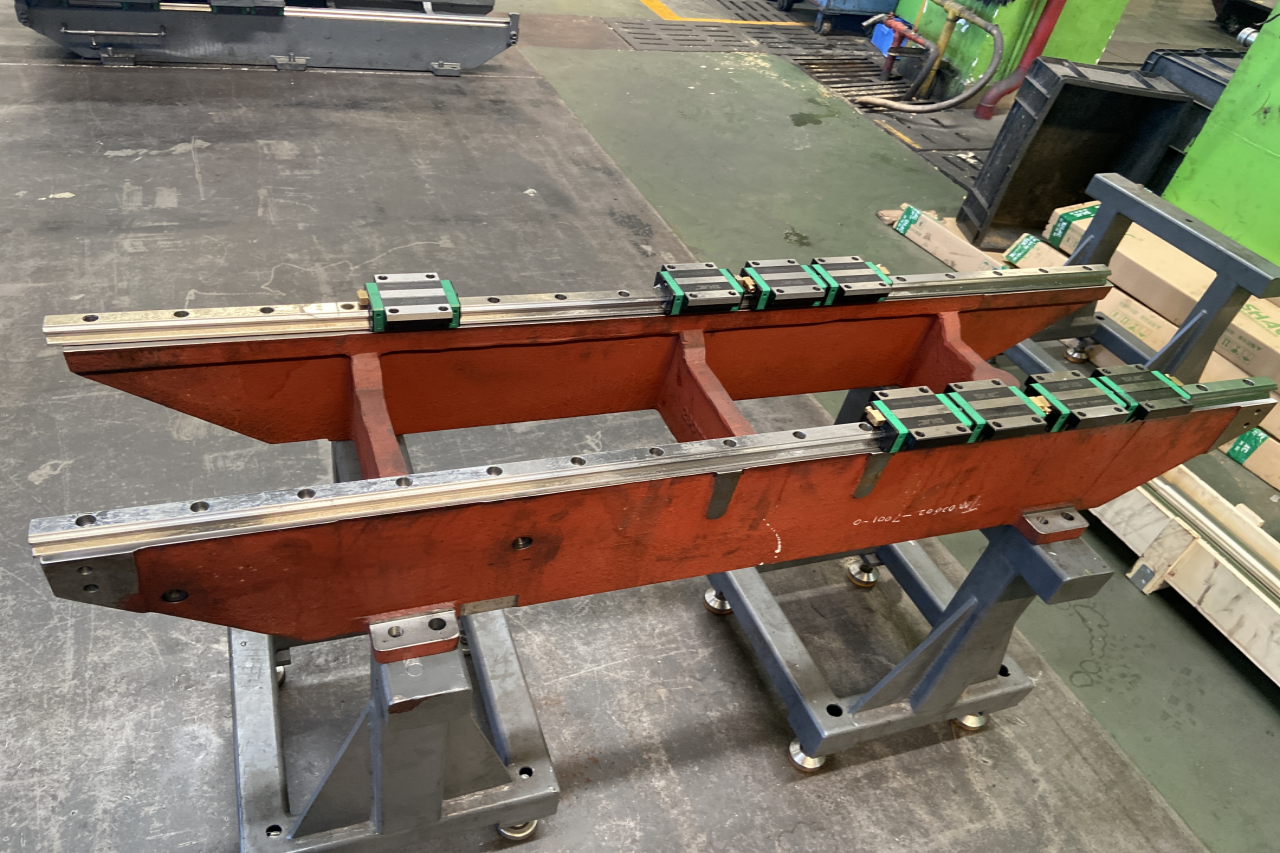
Plastic injection molding machines can efficiently and accurately produce a variety of products. Topstar uses linear guides and specialized components that improve the molding process’s accuracy, stability, and overall performance to make the injection more accurate and stable. Linear guides ensure that plastic injection molding machines can continue to produce high-quality parts even in high-volume, high-speed production environments. In this article, we will introduce linear guides, how they work, and why they are essential to achieving the precision and stability of plastic injection molding machines.
What are linear guides in plastic injection molding machines?
Linear guides are usually installed on the track that guides the injection unit or movable platen to promote smooth and precise linear motion in the machinery. We integrate linear guides into the design of plastic injection molding machines to support and guide the movement of injection units, mold platens, and clamping systems. Its primary purpose is to ensure that parts move in a controlled and stable manner during injection and clamping. Unlike traditional sliding mechanisms that rely on sliding contact, linear guides use rolling elements (such as ball bearings or rollers) to achieve low-friction motion. This design enables smoother, more precise motion, even under heavy loads. Linear guides help improve the machine’s overall performance and reliability by reducing friction and providing smooth motion.
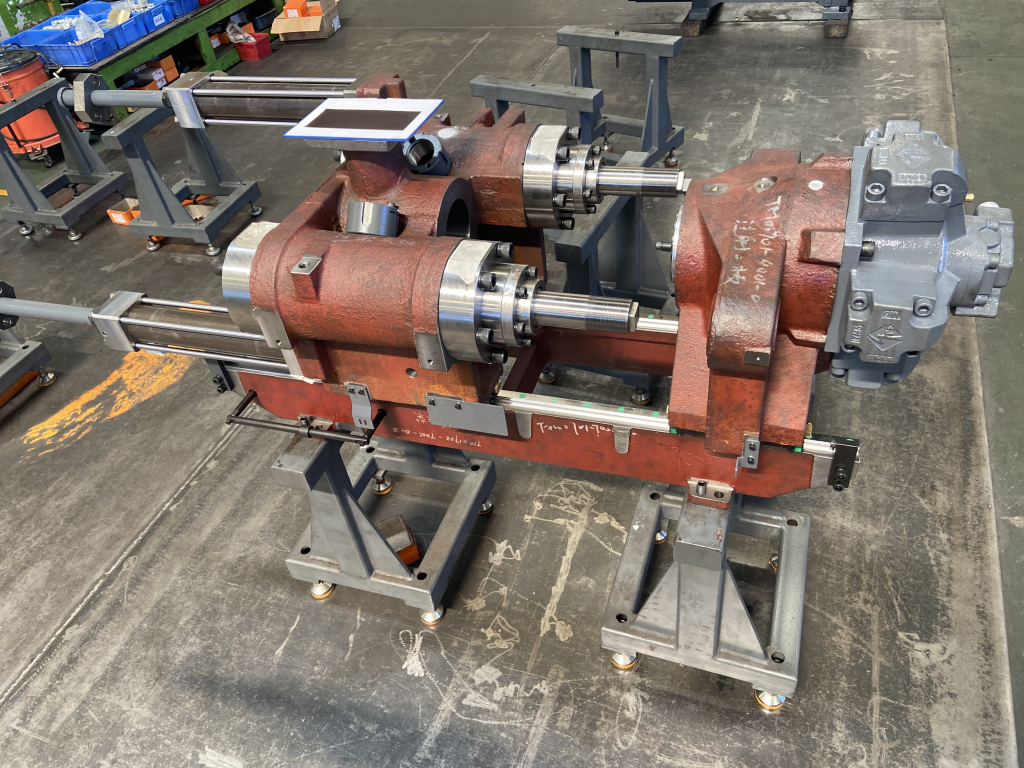
How do linear guides improve injection accuracy?
One of the main advantages of using linear guides in plastic injection molding machines is their ability to improve injection accuracy. The injection process requires precise movement of the injection unit, which requires the correct speed, pressure, and position to deliver the molten plastic into the mold cavity. Any deviation in the movement of the injection unit can cause defects in the final product, such as short shots, flash, or dimensional inaccuracies.
The integration of linear guides ensures that the injection unit moves along a fixed path with minimal deviation, thereby precisely controlling the injection process. The rolling elements within the linear guides enable smooth and consistent motion, eliminating the jitter or hesitation that can occur with traditional sliding mechanisms. This stability ensures that the molten plastic is injected evenly, resulting in parts with consistent quality and tight tolerances. For manufacturers, the improved injection accuracy brought about by linear guides means higher quality products, less waste, and fewer defects.
Role in enhancing stability
The stability of the operation of plastic injection molding machines can also affect the quality of the final product. Linear guides can improve the stability of the moving parts of plastic injection molding machines, ensuring that they remain aligned and balanced throughout the molding process. This stability is crucial when running at high speeds or using heavy molds. In addition, using linear guides can reduce the risk of vibration and mechanical clearance in traditional sliding mechanisms. By providing a stable moving platform, linear guides help maintain the alignment of the mold platen and injection unit, ensuring that the clamping force is evenly distributed and the mold remains adequately closed during the injection process. At the same time, the stability brought by linear guides can also reduce wear on machine components, extend their service life, and reduce maintenance.
Improve production efficiency with linear guides.
Linear guides can make the parts of injection molding machines move faster and more efficiently. Their low-friction design allows for rapid acceleration and deceleration, minimizing the time required for the injection unit and mold platen to move between different positions. The smooth movement provided can also reduce the risk of delays due to sticking or misalignment, ensuring that each cycle runs seamlessly. This improved efficiency enables plastic injection molding machines to produce more parts in a shorter time, thereby improving overall productivity and reducing the cost of each part. Faster, more efficient movement also reduces wear on machine components, extending their life and minimizing maintenance requirements.
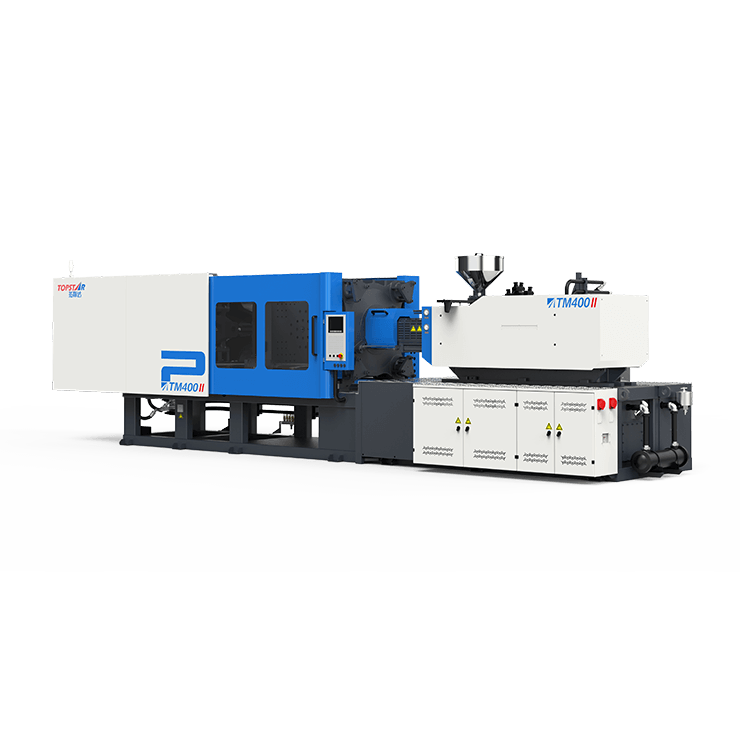
Makes plastic injection molding machines more durable
The rigorous nature of the injection molding process places tremendous stress on moving parts. Linear guides are designed to withstand heavy loads, high speeds, and repetitive motion, ensuring they can operate reliably over long periods. Made with high-quality materials and precision engineering, linear guides resist wear and deformation even in harsh conditions. This durability extends the guides’ life and helps protect other machine components by reducing mechanical stress and ensuring smooth operation. For manufacturers, the long-lasting performance of linear guides means fewer replacements and repairs, resulting in lower maintenance costs and less downtime.
Makes injection more precise and stable
Capable of improving injection accuracy, reducing cycle times, and ensuring consistent part quality, linear guides in Topstar plastic injection molding machines are essential for manufacturers seeking to optimize operations and provide high-quality products. Linear guides help ensure that your injection is more precise and stable.
TRENDING POSTS
- What factors can cause delays in the injection molding process of plastic molding machine? 2024/12/23
- Exhibition Review| Topstar participates in InterPlas Thailand 2024 2024/12/23
- Star Case | Topstar helps Santong upgrade its intelligent plant 2024/12/23
- Topstar Special | National Science and Technology Workers Day 2024/12/23
HOT TOPIC
- 3 in 1 Compact Dehumidifying Dryer
- 5-axis CNC machine
- accuracy
- Air Chillers
- all electric injection molding machine
- all electric injection molding machines
- All-electric injection molding machines
- and overall production quality. Therefore
- AP-RubberPlas
- automated injection molding machine
- Automation changed engineering
- automation of injection molding robots
- auxiliary machine
- Bench Injection Molding Machine
- Cabinet dryer manufacturers
- Cabinet dryers
- chiller
- CNC Drilling Machine
- CNC Drilling Machines
- cnc engraving machine manufacturer
- cnc laser cutting machine manufacturer
- CNC machine
- CNC Machine Center
- CNC Machine for Sale
- CNC Machine Manufacturing
- CNC Machine Tool
- CNC machine tool product
- CNC Machining Center
- CNC wood carving machine
- Cooling system
- Cross-Walking Single Axis Servo Cylinder Robot
- Cross-Walking Single-Axis Servo Cylinder Robot
- Cross-Walking Three-Axis/Five-Axis Servo Driven Robot
- cross-walking three-axis/five-axis servo-driven robot
- Dehumidifier Dryer
- Dehumidifying Dryer
- delta parallel robot
- Desktop Injection Molding Machine
- Desktop injection molding machines
- Desktop Molding Machine
- desktop plastic injection machine
- Desktop Plastic Injection Molding Machine
- direct clamp injection molding machine
- Direct clamp injection molding machines
- Dosing & mixing system
- Drilling Centers
- Drying and dehumidification system
- drying and dehumidifying equipment
- Drying and Dehumidifying System
- drying system
- effective and efficient. Cabinet dryers are also used in other industries where large quantities of material need to be dried
- efficient injection molding machine
- elbow hydraulic injection molding machines
- electric injection molding machine
- electric injection molding machines
- energy-saving injection molding machine
- etc. Among injection molding robots
- exhibition
- features of CNC machine
- Feeding And Conveying System
- Five Axis Machine Center
- Fully automatic injection molding machine
- Gathering Topstar
- giant injection molding machine
- GMU-600 5-Axis Machining Center
- Granulating & Recycling System
- Heavy duty injection molding machine
- Honeycomb rotor dehumidifier
- horizontal injection molding machine
- Horizontal Injection Molding Machines
- Horizontal Injection Moulding Machine
- Horizontal Mixer manufacturer
- How The CNC Machine Works
- hybrid injection molding machine
- hydraulic injection molding machine
- Hydraulic Injection Molding Machines
- in this article
- Industrial robot
- Industrial Robot Chinese brand
- industrial robot parts
- industrial robot supplier
- Industrial robots
- Industry Chain
- Injection Manipulator
- injection mold machines
- Injection molding
- Injection molding automation
- Injection Molding Automation Solution
- injection molding dryer
- Injection molding equipment
- injection molding hopper dryer
- Injection molding machine
- injection molding machine brand
- Injection Molding Machine Factory
- Injection Molding Machine Manufacture
- Injection molding machine manufacturer
- injection molding machine manufacturers
- Injection molding machine procurement
- injection molding machine robotic arm
- injection molding machine with a robot
- Injection molding machines
- injection molding material dehumidifying
- injection molding plant
- Injection Molding Robot
- injection molding robot arm
- Injection molding robot automation
- Injection molding robotic arm
- injection molding robots
- Injection Moulding Robots
- Injection Robot
- Injection robot arm
- Injection robot manufacturer
- Injection robot wholesale
- injection robots
- intelligent injection molding machines
- Introducing Injection Robot
- It is the best choice for drying large quantities of material at once. Cabinetmakers use these machines because they are fast
- large injection molding machine
- Learn what industrial automation and robotics is
- low speed sound-proof granulator
- machine plastic molding
- make sure to add some! Improvements (2) Keyphrase in introduction: Your keyphrase or its synonyms appear in the first paragraph of the copy
- manipulator machine
- manufacturing
- micro injection molding machine
- middle speed granulator
- Mini CNC machine manufacturers.
- Mold Temperature Control System
- mold temperature controller
- molding material Dehumidifying System
- mould temperature controller
- mould temperature controllers
- New electric injection molding machine
- nitrogen dryer manufacturer
- nitrogen dryer system manufacturer
- Oil type mold temperature controller
- open day
- Outbound links: No outbound links appear in this page. Add some! Images: No images appear on this page. Add some! Internal links: No internal links appear in this page
- PET Preform injection molding
- phone case maker machine
- phone case making machine
- plastic bottle making machine
- plastic bottle manufacturing
- plastic bucket making machine
- plastic bucket manufacturing
- Plastic chair making machine
- plastic forming equipment
- plastic hopper dryer
- plastic injection machine
- plastic injection machines
- plastic injection molding
- Plastic injection molding equipment
- Plastic injection molding machine
- Plastic Injection Molding Machines
- plastic injection robot
- Plastic Molding machine
- Plastic Molding Machines
- plastic molding press
- plastic phone case making machine
- plastic-molding machine
- powerful granulator
- Powerful Type Sound-Proof Granulator
- production of plastic seats
- Robot injection molding
- robot injection molding machine
- robot manufacturing companies
- Robotic arm for injection molding machine
- robotic injection molding machines
- robotics in injection molding
- SCARA robot
- SCARA robots
- Service-oriented manufacturing
- Servo Cylinder Robot
- servo driven robot
- Servo Driven Robots
- servo injection robots
- Servo-Driven Robot
- Setup of injection machine
- Silicone Injection Molding Machine
- six-axis industrial robot
- Stainless Hopper Dryer
- Stainless Hopper Dryers
- star club
- swing arm robot
- the choice between servo-driven robots and hydraulic robots will have a certain impact on efficiency
- the most popular injection molding machine
- the type of injection molding robot
- toggle clamp injection molding machine
- Toggle Hydraulic Injection Molding Machines
- toggle injection molding machine
- Top 10 brands of injection robots
- Topstar
- Topstar Engineering
- Topstar Industrial Robots
- Topstar injection molding intelligent
- Topstar Scara Robots
- Useful Injection molding machine
- Vertical machining centers
- volumetric type blender
- water chiller
- water chillers
- water distributor
- Water Type MoldTemperature Controller
- We often face choices when performing injection molding. We will choose the type of injection molding machine
- wholesale of injection molding machines
- x carve CNC