Home / What impact does material viscosity have on injection molding machine performance?
What impact does material viscosity have on injection molding machine performance?
2024/12/11 By Topstar
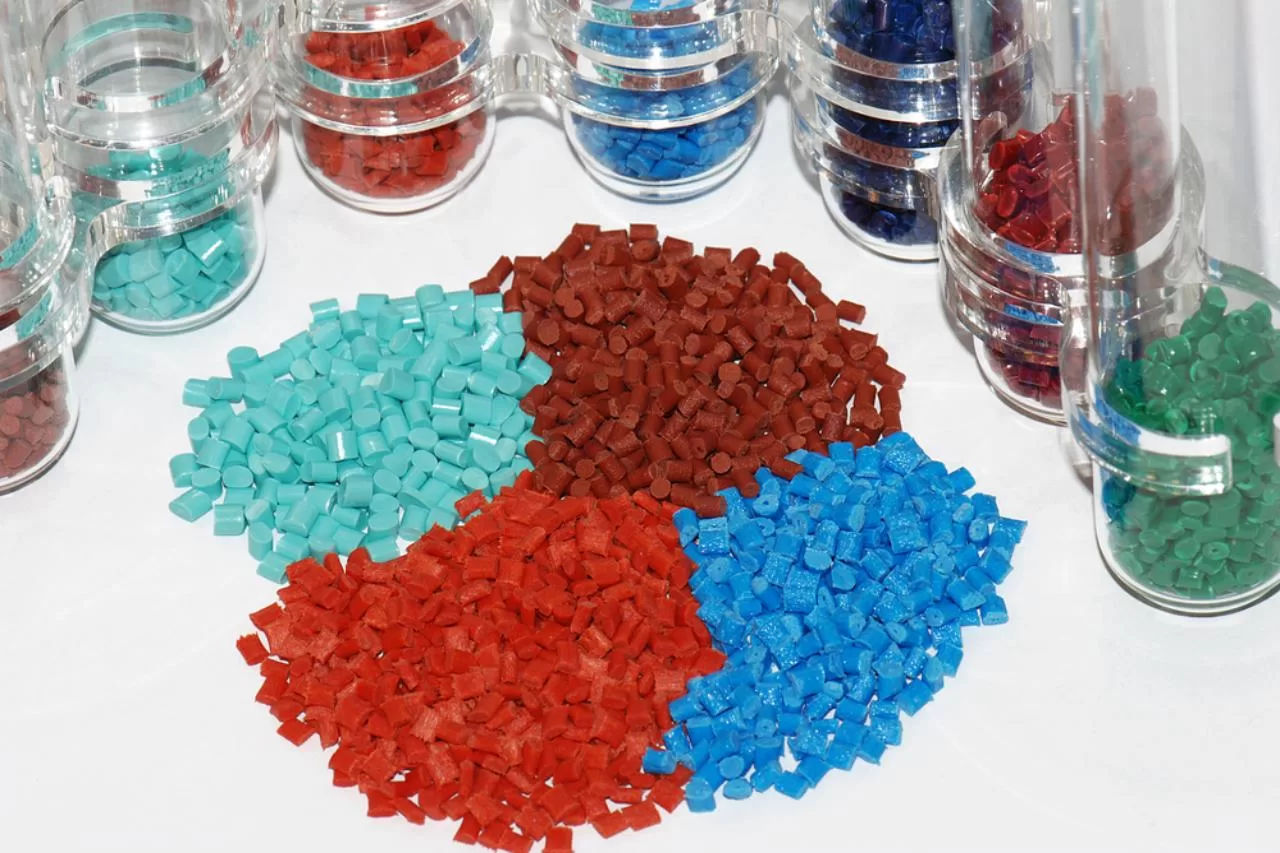
The viscosity of the materials used in injection molding refers to the fluid’s resistance to flow, which can impact how the material behaves in an injection molding machine. The type of material being injected (whether it is a thermoplastic, thermoset, or elastomer) directly affects the viscosity, affecting the overall performance of the injection molding machine. Material flow, fill speed, cycle time, and product quality are all affected by viscosity. This article will explore the impact of material viscosity on an injection molding machine’s performance and how Topstar’s machines are designed to handle a wide range of material viscosities effectively.
How does viscosity affect material flow in an injection molding machine?
The most obvious effect of material viscosity is its effect on how easily the material flows through the injection molding machine. Materials with higher viscosities, such as thick plastics or highly filled compounds, tend to flow more slowly and require you to apply more force and pressure to inject them into the mold, which can increase cycle time. Conversely, materials with lower viscosities, such as certain elastomers or resins, flow more easily and require less pressure, resulting in faster injection speeds. An injection molding machine that does not match the material viscosity may experience problems such as incomplete mold filling, uneven cooling, or long cycle times, affecting product quality and production efficiency.
The impact of high-viscosity materials on injection molding machine performance
High-viscosity materials require more pressure to pass through the injection molding system. These materials are generally more difficult to flow, so the injection molding machine must generate higher pressure to overcome this resistance. Manufacturers using high-viscosity materials must ensure that their injection molding machines provide enough pressure and heating for smooth and consistent flow. Topstar equips its injection molding machines with powerful servo motors, high-quality precision PVD three small parts, double-shot transfer cylinders, and uniform force on the shooting platform. These machines feature fast injection speed, electroplated screw design, and an upgraded nozzle configuration to ensure smooth flow of high-viscosity materials, thereby shortening cycle time and improving efficiency.
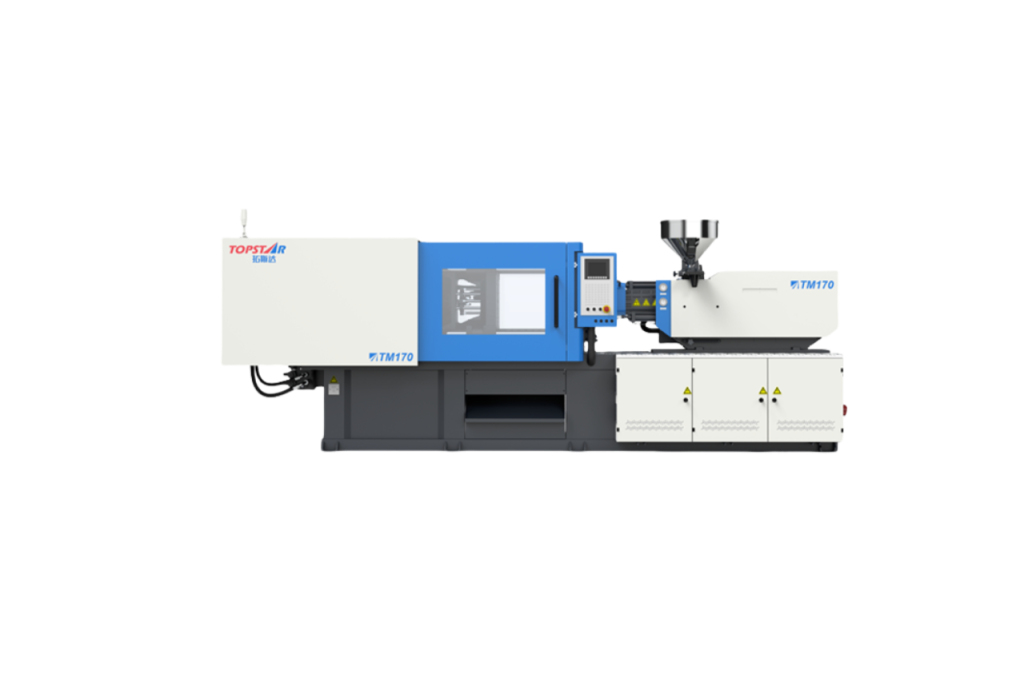
The impact of low-viscosity materials
Low-viscosity materials can also cause problems in the injection molding process. Low-viscosity materials flow too fast, which can cause overfilling, excessive overflow, or insufficient injection in the mold cavity, especially when you do not properly adjust the pressure and speed of the injection molding machine. Topstar uses the double-shot transfer cylinders to make the shooting platform move with uniform force, and the linear guide rails make the injection more stable. You use proportional back pressure control in the pre-plasticization stage, which is easy to operate and achieves multi-stage back pressure settings to improve plasticization quality. You address these issues by controlling injection speed and pressure, enabling manufacturers to fine-tune their processes to handle low-viscosity materials and ensure even material distribution effectively.
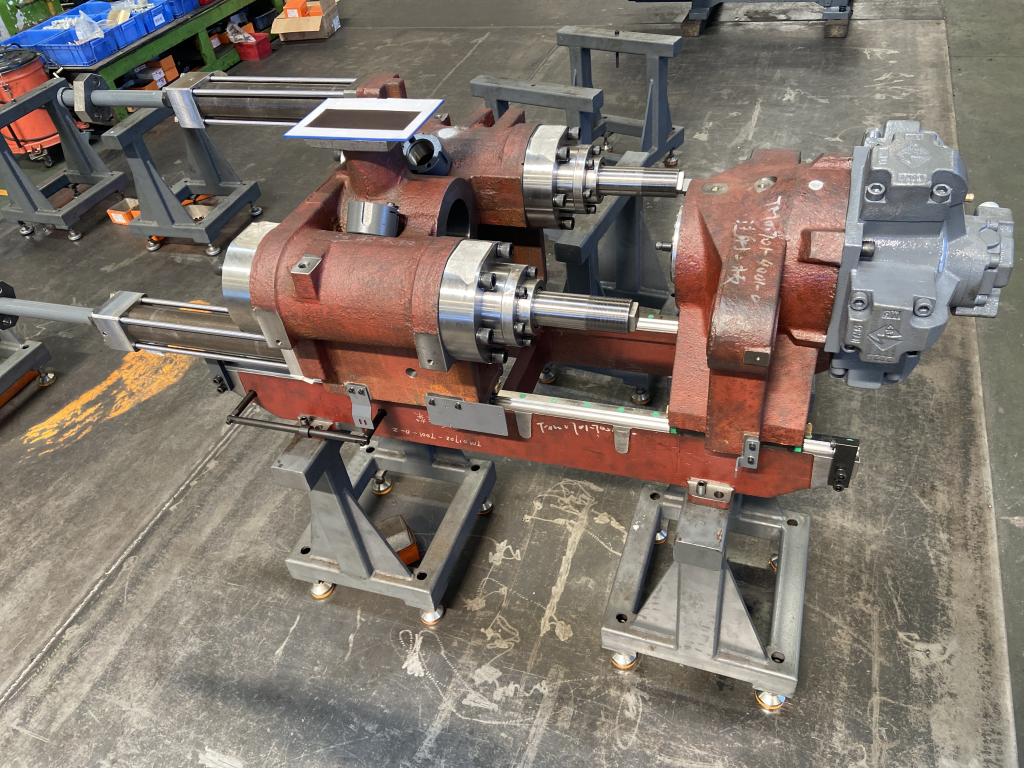
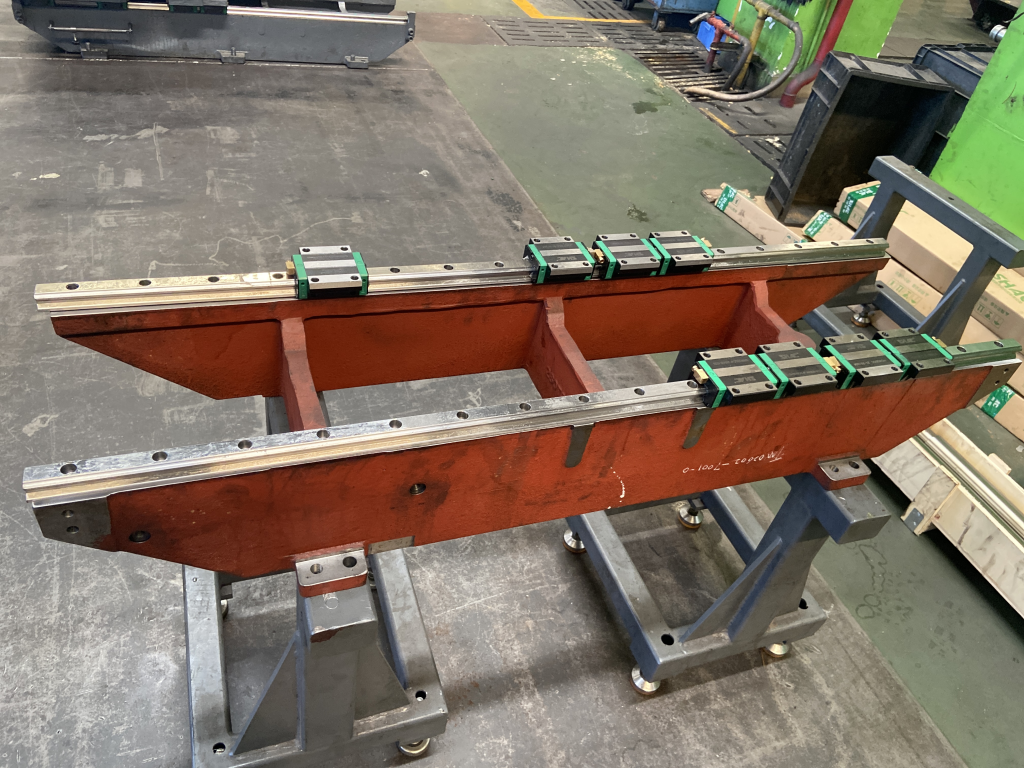
Temperature Control and Viscosity
The viscosity of most materials is temperature dependent, meaning that the material’s flow characteristics will change depending on the temperature it is heated to during the injection molding process. If the material is warm, it will be more viscous, resulting in better flow and mold filling. On the other hand, if you overheat the material, it may degrade, affecting the quality of the final product. Topstar equips its range of injection molding machines with advanced temperature control systems to ensure you heat the material to the optimal injection temperature. They feature precise heating elements and cooling systems that allow manufacturers to maintain consistent material temperatures throughout the injection cycle. Temperature control at the feed port allows for more efficient production and more precise, higher-quality parts, and it reduces the likelihood of molding defects caused by inconsistent material flow.
Optimizing Material Flow for Different Viscosities in Injection Molding
Optimizing material flow for different viscosities is critical to maximizing injection molding performance. The key is to balance factors such as injection pressure, injection speed, barrel temperature, and mold temperature to ensure the material flows smoothly into the mold cavity without causing defects.
Topstar’s injection molding machines are all equipped with electroplated screw configurations and self-developed control systems as standard, allowing manufacturers to optimize the flow of materials at any viscosity level. You can customize the precise screw design according to the characteristics of specific materials to ensure optimal flow and consistency. For example, customers who use PC materials to make light guide plates require injection pressures above 1800kgf/cm², and we generally use chrome-plated screws or bimetallic screws. In addition, Topstar also provides a computer operation interface that allows users to fine-tune the injection process for each specific material viscosity. This helps manufacturers obtain consistent, high-quality parts.
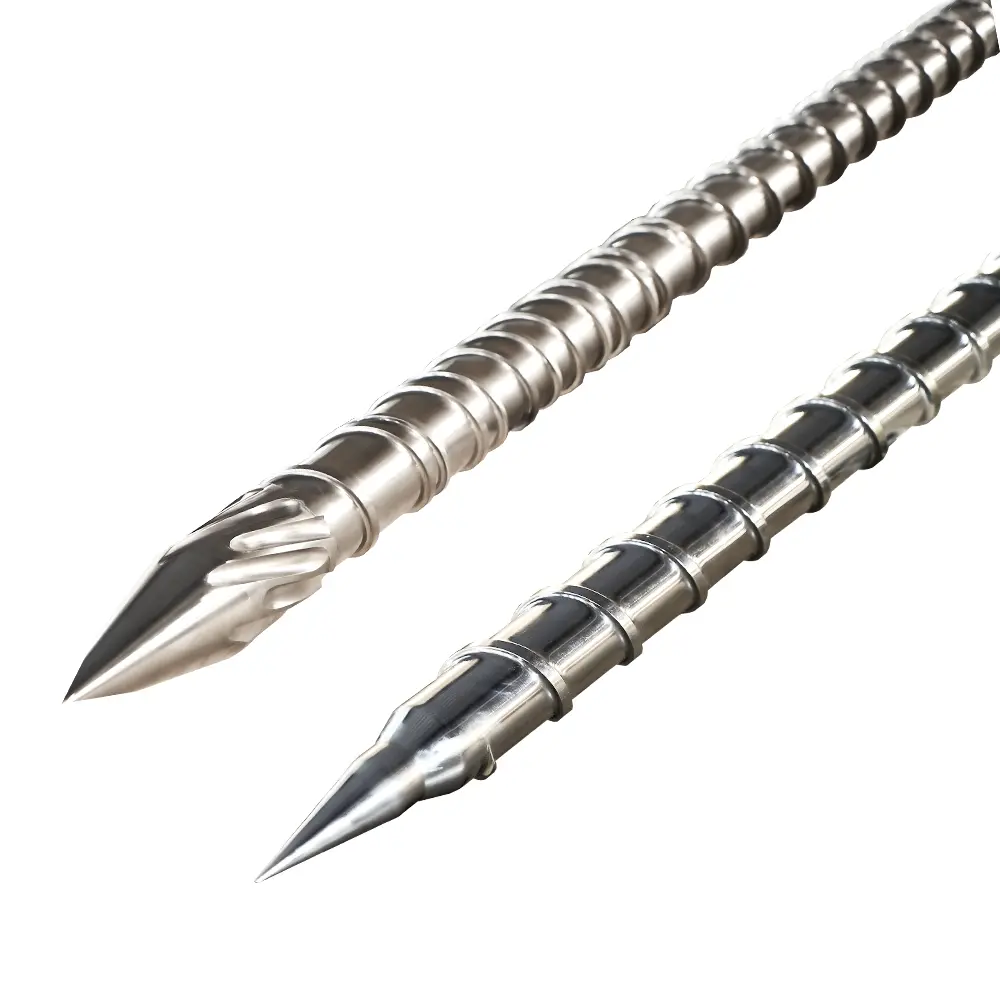
Control material viscosity to improve injection molding performance
Material viscosity is a key factor in injection molding and significantly impacts machine performance, production efficiency, and final product quality. Whether using high-viscosity or low-viscosity materials, it is necessary to ensure that its injection molding machine can effectively handle these materials. The injection molding machines provided by Topstar are designed to handle materials of various viscosities through advanced features such as precision temperature control, adjustable injection speed, and customized screw design. Enable manufacturers to optimize material flow, shorten cycle time, and maintain consistent product quality.
TRENDING POSTS
- What factors can cause delays in the injection molding process of plastic molding machine? 2024/12/11
- Exhibition Review| Topstar participates in InterPlas Thailand 2024 2024/12/11
- Star Case | Topstar helps Santong upgrade its intelligent plant 2024/12/11
- Topstar Special | National Science and Technology Workers Day 2024/12/11
HOT TOPIC
- 3 in 1 Compact Dehumidifying Dryer
- 5-axis CNC machine
- accuracy
- Air Chillers
- all electric injection molding machine
- All-electric injection molding machines
- and overall production quality. Therefore
- AP-RubberPlas
- automated injection molding machine
- Automation changed engineering
- automation of injection molding robots
- auxiliary machine
- Bench Injection Molding Machine
- Cabinet dryer manufacturers
- Cabinet dryers
- chiller
- CNC Drilling Machine
- CNC Drilling Machines
- cnc engraving machine manufacturer
- cnc laser cutting machine manufacturer
- CNC machine
- CNC Machine Center
- CNC Machine for Sale
- CNC Machine Manufacturing
- CNC Machine Tool
- CNC machine tool product
- CNC Machining Center
- CNC wood carving machine
- Cooling system
- Cross-Walking Single Axis Servo Cylinder Robot
- Cross-Walking Single-Axis Servo Cylinder Robot
- Cross-Walking Three-Axis/Five-Axis Servo Driven Robot
- cross-walking three-axis/five-axis servo-driven robot
- Dehumidifier Dryer
- Dehumidifying Dryer
- delta parallel robot
- Desktop Injection Molding Machine
- Desktop injection molding machines
- Desktop Molding Machine
- desktop plastic injection machine
- Desktop Plastic Injection Molding Machine
- direct clamp injection molding machine
- Direct clamp injection molding machines
- Dosing & mixing system
- Drilling Centers
- Drying and dehumidification system
- drying and dehumidifying equipment
- Drying and Dehumidifying System
- drying system
- effective and efficient. Cabinet dryers are also used in other industries where large quantities of material need to be dried
- efficient injection molding machine
- elbow hydraulic injection molding machines
- electric injection molding machine
- electric injection molding machines
- etc. Among injection molding robots
- exhibition
- features of CNC machine
- Feeding And Conveying System
- Five Axis Machine Center
- Fully automatic injection molding machine
- Gathering Topstar
- giant injection molding machine
- GMU-600 5-Axis Machining Center
- Granulating & Recycling System
- Heavy duty injection molding machine
- Honeycomb rotor dehumidifier
- horizontal injection molding machine
- Horizontal Injection Molding Machines
- Horizontal Injection Moulding Machine
- Horizontal Mixer manufacturer
- How The CNC Machine Works
- hybrid injection molding machine
- hydraulic injection molding machine
- Hydraulic Injection Molding Machines
- in this article
- Industrial robot
- Industrial Robot Chinese brand
- industrial robot parts
- industrial robot supplier
- Industrial robots
- Industry Chain
- Injection Manipulator
- injection mold machines
- Injection molding
- Injection molding automation
- Injection Molding Automation Solution
- injection molding dryer
- Injection molding equipment
- injection molding hopper dryer
- Injection molding machine
- injection molding machine brand
- Injection Molding Machine Factory
- Injection Molding Machine Manufacture
- Injection molding machine manufacturer
- injection molding machine manufacturers
- Injection molding machine procurement
- injection molding machine robotic arm
- injection molding machine with a robot
- Injection molding machines
- injection molding material dehumidifying
- injection molding plant
- Injection Molding Robot
- injection molding robot arm
- Injection molding robot automation
- Injection molding robotic arm
- injection molding robots
- Injection Moulding Robots
- Injection Robot
- Injection robot arm
- Injection robot manufacturer
- Injection robot wholesale
- injection robots
- intelligent injection molding machines
- Introducing Injection Robot
- It is the best choice for drying large quantities of material at once. Cabinetmakers use these machines because they are fast
- large injection molding machine
- Learn what industrial automation and robotics is
- low speed sound-proof granulator
- machine plastic molding
- make sure to add some! Improvements (2) Keyphrase in introduction: Your keyphrase or its synonyms appear in the first paragraph of the copy
- manipulator machine
- manufacturing
- micro injection molding machine
- middle speed granulator
- Mini CNC machine manufacturers.
- Mold Temperature Control System
- mold temperature controller
- molding material Dehumidifying System
- mould temperature controller
- mould temperature controllers
- New electric injection molding machine
- nitrogen dryer manufacturer
- nitrogen dryer system manufacturer
- Oil type mold temperature controller
- open day
- Outbound links: No outbound links appear in this page. Add some! Images: No images appear on this page. Add some! Internal links: No internal links appear in this page
- PET Preform injection molding
- phone case maker machine
- phone case making machine
- plastic bottle making machine
- plastic bottle manufacturing
- plastic bucket making machine
- plastic bucket manufacturing
- Plastic chair making machine
- plastic forming equipment
- plastic hopper dryer
- plastic injection machine
- plastic injection machines
- plastic injection molding
- Plastic injection molding equipment
- Plastic injection molding machine
- Plastic Injection Molding Machines
- plastic injection robot
- Plastic Molding machine
- Plastic Molding Machines
- plastic molding press
- plastic phone case making machine
- plastic-molding machine
- powerful granulator
- Powerful Type Sound-Proof Granulator
- production of plastic seats
- Robot injection molding
- robot injection molding machine
- robot manufacturing companies
- Robotic arm for injection molding machine
- robotic injection molding machines
- robotics in injection molding
- SCARA robot
- SCARA robots
- Service-oriented manufacturing
- Servo Cylinder Robot
- servo driven robot
- Servo Driven Robots
- servo injection robots
- Servo-Driven Robot
- Setup of injection machine
- Silicone Injection Molding Machine
- six-axis industrial robot
- Stainless Hopper Dryer
- Stainless Hopper Dryers
- star club
- swing arm robot
- the choice between servo-driven robots and hydraulic robots will have a certain impact on efficiency
- the most popular injection molding machine
- the type of injection molding robot
- toggle clamp injection molding machine
- Toggle Hydraulic Injection Molding Machines
- toggle injection molding machine
- Top 10 brands of injection robots
- Topstar
- Topstar Engineering
- Topstar Industrial Robots
- Topstar injection molding intelligent
- Topstar Scara Robots
- Useful Injection molding machine
- Vertical machining centers
- volumetric type blender
- water chiller
- water chillers
- water distributor
- Water Type MoldTemperature Controller
- We often face choices when performing injection molding. We will choose the type of injection molding machine
- wholesale of injection molding machines
- x carve CNC