What are the benefits of equipment interconnection for horizontal injection molding machine?
2024/11/22 By Topstar
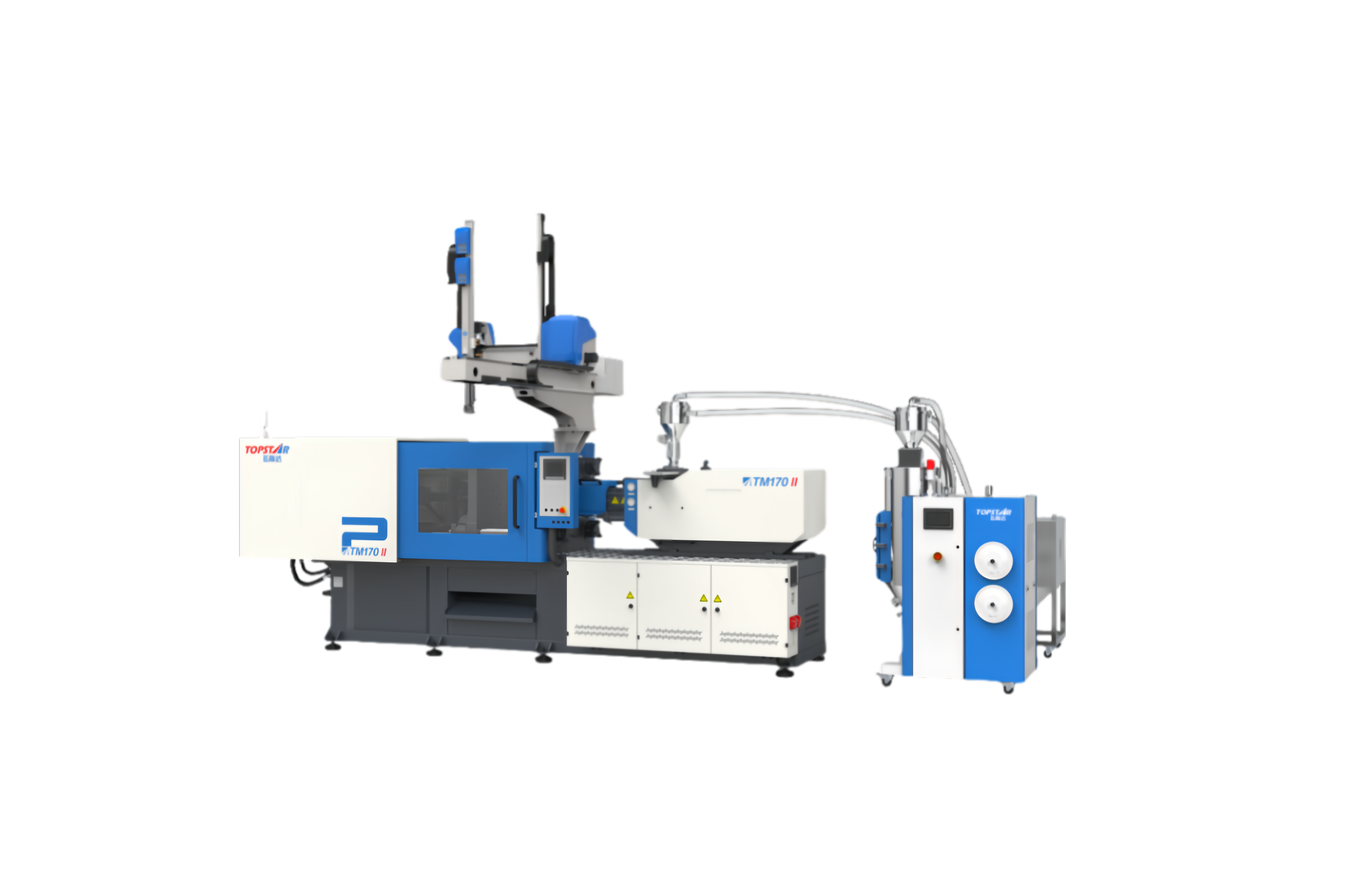
In current injection molding production, the product line of peripheral auxiliary machines is very long. Technical upgrades can provide customers with excellent equipment, but they do not necessarily guarantee customers’ production results. Topstar proposed the “injection molding process machine” concept based on existing technology to simplify customer production, management, and operation. It pays more attention to the system interconnection capabilities of horizontal injection molding machines and peripheral equipment and uses an integrated and open system. Realize the integration of the main machine, auxiliary machine, and automatic control, thereby improving the efficiency of the production cycle. In this guide, we will explore how equipment interconnection can enhance the performance of horizontal injection molding machine and the efficiency of entire injection molding production.
Providing horizontal injection molding machine efficiency through equipment interconnection
Equipment interconnection integrates software and hardware and continuously improves equipment intelligence through communication, control, optimization, and perception. By connecting multiple devices and systems, a control interface is realized to link with various devices, and the entire injection molding process, including injection molding pretreatment, plasticization, molding control, and removal process, is optimized. The best control of injection molding factors, such as temperature, speed, position, pressure, time, etc., is achieved through system integration interconnection, main and auxiliary machine combination, and sensing technology.
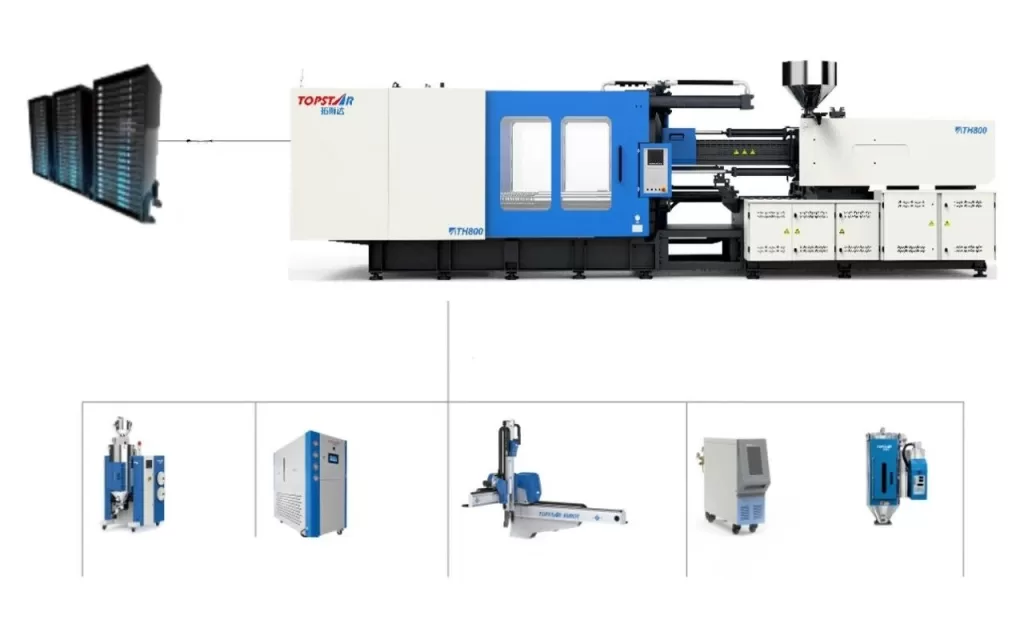
Operators can monitor and adjust machine parameters throughout the production workshop in real-time through the centralized control system. For example, operators can immediately implement changes in injection speed, pressure, or mold temperature without manually accessing each machine. This interconnection reduces downtime and ensures optimal performance, even in high-volume production environments.
Improving the quality of horizontal injection molding machine production through interconnection
Product quality is a top priority, especially in the automotive, healthcare, and electronics industries. The automatic compensation function of the mold opening position brought by the interconnection with the injection molding robot can realize the precise grasping and placement of the injection molding robot during high-speed mold opening operation, making production more stable and efficient. The integrated operation is realized through the host call signal, and the control system automatically optimizes the removal process to improve the injection molding efficiency of the production line. It solves the product quality problem caused by ejection position deviation and uncoordinated suction time, resulting in removal failure and equipment alarm shutdown.
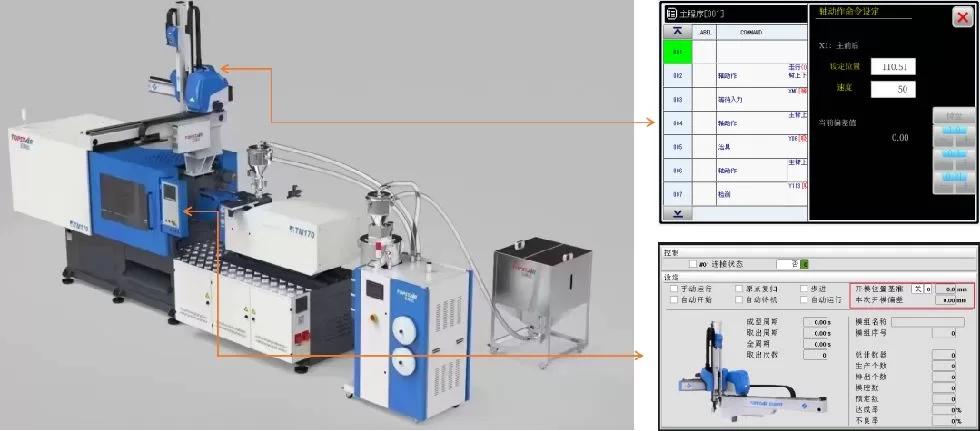
The interconnected injection molding machine can communicate with the quality control system to ensure that each part meets precise specifications. For example, if there is a deviation in mold temperature or injection pressure, the system can immediately adjust the parameters or stop production to prevent part defects.
Cost savings from equipment interconnection
This integration can indirectly save costs when horizontal injection molding machines can interconnect equipment. Automatic coordination between injection molding equipment ensures precise injection volume and reduces errors, thereby minimizing material waste. For example, the interconnected system can detect inconsistencies in raw material feed rates or temperature fluctuations and make real-time adjustments to maintain consistency, preventing the overuse of expensive materials and minimizing scrap.
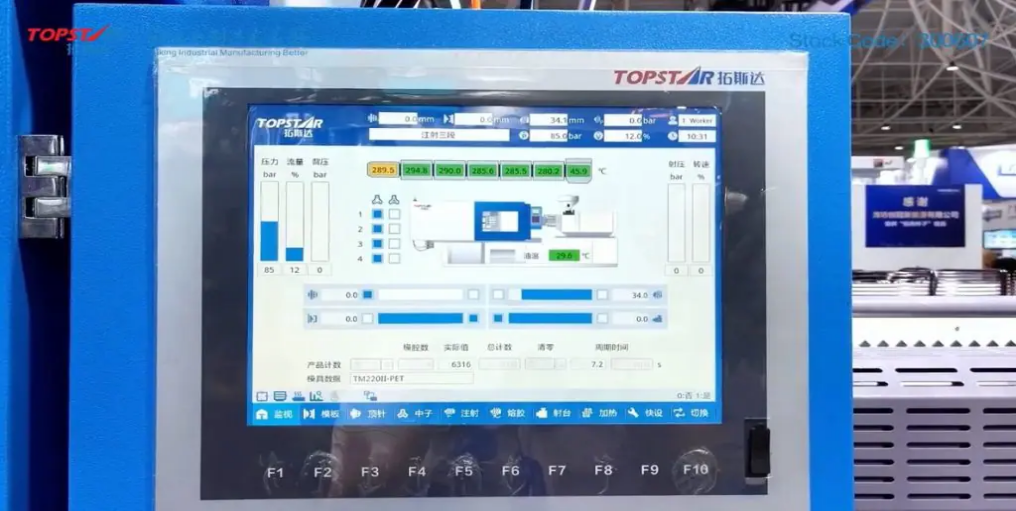
In addition, predictive maintenance reduces expensive breakdowns and repairs. By detecting wear early, manufacturers can schedule maintenance during planned downtime and avoid interruptions to production schedules. Interconnection enhances energy efficiency, allowing machines to operate synchronously, reduce idle time, and optimize power use.
Scalability and flexibility
Equipment interconnection improves the scalability and flexibility of horizontal injection molding machines and the entire production, allowing manufacturers to quickly adapt to changing market needs. You can integrate more machines into the interconnected network without interrupting existing workflows. The centralized control system automatically updates and coordinates new equipment to ensure seamless expansion. The software system of integrated control further enhances flexibility, allowing interconnected machines to store multiple molds and product configurations, allowing manufacturers to switch between production runs with minimal setup time. This reduces downtime and ensures that operations remain agile and responsive to customer needs.
Enhanced collaboration and transparency in manufacturing processes
The equipment connectivity of horizontal injection molding machines promotes collaboration and transparency at all levels of the manufacturing process. Providing a centralized operational view enables teams to work more effectively and make informed decisions. Engineers and operators can access real-time production data from anywhere to ensure everyone can achieve production goals. The connectivity of horizontal injection molding machines enables departments like design and production to communicate effectively and seamlessly, implementing new product designs or modifications. Transparency is further enhanced through digital dashboards and reporting tools. Stakeholders can track KPIs such as production output, horizontal injection molding machine utilization, and defect rates.
More flexible and scalable injection molding solutions
The equipment connectivity of horizontal injection molding machines pays more attention to customers’ production and operation results, providing a holistic injection molding solution rather than just a single device. This solution can meet customers’ comprehensive production efficiency and management needs.
TRENDING POSTS
- What factors can cause delays in the injection molding process of plastic molding machine? 2024/11/22
- Exhibition Review| Topstar participates in InterPlas Thailand 2024 2024/11/22
- Star Case | Topstar helps Santong upgrade its intelligent plant 2024/11/22
- Topstar Special | National Science and Technology Workers Day 2024/11/22
HOT TOPIC
- 3 in 1 Compact Dehumidifying Dryer
- 5-axis CNC machine
- accuracy
- Air Chillers
- all electric injection molding machine
- all electric injection molding machines
- All-electric injection molding machines
- and overall production quality. Therefore
- AP-RubberPlas
- automated injection molding machine
- Automation changed engineering
- automation of injection molding robots
- auxiliary machine
- Bench Injection Molding Machine
- Cabinet dryer manufacturers
- Cabinet dryers
- chiller
- CNC Drilling Machine
- CNC Drilling Machines
- cnc engraving machine manufacturer
- cnc laser cutting machine manufacturer
- CNC machine
- CNC Machine Center
- CNC Machine for Sale
- CNC Machine Manufacturing
- CNC Machine Tool
- CNC machine tool product
- CNC Machining Center
- CNC wood carving machine
- Cooling system
- Cross-Walking Single Axis Servo Cylinder Robot
- Cross-Walking Single-Axis Servo Cylinder Robot
- Cross-Walking Three-Axis/Five-Axis Servo Driven Robot
- cross-walking three-axis/five-axis servo-driven robot
- Dehumidifier Dryer
- Dehumidifying Dryer
- delta parallel robot
- Desktop Injection Molding Machine
- Desktop injection molding machines
- Desktop Molding Machine
- desktop plastic injection machine
- Desktop Plastic Injection Molding Machine
- direct clamp injection molding machine
- Direct clamp injection molding machines
- Dosing & mixing system
- Drilling Centers
- Drying and dehumidification system
- drying and dehumidifying equipment
- Drying and Dehumidifying System
- drying system
- effective and efficient. Cabinet dryers are also used in other industries where large quantities of material need to be dried
- efficient injection molding machine
- elbow hydraulic injection molding machines
- electric injection molding machine
- electric injection molding machines
- energy-saving injection molding machine
- etc. Among injection molding robots
- exhibition
- features of CNC machine
- Feeding And Conveying System
- Five Axis Machine Center
- Fully automatic injection molding machine
- Gathering Topstar
- giant injection molding machine
- GMU-600 5-Axis Machining Center
- Granulating & Recycling System
- Heavy duty injection molding machine
- Honeycomb rotor dehumidifier
- horizontal injection molding machine
- Horizontal Injection Molding Machines
- Horizontal Injection Moulding Machine
- Horizontal Mixer manufacturer
- How The CNC Machine Works
- hybrid injection molding machine
- hydraulic injection molding machine
- Hydraulic Injection Molding Machines
- in this article
- Industrial robot
- Industrial Robot Chinese brand
- industrial robot parts
- industrial robot supplier
- Industrial robots
- Industry Chain
- Injection Manipulator
- injection mold machines
- Injection molding
- Injection molding automation
- Injection Molding Automation Solution
- injection molding dryer
- Injection molding equipment
- injection molding hopper dryer
- Injection molding machine
- injection molding machine brand
- Injection Molding Machine Factory
- Injection Molding Machine Manufacture
- Injection molding machine manufacturer
- injection molding machine manufacturers
- Injection molding machine procurement
- injection molding machine robotic arm
- injection molding machine with a robot
- Injection molding machines
- injection molding material dehumidifying
- injection molding plant
- Injection Molding Robot
- injection molding robot arm
- Injection molding robot automation
- Injection molding robotic arm
- injection molding robots
- Injection Moulding Robots
- Injection Robot
- Injection robot arm
- Injection robot manufacturer
- Injection robot wholesale
- injection robots
- intelligent injection molding machines
- Introducing Injection Robot
- It is the best choice for drying large quantities of material at once. Cabinetmakers use these machines because they are fast
- large injection molding machine
- Learn what industrial automation and robotics is
- low speed sound-proof granulator
- machine plastic molding
- make sure to add some! Improvements (2) Keyphrase in introduction: Your keyphrase or its synonyms appear in the first paragraph of the copy
- manipulator machine
- manufacturing
- micro injection molding machine
- middle speed granulator
- Mini CNC machine manufacturers.
- Mold Temperature Control System
- mold temperature controller
- molding material Dehumidifying System
- mould temperature controller
- mould temperature controllers
- New electric injection molding machine
- nitrogen dryer manufacturer
- nitrogen dryer system manufacturer
- Oil type mold temperature controller
- open day
- Outbound links: No outbound links appear in this page. Add some! Images: No images appear on this page. Add some! Internal links: No internal links appear in this page
- PET Preform injection molding
- phone case maker machine
- phone case making machine
- plastic bottle making machine
- plastic bottle manufacturing
- plastic bucket making machine
- plastic bucket manufacturing
- Plastic chair making machine
- plastic forming equipment
- plastic hopper dryer
- plastic injection machine
- plastic injection machines
- plastic injection molding
- Plastic injection molding equipment
- Plastic injection molding machine
- Plastic Injection Molding Machines
- plastic injection robot
- Plastic Molding machine
- Plastic Molding Machines
- plastic molding press
- plastic phone case making machine
- plastic-molding machine
- powerful granulator
- Powerful Type Sound-Proof Granulator
- production of plastic seats
- Robot injection molding
- robot injection molding machine
- robot manufacturing companies
- Robotic arm for injection molding machine
- robotic injection molding machines
- robotics in injection molding
- SCARA robot
- SCARA robots
- Service-oriented manufacturing
- Servo Cylinder Robot
- servo driven robot
- Servo Driven Robots
- servo injection robots
- Servo-Driven Robot
- Setup of injection machine
- Silicone Injection Molding Machine
- six-axis industrial robot
- Stainless Hopper Dryer
- Stainless Hopper Dryers
- star club
- swing arm robot
- the choice between servo-driven robots and hydraulic robots will have a certain impact on efficiency
- the most popular injection molding machine
- the type of injection molding robot
- toggle clamp injection molding machine
- Toggle Hydraulic Injection Molding Machines
- toggle injection molding machine
- Top 10 brands of injection robots
- Topstar
- Topstar Engineering
- Topstar Industrial Robots
- Topstar injection molding intelligent
- Topstar Scara Robots
- Useful Injection molding machine
- Vertical machining centers
- volumetric type blender
- water chiller
- water chillers
- water distributor
- Water Type MoldTemperature Controller
- We often face choices when performing injection molding. We will choose the type of injection molding machine
- wholesale of injection molding machines
- x carve CNC