Innovative technologies and concepts provided by leading injection molding machine manufacturer
2024/10/28 By Topstar
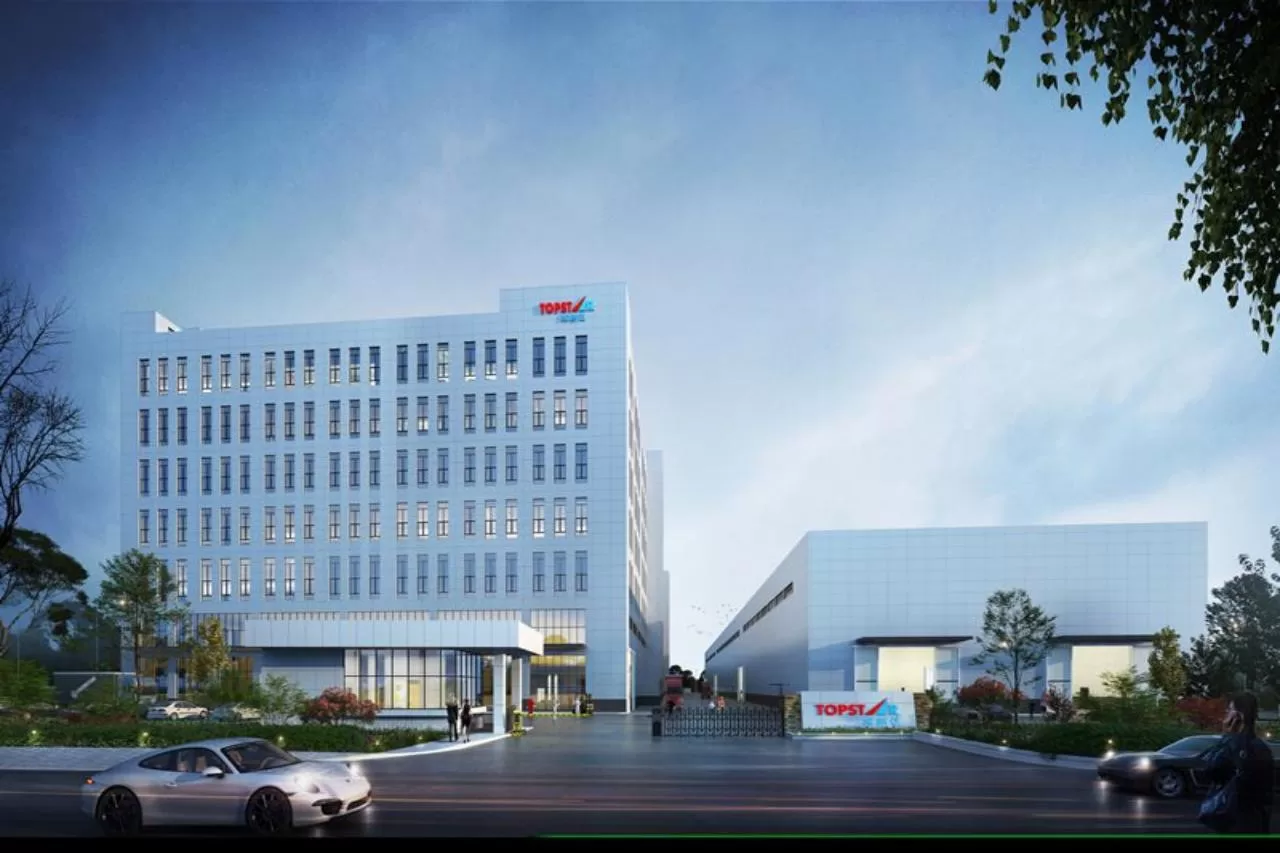
Topstar is an injection molding machine manufacturer with industrial robots, injection molding machines, CNC, and auxiliary equipment as its core. We have three core technologies, control, servo, and vision, to create an intelligent hardware platform driven by core technologies, providing smart factory overall solutions for different manufacturing companies. On this basis, to make injection molding simpler, we proposed the concept of an “integrated process machine.” We adopted it on injection molding machines like the TM and TE ll series. The machine has the characteristics of openness, compatibility, continuous upgrading, and hardware iteration.
Injection molding machine manufacturer is adopting the concept of a “process all-in-one machine.”
In traditional injection molding, injection molding equipment cannot achieve communication integration, which is inconvenient for production management, and cannot achieve compatibility between equipment. The concept of “process all-in-one machine” is to achieve the integration of the main machine, auxiliary machine, and automatic control through an integrated open system, thereby significantly improving the efficiency of the production cycle. We incorporate various links into one system to achieve technical coordination between injection molding machines and peripheral auxiliary equipment, reduce the number of times operators debug the equipment, and make the effect more apparent, especially for those industries with clean production requirements. In this way, the “integrated process machine” of each injection molding unit is an injection molding automation workstation, and the automation level of the production line will be significantly improved.
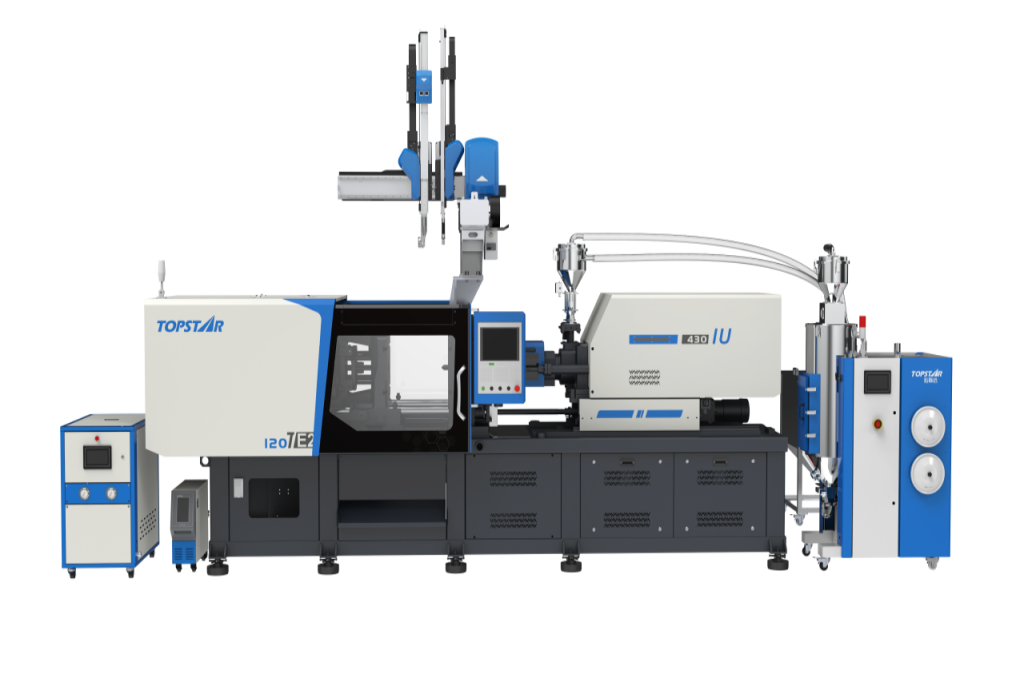
Process-integrated injection molding equipment can facilitate the intercommunication and sharing of production data and better help traditional manufacturing factories implement digital transformation.
With a more intelligent control system
Topstar’s second-generation electric injection molding machine uses a new control method to solve the product stability problem caused by delays in communication with the control system. One of the core principles is to send the injection molding process data to the servo drive through the central controller of the upper controller, and the servo drive generates the operation curve by itself. This intelligent drive control mode reduces the impact of communication delay on the high-speed operation of the servo motor, realizes real-time control of the servo motor, improves the accuracy of position, speed, and pressure control, and increases the response speed by 8-16 times. When the servo drive receives the setting parameters of the HMI, it saves these parameters in the internal latch to directly produce the motor speed curve to execute the corresponding process during each cycle reciprocating operation, making the execution process more efficient.
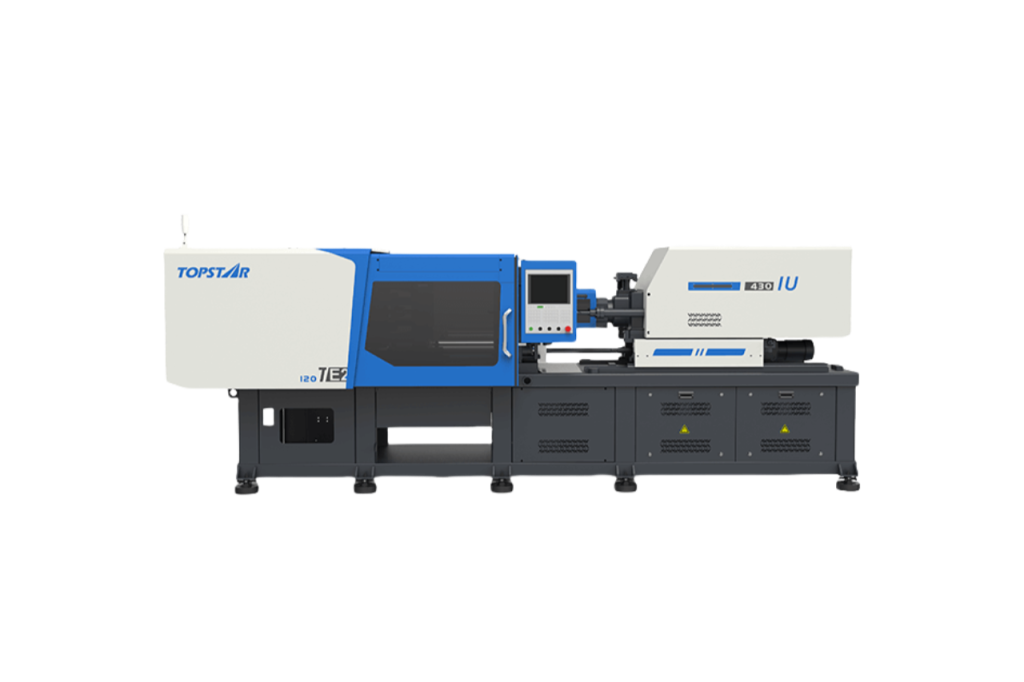
Make temperature control more accurate—mold temperature controller.
The significant temperature fluctuation of the mold temperature controller in injection molding is because the temperature control accuracy cannot meet the actual production requirements. Topstar’s fourth-generation mold temperature controller can improve the temperature control efficiency by 10% and ensure temperature uniformity through the latest PID temperature control algorithm. In addition, solid-state relays are used for temperature control in the hardware part, and the response time can reach 0.1s. We ensure that the temperature fluctuates within ±0.1℃ through the dual guarantee of software and hardware to ensure the product yield. At the same time, 1MHz ultrasonic flow monitoring is also used to monitor the media flow at all times, which can detect bubbles that are larger than 2mm, ensure that the water flow is liquid, and ensure stable and accurate temperature control.
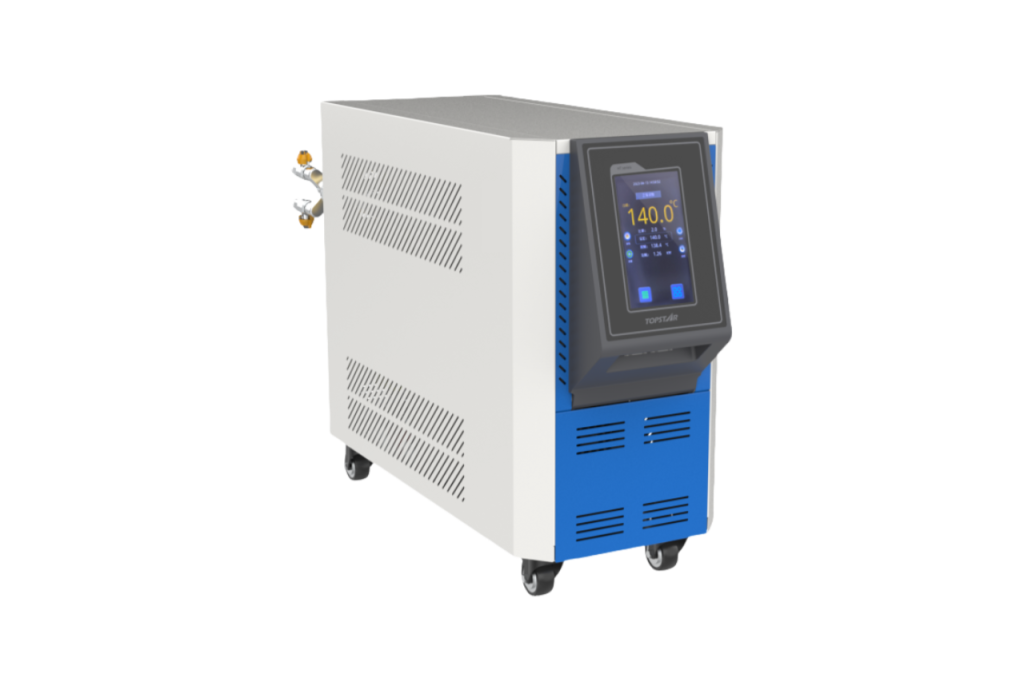
More intelligent injection molding robot
We upgraded and updated the software under Topstar’s self-developed control system. It can support the injection molding machine in calling the robot’s signal, realizing integrated linkage, and controlling more accurately. It also has a built-in dual system so customers can choose freely and program actions for special requirements. Under the fully self-developed five-in-one servo drive system, the injection molding robot has powerful algorithm capabilities, making it more precise, energy-efficient, intelligent, and functional with solid scalability. It can add back-end automation processes according to customer needs. At the same time, advanced manipulator motion control technology is also used to ensure smooth and precise movement according to the predetermined contour when executing complex trajectories or paths, improving the workshop’s production quality and production efficiency.
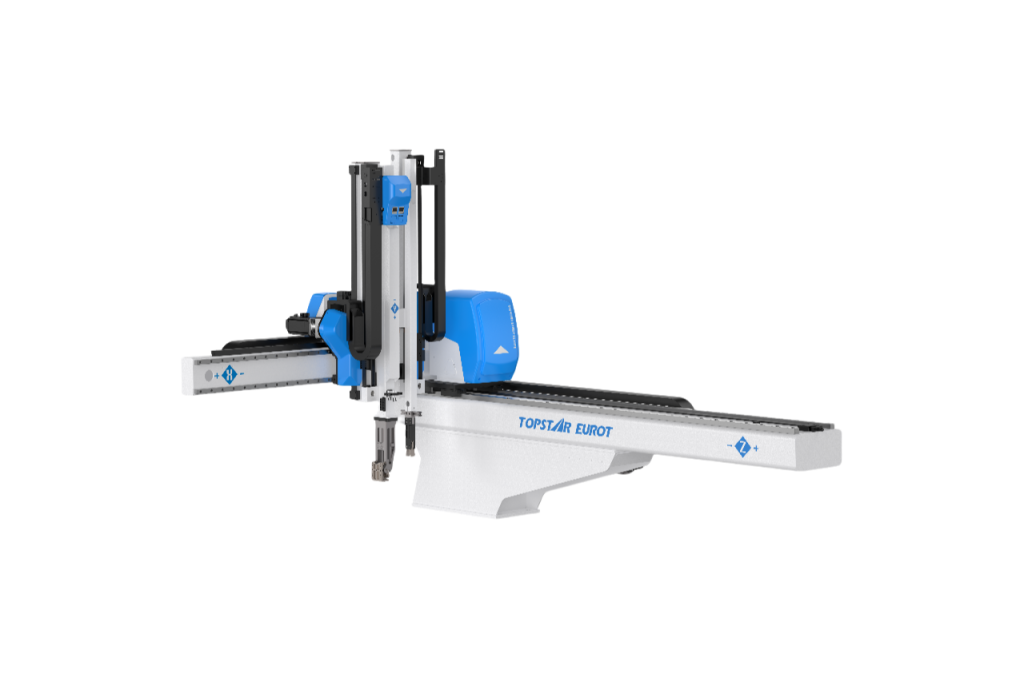
Injection molding machine manufacturer with MES module capabilities for data management
As an injection molding machine manufacturer with global capabilities, I provide more than just a single injection molding equipment. I position myself not as an equipment manufacturer but as one that offers a complete solution for intelligent injection molding. The innovative manufacturing technology used facilitates seamless communication between machines and MES. This integration simplifies workflows, automates repetitive processes, and promotes team collaboration. For example, MES can provide real-time visibility into production indicators, enabling managers to make informed decisions about resource allocation and production scheduling. As a result, manufacturers can respond quickly to changing market demands and optimize their operations for maximum efficiency. By adopting the concept of intelligent whole-field manufacturing and leveraging MES functions as an injection molding machine manufacturer, we can help customers improve productivity, reduce operating costs, and maintain a competitive advantage in a rapidly evolving industry.
More possibilities through technological innovation
Through innovative concepts such as control systems, drive systems, and “integrated process machines,” manufacturers can improve operational efficiency, improve product quality, and achieve the goal of digital development. Leveraging cutting-edge technology’s capabilities is crucial for maintaining competitiveness in the evolving industry and adapting to ever-changing market needs.
TRENDING POSTS
- What factors can cause delays in the injection molding process of plastic molding machine? 2024/10/28
- Exhibition Review| Topstar participates in InterPlas Thailand 2024 2024/10/28
- Star Case | Topstar helps Santong upgrade its intelligent plant 2024/10/28
- Topstar Special | National Science and Technology Workers Day 2024/10/28
HOT TOPIC
- 3 in 1 Compact Dehumidifying Dryer
- 5-axis CNC machine
- accuracy
- Air Chillers
- all electric injection molding machine
- All-electric injection molding machines
- and overall production quality. Therefore
- AP-RubberPlas
- automated injection molding machine
- Automation changed engineering
- automation of injection molding robots
- auxiliary machine
- Bench Injection Molding Machine
- Cabinet dryer manufacturers
- Cabinet dryers
- chiller
- CNC Drilling Machine
- CNC Drilling Machines
- cnc engraving machine manufacturer
- cnc laser cutting machine manufacturer
- CNC machine
- CNC Machine Center
- CNC Machine for Sale
- CNC Machine Manufacturing
- CNC Machine Tool
- CNC machine tool product
- CNC Machining Center
- CNC wood carving machine
- Cooling system
- Cross-Walking Single Axis Servo Cylinder Robot
- Cross-Walking Single-Axis Servo Cylinder Robot
- Cross-Walking Three-Axis/Five-Axis Servo Driven Robot
- cross-walking three-axis/five-axis servo-driven robot
- Dehumidifier Dryer
- Dehumidifying Dryer
- delta parallel robot
- Desktop Injection Molding Machine
- Desktop injection molding machines
- Desktop Molding Machine
- desktop plastic injection machine
- Desktop Plastic Injection Molding Machine
- direct clamp injection molding machine
- Direct clamp injection molding machines
- Dosing & mixing system
- Drilling Centers
- Drying and dehumidification system
- drying and dehumidifying equipment
- Drying and Dehumidifying System
- drying system
- effective and efficient. Cabinet dryers are also used in other industries where large quantities of material need to be dried
- efficient injection molding machine
- elbow hydraulic injection molding machines
- electric injection molding machine
- electric injection molding machines
- etc. Among injection molding robots
- exhibition
- features of CNC machine
- Feeding And Conveying System
- Five Axis Machine Center
- Fully automatic injection molding machine
- Gathering Topstar
- giant injection molding machine
- GMU-600 5-Axis Machining Center
- Granulating & Recycling System
- Heavy duty injection molding machine
- Honeycomb rotor dehumidifier
- horizontal injection molding machine
- Horizontal Injection Molding Machines
- Horizontal Injection Moulding Machine
- Horizontal Mixer manufacturer
- How The CNC Machine Works
- hybrid injection molding machine
- hydraulic injection molding machine
- Hydraulic Injection Molding Machines
- in this article
- Industrial robot
- Industrial Robot Chinese brand
- industrial robot parts
- industrial robot supplier
- Industrial robots
- Industry Chain
- Injection Manipulator
- injection mold machines
- Injection molding
- Injection molding automation
- Injection Molding Automation Solution
- injection molding dryer
- Injection molding equipment
- injection molding hopper dryer
- Injection molding machine
- injection molding machine brand
- Injection Molding Machine Factory
- Injection Molding Machine Manufacture
- Injection molding machine manufacturer
- injection molding machine manufacturers
- Injection molding machine procurement
- injection molding machine robotic arm
- injection molding machine with a robot
- Injection molding machines
- injection molding material dehumidifying
- injection molding plant
- Injection Molding Robot
- injection molding robot arm
- Injection molding robot automation
- Injection molding robotic arm
- injection molding robots
- Injection Moulding Robots
- Injection Robot
- Injection robot arm
- Injection robot manufacturer
- Injection robot wholesale
- injection robots
- intelligent injection molding machines
- Introducing Injection Robot
- It is the best choice for drying large quantities of material at once. Cabinetmakers use these machines because they are fast
- large injection molding machine
- Learn what industrial automation and robotics is
- low speed sound-proof granulator
- machine plastic molding
- make sure to add some! Improvements (2) Keyphrase in introduction: Your keyphrase or its synonyms appear in the first paragraph of the copy
- manipulator machine
- manufacturing
- micro injection molding machine
- middle speed granulator
- Mini CNC machine manufacturers.
- Mold Temperature Control System
- mold temperature controller
- molding material Dehumidifying System
- mould temperature controller
- mould temperature controllers
- New electric injection molding machine
- nitrogen dryer manufacturer
- nitrogen dryer system manufacturer
- Oil type mold temperature controller
- open day
- Outbound links: No outbound links appear in this page. Add some! Images: No images appear on this page. Add some! Internal links: No internal links appear in this page
- PET Preform injection molding
- phone case maker machine
- phone case making machine
- plastic bottle making machine
- plastic bottle manufacturing
- plastic bucket making machine
- plastic bucket manufacturing
- Plastic chair making machine
- plastic forming equipment
- plastic hopper dryer
- plastic injection machine
- plastic injection machines
- plastic injection molding
- Plastic injection molding equipment
- Plastic injection molding machine
- Plastic Injection Molding Machines
- plastic injection robot
- Plastic Molding machine
- Plastic Molding Machines
- plastic molding press
- plastic phone case making machine
- plastic-molding machine
- powerful granulator
- Powerful Type Sound-Proof Granulator
- production of plastic seats
- Robot injection molding
- robot injection molding machine
- robot manufacturing companies
- Robotic arm for injection molding machine
- robotic injection molding machines
- robotics in injection molding
- SCARA robot
- SCARA robots
- Service-oriented manufacturing
- Servo Cylinder Robot
- servo driven robot
- Servo Driven Robots
- servo injection robots
- Servo-Driven Robot
- Setup of injection machine
- Silicone Injection Molding Machine
- six-axis industrial robot
- Stainless Hopper Dryer
- Stainless Hopper Dryers
- star club
- swing arm robot
- the choice between servo-driven robots and hydraulic robots will have a certain impact on efficiency
- the most popular injection molding machine
- the type of injection molding robot
- toggle clamp injection molding machine
- Toggle Hydraulic Injection Molding Machines
- toggle injection molding machine
- Top 10 brands of injection robots
- Topstar
- Topstar Engineering
- Topstar Industrial Robots
- Topstar injection molding intelligent
- Topstar Scara Robots
- Useful Injection molding machine
- Vertical machining centers
- volumetric type blender
- water chiller
- water chillers
- water distributor
- Water Type MoldTemperature Controller
- We often face choices when performing injection molding. We will choose the type of injection molding machine
- wholesale of injection molding machines
- x carve CNC