What options are available for enhancing the flexibility of all electric injection molding machine?
2024/10/16 By Topstar
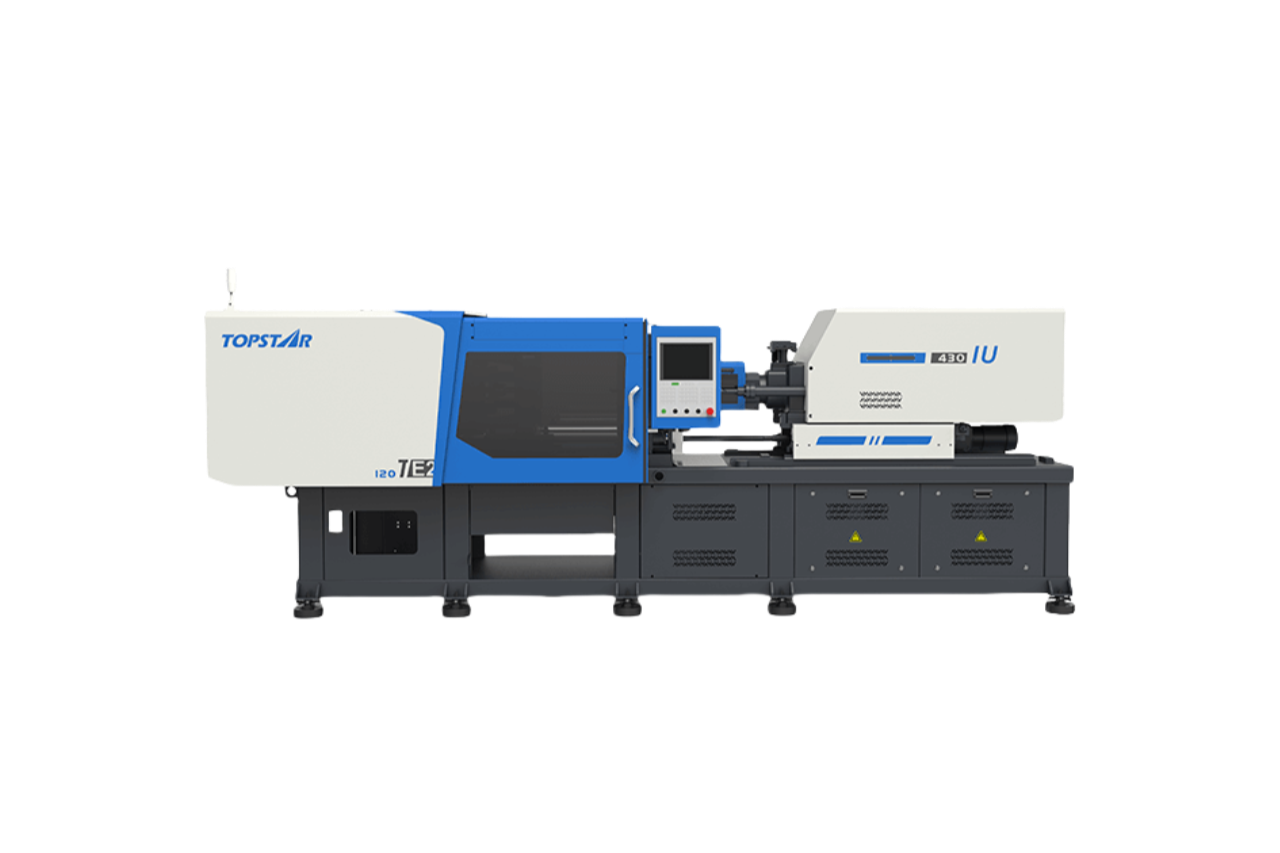
An all electric injection molding machine has become the best choice for the current manufacturing industry’s pursuit of efficiency, precision, and sustainability. These machines can produce high-quality parts while minimizing energy consumption and reducing environmental pollution. However, to fully utilize the advantages of all-electric systems in injection molding, it is necessary to increase their flexibility to adapt to various production needs. Therefore, in this guide, we will share the multiple options available to increase the flexibility of all electric injection molding machines.
Interchangeable molds for all electric injection molding machine
One of the ways to increase the flexibility of all electric injection molding machines is to use interchangeable molds. Topstar’s modular mold systems allow manufacturers to switch between different molds quickly based on production needs. Interchangeable molds reduce downtime and enable manufacturers to diversify their products without investing heavily in new equipment. For example, a company that produces plastic parts for consumer electronics and automotive applications can easily adjust its all electric injection molding machine to adapt to different molds for each industry. In addition, this modern mold design technology enables the creation of lightweight, compact, easy-to-handle and transport molds, further enhancing the flexibility of all electric injection molding machine.
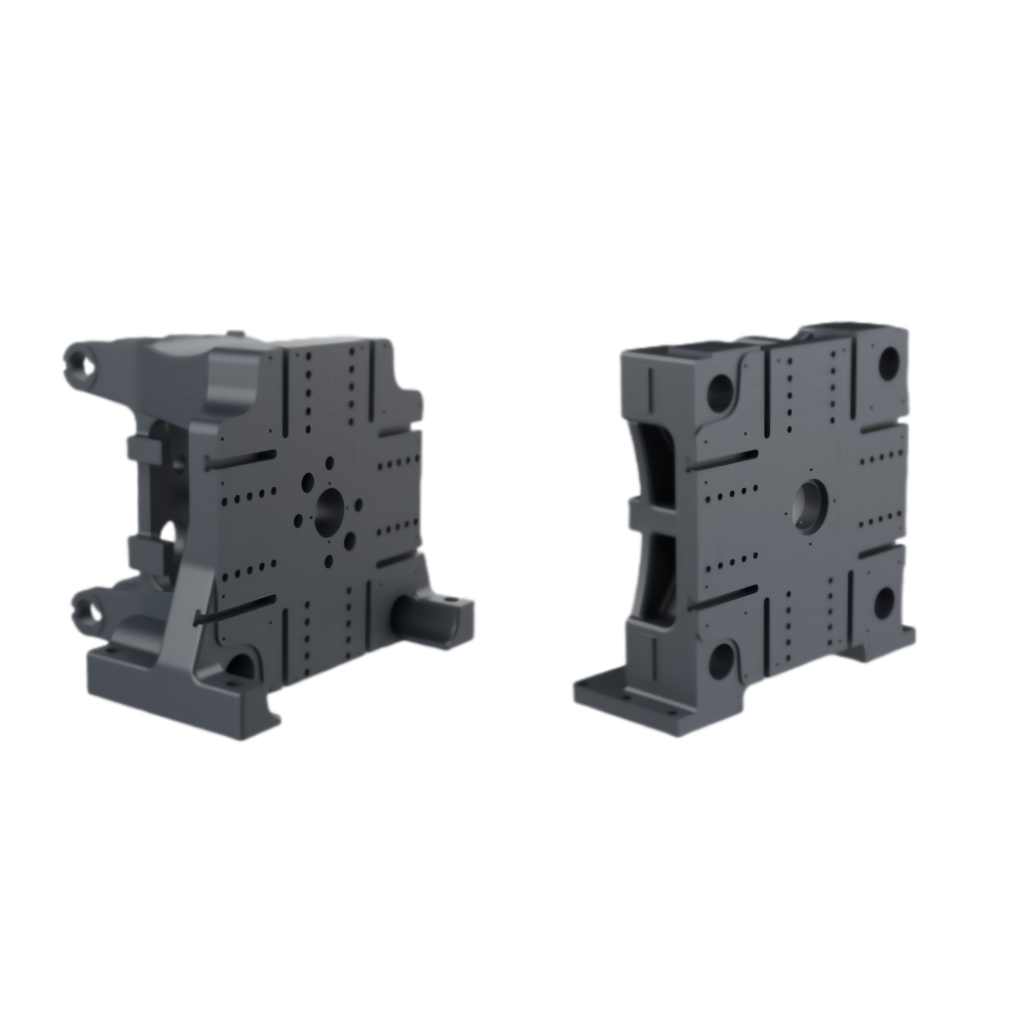
Self-developed control system for all electric injection molding machine
Topstar’s self-developed control system can accurately monitor and adjust parameters, including temperature, pressure, and injection speed. This level of control is crucial to optimize the molding process and ensure consistent product quality. With advanced software solutions, operators can easily program and switch between different production settings to accommodate a variety of materials and part designs. In addition, all electric injection molding machines are now equipped with a user-friendly interface, allowing operators to access real-time data and analysis easily. This information can make process adjustments and identify areas for improvement. By utilizing advanced control systems, manufacturers of all types can significantly improve the flexibility and efficiency of all-electric injection molding operations.
Customizable modular injection units
Customizable injection units are another option to increase the flexibility of all electric injection molding machines. Their modular design can be customized to suit specific production requirements and adapt to various working conditions, allowing manufacturers to optimize their processes based on the type of material used, part geometry, and production volume.
For example, some manufacturers may require higher injection speeds for specific applications, while others may consider increased precision for complex designs. Customizable modular injection units further enhance the machine’s versatility, allowing it to meet various production needs without compromising performance. This flexibility enables manufacturers to handle different product lines efficiently.
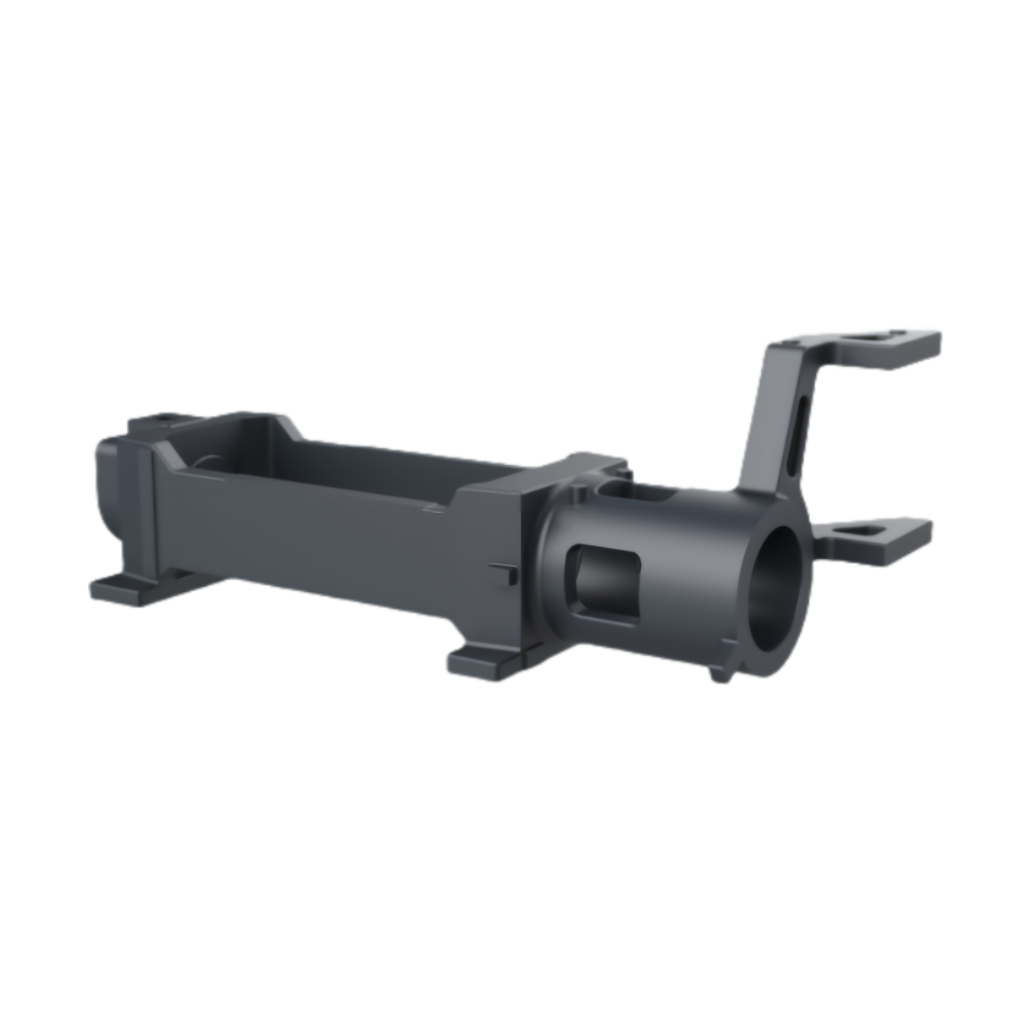
Integration with injection molding robots
Integrating injection molding robot systems with all-electric injection molding machines significantly improves their flexibility. Injection molding robots can be used for various tasks, including parts disassembly, assembly, and packaging, enabling manufacturers to automate processes that originally required manual labor. In addition, we continue to use the concept of “integration of injection molding processes” to make the machine open, compatible, continuously upgraded, and hardware iterative. In contrast, hardware equipment with core technology can provide perception capabilities in real-time communication, compatibility, and data collection.
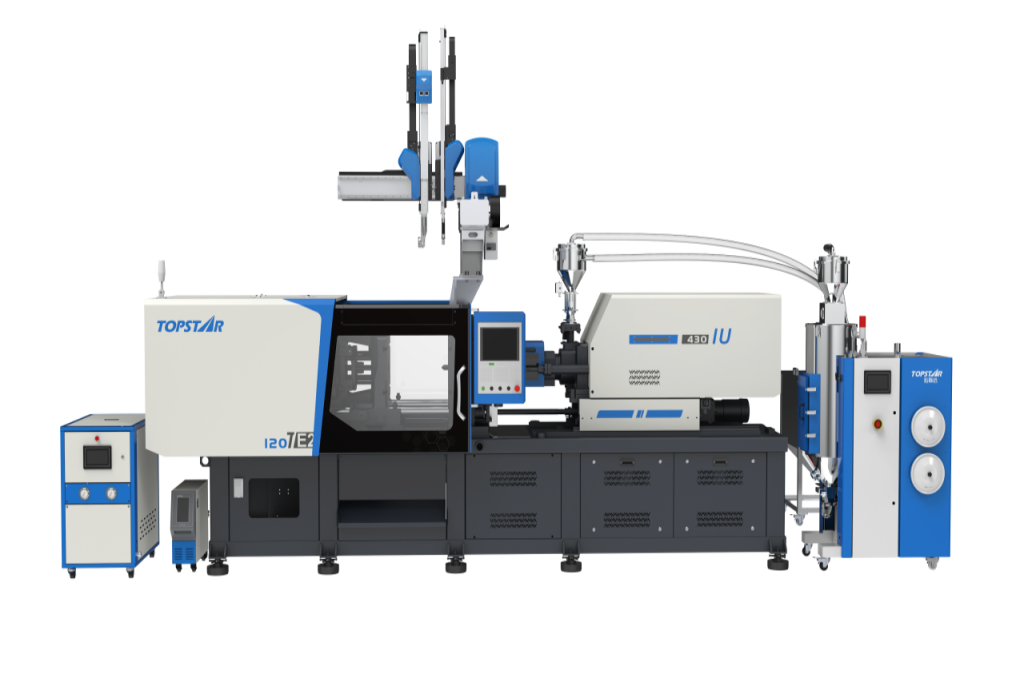
An integrated and open system combines the main machine, auxiliary machine, injection molding machine robot, and automated control, greatly improving the efficiency and flexibility of the production cycle. The process-integrated injection molding machine can also realize the intercommunication and sharing of production data, laying the foundation for the enterprise’s digital transformation.
Maximize flexibility and efficiency
Increasing the flexibility of all electric injection molding machines is essential for manufacturers who want to stay competitive in today’s environment. Options such as interchangeable molds, self-developed control systems, customizable modular injection molding units, and injection molding robot integration can maximize flexibility and efficiency.
TRENDING POSTS
- What factors can cause delays in the injection molding process of plastic molding machine? 2024/10/16
- Exhibition Review| Topstar participates in InterPlas Thailand 2024 2024/10/16
- Star Case | Topstar helps Santong upgrade its intelligent plant 2024/10/16
- Topstar Special | National Science and Technology Workers Day 2024/10/16
HOT TOPIC
- .ervo motor-driven linear robots
- 3 axis robot
- 3 axis robots
- 3 in 1 Compact Dehumidifying Dryer
- 3-axis robot
- 3-axis robots
- 5-axis CNC machine
- accuracy
- Air Chillers
- all electric injection molding machine
- all electric injection molding machines
- All-electric injection molding machines
- and overall production quality. Therefore
- AP-RubberPlas
- automated injection molding machine
- Automation changed engineering
- automation of injection molding robots
- auxiliary machine
- Bench Injection Molding Machine
- Cabinet dryer manufacturers
- Cabinet dryers
- chiller
- CNC Drilling Machine
- CNC Drilling Machines
- cnc engraving machine manufacturer
- cnc laser cutting machine manufacturer
- CNC machine
- CNC Machine Center
- CNC Machine for Sale
- CNC Machine Manufacturing
- CNC Machine Tool
- CNC machine tool product
- CNC Machining Center
- CNC wood carving machine
- Cooling system
- Cross-Walking Single Axis Servo Cylinder Robot
- Cross-Walking Single-Axis Servo Cylinder Robot
- Cross-Walking Three-Axis/Five-Axis Servo Driven Robot
- cross-walking three-axis/five-axis servo-driven robot
- Dehumidifier Dryer
- Dehumidifying Dryer
- delta parallel robot
- Desktop Injection Molding Machine
- Desktop injection molding machines
- Desktop Molding Machine
- desktop plastic injection machine
- Desktop Plastic Injection Molding Machine
- direct clamp injection molding machine
- Direct clamp injection molding machines
- Dosing & mixing system
- Drilling Centers
- Drying and dehumidification system
- drying and dehumidifying equipment
- Drying and Dehumidifying System
- drying system
- effective and efficient. Cabinet dryers are also used in other industries where large quantities of material need to be dried
- efficient injection molding machine
- elbow hydraulic injection molding machines
- electric injection molding machine
- electric injection molding machines
- energy-efficient injection molding robot
- energy-saving injection molding machine
- etc. Among injection molding robots
- exhibition
- features of CNC machine
- Feeding And Conveying System
- Five Axis Machine Center
- Fully automatic injection molding machine
- Gathering Topstar
- giant injection molding machine
- GMU-600 5-Axis Machining Center
- Granulating & Recycling System
- Heavy duty injection molding machine
- High-precision electric molding machines
- high-precision plastic molding machines
- high-speed all electric injection molding machine
- Honeycomb rotor dehumidifier
- horizontal injection molding machine
- Horizontal Injection Molding Machines
- Horizontal Injection Moulding Machine
- Horizontal Mixer manufacturer
- How The CNC Machine Works
- hybrid injection molding machine
- hydraulic injection molding machine
- Hydraulic Injection Molding Machines
- in this article
- Industrial robot
- Industrial Robot Chinese brand
- industrial robot parts
- industrial robot supplier
- Industrial robots
- Industry Chain
- Injection Manipulator
- injection manipulator robot
- injection mold machines
- Injection molding
- Injection molding automation
- Injection Molding Automation Solution
- injection molding dryer
- Injection molding equipment
- injection molding hopper dryer
- Injection molding machine
- injection molding machine brand
- Injection Molding Machine Factory
- Injection Molding Machine Manufacture
- Injection molding machine manufacturer
- injection molding machine manufacturers
- Injection molding machine procurement
- injection molding machine robotic arm
- injection molding machine with a robot
- Injection molding machines
- injection molding material dehumidifying
- injection molding plant
- Injection Molding Robot
- injection molding robot arm
- Injection molding robot automation
- Injection molding robotic arm
- injection molding robots
- Injection moulding machine
- Injection Moulding Robots
- Injection Robot
- Injection robot arm
- Injection robot manufacturer
- Injection robot wholesale
- injection robots
- intelligent injection molding machines
- Introducing Injection Robot
- It is the best choice for drying large quantities of material at once. Cabinetmakers use these machines because they are fast
- large injection molding machine
- Learn what industrial automation and robotics is
- linear robot
- linear robots
- low speed sound-proof granulator
- machine plastic molding
- make sure to add some! Improvements (2) Keyphrase in introduction: Your keyphrase or its synonyms appear in the first paragraph of the copy
- manipulator machine
- manufacturing
- medical grade injection molding machines
- medical injection molding machine
- medical injection molding machines
- micro injection molding machine
- middle speed granulator
- Mini CNC machine manufacturers.
- Mold Temperature Control System
- mold temperature controller
- mold temperature controllers
- molding material Dehumidifying System
- mould temperature control system
- mould temperature controller
- mould temperature controllers
- New electric injection molding machine
- nitrogen dryer manufacturer
- nitrogen dryer system manufacturer
- Oil type mold temperature controller
- Oil type mold temperature controllers
- open day
- Outbound links: No outbound links appear in this page. Add some! Images: No images appear on this page. Add some! Internal links: No internal links appear in this page
- PET Preform injection molding
- phone case maker machine
- phone case making machine
- plastic bottle making machine
- plastic bottle manufacturing
- plastic bucket making machine
- plastic bucket manufacturing
- Plastic chair making machine
- plastic forming equipment
- plastic hopper dryer
- plastic injection machine
- plastic injection machines
- plastic injection molding
- Plastic injection molding equipment
- Plastic injection molding machine
- Plastic Injection Molding Machines
- plastic injection moulding machine
- plastic injection robot
- Plastic Molding machine
- Plastic Molding Machines
- plastic molding press
- plastic moulding machine
- plastic phone case making machine
- plastic-molding machine
- powerful granulator
- Powerful Type Sound-Proof Granulator
- precision injection molding
- precision injection molding machines
- production of plastic seats
- pure water mould temperature controller
- Robot injection molding
- robot injection molding machine
- robot manufacturing companies
- Robotic arm for injection molding machine
- robotic injection molding machines
- robotics in injection molding
- SCARA robot
- SCARA robots
- Service-oriented manufacturing
- Servo Cylinder Robot
- servo driven robot
- Servo Driven Robots
- servo injection robots
- servo motor-driven linear robots
- servo-driven 3-axis robot
- Servo-Driven Robot
- Setup of injection machine
- Silicone Injection Molding Machine
- six-axis industrial robot
- Stainless Hopper Dryer
- Stainless Hopper Dryers
- star club
- swing arm robot
- take-out robots
- the choice between servo-driven robots and hydraulic robots will have a certain impact on efficiency
- the most popular injection molding machine
- the type of injection molding robot
- toggle clamp injection molding machine
- Toggle Hydraulic Injection Molding Machines
- toggle injection molding machine
- Top 10 brands of injection robots
- Topstar
- Topstar Engineering
- Topstar Industrial Robots
- Topstar injection molding intelligent
- Topstar Scara Robots
- Useful Injection molding machine
- Vertical machining centers
- volumetric type blender
- water chiller
- water chillers
- water distributor
- water type mold temperature controller
- Water Type MoldTemperature Controller
- Water-Type Mould Temperature Controllers
- We often face choices when performing injection molding. We will choose the type of injection molding machine
- wholesale of injection molding machines
- x carve CNC