How does a mould temperature controller contribute to reducing scrap rates?
2024/10/14 By Topstar
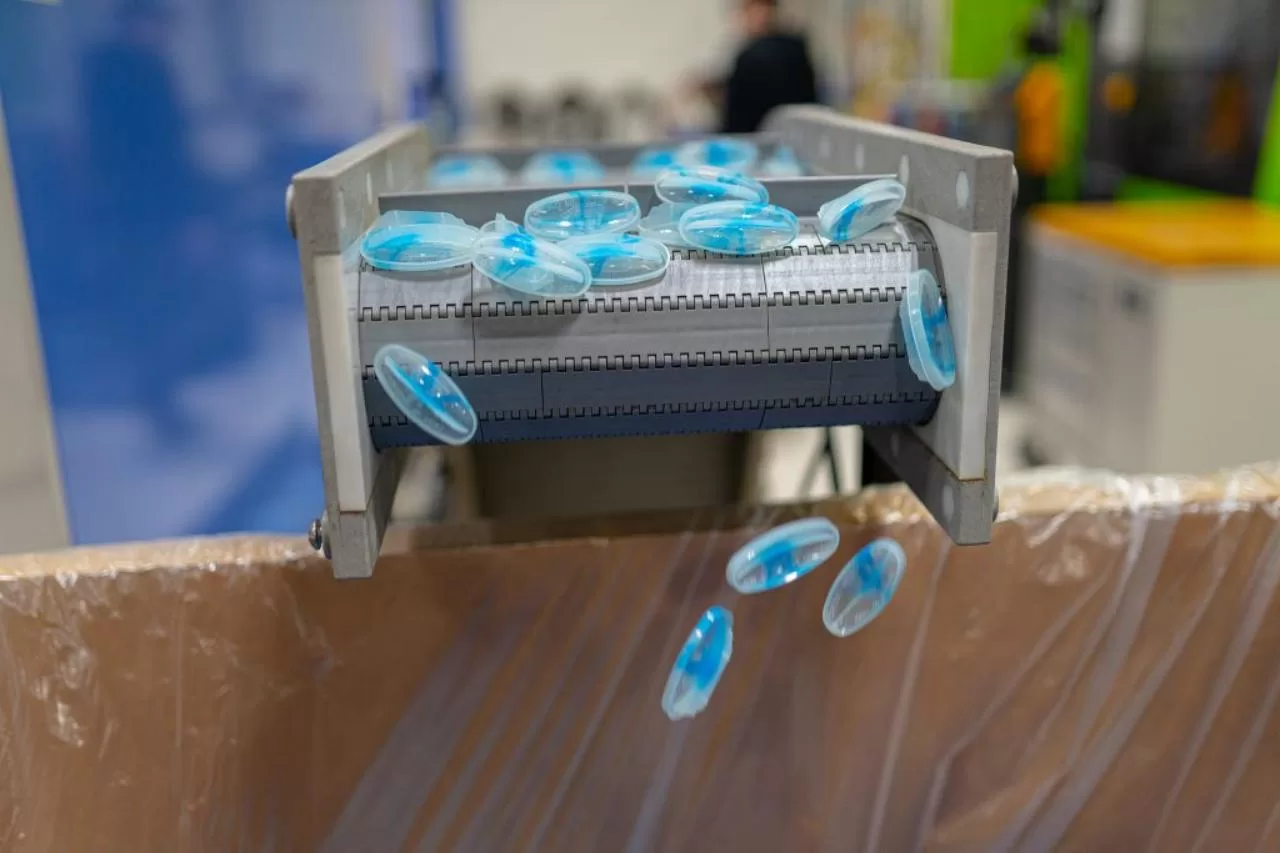
The high scrap rate in the injection moulding process and the frequent occurrence of scrap will greatly affect the production efficiency and product quality of the entire workshop. Therefore, reducing the scrap rate can maintain profitability and improve production efficiency. Many factors can affect the occurrence of scrap rate in this injection moulding process, such as poor mould design or structure, changes in material quality, and inconsistent process parameters such as temperature, pressure, filling rate, etc. One of the essential factors is to ensure that the mould temperature remains within the optimal range throughout the injection moulding process, helping manufacturers improve product quality and reduce material waste. Therefore, we introduce how the Topstar mould temperature controller plays an important role in reducing the scrap rate of plastic manufacturers.
Maintaining the optimal mould temperature to prevent defects
Using mould temperature controllers is one of the most important ways to reduce scrap rates. They are to keep the mould at the optimal temperature. During the injection molding process, the temperature of the mold directly affects the quality of the final product. By accurately controlling the mould temperature, manufacturers can ensure that the plastic flows smoothly into the mold cavity and solidifies at the correct speed. This temperature consistency prevents common defects that would otherwise lead to increased scrap rates. If the temperature of the mold is inconsistent, it will usually result in parts that do not meet the required quality standards, resulting in increased scrap rates. By using mould temperature controllers, manufacturers can avoid these costly problems.
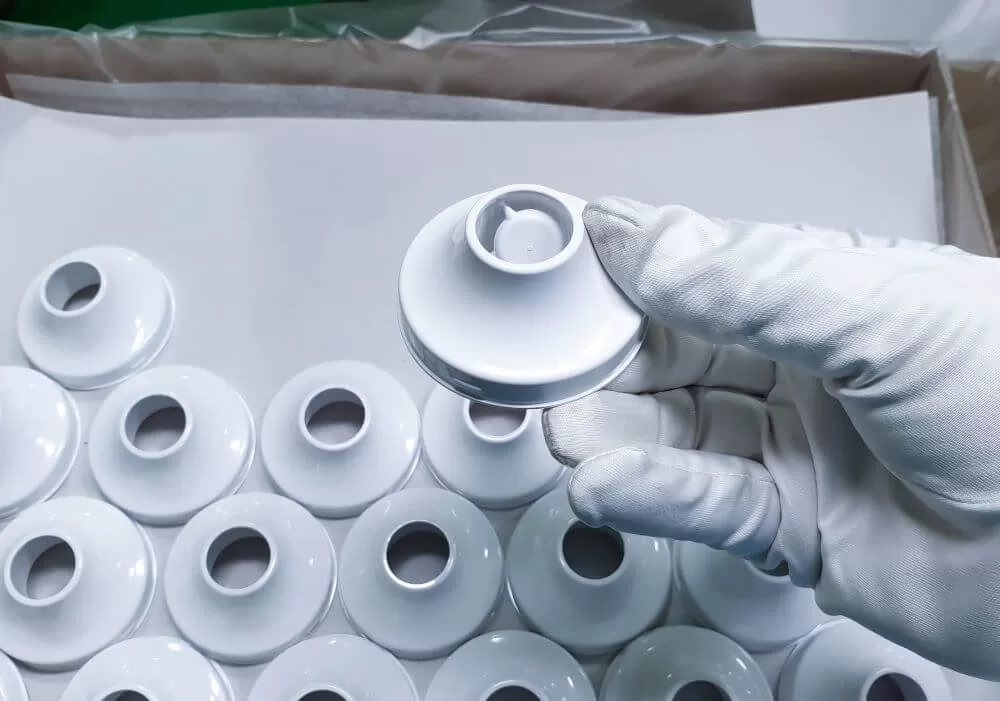
The temperature control of the mould temperature controller is not accurate
Large temperature fluctuations during the injection molding process will lead to inaccurate temperature control. This is because the mold temperature controller’s accuracy cannot meet the actual production requirements. Therefore, the Topstar mould temperature controller adopts the latest PID temperature control algorithm, which can effectively improve the temperature control efficiency by 10% and ensure the uniformity of temperature. At the same time, solid-state relays are also used for temperature control, with a response time of 0.1s.
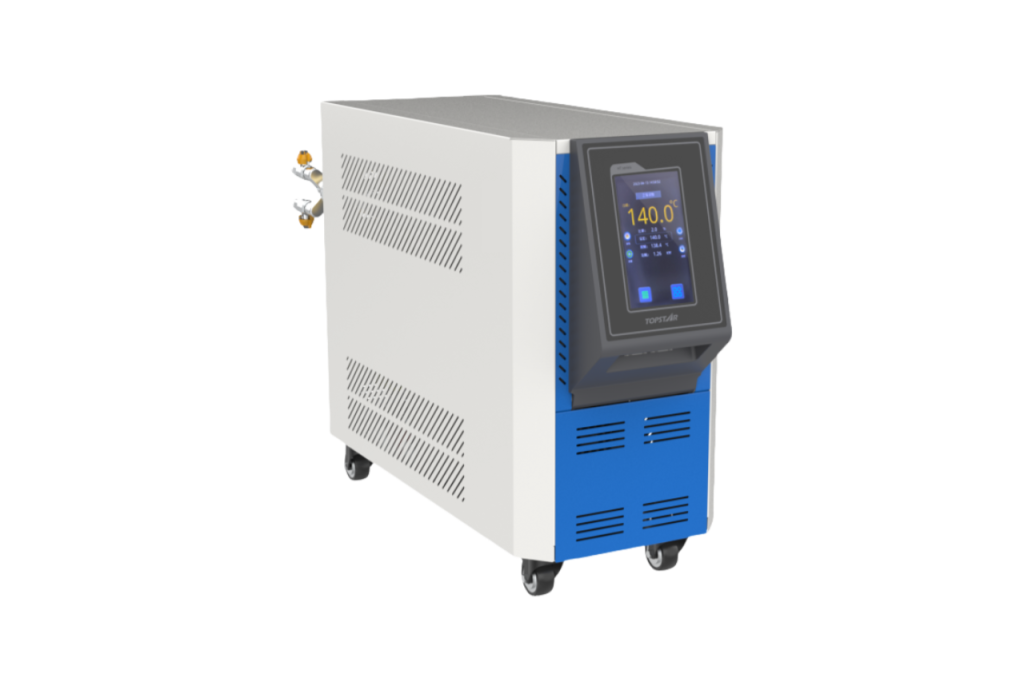
In addition, the pilot version mould temperature controller includes 1MHz ultrasonic flow monitoring as standard, which monitors the media flow in real-time and detects bubbles larger than 2mm to ensure consistent liquid flow and stable, accurate temperature control. It also features a standard gas-liquid separation device, which quickly separates gas from the medium to prevent uneven mold heating. The above functions can avoid temperature mold fluctuations and reduce the defective rate by about 3%~5%.
Unstable water pressure affects the yield rate.
The mould temperature controller is a key device for improving the yield rate, but the water pressure may be unstable, and the water inlet pressure may be low during use. When the water pressure is insufficient, it is easy to dry burn the pipeline, resulting in inaccurate temperature control, which in turn affects the yield rate. Topstar’s mould temperature controller uses water pressure adaptive temperature regulation. The standard 120℃ water-type mould temperature controller is equipped with a pressure detector with a detection accuracy of 1%. The upper limit of the use temperature can be adjusted according to different water inlet pressures to ensure the normal use of the mould temperature controller when the water inlet pressure is low. In addition, the 160℃ and 180℃ mould temperature controllers use indirect cooling sealed circulation mode and micro-boosting pump water replenishment to reduce the requirements for water inlet pressure.
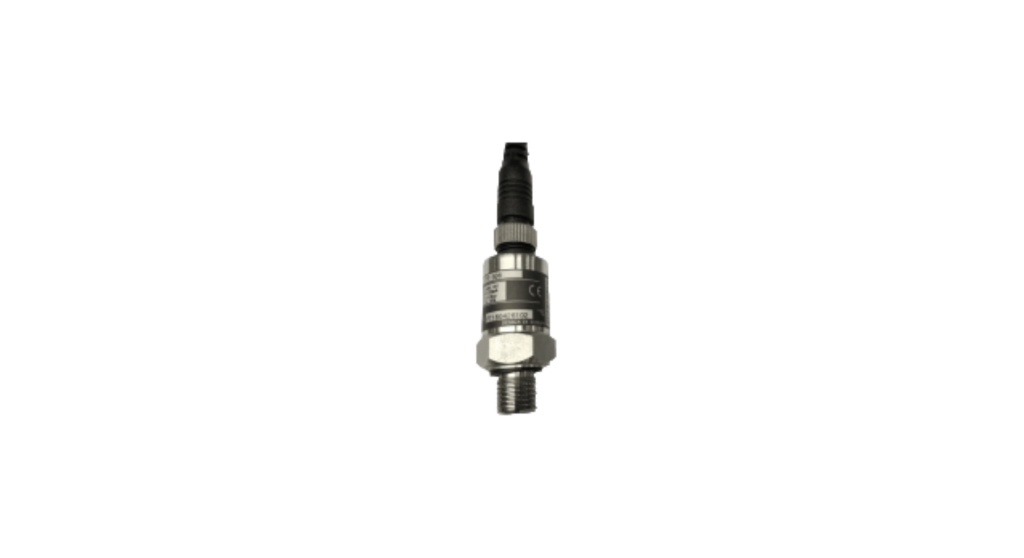
Solve the problem of mold rust
Residual medium inside the mold usually causes mold rust or pipeline blockage, reducing product yield. The mould temperature controller’s heat medium recovery technology completely replaces the residual medium in the mold with high-pressure gas, preventing mold damage and improving product yield. In addition, the water-type mould temperature controller comes with a water tank, uses pure water as the circulating medium, and a closed circulation system to prevent metal ions from corroding the mould and scale from clogging the mold. Lower the requirements for water quality and prevent the mold from rusting.
Support process control and reduce variability
Reducing variability is key to maintaining stable product quality and reducing scrap in any manufacturing process. Mould temperature controllers play a vital role in controlling one of the most critical process variables: temperature. By ensuring that mold temperature remains stable and consistent during each production process, manufacturers can reduce the variability that leads to defects and increased scrap rates.
Inconsistent mold temperature can lead to variations in part quality, such as differences in wall thickness, surface finish, or mechanical properties. These variations often result in scrapped parts because they need to meet the required specifications. Mould temperature controllers help eliminate these problems and maintain consistent temperatures throughout the injection molding process.
Solve different injection molding problems for you
Reducing scrap rates in injection molding can maintain profitability, improve efficiency, and reduce waste. Mould temperature controllers play a key role in achieving these goals, ensuring that the mold maintains an optimal temperature throughout the injection molding process. By preventing defects, improving product consistency, shortening cycle times, and reducing material waste, mould temperature controllers help manufacturers produce high-quality parts with less scrap.
TRENDING POSTS
- What factors can cause delays in the injection molding process of plastic molding machine? 2024/10/14
- Exhibition Review| Topstar participates in InterPlas Thailand 2024 2024/10/14
- Star Case | Topstar helps Santong upgrade its intelligent plant 2024/10/14
- Topstar Special | National Science and Technology Workers Day 2024/10/14
HOT TOPIC
- 3 in 1 Compact Dehumidifying Dryer
- 5-axis CNC machine
- accuracy
- Air Chillers
- all electric injection molding machine
- All-electric injection molding machines
- and overall production quality. Therefore
- AP-RubberPlas
- automated injection molding machine
- Automation changed engineering
- automation of injection molding robots
- auxiliary machine
- Bench Injection Molding Machine
- Cabinet dryer manufacturers
- Cabinet dryers
- chiller
- CNC Drilling Machine
- CNC Drilling Machines
- cnc engraving machine manufacturer
- cnc laser cutting machine manufacturer
- CNC machine
- CNC Machine Center
- CNC Machine for Sale
- CNC Machine Manufacturing
- CNC Machine Tool
- CNC machine tool product
- CNC Machining Center
- CNC wood carving machine
- Cooling system
- Cross-Walking Single Axis Servo Cylinder Robot
- Cross-Walking Single-Axis Servo Cylinder Robot
- Cross-Walking Three-Axis/Five-Axis Servo Driven Robot
- cross-walking three-axis/five-axis servo-driven robot
- Dehumidifier Dryer
- Dehumidifying Dryer
- delta parallel robot
- Desktop Injection Molding Machine
- Desktop injection molding machines
- Desktop Molding Machine
- desktop plastic injection machine
- Desktop Plastic Injection Molding Machine
- direct clamp injection molding machine
- Direct clamp injection molding machines
- Dosing & mixing system
- Drilling Centers
- Drying and dehumidification system
- drying and dehumidifying equipment
- Drying and Dehumidifying System
- drying system
- effective and efficient. Cabinet dryers are also used in other industries where large quantities of material need to be dried
- efficient injection molding machine
- elbow hydraulic injection molding machines
- electric injection molding machine
- electric injection molding machines
- etc. Among injection molding robots
- exhibition
- features of CNC machine
- Feeding And Conveying System
- Five Axis Machine Center
- Fully automatic injection molding machine
- Gathering Topstar
- giant injection molding machine
- GMU-600 5-Axis Machining Center
- Granulating & Recycling System
- Heavy duty injection molding machine
- Honeycomb rotor dehumidifier
- horizontal injection molding machine
- Horizontal Injection Molding Machines
- Horizontal Injection Moulding Machine
- Horizontal Mixer manufacturer
- How The CNC Machine Works
- hybrid injection molding machine
- hydraulic injection molding machine
- Hydraulic Injection Molding Machines
- in this article
- Industrial robot
- Industrial Robot Chinese brand
- industrial robot parts
- industrial robot supplier
- Industrial robots
- Industry Chain
- Injection Manipulator
- injection mold machines
- Injection molding
- Injection molding automation
- Injection Molding Automation Solution
- injection molding dryer
- Injection molding equipment
- injection molding hopper dryer
- Injection molding machine
- injection molding machine brand
- Injection Molding Machine Factory
- Injection Molding Machine Manufacture
- Injection molding machine manufacturer
- injection molding machine manufacturers
- Injection molding machine procurement
- injection molding machine robotic arm
- injection molding machine with a robot
- Injection molding machines
- injection molding material dehumidifying
- injection molding plant
- Injection Molding Robot
- injection molding robot arm
- Injection molding robot automation
- Injection molding robotic arm
- injection molding robots
- Injection Moulding Robots
- Injection Robot
- Injection robot arm
- Injection robot manufacturer
- Injection robot wholesale
- injection robots
- intelligent injection molding machines
- Introducing Injection Robot
- It is the best choice for drying large quantities of material at once. Cabinetmakers use these machines because they are fast
- large injection molding machine
- Learn what industrial automation and robotics is
- low speed sound-proof granulator
- machine plastic molding
- make sure to add some! Improvements (2) Keyphrase in introduction: Your keyphrase or its synonyms appear in the first paragraph of the copy
- manipulator machine
- manufacturing
- micro injection molding machine
- middle speed granulator
- Mini CNC machine manufacturers.
- Mold Temperature Control System
- mold temperature controller
- molding material Dehumidifying System
- mould temperature controller
- mould temperature controllers
- New electric injection molding machine
- nitrogen dryer manufacturer
- nitrogen dryer system manufacturer
- Oil type mold temperature controller
- open day
- Outbound links: No outbound links appear in this page. Add some! Images: No images appear on this page. Add some! Internal links: No internal links appear in this page
- PET Preform injection molding
- phone case maker machine
- phone case making machine
- plastic bottle making machine
- plastic bottle manufacturing
- plastic bucket making machine
- plastic bucket manufacturing
- Plastic chair making machine
- plastic forming equipment
- plastic hopper dryer
- plastic injection machine
- plastic injection machines
- plastic injection molding
- Plastic injection molding equipment
- Plastic injection molding machine
- Plastic Injection Molding Machines
- plastic injection robot
- Plastic Molding machine
- Plastic Molding Machines
- plastic molding press
- plastic phone case making machine
- plastic-molding machine
- powerful granulator
- Powerful Type Sound-Proof Granulator
- production of plastic seats
- Robot injection molding
- robot injection molding machine
- robot manufacturing companies
- Robotic arm for injection molding machine
- robotic injection molding machines
- robotics in injection molding
- SCARA robot
- SCARA robots
- Service-oriented manufacturing
- Servo Cylinder Robot
- servo driven robot
- Servo Driven Robots
- servo injection robots
- Servo-Driven Robot
- Setup of injection machine
- Silicone Injection Molding Machine
- six-axis industrial robot
- Stainless Hopper Dryer
- Stainless Hopper Dryers
- star club
- swing arm robot
- the choice between servo-driven robots and hydraulic robots will have a certain impact on efficiency
- the most popular injection molding machine
- the type of injection molding robot
- toggle clamp injection molding machine
- Toggle Hydraulic Injection Molding Machines
- toggle injection molding machine
- Top 10 brands of injection robots
- Topstar
- Topstar Engineering
- Topstar Industrial Robots
- Topstar injection molding intelligent
- Topstar Scara Robots
- Useful Injection molding machine
- Vertical machining centers
- volumetric type blender
- water chiller
- water chillers
- water distributor
- Water Type MoldTemperature Controller
- We often face choices when performing injection molding. We will choose the type of injection molding machine
- wholesale of injection molding machines
- x carve CNC