What are the most common custom solutions for injection molding machines?
2024/10/10 By Topstar
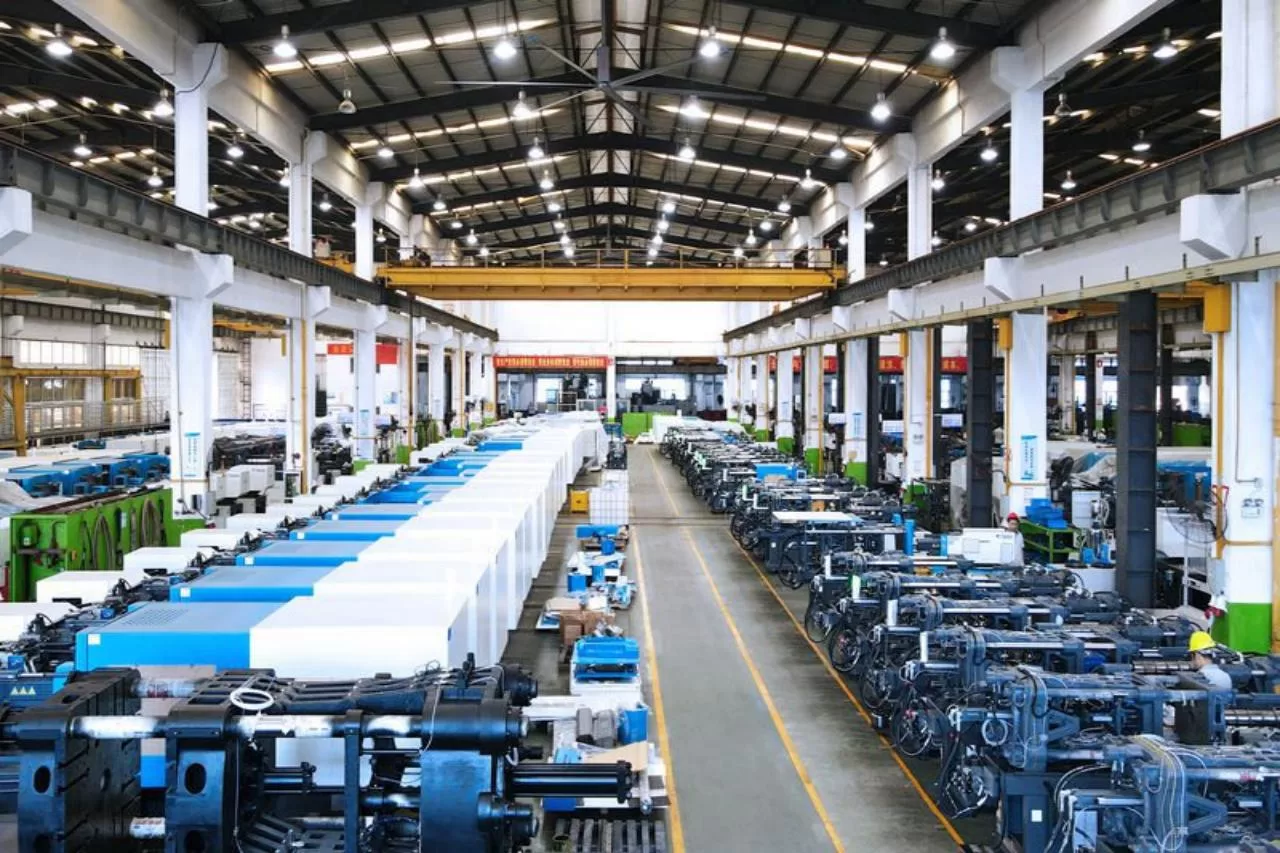
Injection molding machines are essential equipment for producing a variety of plastic products. Different injection molding solutions are required for other regions, companies, and products. For medical, auto parts, and 3C electronics companies, a suitable customized injection molding solution can significantly affect production efficiency, product quality, and overall competitiveness. No matter what industry you are in, Topstar will provide various customized solutions based on the characteristics of the industry, aiming to meet the product needs of different industries. We will share several of the most common customized solutions for injection molding machines.
Choose different customized solutions for injection molding machines according to the industry
One of the most basic customizations of injection molding machines is to choose the suitable machine for a specific industry or product. For example, in South America, Europe, and other countries, companies have achieved significant results with optical products such as silicone car lights. For this industry that requires optical properties and precision and ensures light transmittance, thermal stability, and shape accuracy, Topstar will provide professional injection molding solutions with TE ll series electric injection molding machines as the core.
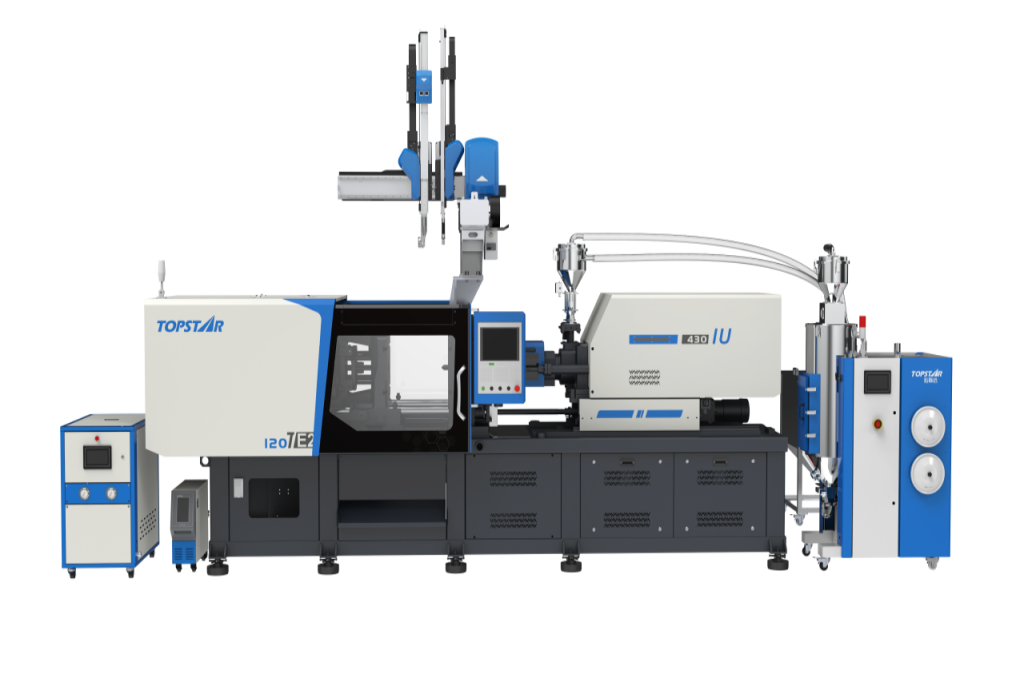
Among them, the TE ll series electric injection molding machine is equipped with two independent injection units, which can efficiently inject two materials in sequence: the first injection of PC material forms the basic structure, and then the injection of silicone raw materials completes the upper structure, reducing the assembly process, improving production efficiency, and producing product effects that traditional single-color injection molding cannot achieve. In addition, it will also be equipped with injection molding robots, mold temperature controllers and other auxiliary tools to more accurately control the injection molding accuracy and achieve efficient injection molding through the central controller. (Click to read for details)
Injection molding solutions for 3C electronics
In the 3C electronics category, products such as wire and cable connectors require not only the functionality of the product but also the aesthetics of the product molding appearance. There are also strict requirements, and the dimensions must be accurate during production.
Based on the product characteristics of this type of enterprise, Topstar will provide an injection molding solution with a TM II injection molding machine as the core. This solution can adjust the process parameters, such as drying time, temperature, and pressure of the peripheral auxiliary machine through the host. Thoroughly dry the raw materials before production to reduce defects such as bubbles, silver streaks, and water splashes in the product during the molding process.
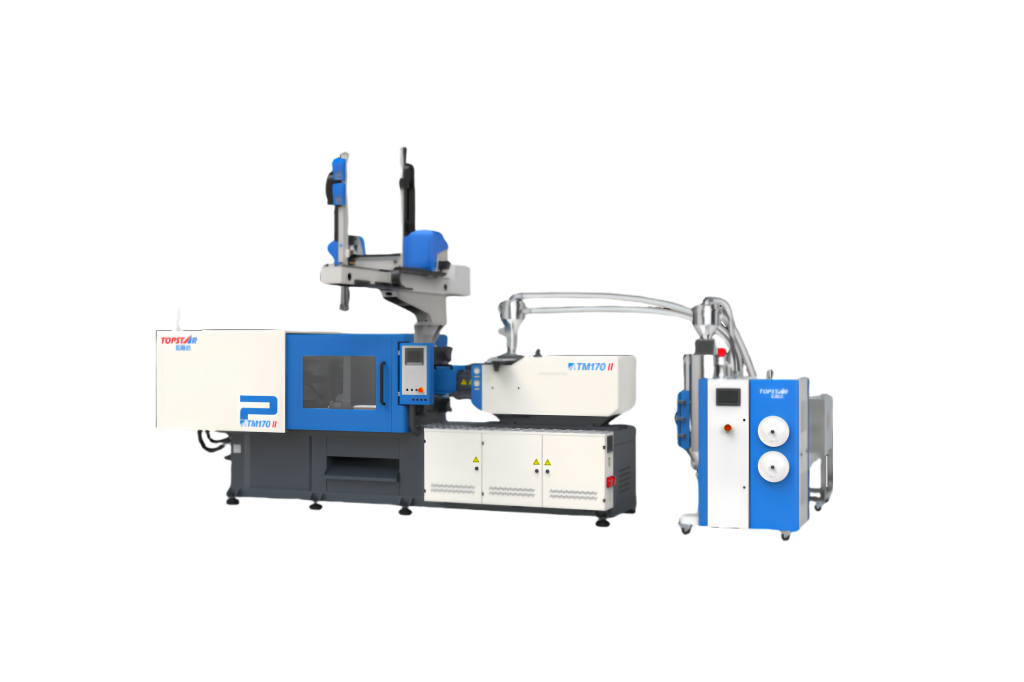
The core feature of this solution is the equipment is reasonably distributed according to the production process by using a distributed control method so as to realize the local control and monitoring of the equipment, shorten the data transmission distance, increase the data transmission speed and reduce the failure rate. (Click to read for details)
For daily chemical products, food packaging and other industries
In this type of industry, there are extremely high requirements for product quality. We know that manufacturers mainly make most packaging bottles from PET materials, which have high viscosity and are sensitive to temperature. Improper temperature can easily cause poor product permeability and uneven wall thickness, resulting in waste of raw materials and increased production costs.
In view of the difficulty of molding PET raw materials, Tosda provides a unique injection molding machine solution for PET. The use of special screws, high-torque motors, and increased power systems can improve the overall plasticizing efficiency by more than 20%. At the same time, it also dramatically reduces the defects such as bubbles and impurities that may occur during the molding process, ensuring the permeability and yield rate of the molded preforms.
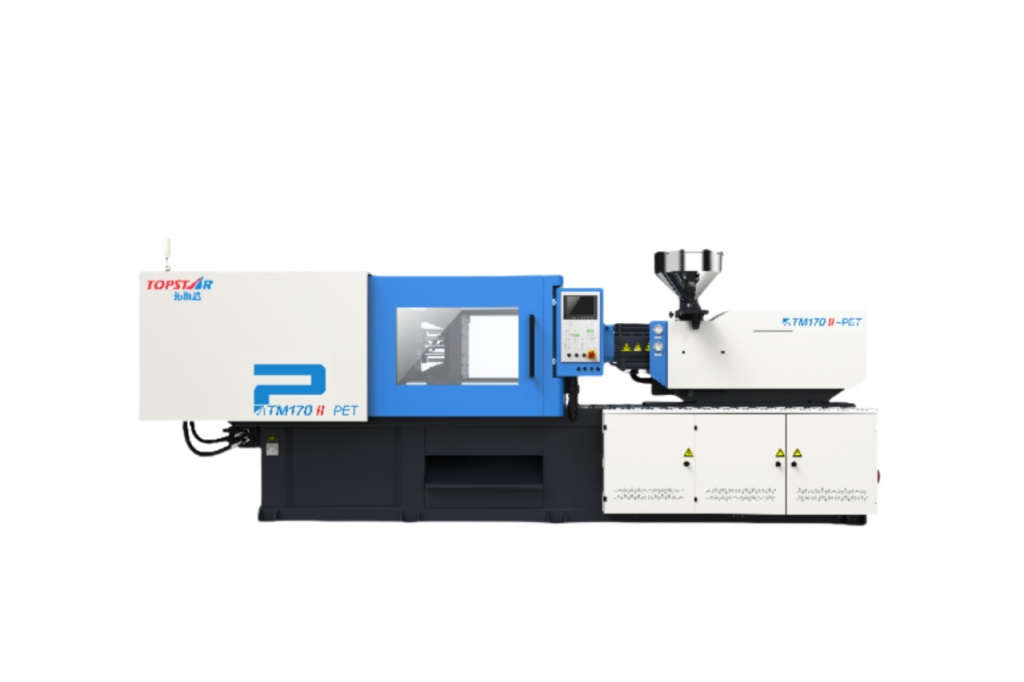
In addition, the process-integrated design concept based on the self-developed control system can support the host linkage robot signal and the host joint adjustment of the critical process parameters of the peripheral auxiliary machines. At the same time, the engineers equip the machine with an infrared heating coil to improve the efficiency of heat energy conversion and effectively reduce energy consumption during the production process.
Injection molding machine whole plant solution
In many countries and regions with underdeveloped economies, when night falls, workers continue transporting finished products on the production line in production workshops spanning tens of thousands of square meters, which remain in a dark light state. Only the equipment status indicator light and the quality inspection station are on. Many factory workshops reflect the need for more intelligence, low efficiency, long production cycles, and incompatible equipment.
At present, global industrialization has entered the 4.0 era. “Unmanned and intelligent are the general trend. Topstar uses the intelligent whole-plant solution of injection molding machines to help traditional factory workshops realize process intelligence and self-completion of automated equipment so as to achieve accurate uncrewed operation.
1-1024x682.webp)
The whole injection molding plant includes one-stop module planning and construction, injection molding machine + auxiliary equipment, front automation central feeding, back-end robot automation module, water, electricity and gas energy module, data management MES core block to realize the modular planning of the whole intelligent injection molding plant. Invest in manufacturing more accessible, and learn the integrated design, production, implementation and maintenance of factory planning + injection molding automation production line + data management of intelligent manufacturing comprehensive service platform.
Providing suitable solutions for different industries
Finding the right customized solution for injection molding machines is the key to optimizing production efficiency, reducing costs and improving product quality. Topstar will provide a wide range of personalized options based on the characteristics of different industries and product requirements to meet the specific needs of various sectors. If your industry has unique requirements and needs customized solutions, please feel free to contact us.
TRENDING POSTS
- What factors can cause delays in the injection molding process of plastic molding machine? 2024/10/10
- Exhibition Review| Topstar participates in InterPlas Thailand 2024 2024/10/10
- Star Case | Topstar helps Santong upgrade its intelligent plant 2024/10/10
- Topstar Special | National Science and Technology Workers Day 2024/10/10
HOT TOPIC
- 3 in 1 Compact Dehumidifying Dryer
- 5-axis CNC machine
- accuracy
- Air Chillers
- all electric injection molding machine
- all electric injection molding machines
- All-electric injection molding machines
- and overall production quality. Therefore
- AP-RubberPlas
- automated injection molding machine
- Automation changed engineering
- automation of injection molding robots
- auxiliary machine
- Bench Injection Molding Machine
- Cabinet dryer manufacturers
- Cabinet dryers
- chiller
- CNC Drilling Machine
- CNC Drilling Machines
- cnc engraving machine manufacturer
- cnc laser cutting machine manufacturer
- CNC machine
- CNC Machine Center
- CNC Machine for Sale
- CNC Machine Manufacturing
- CNC Machine Tool
- CNC machine tool product
- CNC Machining Center
- CNC wood carving machine
- Cooling system
- Cross-Walking Single Axis Servo Cylinder Robot
- Cross-Walking Single-Axis Servo Cylinder Robot
- Cross-Walking Three-Axis/Five-Axis Servo Driven Robot
- cross-walking three-axis/five-axis servo-driven robot
- Dehumidifier Dryer
- Dehumidifying Dryer
- delta parallel robot
- Desktop Injection Molding Machine
- Desktop injection molding machines
- Desktop Molding Machine
- desktop plastic injection machine
- Desktop Plastic Injection Molding Machine
- direct clamp injection molding machine
- Direct clamp injection molding machines
- Dosing & mixing system
- Drilling Centers
- Drying and dehumidification system
- drying and dehumidifying equipment
- Drying and Dehumidifying System
- drying system
- effective and efficient. Cabinet dryers are also used in other industries where large quantities of material need to be dried
- efficient injection molding machine
- elbow hydraulic injection molding machines
- electric injection molding machine
- electric injection molding machines
- energy-saving injection molding machine
- etc. Among injection molding robots
- exhibition
- features of CNC machine
- Feeding And Conveying System
- Five Axis Machine Center
- Fully automatic injection molding machine
- Gathering Topstar
- giant injection molding machine
- GMU-600 5-Axis Machining Center
- Granulating & Recycling System
- Heavy duty injection molding machine
- Honeycomb rotor dehumidifier
- horizontal injection molding machine
- Horizontal Injection Molding Machines
- Horizontal Injection Moulding Machine
- Horizontal Mixer manufacturer
- How The CNC Machine Works
- hybrid injection molding machine
- hydraulic injection molding machine
- Hydraulic Injection Molding Machines
- in this article
- Industrial robot
- Industrial Robot Chinese brand
- industrial robot parts
- industrial robot supplier
- Industrial robots
- Industry Chain
- Injection Manipulator
- injection mold machines
- Injection molding
- Injection molding automation
- Injection Molding Automation Solution
- injection molding dryer
- Injection molding equipment
- injection molding hopper dryer
- Injection molding machine
- injection molding machine brand
- Injection Molding Machine Factory
- Injection Molding Machine Manufacture
- Injection molding machine manufacturer
- injection molding machine manufacturers
- Injection molding machine procurement
- injection molding machine robotic arm
- injection molding machine with a robot
- Injection molding machines
- injection molding material dehumidifying
- injection molding plant
- Injection Molding Robot
- injection molding robot arm
- Injection molding robot automation
- Injection molding robotic arm
- injection molding robots
- Injection Moulding Robots
- Injection Robot
- Injection robot arm
- Injection robot manufacturer
- Injection robot wholesale
- injection robots
- intelligent injection molding machines
- Introducing Injection Robot
- It is the best choice for drying large quantities of material at once. Cabinetmakers use these machines because they are fast
- large injection molding machine
- Learn what industrial automation and robotics is
- low speed sound-proof granulator
- machine plastic molding
- make sure to add some! Improvements (2) Keyphrase in introduction: Your keyphrase or its synonyms appear in the first paragraph of the copy
- manipulator machine
- manufacturing
- micro injection molding machine
- middle speed granulator
- Mini CNC machine manufacturers.
- Mold Temperature Control System
- mold temperature controller
- molding material Dehumidifying System
- mould temperature controller
- mould temperature controllers
- New electric injection molding machine
- nitrogen dryer manufacturer
- nitrogen dryer system manufacturer
- Oil type mold temperature controller
- open day
- Outbound links: No outbound links appear in this page. Add some! Images: No images appear on this page. Add some! Internal links: No internal links appear in this page
- PET Preform injection molding
- phone case maker machine
- phone case making machine
- plastic bottle making machine
- plastic bottle manufacturing
- plastic bucket making machine
- plastic bucket manufacturing
- Plastic chair making machine
- plastic forming equipment
- plastic hopper dryer
- plastic injection machine
- plastic injection machines
- plastic injection molding
- Plastic injection molding equipment
- Plastic injection molding machine
- Plastic Injection Molding Machines
- plastic injection robot
- Plastic Molding machine
- Plastic Molding Machines
- plastic molding press
- plastic phone case making machine
- plastic-molding machine
- powerful granulator
- Powerful Type Sound-Proof Granulator
- production of plastic seats
- Robot injection molding
- robot injection molding machine
- robot manufacturing companies
- Robotic arm for injection molding machine
- robotic injection molding machines
- robotics in injection molding
- SCARA robot
- SCARA robots
- Service-oriented manufacturing
- Servo Cylinder Robot
- servo driven robot
- Servo Driven Robots
- servo injection robots
- Servo-Driven Robot
- Setup of injection machine
- Silicone Injection Molding Machine
- six-axis industrial robot
- Stainless Hopper Dryer
- Stainless Hopper Dryers
- star club
- swing arm robot
- the choice between servo-driven robots and hydraulic robots will have a certain impact on efficiency
- the most popular injection molding machine
- the type of injection molding robot
- toggle clamp injection molding machine
- Toggle Hydraulic Injection Molding Machines
- toggle injection molding machine
- Top 10 brands of injection robots
- Topstar
- Topstar Engineering
- Topstar Industrial Robots
- Topstar injection molding intelligent
- Topstar Scara Robots
- Useful Injection molding machine
- Vertical machining centers
- volumetric type blender
- water chiller
- water chillers
- water distributor
- Water Type MoldTemperature Controller
- We often face choices when performing injection molding. We will choose the type of injection molding machine
- wholesale of injection molding machines
- x carve CNC