Innovative injection molding machines for the automotive lighting industry
2024/10/01 By Topstar
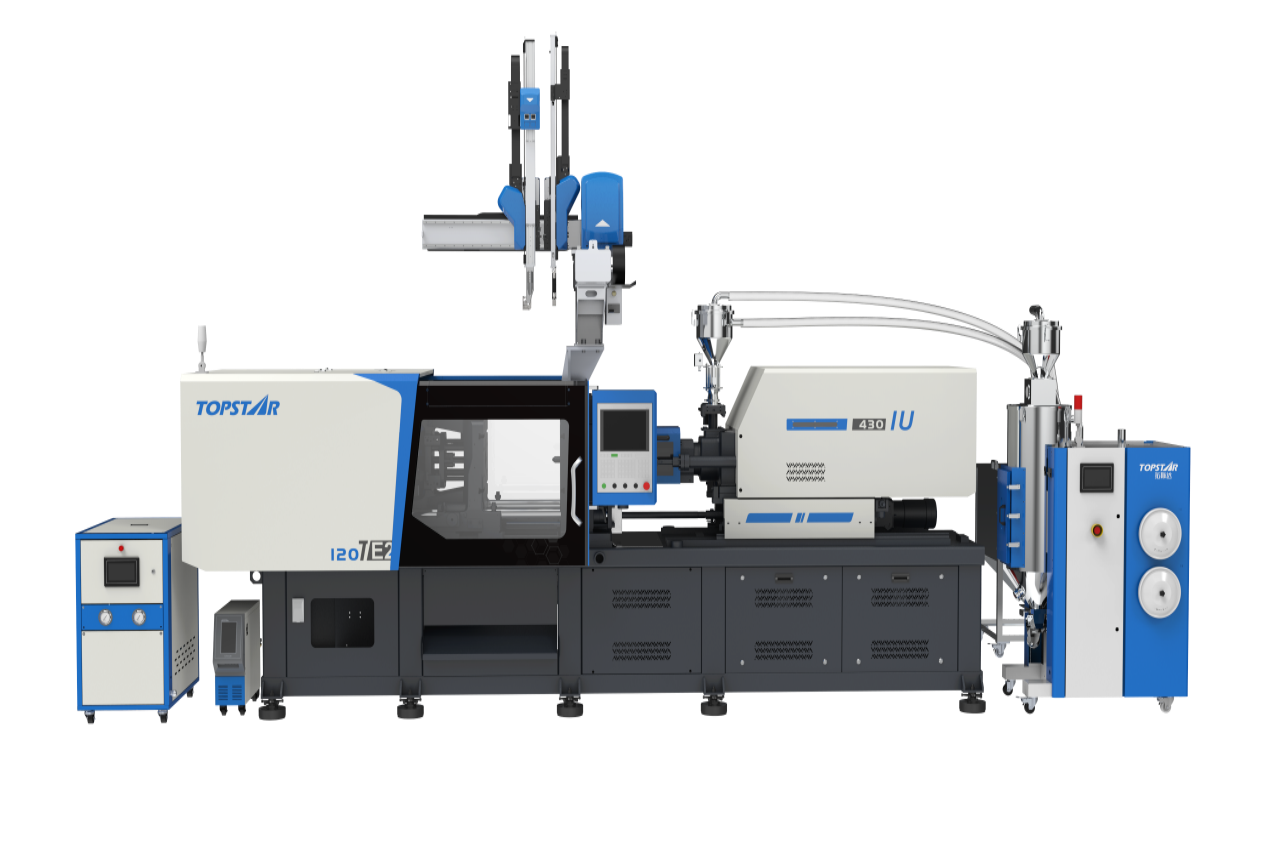
Automobile headlights comprise reflectors, lenses, housings, light sources, etc. The lightweight design makes more than 90% use plastics in manufacturing. The plastics used, such as PC, PP, ABS, PMMA, etc., can improve headlights’ light transmittance and shock resistance due to their lightweight, impact resistance, and high transparency. Topstar provides innovative injection molding machines solution for “automotive lighting silicone car lights dual-material” and “automotive PMMA thick-walled car lights.” The two solutions can meet headlight plastic products’ optical and precision requirements, ensure light transmittance, thermal stability and shape accuracy, and improve production efficiency and product quality.
Automotive lighting silicone car lights dual-material particular injection molding machines solution
TE ll electric injection molding machine at the core of the solution
Research on silicone car light molding technology in Europe has achieved remarkable results, and it has become an innovative breakthrough in automotive lighting. It has gradually entered the field of intelligent driving. The ADB system is the configuration trend in the future field of intelligent driving lighting. It can intelligently sense vehicle and road conditions, automatically adjust the high beam, and significantly improve night driving safety.
As the raw material of automotive ADB silicone inner lens, liquid silicone can provide higher design flexibility than traditional optical lens materials. It can manufacture high-precision and complex automotive silicone inner lens products. It also has excellent heat resistance and anti-yellowing properties, which ensures the stability of the lens in the entire car. For silicone headlight molding technology, Topstar has launched a dedicated injection molding solution and secondary injection molding process with TE ll electric injection molding machine as the core to ensure that the product meets optical standards.
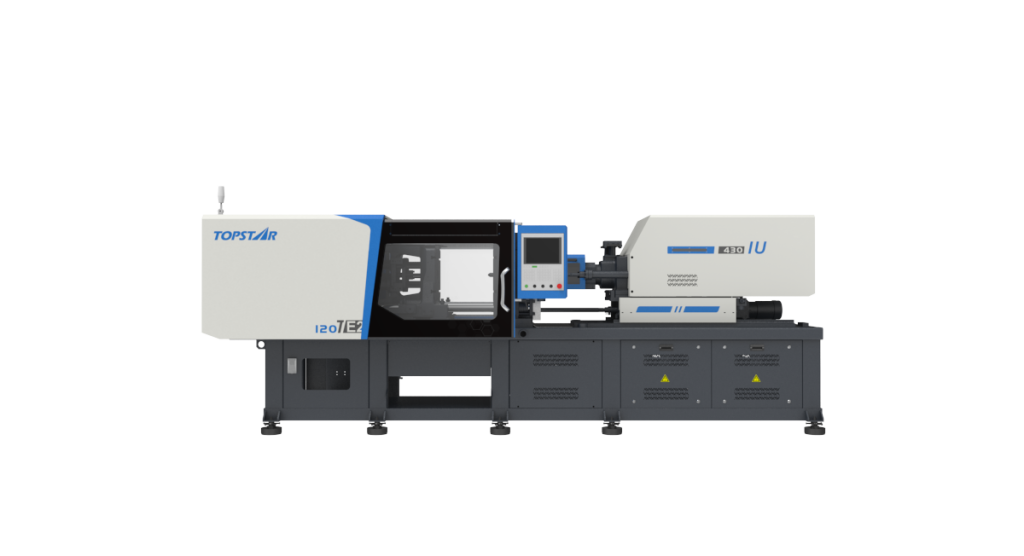
Two independent injection units
This solution’s TE ll electric injection molding machine has two independent injection units, which can efficiently inject two materials in sequence. The injection molding machine forms the basic structure by first injecting the PC material. Then, it injects the raw silicone material to complete the upper structure, reducing assembly steps, improving production efficiency, and achieving product effects that traditional single-color injection molding cannot match.
High stability template
Wide support feet provide stable dynamic support to protect the mold and machine better. It adopts a non-contact tie rod that does not require lubrication, which can reduce pollutants and the column’s strain. It also has a linear guide rail, low damping, smoother operation, and more sensitive low-pressure mold protection.
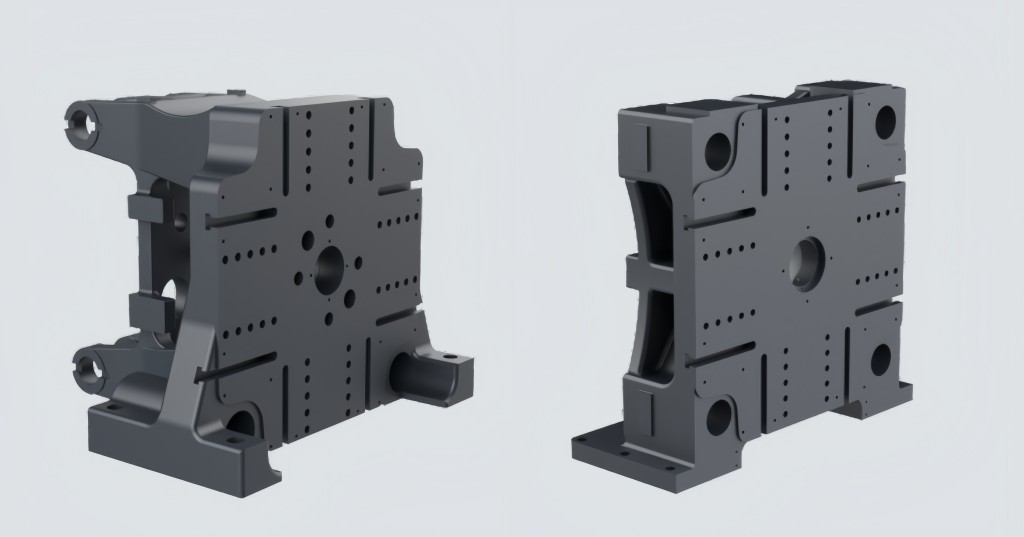
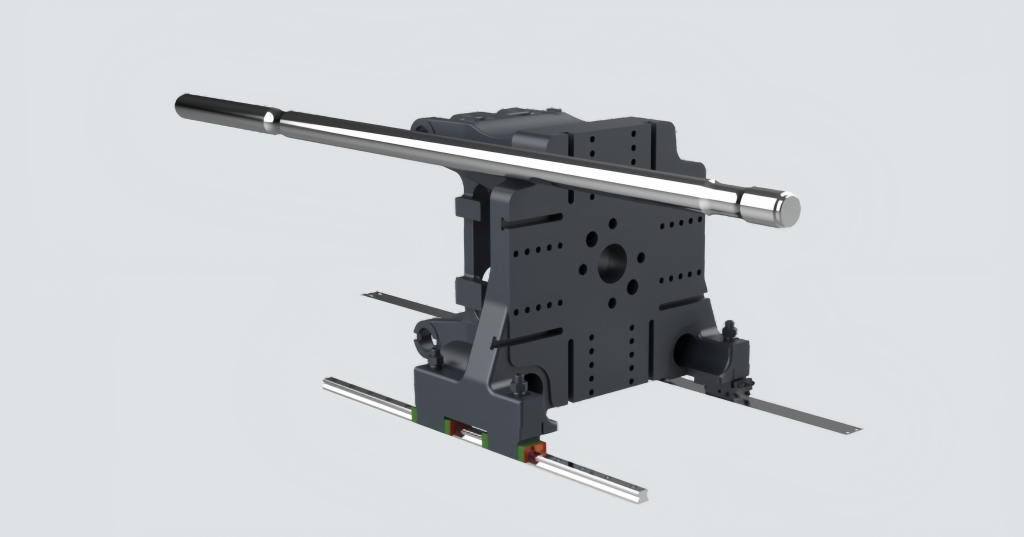
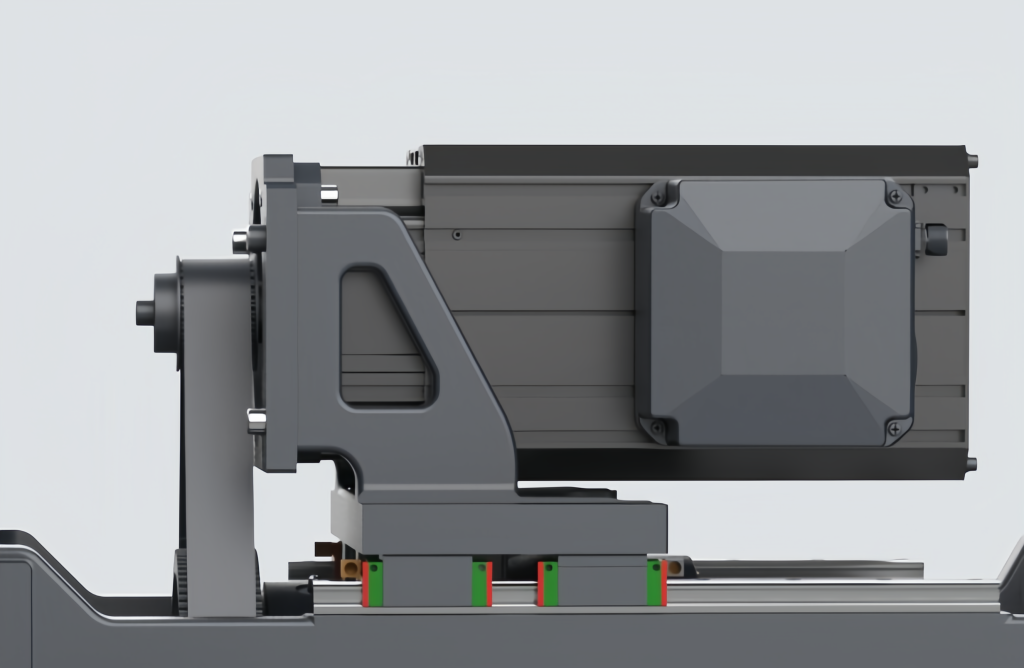
Topstar provides one-stop services, from raw silicone materials to mold design and injection molding equipment to solutions for customers in the automotive lighting industry to meet the market demand for high-end automotive lighting products.
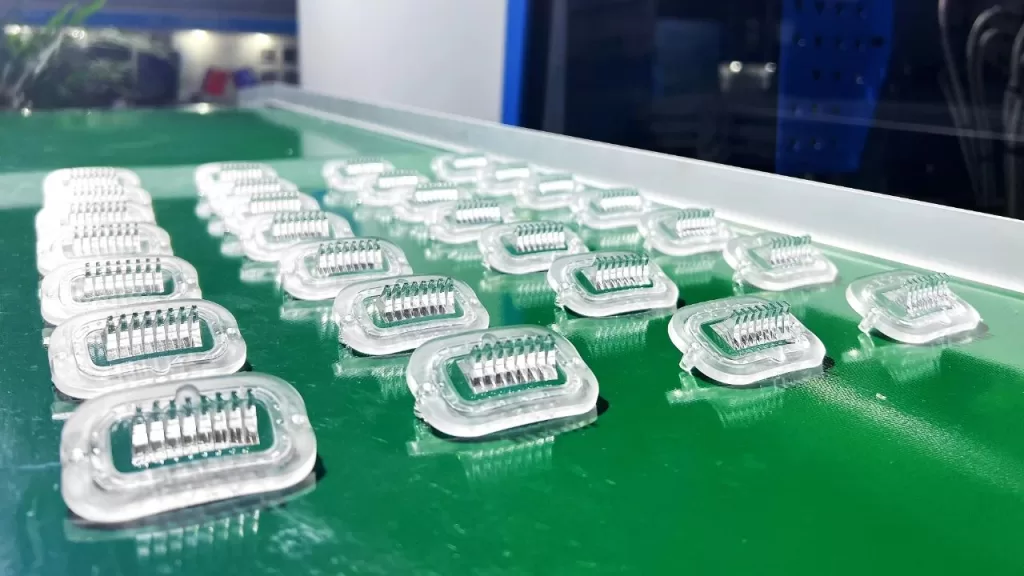
Particular injection molding machines solution for automotive PMMA thick-walled headlights
The automotive PMMA thick-walled headlight solution targets the internal stress and bubble defects that may form in the thick-walled headlight lens during high-pressure injection molding.
This solution performs secondary injection molding on the headlight lens with a wall thickness of 35mm, significantly improving product quality and optical performance and shortening the molding cycle.
Direct pressure injection molding machine at the core of the solution
The automotive light guide machine adopts a direct pressure injection molding machine with a clamping structure, which can ensure that the clamping force is evenly distributed in the center of the template, the template parallelism and the perfect fit of the mold, which is conducive to exhaust and effectively solves the bubble and under-injection problems of light guide products in production. Through the control of critical parameters such as high injection pressure and low speed (uniform speed), it can comprehensively solve the problems of yellowing, shrinkage, shrinkage, shrinkage and black spots that may occur in the production process of light guide products, ensuring the high quality and optical performance of the products.
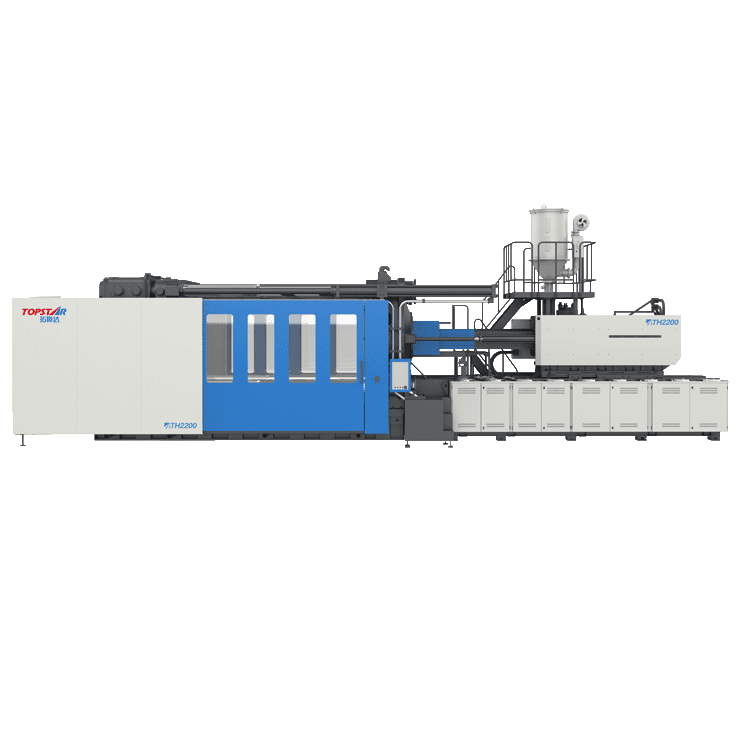
At the same time, it is equipped with an optical-grade dedicated shooting platform, a forward movement design for the shooting platform, and a double-axis oil cylinder to further enhance the accuracy and consistency of injection. In addition, it is equipped with Topstar’s six-axis robot as a back-end automation system to accurately grasp semi-finished products for the first injection and precise placement of secondary injection, ensuring the dual improvement of production efficiency and product consistency.
Make injection molding easier.
Topstar will continue to understand customer needs sincerely, follow the development trend of the automotive lighting industry, provide customers with more suitable solutions, provide more innovative support, and make injection molding easier.
TRENDING POSTS
- What factors can cause delays in the injection molding process of plastic molding machine? 2024/10/01
- Exhibition Review| Topstar participates in InterPlas Thailand 2024 2024/10/01
- Star Case | Topstar helps Santong upgrade its intelligent plant 2024/10/01
- Topstar Special | National Science and Technology Workers Day 2024/10/01
HOT TOPIC
- .ervo motor-driven linear robots
- 1.0 guangdong topstar technology co. ltd
- 1.0 topstar china
- 1.0 topstar robot
- 11
- 2
- 21
- 23
- 3 axis robot
- 3 axis robots
- 3 in 1 Compact Dehumidifying Dryer
- 3-axis robot
- 3-axis robots
- 39
- 41
- 5-axis CNC machine
- 62
- accuracy
- Air Chillers
- all electric injection molding machine
- all electric injection molding machines
- All-electric injection molding machines
- and overall production quality. Therefore
- AP-RubberPlas
- automated injection molding machine
- Automation changed engineering
- automation of injection molding robots
- auxiliary machine
- Bench Injection Molding Machine
- Cabinet dryer manufacturers
- Cabinet dryers
- chiller
- CNC Drilling Machine
- CNC Drilling Machines
- cnc engraving machine manufacturer
- cnc laser cutting machine manufacturer
- CNC machine
- CNC Machine Center
- CNC Machine for Sale
- CNC Machine Manufacturing
- CNC Machine Tool
- CNC machine tool product
- CNC Machining Center
- CNC wood carving machine
- Cooling system
- Cross-Walking Single Axis Servo Cylinder Robot
- Cross-Walking Single-Axis Servo Cylinder Robot
- Cross-Walking Three-Axis/Five-Axis Servo Driven Robot
- cross-walking three-axis/five-axis servo-driven robot
- Dehumidifier Dryer
- Dehumidifying Dryer
- delta parallel robot
- Desktop Injection Molding Machine
- Desktop injection molding machines
- Desktop Molding Machine
- desktop plastic injection machine
- Desktop Plastic Injection Molding Machine
- direct clamp injection molding machine
- Direct clamp injection molding machines
- Dosing & mixing system
- Drilling Centers
- Drying and dehumidification system
- drying and dehumidifying equipment
- Drying and Dehumidifying System
- drying system
- effective and efficient. Cabinet dryers are also used in other industries where large quantities of material need to be dried
- efficient injection molding machine
- elbow hydraulic injection molding machines
- electric injection molding machine
- electric injection molding machines
- energy-efficient injection molding robot
- energy-saving injection molding machine
- etc. Among injection molding robots
- exhibition
- features of CNC machine
- Feeding And Conveying System
- Five Axis Machine Center
- Fully automatic injection molding machine
- Gathering Topstar
- giant injection molding machine
- GMU-600 5-Axis Machining Center
- Granulating & Recycling System
- Heavy duty injection molding machine
- High-precision electric molding machines
- high-precision plastic molding machines
- high-speed all electric injection molding machine
- Honeycomb rotor dehumidifier
- horizontal injection molding machine
- Horizontal Injection Molding Machines
- Horizontal Injection Moulding Machine
- Horizontal Mixer manufacturer
- How The CNC Machine Works
- hybrid injection molding machine
- hydraulic injection molding machine
- Hydraulic Injection Molding Machines
- in this article
- Industrial robot
- Industrial Robot Chinese brand
- industrial robot parts
- industrial robot supplier
- Industrial robots
- Industry Chain
- Injection Manipulator
- injection manipulator robot
- injection mold machines
- Injection molding
- Injection molding automation
- Injection Molding Automation Solution
- injection molding dryer
- Injection molding equipment
- injection molding hopper dryer
- Injection molding machine
- injection molding machine brand
- Injection Molding Machine Factory
- Injection Molding Machine Manufacture
- Injection molding machine manufacturer
- injection molding machine manufacturers
- Injection molding machine procurement
- injection molding machine robotic arm
- injection molding machine with a robot
- Injection molding machines
- injection molding material dehumidifying
- injection molding plant
- Injection Molding Robot
- injection molding robot arm
- Injection molding robot automation
- Injection molding robotic arm
- injection molding robots
- Injection moulding machine
- Injection Moulding Robots
- Injection Robot
- Injection robot arm
- Injection robot manufacturer
- Injection robot wholesale
- injection robots
- intelligent injection molding machines
- Introducing Injection Robot
- It is the best choice for drying large quantities of material at once. Cabinetmakers use these machines because they are fast
- large injection molding machine
- large injection molding machines
- Learn what industrial automation and robotics is
- linear robot
- linear robots
- low speed sound-proof granulator
- machine plastic molding
- make sure to add some! Improvements (2) Keyphrase in introduction: Your keyphrase or its synonyms appear in the first paragraph of the copy
- manipulator machine
- manufacturing
- medical grade injection molding machines
- medical injection molding machine
- medical injection molding machines
- micro injection molding machine
- middle speed granulator
- Mini CNC machine manufacturers.
- Mold Temperature Control System
- mold temperature controller
- mold temperature controllers
- molding material Dehumidifying System
- mould temperature control system
- mould temperature controller
- mould temperature controllers
- New electric injection molding machine
- nitrogen dryer manufacturer
- nitrogen dryer system manufacturer
- Oil type mold temperature controller
- Oil type mold temperature controllers
- open day
- Outbound links: No outbound links appear in this page. Add some! Images: No images appear on this page. Add some! Internal links: No internal links appear in this page
- PET Preform injection molding
- phone case maker machine
- phone case making machine
- plastic bottle making machine
- plastic bottle manufacturing
- plastic bucket making machine
- plastic bucket manufacturing
- Plastic chair making machine
- plastic forming equipment
- plastic hopper dryer
- plastic injection machine
- plastic injection machines
- plastic injection molding
- Plastic injection molding equipment
- Plastic injection molding machine
- Plastic Injection Molding Machines
- plastic injection moulding machine
- plastic injection robot
- Plastic Molding machine
- Plastic Molding Machines
- plastic molding press
- plastic moulding machine
- plastic phone case making machine
- plastic-molding machine
- powerful granulator
- Powerful Type Sound-Proof Granulator
- precision injection molding
- precision injection molding machines
- production of plastic seats
- pure water mould temperature controller
- Robot injection molding
- robot injection molding machine
- robot manufacturing companies
- Robotic arm for injection molding machine
- robotic injection molding machines
- robotics in injection molding
- SCARA robot
- SCARA robots
- Service-oriented manufacturing
- Servo Cylinder Robot
- servo driven robot
- Servo Driven Robots
- servo injection robots
- servo motor-driven linear robots
- servo-driven 3-axis robot
- Servo-Driven Robot
- Setup of injection machine
- Silicone Injection Molding Machine
- six-axis industrial robot
- Stainless Hopper Dryer
- Stainless Hopper Dryers
- star club
- swing arm robot
- take-out robots
- the choice between servo-driven robots and hydraulic robots will have a certain impact on efficiency
- the most popular injection molding machine
- the type of injection molding robot
- toggle clamp injection molding machine
- Toggle Hydraulic Injection Molding Machines
- toggle injection molding machine
- Top 10 brands of injection robots
- Topstar
- Topstar Engineering
- Topstar Industrial Robots
- Topstar injection molding intelligent
- Topstar Scara Robots
- Useful Injection molding machine
- Vertical machining centers
- volumetric type blender
- water chiller
- water chillers
- water distributor
- water type mold temperature controller
- Water Type MoldTemperature Controller
- Water-Type Mould Temperature Controllers
- We often face choices when performing injection molding. We will choose the type of injection molding machine
- wholesale of injection molding machines
- x carve CNC
- 热门查询 点击次数 展示 排名 topstar