What are the advantages of using a servo-driven plastic injection molding machine?
2024/09/20 By Topstar

The technology behind plastic injection molding machine in industries such as automotive, electronics, and consumer goods is critical to delivering high-quality products while optimizing operating costs. One of the most innovative advances in these technologies is the use of servo-driven plastic injection molding machines, which offer many advantages and differences over traditional hydraulic systems. Below, we share the key benefits of Topstar’s servo-driven plastic injection molding machines, their technical features, and why they are the right choice for your precision manufacturing process.
Improve Energy Efficiency with Servo Drive
One of the most obvious advantages of using servo-driven technology is its improved energy efficiency. Unlike traditional hydraulic presses that run continuously, servo-driven machines adjust their energy consumption according to process needs. Servo motors control the movement of the injection unit and clamping system, allowing precise control of speed, pressure, and position. This real-time adjustment means that energy is only used when necessary, reducing total power consumption by up to 30-80% compared to standard hydraulic presses. For manufacturers, this can save a lot of electricity costs.
Improved precision and control in plastic injection molding
In the medical field or electronics, even the slightest deviation in the molding process can lead to defective or rejected parts. Servo-driven plastic injection molding machines offer precision and control over traditional hydraulic systems. Servo motors can provide precise positioning and motion control, making the injection, clamping and ejection processes more accurate. This high level of control allows for more excellent repeatability, ensuring the same quality for every part produced. Topstar’s proprietary servo drive technology can adjust factors such as injection speed, pressure, and clamping force in real-time, allowing manufacturers to fine-tune the process to meet exact specifications.
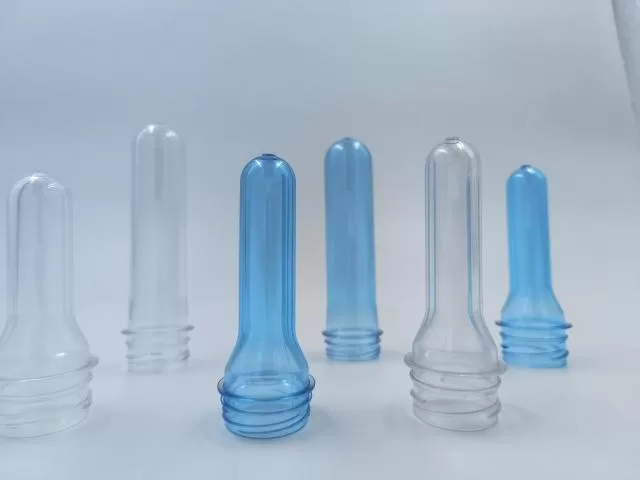
Servo-driven plastic injection molding machine reduces cycle times
Another significant benefit of servo-driven plastic injection molding machines is the ability to achieve faster cycle times. The servo motors can quickly accelerate and decelerate machine motion. At the same time, the new oblique hinge layout allows for ultra-long mold opening, which reduces mold opening and closing times, speeds up injection speeds and improves ejection process efficiency. This increase in speed can significantly reduce the total cycle time per part, thereby increasing production capacity. For manufacturers in high-volume manufacturing industries such as automotive, the ability to produce more parts in less time can provide a substantial competitive advantage. In addition to speeding up the production process, servo drives also provide smoother transitions between the different stages of the molding cycle. This reduces wear on machine components and extends the life of the equipment.
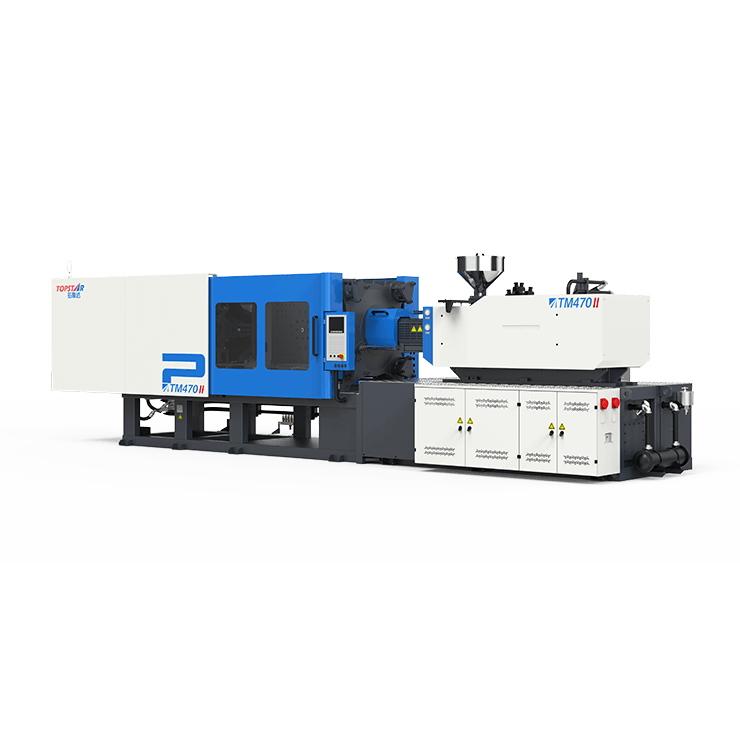
Servo-driven plastic injection molding machines are more flexible and versatile
Flexibility is essential for manufacturers who produce multiple products or frequently change molds for production. Plastic injection molding machines using servo drives are highly flexible, and the new mold adjustment mechanism can achieve automatic and precise mold adjustment with one click, allowing manufacturers to easily switch between different molds, materials and processes without a lot of adjustments or reconfigurations.
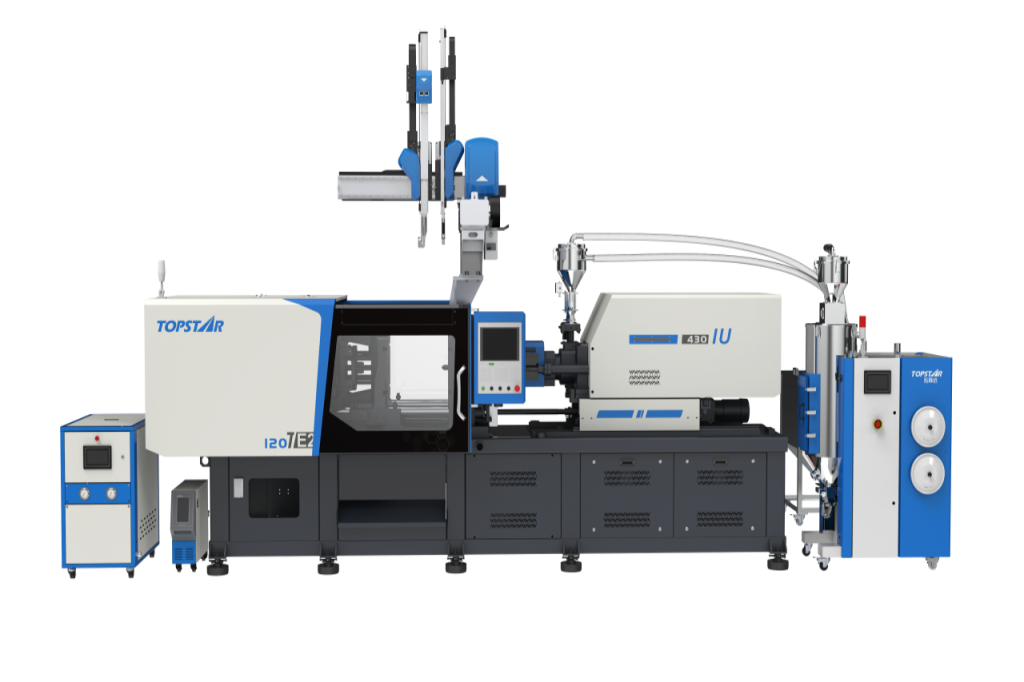
The precise control provided by servo drive technology enables it to handle a variety of plastic materials, including high-performance engineering plastics that require specific processing conditions. This versatility allows manufacturers to use the same plastic injection molding machine to produce parts for multiple industries, such as automotive, electronics, medical and consumer goods. At the same time, Topstar’s servo control technology can also be highly integrated with other auxiliary machine systems, allowing users to obtain auxiliary equipment operating data directly on the injection molding machine and making operation more convenient.
It can target a variety of process technologies for specific industry equipment, such as robot end jitter suppression, multi-pump converging/dividing hydraulic control, and multi-axis coordinated synchronous control.
Improved Product Quality
One of the main ways servo-driven machines improve product quality is through precise control of the molding process. By precisely controlling injection speed, pressure, and cooling time, manufacturers can minimize common defects such as flash, warping, and short shots. Servo drives also provide better control of clamping force, ensuring the mold remains tightly sealed during injection and preventing problems such as material leaks or incomplete fill. The improved repeatability of servo-driven machines means manufacturers can produce a large number of parts with consistent quality, reducing the number of rejected parts and minimizing waste.
Why Choose a Servo-Driven Plastic Injection Molding Machine?
Servo-driven plastic injection molding machines can improve efficiency and precision, among many other advantages of the production process. At Topstar, we help our customers stay ahead by using our own servo-driven plastic injection molding machines. Whether you are producing parts for the automotive, medical, or consumer goods industries, they are designed to meet the highest standards of performance, reliability, and flexibility.
TRENDING POSTS
- What factors can cause delays in the injection molding process of plastic molding machine? 2024/09/20
- Exhibition Review| Topstar participates in InterPlas Thailand 2024 2024/09/20
- Star Case | Topstar helps Santong upgrade its intelligent plant 2024/09/20
- Topstar Special | National Science and Technology Workers Day 2024/09/20
HOT TOPIC
- .ervo motor-driven linear robots
- 3 axis robot
- 3 axis robots
- 3 in 1 Compact Dehumidifying Dryer
- 3-axis robot
- 3-axis robots
- 5-axis CNC machine
- accuracy
- Air Chillers
- all electric injection molding machine
- all electric injection molding machines
- All-electric injection molding machines
- and overall production quality. Therefore
- AP-RubberPlas
- automated injection molding machine
- Automation changed engineering
- automation of injection molding robots
- auxiliary machine
- Bench Injection Molding Machine
- Cabinet dryer manufacturers
- Cabinet dryers
- chiller
- CNC Drilling Machine
- CNC Drilling Machines
- cnc engraving machine manufacturer
- cnc laser cutting machine manufacturer
- CNC machine
- CNC Machine Center
- CNC Machine for Sale
- CNC Machine Manufacturing
- CNC Machine Tool
- CNC machine tool product
- CNC Machining Center
- CNC wood carving machine
- Cooling system
- Cross-Walking Single Axis Servo Cylinder Robot
- Cross-Walking Single-Axis Servo Cylinder Robot
- Cross-Walking Three-Axis/Five-Axis Servo Driven Robot
- cross-walking three-axis/five-axis servo-driven robot
- Dehumidifier Dryer
- Dehumidifying Dryer
- delta parallel robot
- Desktop Injection Molding Machine
- Desktop injection molding machines
- Desktop Molding Machine
- desktop plastic injection machine
- Desktop Plastic Injection Molding Machine
- direct clamp injection molding machine
- Direct clamp injection molding machines
- Dosing & mixing system
- Drilling Centers
- Drying and dehumidification system
- drying and dehumidifying equipment
- Drying and Dehumidifying System
- drying system
- effective and efficient. Cabinet dryers are also used in other industries where large quantities of material need to be dried
- efficient injection molding machine
- elbow hydraulic injection molding machines
- electric injection molding machine
- electric injection molding machines
- energy-efficient injection molding robot
- energy-saving injection molding machine
- etc. Among injection molding robots
- exhibition
- features of CNC machine
- Feeding And Conveying System
- Five Axis Machine Center
- Fully automatic injection molding machine
- Gathering Topstar
- giant injection molding machine
- GMU-600 5-Axis Machining Center
- Granulating & Recycling System
- Heavy duty injection molding machine
- High-precision electric molding machines
- high-precision plastic molding machines
- high-speed all electric injection molding machine
- Honeycomb rotor dehumidifier
- horizontal injection molding machine
- Horizontal Injection Molding Machines
- Horizontal Injection Moulding Machine
- Horizontal Mixer manufacturer
- How The CNC Machine Works
- hybrid injection molding machine
- hydraulic injection molding machine
- Hydraulic Injection Molding Machines
- in this article
- Industrial robot
- Industrial Robot Chinese brand
- industrial robot parts
- industrial robot supplier
- Industrial robots
- Industry Chain
- Injection Manipulator
- injection manipulator robot
- injection mold machines
- Injection molding
- Injection molding automation
- Injection Molding Automation Solution
- injection molding dryer
- Injection molding equipment
- injection molding hopper dryer
- Injection molding machine
- injection molding machine brand
- Injection Molding Machine Factory
- Injection Molding Machine Manufacture
- Injection molding machine manufacturer
- injection molding machine manufacturers
- Injection molding machine procurement
- injection molding machine robotic arm
- injection molding machine with a robot
- Injection molding machines
- injection molding material dehumidifying
- injection molding plant
- Injection Molding Robot
- injection molding robot arm
- Injection molding robot automation
- Injection molding robotic arm
- injection molding robots
- Injection moulding machine
- Injection Moulding Robots
- Injection Robot
- Injection robot arm
- Injection robot manufacturer
- Injection robot wholesale
- injection robots
- intelligent injection molding machines
- Introducing Injection Robot
- It is the best choice for drying large quantities of material at once. Cabinetmakers use these machines because they are fast
- large injection molding machine
- Learn what industrial automation and robotics is
- linear robot
- linear robots
- low speed sound-proof granulator
- machine plastic molding
- make sure to add some! Improvements (2) Keyphrase in introduction: Your keyphrase or its synonyms appear in the first paragraph of the copy
- manipulator machine
- manufacturing
- medical grade injection molding machines
- medical injection molding machine
- medical injection molding machines
- micro injection molding machine
- middle speed granulator
- Mini CNC machine manufacturers.
- Mold Temperature Control System
- mold temperature controller
- mold temperature controllers
- molding material Dehumidifying System
- mould temperature control system
- mould temperature controller
- mould temperature controllers
- New electric injection molding machine
- nitrogen dryer manufacturer
- nitrogen dryer system manufacturer
- Oil type mold temperature controller
- Oil type mold temperature controllers
- open day
- Outbound links: No outbound links appear in this page. Add some! Images: No images appear on this page. Add some! Internal links: No internal links appear in this page
- PET Preform injection molding
- phone case maker machine
- phone case making machine
- plastic bottle making machine
- plastic bottle manufacturing
- plastic bucket making machine
- plastic bucket manufacturing
- Plastic chair making machine
- plastic forming equipment
- plastic hopper dryer
- plastic injection machine
- plastic injection machines
- plastic injection molding
- Plastic injection molding equipment
- Plastic injection molding machine
- Plastic Injection Molding Machines
- plastic injection moulding machine
- plastic injection robot
- Plastic Molding machine
- Plastic Molding Machines
- plastic molding press
- plastic moulding machine
- plastic phone case making machine
- plastic-molding machine
- powerful granulator
- Powerful Type Sound-Proof Granulator
- precision injection molding
- precision injection molding machines
- production of plastic seats
- pure water mould temperature controller
- Robot injection molding
- robot injection molding machine
- robot manufacturing companies
- Robotic arm for injection molding machine
- robotic injection molding machines
- robotics in injection molding
- SCARA robot
- SCARA robots
- Service-oriented manufacturing
- Servo Cylinder Robot
- servo driven robot
- Servo Driven Robots
- servo injection robots
- servo motor-driven linear robots
- servo-driven 3-axis robot
- Servo-Driven Robot
- Setup of injection machine
- Silicone Injection Molding Machine
- six-axis industrial robot
- Stainless Hopper Dryer
- Stainless Hopper Dryers
- star club
- swing arm robot
- take-out robots
- the choice between servo-driven robots and hydraulic robots will have a certain impact on efficiency
- the most popular injection molding machine
- the type of injection molding robot
- toggle clamp injection molding machine
- Toggle Hydraulic Injection Molding Machines
- toggle injection molding machine
- Top 10 brands of injection robots
- Topstar
- Topstar Engineering
- Topstar Industrial Robots
- Topstar injection molding intelligent
- Topstar Scara Robots
- Useful Injection molding machine
- Vertical machining centers
- volumetric type blender
- water chiller
- water chillers
- water distributor
- water type mold temperature controller
- Water Type MoldTemperature Controller
- Water-Type Mould Temperature Controllers
- We often face choices when performing injection molding. We will choose the type of injection molding machine
- wholesale of injection molding machines
- x carve CNC