How to improve mold alignment in a horizontal injection molding machine?
2024/09/18 By Topstar
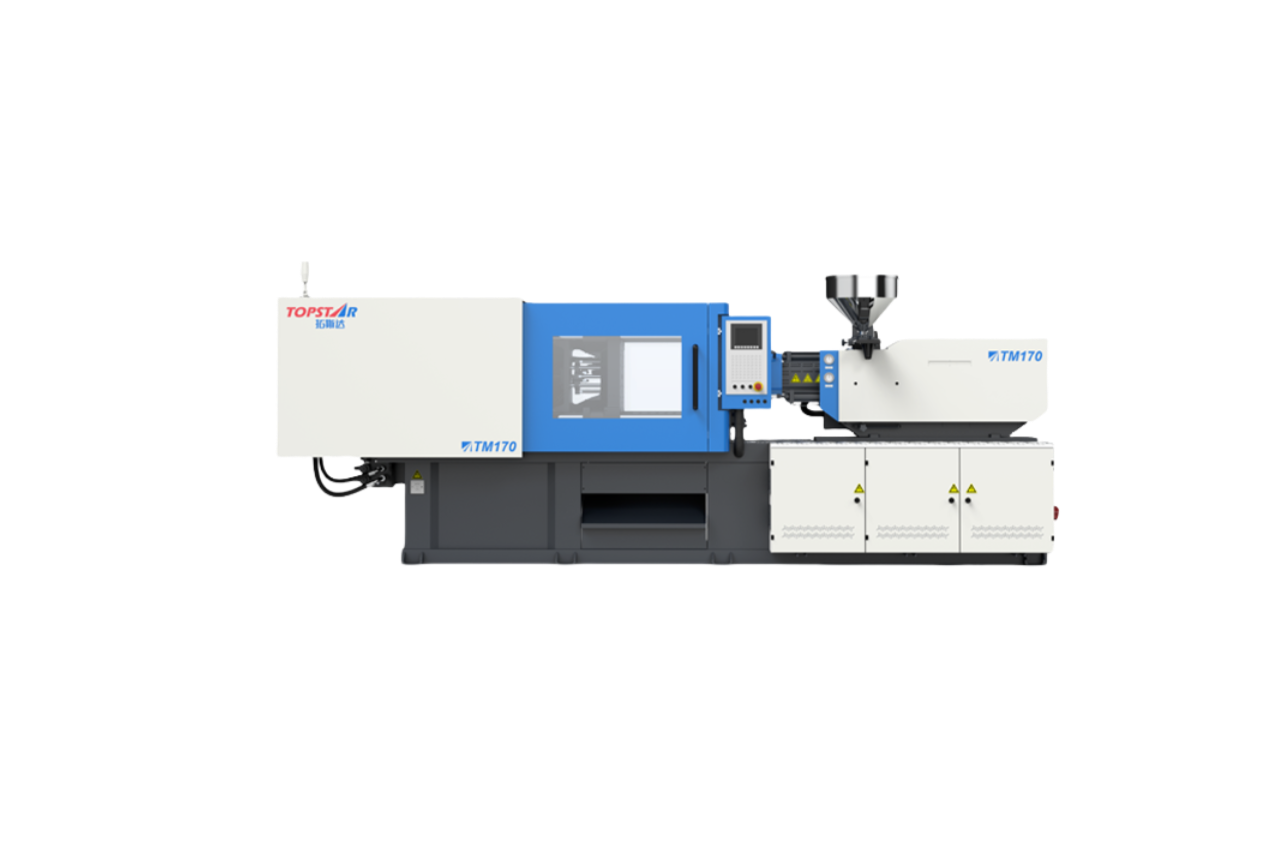
Improper mold alignment on horizontal injection molding machine can lead to various problems, including molded part defects, excessive machine wear, and even downtime. Whether in the automotive, consumer goods, or medical device industries, ensuring your molds are properly aligned can maximize efficiency, extend machine life, and improve product consistency. In this blog post, we’ll share Topstar’s practical strategies for strengthening mold alignment on horizontal injection molding machines and discuss factors that can affect alignment during injection molding.
Importance of mold alignment on horizontal injection molding machine
The main function of a horizontal injection molding machine is to produce precision plastic parts by injecting molten material into the mold. Mold alignment refers to the precise positioning of the two halves of the mold (the fixed platen and the movable platen) during the injection process. The molten material flows evenly into the cavity when the mold aligns perfectly, producing high-quality, uniform parts. On the other hand, misaligned molds can lead to problems such as flash, uneven filling, under-injection, and even damage to the mold and machine components. In horizontal injection molding machines, proper mold alignment evenly distributes the forces generated during injection and clamping on the mold. By addressing mold alignment issues, you can improve product quality, reduce machine downtime, and minimize the need for costly repairs or replacements.
Factors Affecting Horizontal Injection Molding Machine Mold Alignment
One of the main reasons for misalignment on horizontal injection molding machines is improper mold installation. You must properly install and center the mold on the machine platen during setup.
Another common factor is the wear of machine components over time. Tie rods, bushings, and other moving parts in horizontal injection molding machines can wear with extended use, causing misalignment between mold halves. Temperature fluctuations can also affect mold alignment. As the mold heats up and cools during the injection process, thermal expansion and contraction can cause changes in the alignment of the mold halves. Finally, the condition of the mold itself plays a critical role in alignment. Worn or damaged mold components can cause misalignment and poor part quality.
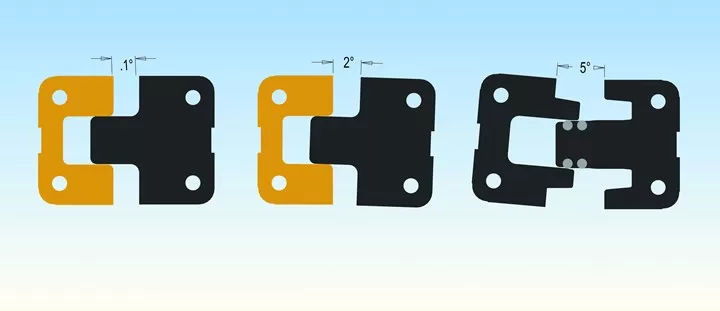
Brand-new mold adjustment structure for horizontal injection molding machines
Topstar has adopted a brand-new mold adjustment structure in its horizontal injection molding machines to achieve automatic adjustment functions. This one-touch operation simplifies mold setup, making it faster and easier to operate, even for operators with less technical knowledge. Automation ensures that the system aligns and adjusts the mold properly without manual intervention, thereby reducing the possibility of human error. This automated adjustment function is particularly useful in production environments where operators frequently change molds. It greatly reduces setup time, speeds up turnover, and increases productivity. The automated system can accurately adjust the mold to the optimal position, ensuring that the clamping force is evenly distributed on the mold. The uniformity of the clamping pressure prevents damage to the mold and the part being produced, resulting in higher-quality products with fewer defects.

Regular maintenance and inspections to prevent mold misalignment
Regular maintenance helps prevent misalignment and extends the machine’s and mold components’ life, even with a brand-new automatic mold adjustment structure.
During maintenance, check tie rods for signs of wear, bending or damage. Worn or damaged tie rods can cause uneven pressure on the mold, leading to misalignment and inconsistent parts.
Similarly, worn bushings can cause the two halves of the mold to shift during the molding process, resulting in poor alignment and defects in the final product. In addition to inspecting machine components, performing routine maintenance on the mold itself is also important. This includes checking guide pins, bushings and parting lines for wear or damage. If wear affects these parts, the two halves of the mold may not close properly and may misalign.
Control Temperature to Keep Molds Aligned
During the injection molding process, molds are subject to large temperature fluctuations because the mold heats up during the injection process and cools down as the plastic material solidifies. To prevent these temperature-induced changes, it is important to closely monitor and control mold temperature throughout the injection molding cycle. Mold temperature controllers can help maintain consistent temperatures, reducing the risk of misalignment caused by thermal expansion and contraction. Advanced cooling systems can help ensure that the mold remains evenly heated and aligned throughout the production process for complex molds with complex geometries or multiple cavities.
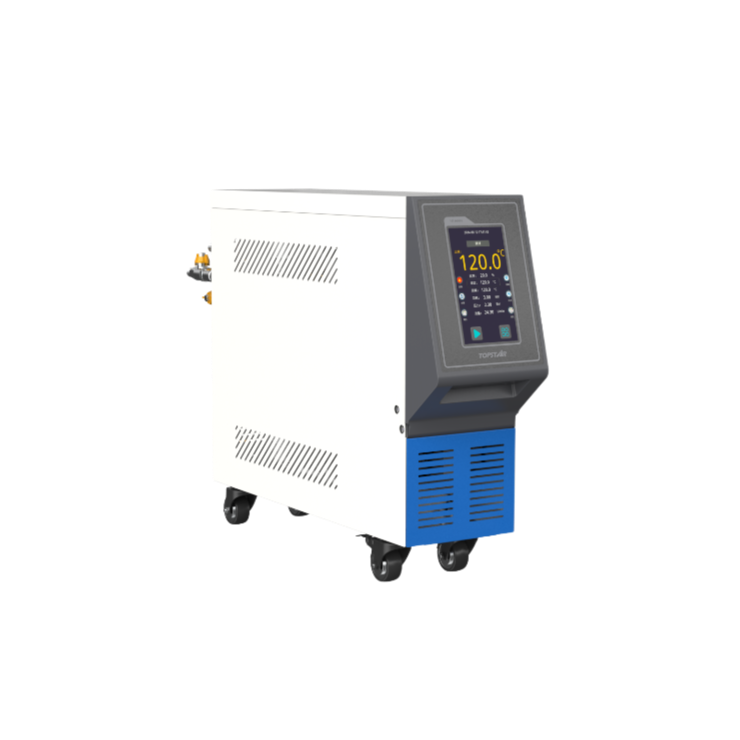
Achieve optimal mold alignment
To achieve accurate mold alignment, Topstar has adopted a new mold adjustment structure to improve the mold alignment of horizontal injection molding machines. In addition, through key factors such as correct settings, regular maintenance, accurate monitoring and temperature control, the risk of misalignment and its related problems can be significantly reduced. Whether you want to improve mold alignment, increase productivity or reduce machine wear, our team of experts will help you.
TRENDING POSTS
- What factors can cause delays in the injection molding process of plastic molding machine? 2024/09/18
- Exhibition Review| Topstar participates in InterPlas Thailand 2024 2024/09/18
- Star Case | Topstar helps Santong upgrade its intelligent plant 2024/09/18
- Topstar Special | National Science and Technology Workers Day 2024/09/18
HOT TOPIC
- .ervo motor-driven linear robots
- 3 axis robot
- 3 axis robots
- 3 in 1 Compact Dehumidifying Dryer
- 3-axis robot
- 3-axis robots
- 5-axis CNC machine
- accuracy
- Air Chillers
- all electric injection molding machine
- all electric injection molding machines
- All-electric injection molding machines
- and overall production quality. Therefore
- AP-RubberPlas
- automated injection molding machine
- Automation changed engineering
- automation of injection molding robots
- auxiliary machine
- Bench Injection Molding Machine
- Cabinet dryer manufacturers
- Cabinet dryers
- chiller
- CNC Drilling Machine
- CNC Drilling Machines
- cnc engraving machine manufacturer
- cnc laser cutting machine manufacturer
- CNC machine
- CNC Machine Center
- CNC Machine for Sale
- CNC Machine Manufacturing
- CNC Machine Tool
- CNC machine tool product
- CNC Machining Center
- CNC wood carving machine
- Cooling system
- Cross-Walking Single Axis Servo Cylinder Robot
- Cross-Walking Single-Axis Servo Cylinder Robot
- Cross-Walking Three-Axis/Five-Axis Servo Driven Robot
- cross-walking three-axis/five-axis servo-driven robot
- Dehumidifier Dryer
- Dehumidifying Dryer
- delta parallel robot
- Desktop Injection Molding Machine
- Desktop injection molding machines
- Desktop Molding Machine
- desktop plastic injection machine
- Desktop Plastic Injection Molding Machine
- direct clamp injection molding machine
- Direct clamp injection molding machines
- Dosing & mixing system
- Drilling Centers
- Drying and dehumidification system
- drying and dehumidifying equipment
- Drying and Dehumidifying System
- drying system
- effective and efficient. Cabinet dryers are also used in other industries where large quantities of material need to be dried
- efficient injection molding machine
- elbow hydraulic injection molding machines
- electric injection molding machine
- electric injection molding machines
- energy-efficient injection molding robot
- energy-saving injection molding machine
- etc. Among injection molding robots
- exhibition
- features of CNC machine
- Feeding And Conveying System
- Five Axis Machine Center
- Fully automatic injection molding machine
- Gathering Topstar
- giant injection molding machine
- GMU-600 5-Axis Machining Center
- Granulating & Recycling System
- Heavy duty injection molding machine
- High-precision electric molding machines
- high-precision plastic molding machines
- high-speed all electric injection molding machine
- Honeycomb rotor dehumidifier
- horizontal injection molding machine
- Horizontal Injection Molding Machines
- Horizontal Injection Moulding Machine
- Horizontal Mixer manufacturer
- How The CNC Machine Works
- hybrid injection molding machine
- hydraulic injection molding machine
- Hydraulic Injection Molding Machines
- in this article
- Industrial robot
- Industrial Robot Chinese brand
- industrial robot parts
- industrial robot supplier
- Industrial robots
- Industry Chain
- Injection Manipulator
- injection manipulator robot
- injection mold machines
- Injection molding
- Injection molding automation
- Injection Molding Automation Solution
- injection molding dryer
- Injection molding equipment
- injection molding hopper dryer
- Injection molding machine
- injection molding machine brand
- Injection Molding Machine Factory
- Injection Molding Machine Manufacture
- Injection molding machine manufacturer
- injection molding machine manufacturers
- Injection molding machine procurement
- injection molding machine robotic arm
- injection molding machine with a robot
- Injection molding machines
- injection molding material dehumidifying
- injection molding plant
- Injection Molding Robot
- injection molding robot arm
- Injection molding robot automation
- Injection molding robotic arm
- injection molding robots
- Injection moulding machine
- Injection Moulding Robots
- Injection Robot
- Injection robot arm
- Injection robot manufacturer
- Injection robot wholesale
- injection robots
- intelligent injection molding machines
- Introducing Injection Robot
- It is the best choice for drying large quantities of material at once. Cabinetmakers use these machines because they are fast
- large injection molding machine
- large injection molding machines
- Learn what industrial automation and robotics is
- linear robot
- linear robots
- low speed sound-proof granulator
- machine plastic molding
- make sure to add some! Improvements (2) Keyphrase in introduction: Your keyphrase or its synonyms appear in the first paragraph of the copy
- manipulator machine
- manufacturing
- medical grade injection molding machines
- medical injection molding machine
- medical injection molding machines
- micro injection molding machine
- middle speed granulator
- Mini CNC machine manufacturers.
- Mold Temperature Control System
- mold temperature controller
- mold temperature controllers
- molding material Dehumidifying System
- mould temperature control system
- mould temperature controller
- mould temperature controllers
- New electric injection molding machine
- nitrogen dryer manufacturer
- nitrogen dryer system manufacturer
- Oil type mold temperature controller
- Oil type mold temperature controllers
- open day
- Outbound links: No outbound links appear in this page. Add some! Images: No images appear on this page. Add some! Internal links: No internal links appear in this page
- PET Preform injection molding
- phone case maker machine
- phone case making machine
- plastic bottle making machine
- plastic bottle manufacturing
- plastic bucket making machine
- plastic bucket manufacturing
- Plastic chair making machine
- plastic forming equipment
- plastic hopper dryer
- plastic injection machine
- plastic injection machines
- plastic injection molding
- Plastic injection molding equipment
- Plastic injection molding machine
- Plastic Injection Molding Machines
- plastic injection moulding machine
- plastic injection robot
- Plastic Molding machine
- Plastic Molding Machines
- plastic molding press
- plastic moulding machine
- plastic phone case making machine
- plastic-molding machine
- powerful granulator
- Powerful Type Sound-Proof Granulator
- precision injection molding
- precision injection molding machines
- production of plastic seats
- pure water mould temperature controller
- Robot injection molding
- robot injection molding machine
- robot manufacturing companies
- Robotic arm for injection molding machine
- robotic injection molding machines
- robotics in injection molding
- SCARA robot
- SCARA robots
- Service-oriented manufacturing
- Servo Cylinder Robot
- servo driven robot
- Servo Driven Robots
- servo injection robots
- servo motor-driven linear robots
- servo-driven 3-axis robot
- Servo-Driven Robot
- Setup of injection machine
- Silicone Injection Molding Machine
- six-axis industrial robot
- Stainless Hopper Dryer
- Stainless Hopper Dryers
- star club
- swing arm robot
- take-out robots
- the choice between servo-driven robots and hydraulic robots will have a certain impact on efficiency
- the most popular injection molding machine
- the type of injection molding robot
- toggle clamp injection molding machine
- Toggle Hydraulic Injection Molding Machines
- toggle injection molding machine
- Top 10 brands of injection robots
- Topstar
- Topstar Engineering
- Topstar Industrial Robots
- Topstar injection molding intelligent
- Topstar Scara Robots
- Useful Injection molding machine
- Vertical machining centers
- volumetric type blender
- water chiller
- water chillers
- water distributor
- water type mold temperature controller
- Water Type MoldTemperature Controller
- Water-Type Mould Temperature Controllers
- We often face choices when performing injection molding. We will choose the type of injection molding machine
- wholesale of injection molding machines
- x carve CNC