How do injection molding machine manufacturers provide intelligent injection molding solutions?
2024/09/06 By Topstar
1-jpg.webp)
What distinguishes Topstar from other injection molding machine manufacturers is that it provides users with not only injection molding machines but also intelligent injection molding solutions. Industry 4.0 makes the injection molding industry and other manufacturing industries more intelligent, so we not only make products intelligent but also make users’ factory workshops intelligent. Intelligent injection molding solutions can improve productivity, improve quality, and reduce waste while reducing costs and shortening delivery time.
Injection molding machine manufacturers: intelligent injection molding whole plant solution
What is different from other injection molding machine manufacturers is that the intelligent injection molding solutions provided include factory planning, injection molding automation production lines, and data management. In the past, injection molding was a laboratory-intensive process that required constant supervision and manual adjustments. However, today, advanced intelligent management technologies and injection molding systems improve the efficiency and accuracy of the injection molding process.
The injection moulding automation production line can control all aspects of the moulding cycle, from injection moulding machines + auxiliary equipment to front-end automated central feeding, back-end robot automation modules, data management MES modules, and so on. It achieves more consistent production and minimizes human errors, ensuring that each part is manufactured according to precise specifications to support the integrated design, production, and maintenance of an intelligent manufacturing platform.
Injection molding machine + auxiliary equipment
Topstar divides its injection molding machine series into the TMll series, the TEll electric injection molding machine series, and the TH series direct pressure injection molding machine. Different from other injection molding machine manufacturers, Topstar uses a self-developed control system, which can communicate and interconnect with related auxiliary equipment while performing injection molding. The TMll series injection molding machine adopts the classic inward-turned five-point machine hinge structure, with stable and reliable performance and higher overall cost performance. At the same time, it adopts servo motors and internal gear pumps with fast response speed, stable pressure, and good energy-saving effects. In addition, it also has a double-cylinder balanced injection structure and CNC back pressure setting, which makes melting, injection, and pressure holding more stable.
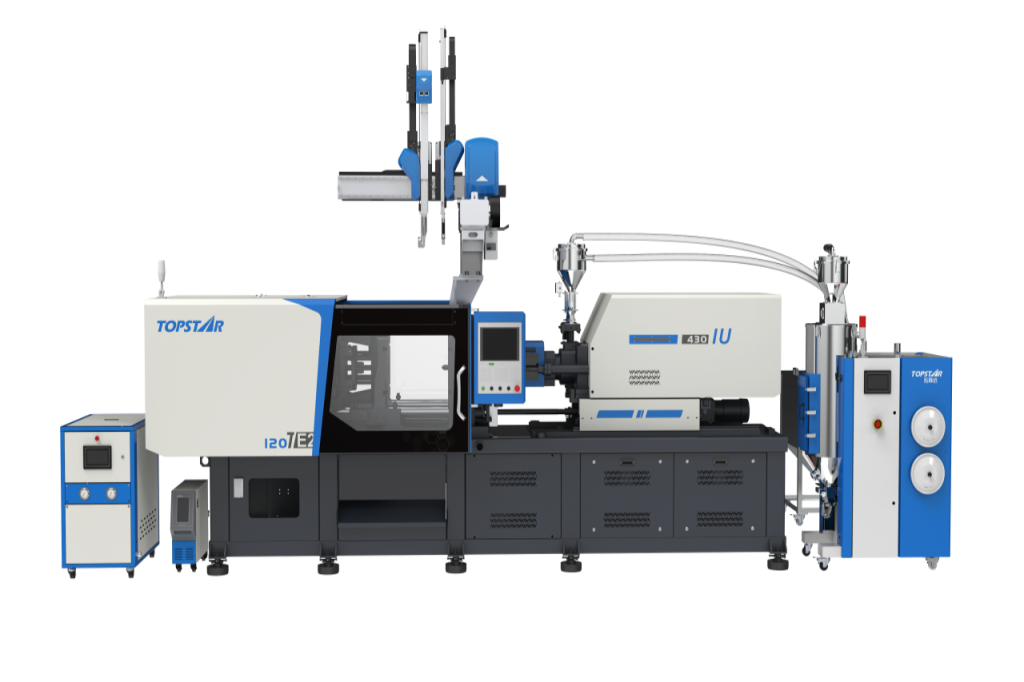
Tell series is a new second-generation electric injection molding machine developed under the Topstar PID process. Compared with the first generation of tops, it has higher molding performance, precision and stability, and higher reliability. The non-contact tie rod does not require lubrication to reduce pollution. High-performance pressure holding capacity can also make thick-walled products molded in one go.
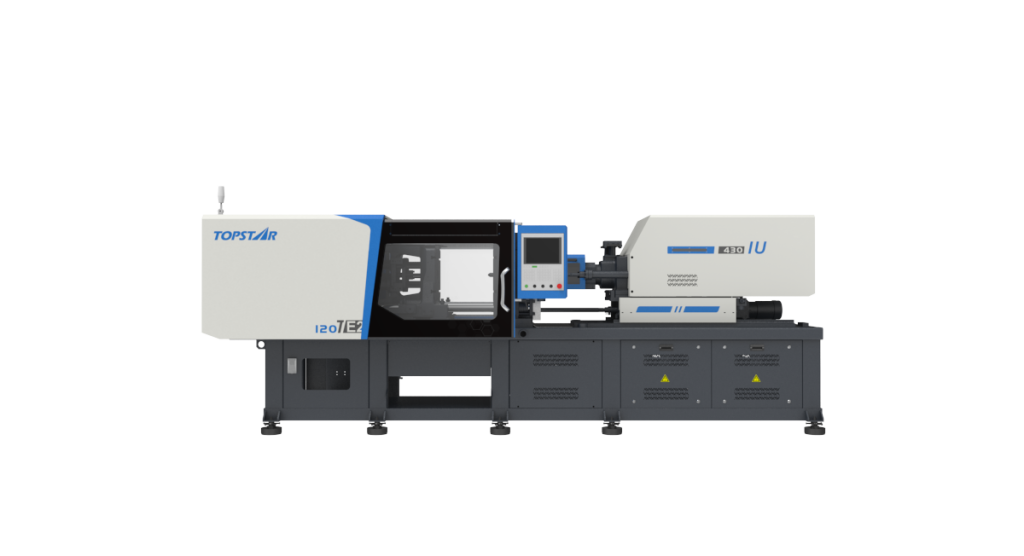
The TH injection molding machine series adopts a direct pressure central clamping structure, which can evenly distribute the clamping force on the mold projection, reduce machine plate deformation, product flash, achieve uniform product wall thickness, and long mold life.
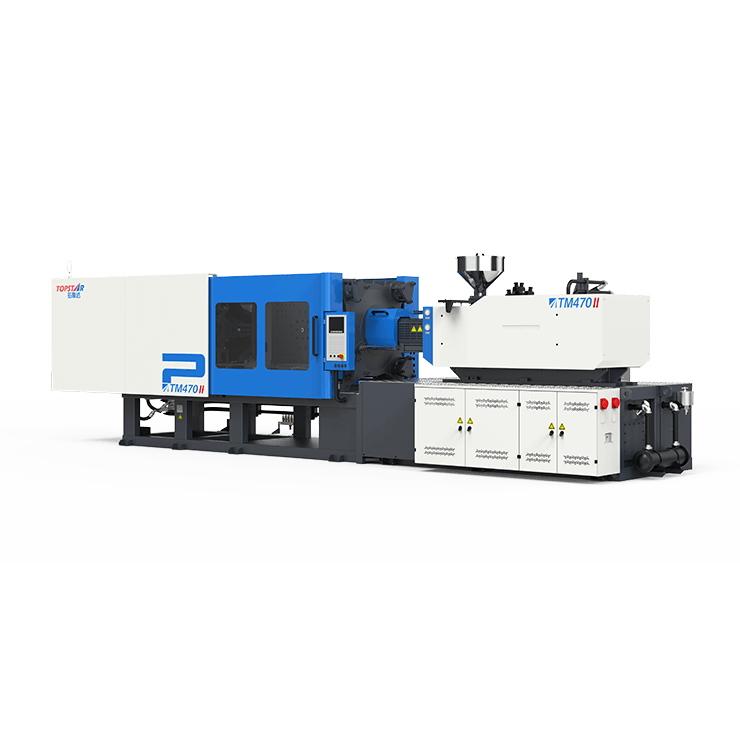
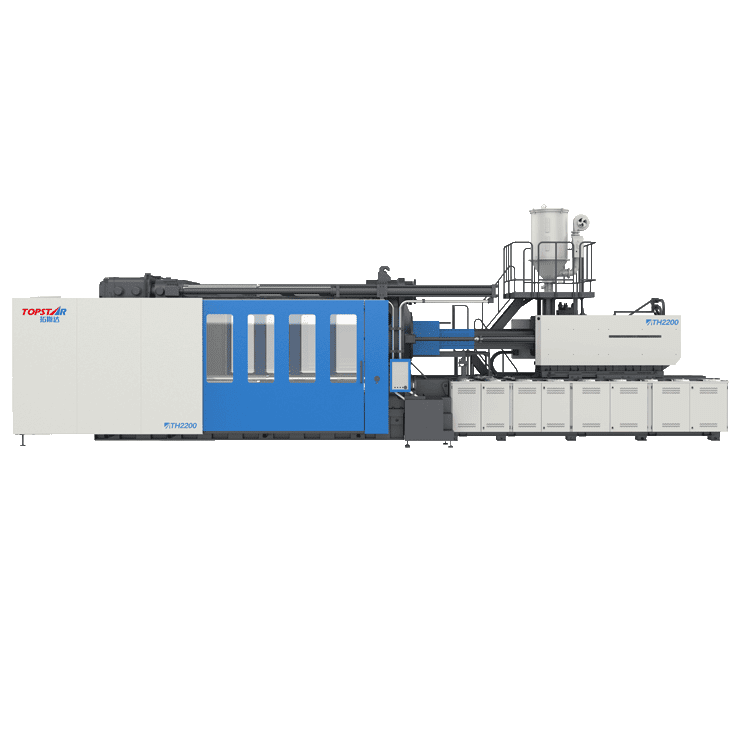
Material Centralized Feeding System
The Material Centralized Feeding System is an integrated material handling solution that automatically transports raw materials, such as plastic pellets, to multiple injection molding machines from a central location. The system replaces traditional manual material feeding methods, ensuring that the machines receive a steady, consistent flow of material without human intervention.
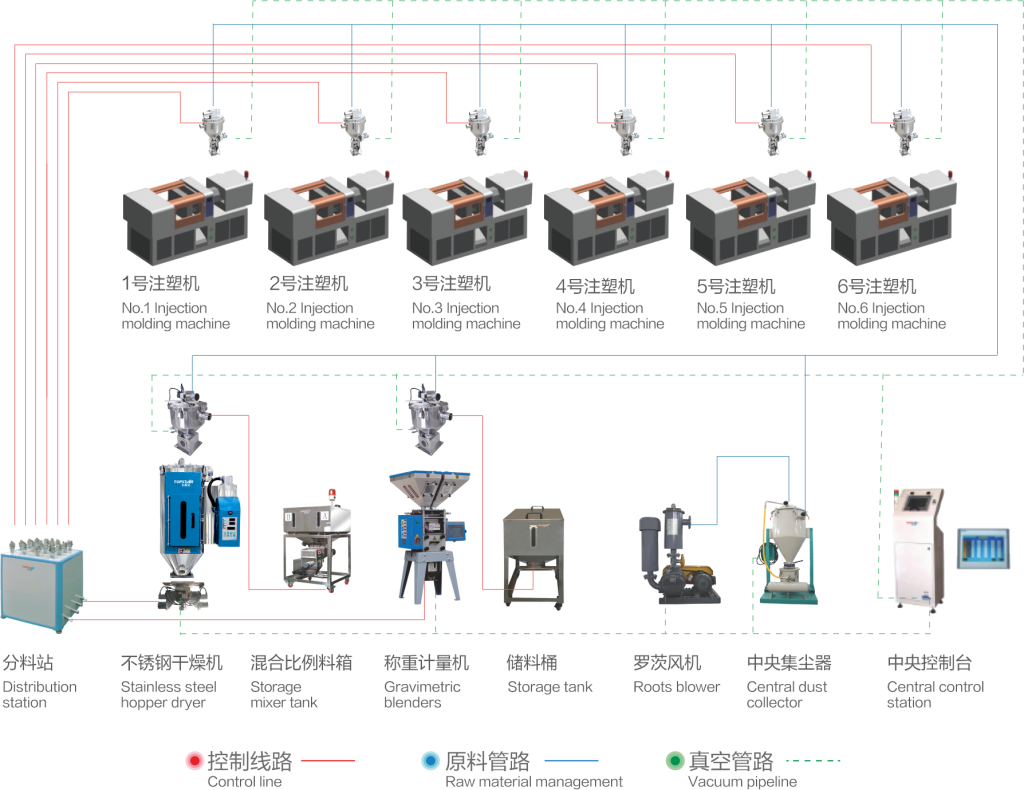
Core features
Automated material delivery: The system uses pneumatic conveyors to automatically deliver materials from a central warehouse to the injection molding machines. Sensors and control systems ensure that each machine receives the correct amount of material as needed, preventing shortages or overfilling that lead to inefficient production.
Real-time monitoring and control: The system is equipped with real-time monitoring capabilities, allowing operators to oversee the material supply process from a central console. The feed rate can be adjusted to the specific needs of each machine, optimizing the flow of materials throughout the production line.
Contamination-free handling: One of the main advantages of this automated system is its closed-loop design, which reduces the risk of contamination. By minimizing human contact with raw materials, the system ensures that materials remain clean and free of debris, thereby improving the quality of the finished product.
Energy-saving operation: The central feeding system only operates when materials need to be delivered to the machine, thereby minimizing energy consumption. This energy-efficient design reduces operating costs while also contributing to a more sustainable manufacturing process.
T-MES Intelligent Manufacturing Execution System
MES is a production management system for the workshop execution layer, which integrates production from production plan execution, production process monitoring, equipment operation management, product quality and traceability, personnel scheduling, billboard display and multi-dimensional other output. Plastic manufacturers can integrate data collection and analysis functions into their machines to provide real-time insights into the molding process. The machine embeds sensors and monitoring systems to track key parameters such as temperature, pressure, flow, and cycle time. The system then analyzes this data to identify trends, detect anomalies, and optimize production processes.
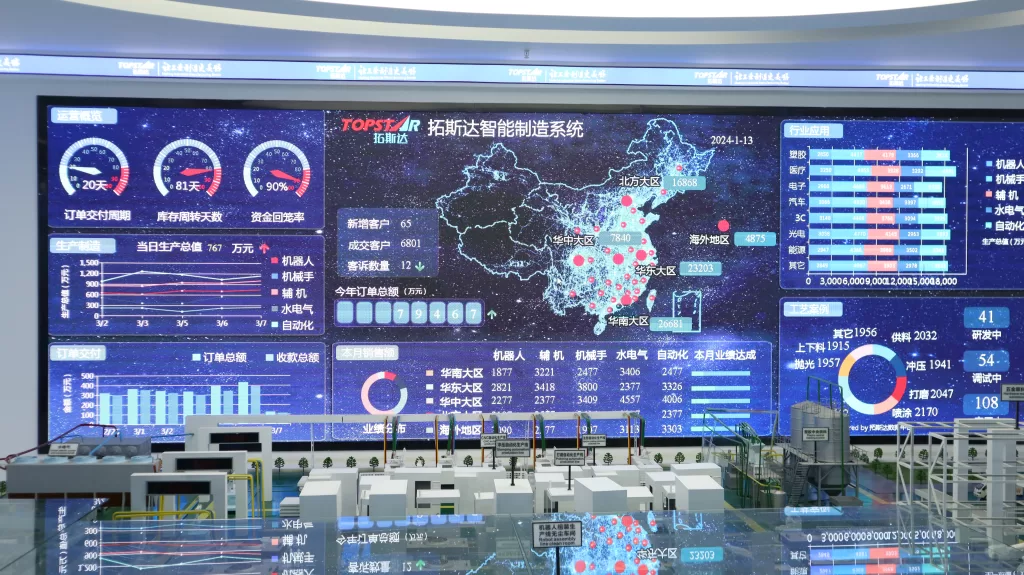
By leveraging the power of data, manufacturers can make informed decisions, improve the efficiency and quality of injection molding operations and arrange work reasonably. For industries such as medical devices or aerospace, where precision and quality are critical, data-driven injection molding solutions ensure that each component meets strict regulatory and performance standards.
The future of intelligent injection molding solutions
Through automation, data analytics, Industry 4.0, industrial intelligence, and energy-saving technologies, companies in multiple industries can be provided with the tools they need to remain competitive in a rapidly changing market.
Whether it is improving precision in the medical device industry, increasing efficiency in automotive production, or reducing material waste in consumer goods manufacturing, Topstar, as an excellent injection molding machine manufacturer, is providing solutions that drive innovation and success. Whether you want to improve efficiency, reduce costs, or improve product quality, our smart injection molding solutions can help you achieve a comprehensive service platform for smart manufacturing.
TRENDING POSTS
- What factors can cause delays in the injection molding process of plastic molding machine? 2024/09/06
- Exhibition Review| Topstar participates in InterPlas Thailand 2024 2024/09/06
- Star Case | Topstar helps Santong upgrade its intelligent plant 2024/09/06
- Topstar Special | National Science and Technology Workers Day 2024/09/06
HOT TOPIC
- .ervo motor-driven linear robots
- 3 axis robot
- 3 axis robots
- 3 in 1 Compact Dehumidifying Dryer
- 3-axis robot
- 3-axis robots
- 5-axis CNC machine
- accuracy
- Air Chillers
- all electric injection molding machine
- all electric injection molding machines
- All-electric injection molding machines
- and overall production quality. Therefore
- AP-RubberPlas
- automated injection molding machine
- Automation changed engineering
- automation of injection molding robots
- auxiliary machine
- Bench Injection Molding Machine
- Cabinet dryer manufacturers
- Cabinet dryers
- chiller
- CNC Drilling Machine
- CNC Drilling Machines
- cnc engraving machine manufacturer
- cnc laser cutting machine manufacturer
- CNC machine
- CNC Machine Center
- CNC Machine for Sale
- CNC Machine Manufacturing
- CNC Machine Tool
- CNC machine tool product
- CNC Machining Center
- CNC wood carving machine
- Cooling system
- Cross-Walking Single Axis Servo Cylinder Robot
- Cross-Walking Single-Axis Servo Cylinder Robot
- Cross-Walking Three-Axis/Five-Axis Servo Driven Robot
- cross-walking three-axis/five-axis servo-driven robot
- Dehumidifier Dryer
- Dehumidifying Dryer
- delta parallel robot
- Desktop Injection Molding Machine
- Desktop injection molding machines
- Desktop Molding Machine
- desktop plastic injection machine
- Desktop Plastic Injection Molding Machine
- direct clamp injection molding machine
- Direct clamp injection molding machines
- Dosing & mixing system
- Drilling Centers
- Drying and dehumidification system
- drying and dehumidifying equipment
- Drying and Dehumidifying System
- drying system
- effective and efficient. Cabinet dryers are also used in other industries where large quantities of material need to be dried
- efficient injection molding machine
- elbow hydraulic injection molding machines
- electric injection molding machine
- electric injection molding machines
- energy-efficient injection molding robot
- energy-saving injection molding machine
- etc. Among injection molding robots
- exhibition
- features of CNC machine
- Feeding And Conveying System
- Five Axis Machine Center
- Fully automatic injection molding machine
- Gathering Topstar
- giant injection molding machine
- GMU-600 5-Axis Machining Center
- Granulating & Recycling System
- Heavy duty injection molding machine
- High-precision electric molding machines
- high-precision plastic molding machines
- high-speed all electric injection molding machine
- Honeycomb rotor dehumidifier
- horizontal injection molding machine
- Horizontal Injection Molding Machines
- Horizontal Injection Moulding Machine
- Horizontal Mixer manufacturer
- How The CNC Machine Works
- hybrid injection molding machine
- hydraulic injection molding machine
- Hydraulic Injection Molding Machines
- in this article
- Industrial robot
- Industrial Robot Chinese brand
- industrial robot parts
- industrial robot supplier
- Industrial robots
- Industry Chain
- Injection Manipulator
- injection manipulator robot
- injection mold machines
- Injection molding
- Injection molding automation
- Injection Molding Automation Solution
- injection molding dryer
- Injection molding equipment
- injection molding hopper dryer
- Injection molding machine
- injection molding machine brand
- Injection Molding Machine Factory
- Injection Molding Machine Manufacture
- Injection molding machine manufacturer
- injection molding machine manufacturers
- Injection molding machine procurement
- injection molding machine robotic arm
- injection molding machine with a robot
- Injection molding machines
- injection molding material dehumidifying
- injection molding plant
- Injection Molding Robot
- injection molding robot arm
- Injection molding robot automation
- Injection molding robotic arm
- injection molding robots
- Injection moulding machine
- Injection Moulding Robots
- Injection Robot
- Injection robot arm
- Injection robot manufacturer
- Injection robot wholesale
- injection robots
- intelligent injection molding machines
- Introducing Injection Robot
- It is the best choice for drying large quantities of material at once. Cabinetmakers use these machines because they are fast
- large injection molding machine
- large injection molding machines
- Learn what industrial automation and robotics is
- linear robot
- linear robots
- low speed sound-proof granulator
- machine plastic molding
- make sure to add some! Improvements (2) Keyphrase in introduction: Your keyphrase or its synonyms appear in the first paragraph of the copy
- manipulator machine
- manufacturing
- medical grade injection molding machines
- medical injection molding machine
- medical injection molding machines
- micro injection molding machine
- middle speed granulator
- Mini CNC machine manufacturers.
- Mold Temperature Control System
- mold temperature controller
- mold temperature controllers
- molding material Dehumidifying System
- mould temperature control system
- mould temperature controller
- mould temperature controllers
- New electric injection molding machine
- nitrogen dryer manufacturer
- nitrogen dryer system manufacturer
- Oil type mold temperature controller
- Oil type mold temperature controllers
- open day
- Outbound links: No outbound links appear in this page. Add some! Images: No images appear on this page. Add some! Internal links: No internal links appear in this page
- PET Preform injection molding
- phone case maker machine
- phone case making machine
- plastic bottle making machine
- plastic bottle manufacturing
- plastic bucket making machine
- plastic bucket manufacturing
- Plastic chair making machine
- plastic forming equipment
- plastic hopper dryer
- plastic injection machine
- plastic injection machines
- plastic injection molding
- Plastic injection molding equipment
- Plastic injection molding machine
- Plastic Injection Molding Machines
- plastic injection moulding machine
- plastic injection robot
- Plastic Molding machine
- Plastic Molding Machines
- plastic molding press
- plastic moulding machine
- plastic phone case making machine
- plastic-molding machine
- powerful granulator
- Powerful Type Sound-Proof Granulator
- precision injection molding
- precision injection molding machines
- production of plastic seats
- pure water mould temperature controller
- Robot injection molding
- robot injection molding machine
- robot manufacturing companies
- Robotic arm for injection molding machine
- robotic injection molding machines
- robotics in injection molding
- SCARA robot
- SCARA robots
- Service-oriented manufacturing
- Servo Cylinder Robot
- servo driven robot
- Servo Driven Robots
- servo injection robots
- servo motor-driven linear robots
- servo-driven 3-axis robot
- Servo-Driven Robot
- Setup of injection machine
- Silicone Injection Molding Machine
- six-axis industrial robot
- Stainless Hopper Dryer
- Stainless Hopper Dryers
- star club
- swing arm robot
- take-out robots
- the choice between servo-driven robots and hydraulic robots will have a certain impact on efficiency
- the most popular injection molding machine
- the type of injection molding robot
- toggle clamp injection molding machine
- Toggle Hydraulic Injection Molding Machines
- toggle injection molding machine
- Top 10 brands of injection robots
- Topstar
- Topstar Engineering
- Topstar Industrial Robots
- Topstar injection molding intelligent
- Topstar Scara Robots
- Useful Injection molding machine
- Vertical machining centers
- volumetric type blender
- water chiller
- water chillers
- water distributor
- water type mold temperature controller
- Water Type MoldTemperature Controller
- Water-Type Mould Temperature Controllers
- We often face choices when performing injection molding. We will choose the type of injection molding machine
- wholesale of injection molding machines
- x carve CNC