Electric injection molding machine solutions for the medical field
2024/09/04 By Topstar
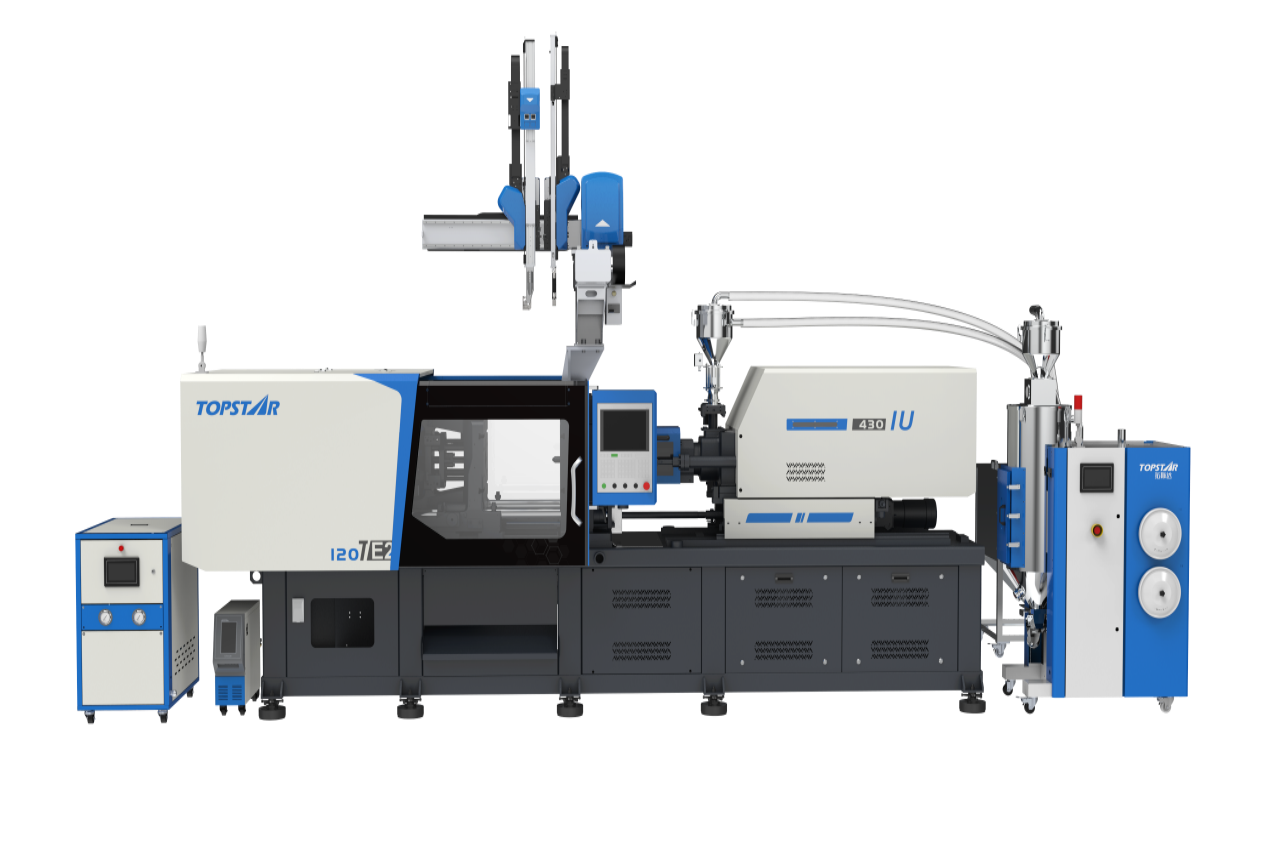
All products in the medical field must meet strict quality control standards, precision, and cleanliness. When providing injection molding solutions to customers in the medical field, an electric injection molding machine is used to meet strict quality standards, ensure cost-effectiveness, and develop a comprehensive injection molding turnkey plan for you. In this article, we will ask you to share the core components of Topstar’s injection molding turnkey plan and the advantages of electric injection molding machines.
Injection molding Whole plant solution
Topstar’s injection molding plant includes one-stop module planning and construction, injection molding machine + auxiliary equipment, front automation central feeding, back-end robot automation module, water, electricity, and gas energy module, data management MES module to achieve intelligent injection molding plant modular planning, making an investment in manufacturing easier. A comprehensive intelligent manufacturing service platform that realizes integrated design, production, implementation, and maintenance of factory planning + injection molding automation production line + data management.
-1024x551.webp)
Why are electric injection molding machine ideal for the medical field?
The medical field requires precise manufacturing processes to produce high-quality parts with strict tolerances. Compared with traditional hydraulic injection molding machines, the most significant advantage is the accurate control that electric injection molding machines can provide. These machines use electric servomotors to control the entire injection process, from clamping force to speed, allowing for precise and repeatable motion.
Another advantage is cleanliness. The fact that fully electric machines do not require hydraulic oil also means that fully electric injection molding machines are quieter and more energy efficient, eliminating the risk of oil leaks and contamination. This is particularly important in medicine, where maintaining cleanliness and sterility is essential.
At the same time, their ability to precisely control the injection process reduces cycle times, significantly increasing production capacity.
Core features of Topstar electric injection molding machine
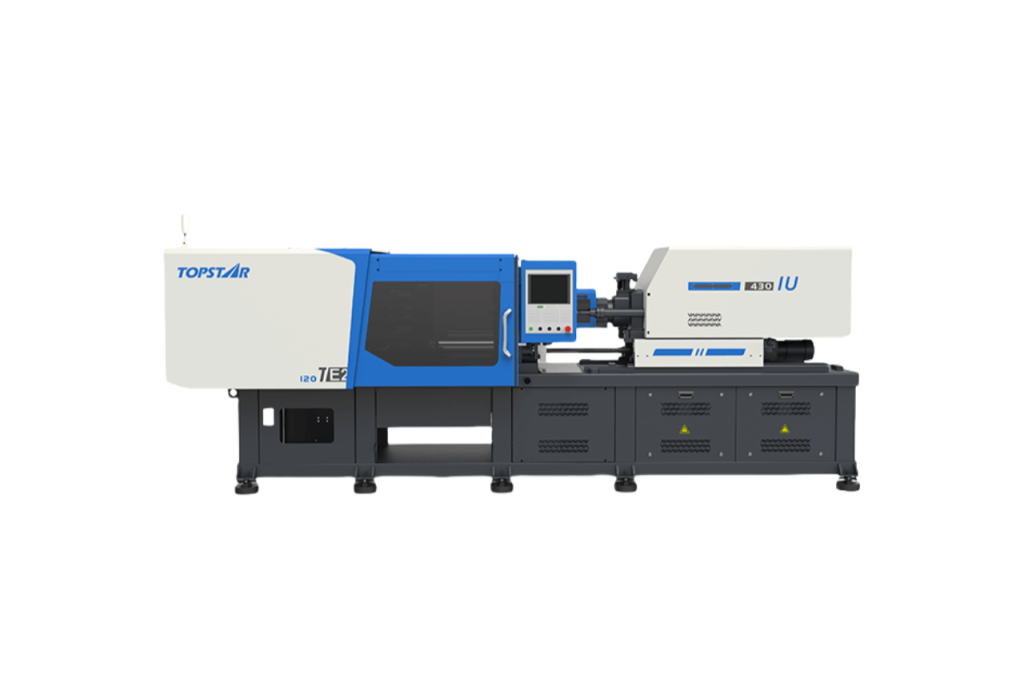
Servo self-drive and ultra-low speed operation
At the heart of Topstar electric injection molding machines is the self-developed servo self-drive system, which can control the various movements and functions of the machine with extremely high precision. Unlike traditional hydraulic systems that rely on fluid pressure and valves, the servo self-drive system can directly and accurately control injection speed, pressure, and position. In addition, servo self-drive technology helps improve the machine’s overall energy efficiency. By using electricity only when needed, the system minimizes energy waste.
Ultra-low speed operation enables them to carefully control the material flow into the mold when producing thin-walled parts or complex components, eliminating undesirable defects such as product flow marks. By reducing the injection speed, the machine ensures that the material fills the mold completely and evenly, producing higher-quality parts with less scrap.
High-precision pressure control and low-damping injection unit
The high-precision pressure control system accurately regulates the pressure during the injection process and ensures that the molten material delivers the required force to the mold cavity. When it comes to medical plastic parts, by maintaining optimal pressure throughout the injection cycle, Topstar’s machines help prevent common defects such as sink marks, voids, or flashes, which can occur when pressure is too high or too low.
The low-damping design minimizes the resistance encountered by the injection screw as it moves forward, allowing for more consistent and controlled delivery of material into the mold. The benefits of the low-damping injection unit are particularly evident in applications that require high-speed injection or when processing materials with challenging flow characteristics. The machine can maintain a steady injection speed by reducing the damping effect, improving part stability.
High-performance holding pressure capability of electric injection molding machine
High-performance holding pressure capability ensures that the pressure applied during the injection process remains consistent, even after the initial injection phase. Pressure maintenance is critical to ensure that the molten material fills the mold cavity correctly, especially in areas where the material may begin to cool and solidify prematurely. When producing medical products, pressure changes can cause defects such as sink marks, voids, or warping. By maintaining consistent pressure throughout the holding phase, electric injection molding machines help ensure the final product meets strict quality standards and improve the ability to mold thick-walled products in one go.
Comprehensive Injection Molding Solutions
Topstar is dedicated to delivering complete injection molding solutions that cater to the specific requirements of the medical industry. Electric injection molding machines ensure your production process is optimized for consistent products through their servo self-drive, high-precision pressure control, and high-performance holding pressure capabilities. Whether you are producing large quantities of medical disposables, complex implantable devices, or custom parts, our all-electric machines can provide the precision and control required to meet the highest quality and compliance standards.
TRENDING POSTS
- What factors can cause delays in the injection molding process of plastic molding machine? 2024/09/04
- Exhibition Review| Topstar participates in InterPlas Thailand 2024 2024/09/04
- Star Case | Topstar helps Santong upgrade its intelligent plant 2024/09/04
- Topstar Special | National Science and Technology Workers Day 2024/09/04
HOT TOPIC
- .ervo motor-driven linear robots
- 1.0 guangdong topstar technology co. ltd
- 1.0 topstar china
- 1.0 topstar robot
- 11
- 2
- 21
- 23
- 3 axis robot
- 3 axis robots
- 3 in 1 Compact Dehumidifying Dryer
- 3-axis robot
- 3-axis robots
- 39
- 41
- 5-axis CNC machine
- 62
- accuracy
- Air Chillers
- all electric injection molding machine
- all electric injection molding machines
- All-electric injection molding machines
- and overall production quality. Therefore
- AP-RubberPlas
- automated injection molding machine
- Automation changed engineering
- automation of injection molding robots
- auxiliary machine
- Bench Injection Molding Machine
- Cabinet dryer manufacturers
- Cabinet dryers
- chiller
- CNC Drilling Machine
- CNC Drilling Machines
- cnc engraving machine manufacturer
- cnc laser cutting machine manufacturer
- CNC machine
- CNC Machine Center
- CNC Machine for Sale
- CNC Machine Manufacturing
- CNC Machine Tool
- CNC machine tool product
- CNC Machining Center
- CNC wood carving machine
- Cooling system
- Cross-Walking Single Axis Servo Cylinder Robot
- Cross-Walking Single-Axis Servo Cylinder Robot
- Cross-Walking Three-Axis/Five-Axis Servo Driven Robot
- cross-walking three-axis/five-axis servo-driven robot
- Dehumidifier Dryer
- Dehumidifying Dryer
- delta parallel robot
- Desktop Injection Molding Machine
- Desktop injection molding machines
- Desktop Molding Machine
- desktop plastic injection machine
- Desktop Plastic Injection Molding Machine
- direct clamp injection molding machine
- Direct clamp injection molding machines
- Dosing & mixing system
- Drilling Centers
- Drying and dehumidification system
- drying and dehumidifying equipment
- Drying and Dehumidifying System
- drying system
- effective and efficient. Cabinet dryers are also used in other industries where large quantities of material need to be dried
- efficient injection molding machine
- elbow hydraulic injection molding machines
- electric injection molding machine
- electric injection molding machines
- energy-efficient injection molding robot
- energy-saving injection molding machine
- etc. Among injection molding robots
- exhibition
- features of CNC machine
- Feeding And Conveying System
- Five Axis Machine Center
- Fully automatic injection molding machine
- Gathering Topstar
- giant injection molding machine
- GMU-600 5-Axis Machining Center
- Granulating & Recycling System
- Heavy duty injection molding machine
- High-precision electric molding machines
- high-precision plastic molding machines
- high-speed all electric injection molding machine
- Honeycomb rotor dehumidifier
- horizontal injection molding machine
- Horizontal Injection Molding Machines
- Horizontal Injection Moulding Machine
- Horizontal Mixer manufacturer
- How The CNC Machine Works
- hybrid injection molding machine
- hydraulic injection molding machine
- Hydraulic Injection Molding Machines
- in this article
- Industrial robot
- Industrial Robot Chinese brand
- industrial robot parts
- industrial robot supplier
- Industrial robots
- Industry Chain
- Injection Manipulator
- injection manipulator robot
- injection mold machines
- Injection molding
- Injection molding automation
- Injection Molding Automation Solution
- injection molding dryer
- Injection molding equipment
- injection molding hopper dryer
- Injection molding machine
- injection molding machine brand
- Injection Molding Machine Factory
- Injection Molding Machine Manufacture
- Injection molding machine manufacturer
- injection molding machine manufacturers
- Injection molding machine procurement
- injection molding machine robotic arm
- injection molding machine with a robot
- Injection molding machines
- injection molding material dehumidifying
- injection molding plant
- Injection Molding Robot
- injection molding robot arm
- Injection molding robot automation
- Injection molding robotic arm
- injection molding robots
- Injection moulding machine
- injection moulding machines
- Injection Moulding Robots
- Injection Robot
- Injection robot arm
- Injection robot manufacturer
- Injection robot wholesale
- injection robots
- intelligent injection molding machines
- Introducing Injection Robot
- It is the best choice for drying large quantities of material at once. Cabinetmakers use these machines because they are fast
- large injection molding machine
- large injection molding machines
- Learn what industrial automation and robotics is
- linear robot
- linear robots
- low speed sound-proof granulator
- machine plastic molding
- make sure to add some! Improvements (2) Keyphrase in introduction: Your keyphrase or its synonyms appear in the first paragraph of the copy
- manipulator machine
- manufacturing
- medical grade injection molding machines
- medical injection molding machine
- medical injection molding machines
- micro injection molding machine
- middle speed granulator
- Mini CNC machine manufacturers.
- Mold Temperature Control System
- mold temperature controller
- mold temperature controllers
- molding material Dehumidifying System
- mould temperature control system
- mould temperature controller
- mould temperature controllers
- New electric injection molding machine
- nitrogen dryer manufacturer
- nitrogen dryer system manufacturer
- Oil type mold temperature controller
- Oil type mold temperature controllers
- open day
- Outbound links: No outbound links appear in this page. Add some! Images: No images appear on this page. Add some! Internal links: No internal links appear in this page
- PET Preform injection molding
- phone case maker machine
- phone case making machine
- plastic bottle making machine
- plastic bottle manufacturing
- plastic bucket making machine
- plastic bucket manufacturing
- Plastic chair making machine
- plastic forming equipment
- plastic hopper dryer
- plastic injection machine
- plastic injection machines
- plastic injection molding
- Plastic injection molding equipment
- Plastic injection molding machine
- Plastic Injection Molding Machines
- plastic injection moulding machine
- plastic injection moulding machines
- plastic injection robot
- Plastic Molding machine
- Plastic Molding Machines
- plastic molding press
- plastic moulding machine
- plastic phone case making machine
- plastic-molding machine
- powerful granulator
- Powerful Type Sound-Proof Granulator
- precision injection molding
- precision injection molding machines
- production of plastic seats
- pure water mould temperature controller
- Robot injection molding
- robot injection molding machine
- robot manufacturing companies
- Robotic arm for injection molding machine
- robotic injection molding machines
- robotics in injection molding
- SCARA robot
- SCARA robots
- Service-oriented manufacturing
- Servo Cylinder Robot
- servo driven robot
- Servo Driven Robots
- servo injection robots
- servo motor-driven linear robots
- servo-driven 3-axis robot
- Servo-Driven Robot
- Setup of injection machine
- Silicone Injection Molding Machine
- six-axis industrial robot
- Stainless Hopper Dryer
- Stainless Hopper Dryers
- star club
- swing arm robot
- take-out robots
- the choice between servo-driven robots and hydraulic robots will have a certain impact on efficiency
- the most popular injection molding machine
- the type of injection molding robot
- toggle clamp injection molding machine
- Toggle Hydraulic Injection Molding Machines
- toggle injection molding machine
- Top 10 brands of injection robots
- Topstar
- Topstar Engineering
- Topstar Industrial Robots
- Topstar injection molding intelligent
- Topstar Scara Robots
- Useful Injection molding machine
- Vertical machining centers
- volumetric type blender
- water chiller
- water chillers
- water distributor
- water type mold temperature controller
- Water Type MoldTemperature Controller
- Water-Type Mould Temperature Controllers
- We often face choices when performing injection molding. We will choose the type of injection molding machine
- wholesale of injection molding machines
- x carve CNC
- 热门查询 点击次数 展示 排名 topstar